In 2025, the demand for high-quality pharmaceuticals continues to rise, driven by technological advancements and stringent regulations. This article provides an in-depth analysis of the pill presser market, key factors to consider when selecting a machine, and the latest innovations and trends. It aims to assist professional buyers in making informed decisions to enhance their operations.
Table of Contents:
– Market Overview of Pill Pressers
– Detailed Analysis of the Pill Presser Market
– Innovations and Trends in Pill Pressing Technology
– Key Factors When Selecting a Pill Presser
– Innovations in Pill Presser Technology
– Regulatory Compliance and Quality Assurance
– Future Trends and Developments
– Final Thoughts
Market Overview of Pill Pressers
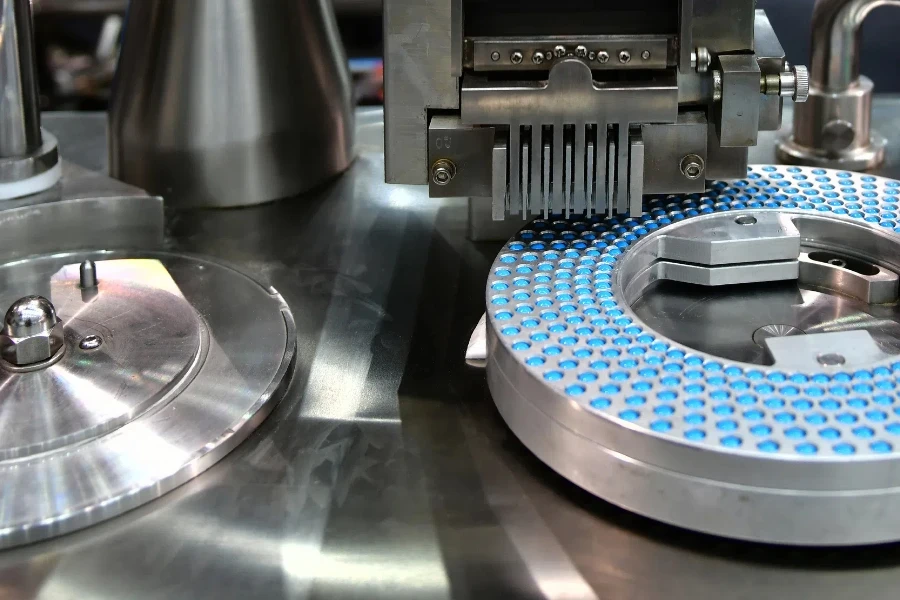
The global pill presser market has been experiencing significant growth. The market was valued at approximately USD 3.12 billion in 2024 and is projected to reach USD 5.62 billion by 2030, growing at a compound annual growth rate (CAGR) of 9.93%. This growth is driven by increasing demand for high-quality pharmaceuticals, stringent regulatory requirements, and technological advancements in pill pressing machinery.
North America holds a substantial share of the market, attributed to the presence of major pharmaceutical companies and advanced healthcare infrastructure. Europe follows closely, with Germany and the United Kingdom leading in pill presser adoption due to stringent drug manufacturing regulations. The Asia-Pacific region is expected to witness the highest growth rate, fueled by expanding pharmaceutical manufacturing capabilities in countries like China and India.
Key players in the market include Accutek Packaging Equipment Companies, ACG Group, Bosch Packaging Technology, and IMA Group. These companies focus on innovations such as automation, real-time monitoring, and enhanced precision to meet the growing demand for efficient and reliable pill pressing solutions. The market is characterized by moderate competition, with companies striving to differentiate through technological advancements and superior customer service.
