Polypropylene (PP), as one of the five general-purpose plastics, is widely used in various industries. However, the flammable property of PP limits its application and hinders the further development of the material, so people have been concerned about the flame retardant modification of PP.
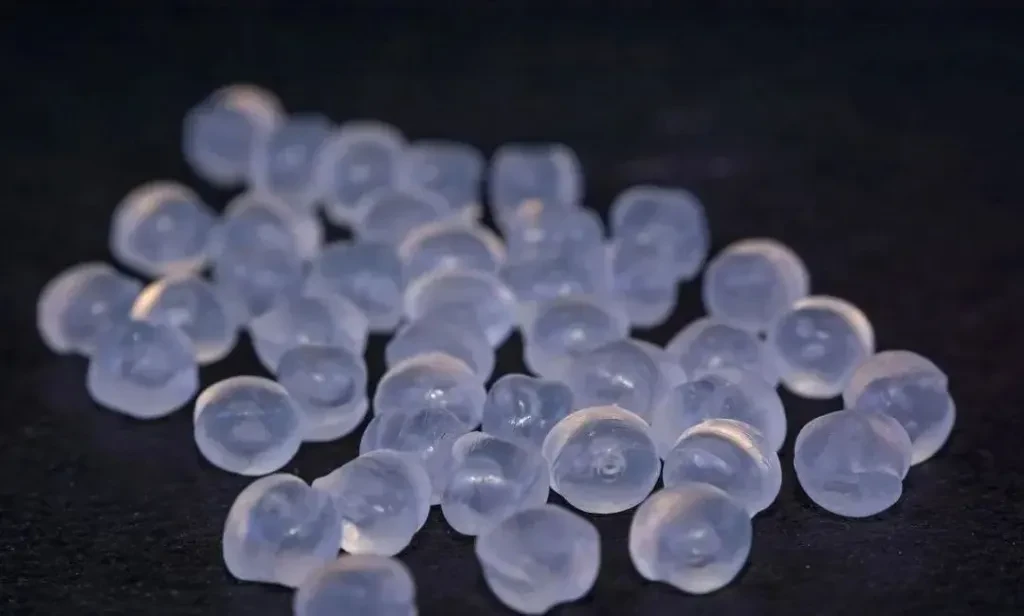
Polymer materials are polymer compounds containing elements such as carbon, hydrogen and oxygen, most of which are combustible. The combustion of polymer materials is a series of physical changes and chemical reactions of the integrated process, showing special phenomena such as melting and softening, volume changes. The combustion process consists of three steps:
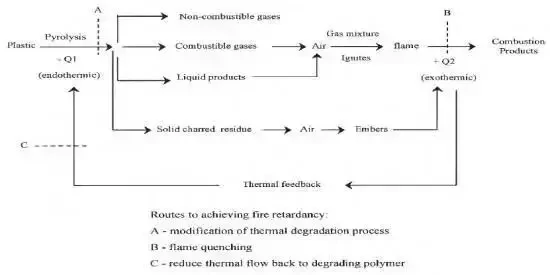
Firstly, the thermal decomposition reaction produces small molecules of gas, then the gas mixture reaches the combustion conditions to trigger a violent chemical reaction, and finally, the rapid combustion of the combustible gas mixture produces a large amount of heat, and the cycle of reaction continues.
Since PP has an oxygen index of only 17.4, it is flammable and generates a large amount of heat during combustion, which can easily cause fires and pose a threat to life and property. In the field of electronics and electrical appliances, the flammability of PP restricts its wider application, so it is necessary to carry out flame-retardant treatment for PP materials.
Flame retardant mechanism
The flame retardant mechanism mainly includes chain reaction termination mechanism, surface isolation mechanism and interrupted heat exchange mechanism. The chain reaction termination mechanism terminates the combustion reaction by consuming HO- produced during the combustion process, the surface isolation mechanism generates solid compounds to block air contact, and the interrupted heat exchange mechanism absorbs the heat of combustion to achieve self-extinction.
The activated carbon in the metal hydroxide flame retardant can effectively combine with magnesium hydroxide to reduce the possibility of agglomeration, improve the compatibility with the PP matrix, and enhance the flame retardancy of the material. The ratio and activation degree of the flame retardant were adjusted by testing the change of oil absorption value, and it was finally found that the limiting oxygen index reached a maximum value of 28.9% when 25 wt% activated carbon modified magnesium hydroxide flame retardant was added to PP.

Metal hydroxide flame retardants are additives used to improve the flame retardancy of polypropylene (PP) materials. In order to further enhance the mechanical strength of the material, the researchers also introduced polyolefin elastomer (POE) and calcium carbonate nanoparticles (CaCO3) into it. The results showed that the modified PP composites not only possessed excellent flame retardant properties, but also exhibited high mechanical strength.
