In 2025, the fluid bed dryer market is projected to hit USD 7.8 billion, driven by demand in food and pharmaceuticals. This article provides an in-depth analysis of selecting the right fluid bed dryer, focusing on performance, design, energy efficiency, and safety standards. Professional buyers will find valuable insights to make informed decisions and enhance operational efficiency.
Table of Contents:
-Market Overview: Fluid Bed Dryer Industry
-Detailed Introduction and Analysis of the Fluid Bed Dryer Market
-Key Factors When Selecting a Fluid Bed Dryer
-Latest Technological Advancements in Fluid Bed Dryers
-Practical Applications and Case Studies
-Final Thoughts
Market Overview: Fluid Bed Dryer Industry
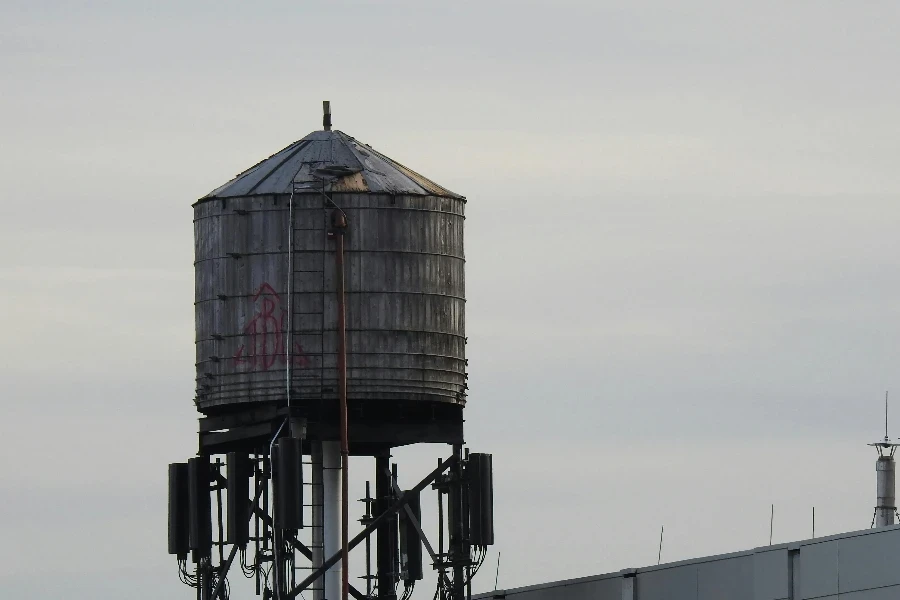
The global fluid bed dryer market has experienced substantial growth and is projected to continue expanding. By 2025, the market size for industrial dryers, including fluid bed dryers, is estimated to reach USD 7.8 billion, up from USD 5.6 billion in 2023. This reflects a compound annual growth rate (CAGR) of 3.75% from 2023 to 2032. This growth is largely driven by the food and beverage industry, which requires efficient drying methods for processed, dehydrated, and frozen food products.
Fluid bed dryers are widely used across various industries due to their efficiency in moisture removal and ability to handle diverse materials. The Asia-Pacific region holds the largest market share due to rapid industrialization, increasing demand for processed food products, and advancements in pharmaceutical technology. North America and Europe also have significant market shares, driven by strict regulatory frameworks and high demand for advanced drying technologies.
Major players in the market include Andritz AG, GEA Group Aktiengesellschaft, and Glatt GmbH. These companies are continually innovating to meet evolving industry needs. The introduction of advanced fluid bed dryers with enhanced energy efficiency and automation is expected to further drive market growth.