Detailed Analysis of the Pill Presser Market
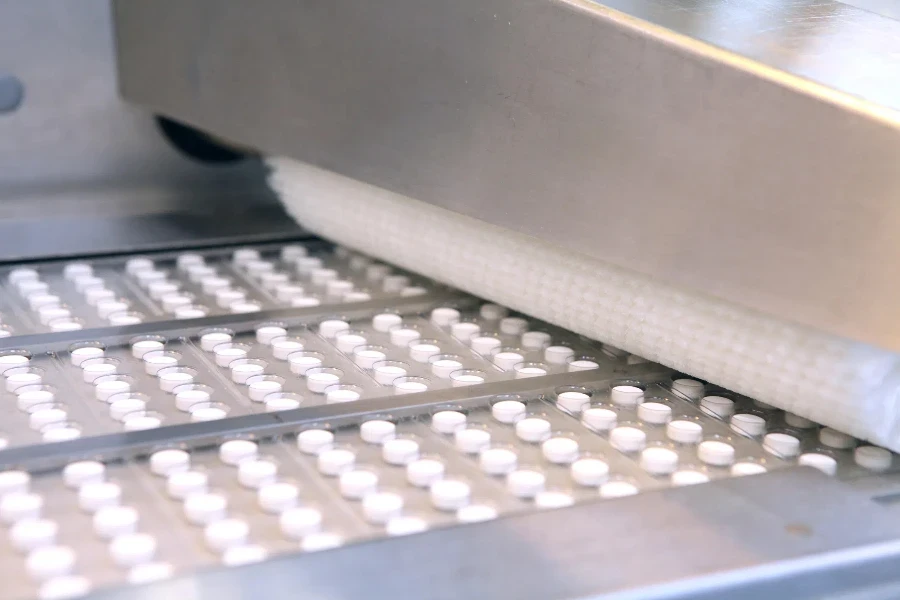
The pill presser market is segmented based on product type, automation grade, application, end-user, and sales channel. Product types include rotary tablet presses and single-station tablet presses, with rotary presses dominating due to their high production capacity and efficiency. Automation grades range from fully-automatic to semi-automatic, with the former preferred for large-scale production due to reduced labor costs and higher precision.
Key performance benchmarks in the market include tablet uniformity, production speed, and machine downtime. Manufacturers are continuously improving these parameters to enhance productivity and ensure compliance with stringent quality standards. The market is also influenced by economic factors such as healthcare expenditure and pharmaceutical industry growth, driving demand for advanced pill pressing machinery.
Consumer behavior is shifting towards high-quality, easy-to-swallow tablets, increasing demand for precise and reliable pill pressers. Distribution channels include direct sales, distributors, and online platforms, with a growing trend towards e-commerce due to convenience and broader reach. Recent innovations in the market include integrating digital technologies like IoT for real-time monitoring and predictive maintenance, enhancing machine efficiency and reducing operational costs.
Innovations and Trends in Pill Pressing Technology
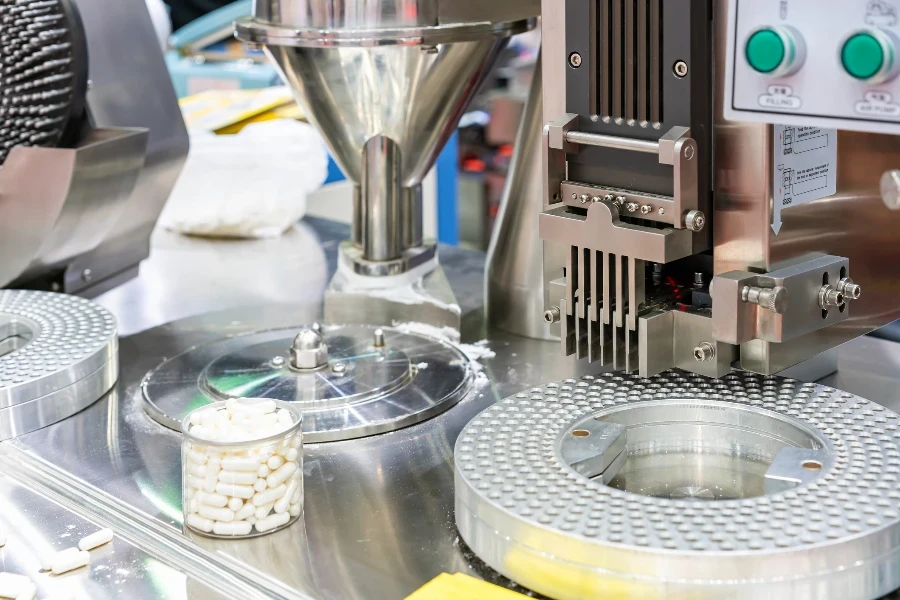
The pill presser market is witnessing rapid advancements in technology, focusing on automation and digitalization. Automated pill pressers are becoming increasingly popular due to their ability to enhance production efficiency, reduce human error, and ensure consistent tablet quality. These machines are equipped with advanced control systems, real-time monitoring capabilities, and predictive maintenance features, minimizing downtime and optimizing production processes.