Detailed Introduction and Analysis of the Fluid Bed Dryer Market
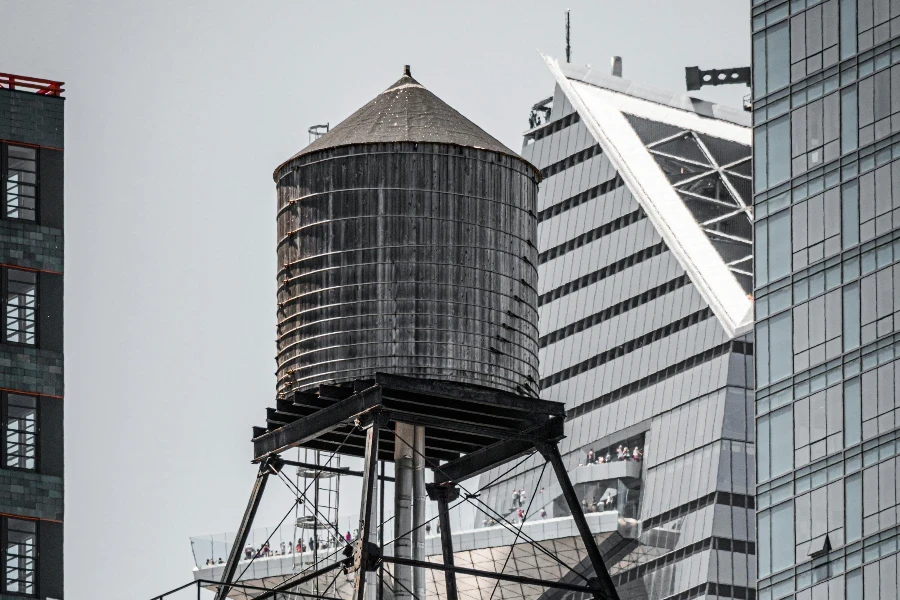
Fluid bed dryers work on the principle of fluidization, where hot air is passed through a perforated distributor to fluidize the material, achieving efficient drying. Key performance benchmarks include uniform drying, high thermal efficiency, and the ability to handle heat-sensitive materials. Fluid bed dryers are the most preferred type of industrial dryers, especially in the food, pharmaceutical, and chemical sectors.
Economic factors such as rising disposable incomes and increasing urbanization in emerging economies drive demand for processed and convenient food products, boosting the fluid bed dryer market. Shifts in consumer behavior towards high-quality, long-shelf-life products support this demand. Distribution channels are evolving, with a significant rise in online sales and direct procurement from manufacturers due to convenience and detailed product specifications.
Recent innovations in fluid bed dryers include IoT and automation integration for real-time monitoring and control, enhancing operational efficiency and reducing downtime. The product lifecycle stages of fluid bed dryers are evolving, with a focus on sustainable and energy-efficient designs to meet environmental regulations. Digitalization trends are leading to the development of smart dryers offering predictive maintenance and energy management features.
Manufacturers address customer pain points such as high initial investment costs and maintenance requirements by introducing cost-effective, low-maintenance models. Brand positioning strategies emphasize the reliability, efficiency, and sustainability of fluid bed dryers. Differentiation strategies include offering customized solutions tailored to specific industrial needs and providing comprehensive after-sales support.
Niche markets for fluid bed dryers include the pharmaceutical industry, with a high demand for precise drying solutions for active pharmaceutical ingredients (APIs) and excipients. The food processing industry also represents a significant niche market, requiring efficient drying of various food products to enhance shelf life and quality.
In summary, the fluid bed dryer market is set for continued growth, driven by technological advancements, increasing demand from key industries, and evolving consumer preferences. Manufacturers are focusing on innovation, sustainability, and customer-centric solutions to maintain a competitive edge in this dynamic market.
Key Factors When Selecting a Fluid Bed Dryer
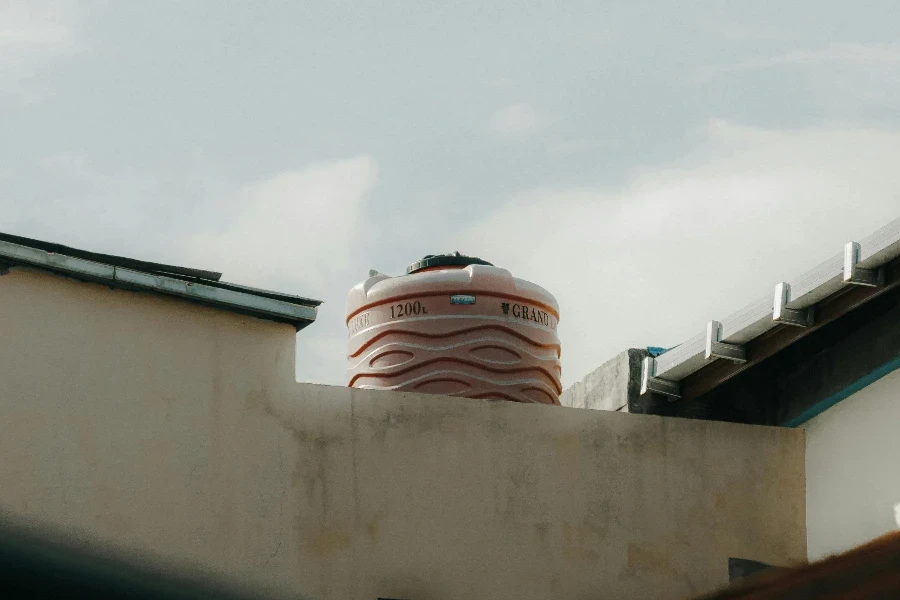
Selecting the right fluid bed dryer is crucial for ensuring optimal performance and efficiency in various industrial applications. Several key factors significantly impact the dryer’s effectiveness and suitability for specific processes.
Performance and Functionality
Performance and functionality are paramount when selecting a fluid bed dryer. The dryer must handle the required throughput and moisture content efficiently. Key performance metrics include drying time, moisture removal rate, and energy consumption. Fluid bed dryers provide uniform drying, essential for products needing consistent moisture content. The drying process suspends particles in a hot air stream, facilitating even heat distribution and efficient moisture evaporation. Advanced models may feature adjustable airflow rates and temperature controls for precise drying conditions tailored to specific materials.
Design and Technical Specifications
The design and technical specifications of a fluid bed dryer are critical to its performance. These specifications include the type of fluidization mechanism, material of construction, and overall size and capacity of the dryer. Fluid bed dryers can have different fluidization mechanisms, such as vibrating or static beds. Vibrating fluid bed dryers are ideal for materials that tend to agglomerate, as vibrations help break up clumps and ensure uniform drying. Static fluid bed dryers are suitable for free-flowing materials and offer simplicity in design and operation. The material of construction is crucial, especially when dealing with corrosive or abrasive materials. Stainless steel is commonly used for its durability and resistance to corrosion, ensuring a longer lifespan for the equipment. The size and capacity of the dryer should align with production requirements, ensuring it can handle the anticipated load without compromising efficiency.
Energy Efficiency and Environmental Impact
Energy efficiency is a critical factor in selecting a fluid bed dryer, as it directly affects operational costs and environmental impact. Modern fluid bed dryers are designed with energy-saving features such as heat recovery systems and optimized airflow patterns to minimize energy consumption. Heat recovery systems capture and reuse heat from the exhaust air, reducing the overall energy demand of the drying process. Advanced control systems allow for precise regulation of airflow and temperature, further enhancing energy efficiency. Environmental considerations are also important, particularly in industries with stringent regulatory requirements. Fluid bed dryers with advanced filtration systems minimize the release of dust and other particulates into the environment, ensuring compliance with environmental standards.
Safety Standards and Certifications
Safety is a paramount concern in the operation of fluid bed dryers. It is essential to select equipment that meets relevant safety standards and certifications to protect operators and the facility. Fluid bed dryers should have safety features such as explosion-proof designs, emergency shut-off systems, and temperature monitoring controls. These features help prevent accidents and ensure safe operation, especially when dealing with flammable or hazardous materials. Certifications from recognized bodies like the Occupational Safety and Health Administration (OSHA) and the European Union’s ATEX directive assure that the equipment meets stringent safety standards. Compliance with industry-specific standards, such as those from the Food and Drug Administration (FDA) for food processing applications, ensures the dryer is suitable for specific use cases.
Cost and Budget Considerations
The cost of a fluid bed dryer is a significant factor in the selection process. It is important to consider not only the initial purchase price but also the total cost of ownership, including maintenance, energy consumption, and potential downtime. While high-end models with advanced features may come with a higher price tag, they can offer long-term savings through improved efficiency and reduced maintenance costs. Evaluating the return on investment (ROI) by considering the potential benefits of enhanced performance, energy savings, and reduced operational costs is essential. Budget constraints should be balanced with the need for reliability and performance. Investing in higher-quality equipment may be beneficial to avoid frequent repairs and replacements, which can be costly in the long run.