Digitalization is crucial in the evolution of pill pressing technology. Internet of Things (IoT) integration allows for real-time data collection and analysis, enabling manufacturers to monitor machine performance, detect issues early, and make data-driven decisions. This improves operational efficiency and ensures compliance with regulatory standards by maintaining detailed records of the manufacturing process.
Social trends such as the increasing prevalence of chronic diseases and the aging population are driving demand for pharmaceuticals, thereby boosting the pill presser market. Consumers increasingly seek high-quality medications that are easy to swallow, leading to a focus on tablet uniformity and aesthetic appeal in pill pressing. Manufacturers are investing in research and development to create machines that can handle varied formulations and produce tablets with precise dimensions and smooth surfaces.
Key Factors When Selecting a Pill Presser
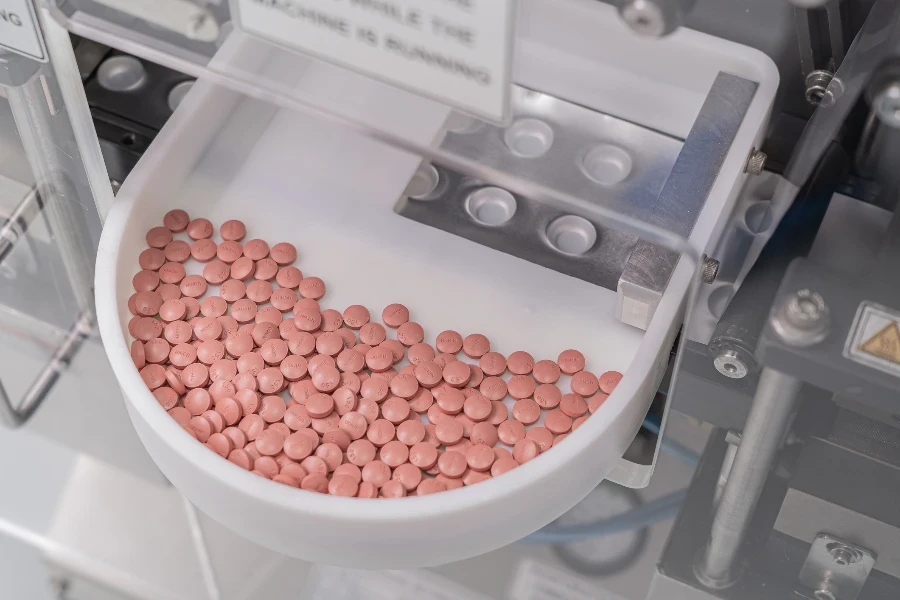
When selecting a pill presser, several key factors must be considered to ensure the machine meets the specific needs of your operation. These factors include technical specifications, performance, design, safety standards, and cost-effectiveness. Below, we delve into each of these aspects in greater detail.
Technical Specifications
Technical specifications are crucial when selecting a pill presser as they directly impact the machine’s performance and suitability for your production requirements.
Operating Force and Rated Capacity
The operating force of a pill presser is the maximum load required to compress the ingredients into a pill, typically measured in tons. For instance, a machine with a rated capacity of 50 tons can exert significant pressure, ensuring the pills are compact and uniform. The rated capacity, which is the pressure exerted at the bottom of the stroke, must align with the material being compressed to avoid damage and ensure efficiency.
Production Rate
The production rate, expressed in pills per minute, is crucial for meeting demand. High-speed machines can produce thousands of pills per hour, essential for large-scale manufacturing. For example, a machine with a production rate of 1000 pills per minute would be suitable for high-demand scenarios, whereas smaller operations might only require a machine with a rate of 200 pills per minute.
Sheet Capacity
Sheet capacity refers to the maximum thickness, length, and depth of the material the machine can handle. For pill pressers, this translates to the maximum dimensions of the pill mold. Machines with larger sheet capacities can produce larger or more complex pill shapes, providing flexibility in product design.
Performance and Functionality
Performance and functionality are critical to the efficiency and reliability of a pill presser.
Automation and Control Systems
Modern pill pressers often include advanced automation features such as computer numeric control (CNC) or programmable logic controllers (PLC). These systems allow precise control over the pressing process, adjusting parameters like pressure, speed, and timing to optimize production. For example, a CNC-controlled pill presser can automatically adjust the pressure applied to each pill, ensuring uniformity and reducing waste.
Special Features
Some pill pressers come with integral features such as material feeders, which automate the loading of raw materials, or laser cutting systems for precise pill shaping. Multi-station pressers with rotary tools and turrets can perform multiple operations simultaneously, increasing efficiency. These features are particularly beneficial in high-volume production environments.
Energy Efficiency
Energy efficiency is an important consideration, especially for large-scale operations. Machines with energy-efficient motors and systems can significantly reduce operational costs. For example, a pill presser with a high-efficiency servo motor can reduce energy consumption by up to 30% compared to traditional motors.
Design
The design of a pill presser can impact its usability and integration into your production line.
Build Quality and Materials
High-quality materials such as stainless steel are preferred for their durability and resistance to corrosion. A well-built machine will have a longer lifespan and require less maintenance. For instance, a pill presser with a 304 series stainless steel body will be robust and easy to clean, essential for maintaining hygiene standards in pharmaceutical production.
Ergonomics
Ergonomic design features such as adjustable height and user-friendly interfaces can improve operator comfort and efficiency. Machines with touch-screen controls and intuitive software can reduce the learning curve and minimize the risk of operator error.
Footprint and Space Requirements
The physical size of the machine is also a critical factor, especially in facilities with limited space. Compact designs that offer high performance without occupying excessive floor space are ideal. For example, a pill presser with a small footprint but high output capacity can maximize production efficiency in a constrained environment.
Safety Standards and Certifications
Safety is a non-negotiable aspect of any pharmaceutical machinery. Ensuring that the pill presser complies with relevant safety standards and certifications is essential.
Compliance with International Standards
Compliance with standards such as the FDA’s Current Good Manufacturing Practice (CGMP) regulations and ISO certifications ensures that the machine is safe and suitable for pharmaceutical production. Machines that meet these standards have been rigorously tested for safety and performance.
Built-in Safety Features
Modern pill pressers often come equipped with safety features such as emergency stop buttons, safety guards, and overload protection. These features protect operators from injury and prevent damage to the machine. For instance, an emergency stop button can immediately halt the machine’s operation in case of a malfunction, preventing accidents.
Cost-Effectiveness and Budget
Cost-effectiveness is a crucial consideration, balancing initial investment with long-term operational costs.
Initial Setup Costs
The initial cost of a pill presser includes not only the purchase price but also installation and training expenses. High-end machines with advanced features may have higher upfront costs but can offer better performance and lower operational costs over time.
Operational and Maintenance Costs
Operational costs, including energy consumption, maintenance, and replacement parts, should be considered. Machines with higher energy efficiency and robust build quality can reduce these costs. For example, a pill presser with low-maintenance components and readily available spare parts will have lower long-term costs.
Resale Value
The resale value of the machine can also impact its overall cost-effectiveness. Machines from reputable manufacturers with good track records tend to retain their value better, providing a higher return on investment if you decide to upgrade or sell the equipment.