Latest Technological Advancements in Fluid Bed Dryers
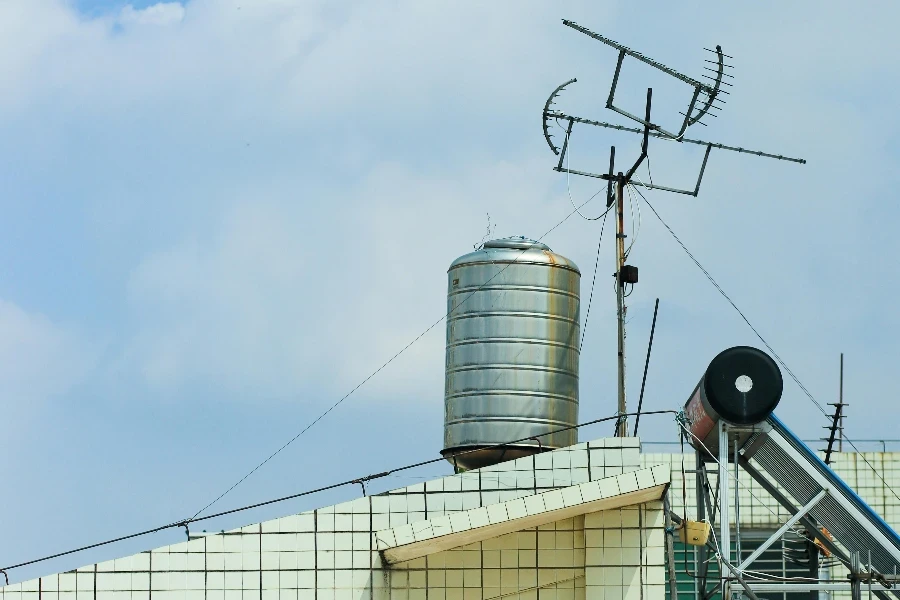
The fluid bed dryer industry has seen significant technological advancements in recent years, enhancing the efficiency, versatility, and safety of these machines. These advancements are driven by the need for more energy-efficient, environmentally friendly, and user-friendly equipment.
Advanced Control Systems
One notable advancement in fluid bed dryers is the integration of advanced control systems. These systems allow for precise regulation of drying parameters such as temperature, airflow, and humidity, ensuring optimal drying conditions for different materials. Modern control systems often include programmable logic controllers (PLCs) and human-machine interfaces (HMIs), providing operators with real-time data and the ability to adjust settings easily. This level of control enhances the efficiency and consistency of the drying process, reducing the risk of over-drying or under-drying.
Heat Recovery and Energy Efficiency
Energy efficiency remains a key focus in the development of fluid bed dryers. Newer models are equipped with heat recovery systems that capture and reuse heat from the exhaust air, significantly reducing energy consumption. These systems often incorporate advanced heat exchangers and thermal insulation materials to maximize heat retention and minimize energy loss. Some models feature variable frequency drives (VFDs) that adjust the speed of fans and blowers based on the drying requirements, further enhancing energy efficiency.
Enhanced Filtration and Environmental Compliance
Environmental compliance is increasingly important in the fluid bed dryer industry, particularly in regions with strict emission regulations. Advanced filtration systems are now commonly integrated into fluid bed dryers to capture dust and other particulates, ensuring cleaner exhaust air. These filtration systems may include high-efficiency particulate air (HEPA) filters and baghouse dust collectors, providing high levels of filtration efficiency. Some models feature automated cleaning mechanisms that maintain filter performance and reduce maintenance requirements.
Modular and Customizable Designs
To meet the diverse needs of different industries, fluid bed dryers are now available in modular and customizable designs. These designs allow for easy integration into existing production lines and the flexibility to adapt to changing process requirements. Modular fluid bed dryers can be configured with various options such as different fluidization mechanisms, heat sources, and control systems. This flexibility enables manufacturers to tailor the equipment to their specific needs, ensuring optimal performance and efficiency.