Innovations in Pill Presser Technology
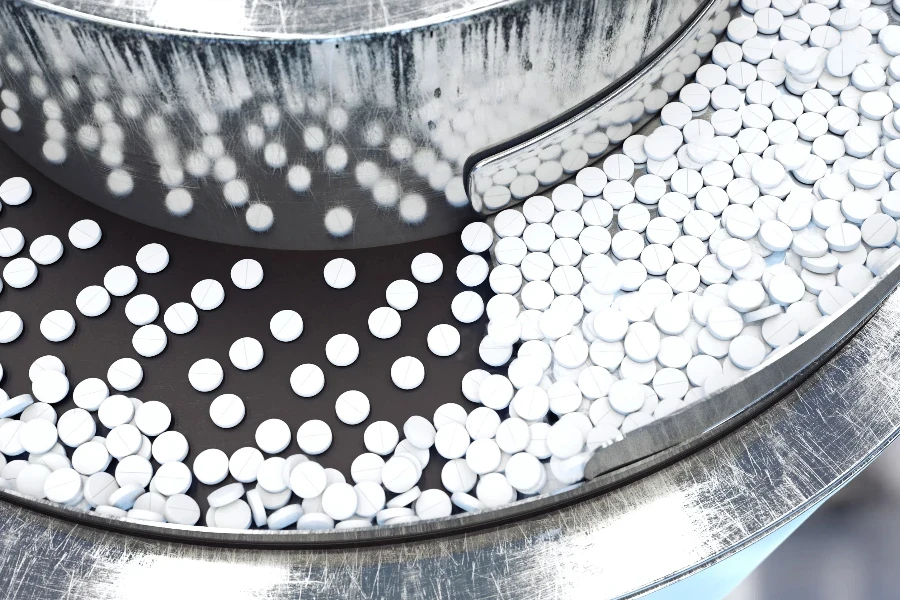
In recent years, technological advancements have significantly improved the efficiency, accuracy, and versatility of pill pressers. These innovations are shaping the future of pharmaceutical manufacturing.
Advanced Automation and AI Integration
The integration of advanced automation and artificial intelligence (AI) is revolutionizing pill pressing technology. AI can optimize the pressing process by analyzing data in real-time and making adjustments to parameters such as pressure and speed. This results in higher precision and consistency, reducing waste and improving product quality. AI-driven systems can also predict maintenance needs, minimizing downtime and extending the machine’s lifespan.
3D Printing and Customization
3D printing technology is being increasingly used to create custom molds for pill pressers. This allows for greater flexibility in pill design, enabling manufacturers to produce pills with complex shapes and unique branding elements. 3D-printed molds can be quickly produced and modified, reducing lead times and costs associated with traditional mold-making processes.
Internet of Things (IoT) Connectivity
IoT connectivity allows pill pressers to be integrated into a smart manufacturing ecosystem. Machines equipped with IoT sensors can communicate with other equipment and systems, providing real-time data on performance, production rates, and maintenance needs. This connectivity enables remote monitoring and diagnostics, improving operational efficiency and reducing the need for on-site technical support.
Regulatory Compliance and Quality Assurance
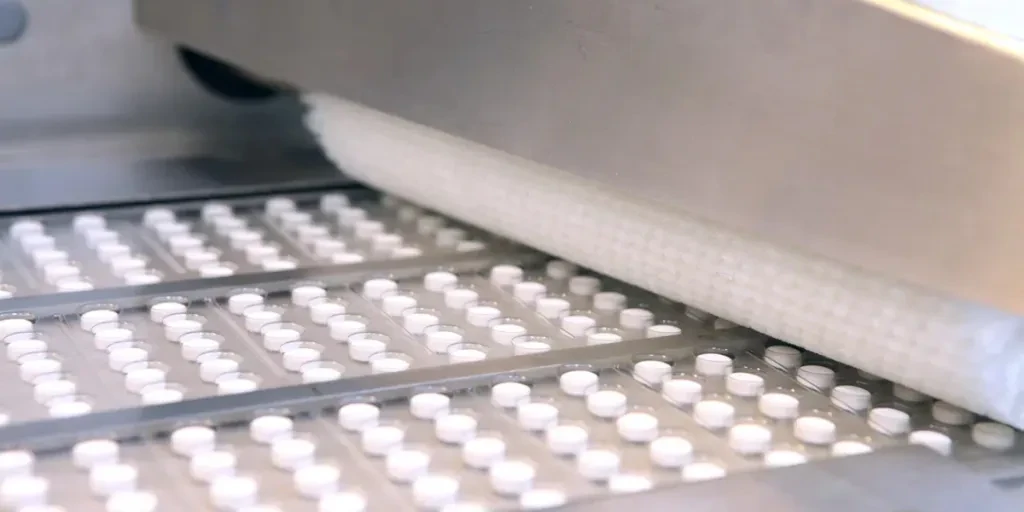
Ensuring regulatory compliance and maintaining high standards of quality are critical in the pharmaceutical industry. Pill pressers must adhere to stringent regulations to ensure the safety and efficacy of the products they produce.
FDA and CGMP Compliance
Compliance with the FDA’s CGMP regulations is mandatory for pharmaceutical manufacturers. These regulations cover all aspects of production, including the design, monitoring, and control of manufacturing processes and facilities. Pill pressers must be designed and operated in accordance with these regulations to ensure that the pills produced are safe and meet quality standards.
ISO Certifications
ISO certifications, such as ISO 9001 for quality management systems and ISO 13485 for medical devices, provide additional assurance of a machine’s quality and reliability. Manufacturers of pill pressers that hold these certifications have demonstrated their commitment to maintaining high standards of quality and regulatory compliance.
Quality Control and Testing
Rigorous quality control and testing procedures are essential to ensure the consistent performance of pill pressers. This includes regular calibration of the machine, inspection of the pills produced, and validation of the pressing process. Advanced testing methods, such as automated visual inspection systems, can detect defects and ensure that only high-quality pills reach the market.
Future Trends and Developments
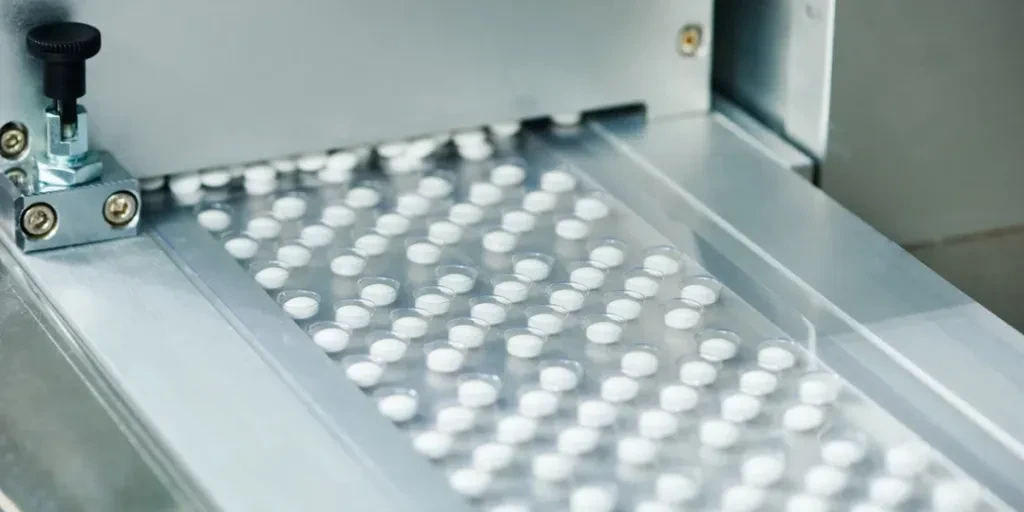
The pill presser industry is continuously evolving, with new trends and developments shaping the future of pharmaceutical manufacturing.
Sustainable Manufacturing Practices
Sustainability is becoming increasingly important in the pharmaceutical industry. Manufacturers are adopting eco-friendly practices, such as using energy-efficient machines and reducing waste. Pill pressers with low energy consumption and the ability to recycle materials are gaining popularity as companies strive to minimize their environmental impact.
Personalization and Precision Medicine
The trend towards personalized medicine is driving the need for more flexible and precise pill pressers. Machines that can produce small batches of customized pills with varying dosages and formulations are becoming essential. This shift towards precision medicine requires pill pressers to be highly adaptable and capable of producing a wide range of pill types.
Enhanced User Interfaces
User interfaces for pill pressers are becoming more intuitive and user-friendly. Touch-screen controls, interactive displays, and user-friendly software make it easier for operators to set up and monitor the pressing process. These enhancements reduce the learning curve and improve overall efficiency.
Final Thoughts
In summary, selecting the right pill presser involves careful consideration of various factors, including technical specifications, performance, design, safety standards, and cost-effectiveness. Advances in technology, such as AI integration, 3D printing, and IoT connectivity, are driving innovation in the industry. Ensuring regulatory compliance and maintaining high standards of quality are essential for the safe and effective production of pharmaceutical pills. As the industry continues to evolve, staying informed about the latest trends and developments will help you make the best choice for your manufacturing needs.