Industry 4.0 and IoT Integration
The integration of Industry 4.0 and Internet of Things (IoT) technologies is transforming the fluid bed dryer industry. These technologies enable remote monitoring and control of fluid bed dryers, providing real-time data on equipment performance and process conditions. IoT-enabled fluid bed dryers can be connected to central monitoring systems, allowing operators to track performance metrics, receive alerts for maintenance issues, and optimize the drying process based on data analytics. This level of connectivity enhances operational efficiency and reduces the risk of downtime.
Practical Applications and Case Studies
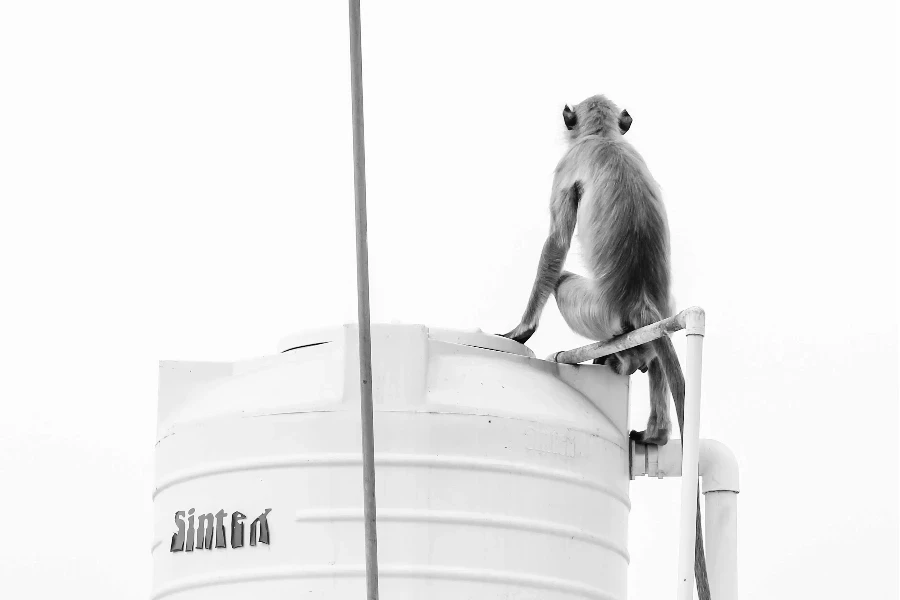
Fluid bed dryers are used in a wide range of industries, from pharmaceuticals and food processing to chemicals and minerals. Understanding the practical applications and benefits of fluid bed dryers can help in selecting the right equipment for specific needs.
Pharmaceutical Industry
In the pharmaceutical industry, fluid bed dryers are commonly used for drying granulated materials and active pharmaceutical ingredients (APIs). The uniform drying provided by fluid bed dryers ensures consistent moisture content, which is critical for maintaining the stability and efficacy of pharmaceutical products. A case study from a leading pharmaceutical company demonstrated the benefits of using a fluid bed dryer for drying a heat-sensitive API. The company reported a significant reduction in drying time and energy consumption, along with improved product quality and batch consistency.
Food Processing Industry
Fluid bed dryers are also widely used in the food processing industry for drying various products such as cereals, grains, and spices. The gentle drying process helps to preserve the nutritional content and sensory properties of food products. A food processing company specializing in dehydrated vegetables implemented a fluid bed dryer to replace an older drying system. The new dryer provided faster drying times and improved energy efficiency, resulting in cost savings and higher production throughput.
Chemical Industry
In the chemical industry, fluid bed dryers are used for drying powders, granules, and other bulk materials. The ability to handle a wide range of particle sizes and moisture levels makes fluid bed dryers suitable for various chemical processes. A chemical manufacturer used a fluid bed dryer to dry a hygroscopic powder that was prone to clumping. The fluid bed dryer provided uniform drying and prevented clumping, improving the handling and packaging of the final product.
Final Thoughts
Selecting the right fluid bed dryer involves considering various factors such as performance, design, energy efficiency, safety standards, and cost. By understanding the latest technological advancements and practical applications, manufacturers can make informed decisions to enhance their drying processes and achieve optimal results.