Boron flame retardants
Boron flame retardants play an important role in PP/BN@MGO composites. Due to the encapsulated structure and alkylation modification of the BN@MGO flame retardant, the carbon element can be enriched on the surface of the filler, which enhances the affinity with the PP body and enables it to be uniformly distributed in the PP matrix.
Meanwhile, the modified treated BN@MGO has a zigzag path effect and high thermal stability, which results in a material with a low coefficient of thermal expansion and high flame retardancy. These properties allow PP/BN@MGO composites to have a wide range of applications in the fields of efficient heat dissipation electronic devices, household appliances and thermal management.
In addition, when the boron flame retardant APP/MCA-K-ZB was added at 25 wt% (APP/MCA-K-ZB mass ratio of 3/1), the PP composite could achieve the V-0 rating in UL-94 test, while the limiting oxygen index was as high as 32.7%. Thermogravimetric analysis (TGA) and scanning electron microscopy (SEM) test results show that the addition of APP/MCA-K-ZB can form a dense graphite carbon layer, which effectively protects the PP matrix underneath from further combustion, and improves the material’s thermal stability and carbon formation capability.
Silicon flame retardants
HNTs-Si in silicone flame retardants can maintain the original tubular structure and twist with the thermally degraded PP chain to form a dense carbon layer, which effectively inhibits the heat, mass and smoke transfer during PP combustion. Polysiloxane can reduce the polarity of the surface of HNTs-Si, increasing the compatibility with the PP substrate, and the crack bridging effect in turn improves the ductility of PP composites.
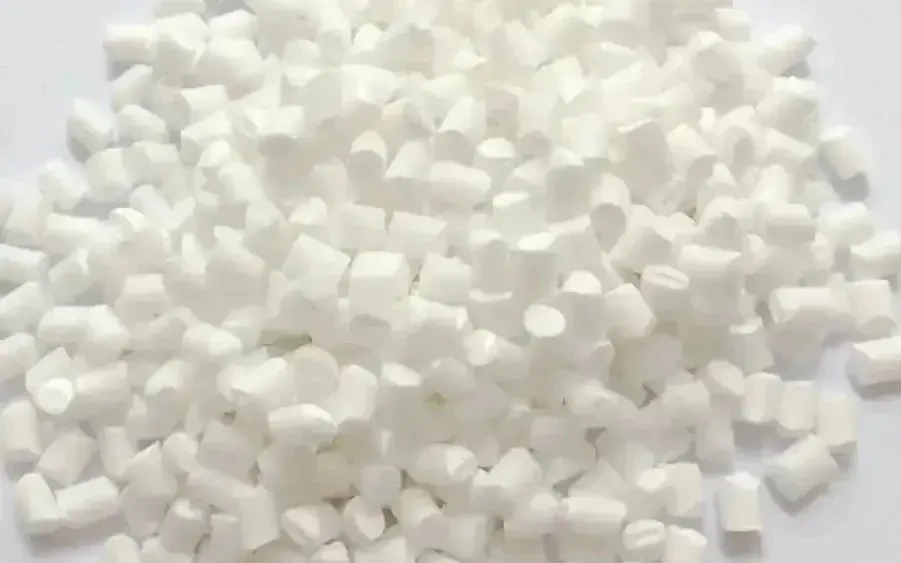
In addition, among the silica-based flame retardants, nano-Sb2O3 and OMMT can form a dense carbon layer after modification, which effectively improves the thermal stability and flame retardancy of PP-based composites. The heterogeneous nucleation of OMMT and nano-Sb2O3 in the PP matrix can improve the crystallinity and tensile strength of the materials.
Phosphorus flame retardants
Sorbitol and ammonium polyphosphate in phosphorus flame retardants can form a carbonised layer to retard heat propagation and improve the flame retardancy of the material. The combined effect of SPDEB and ammonium polyphosphate can effectively improve the flame retardancy of PP materials and reduce the emission of flammable gases.
Nitrogen-based flame retardants
MPP and AP in nitrogen-based flame retardants can release non-combustible gases and phosphorus-containing substances, dilute the combustible gases in the air, and act as gas shielding, thus reducing combustion. Supramolecular self-assembly methods can use non-covalent bonds to synthesise compounds with specific structures, improve the dispersion of flame retardants in materials and enhance flame retardancy.
Intumescent flame retardant
NiCo2O4 is an intumescent flame retardant with the advantages of controllable morphology, large specific surface area, multiple active sites, and easy and diverse preparation methods. As a nickel-based compound, it exhibits excellent carbon-catalytic ability, which both reduces the combustion products and improves the flame retardancy of the material.
This superiority mainly stems from the role of Ni+ ions in it, which can accelerate the thermal decomposition of polyethylene acrylate (PER), enhance the charring of ammonium polyphosphate, and promote the formation of expanded char layer in polypropylene (PP)/intumescent flame retardant system. Meanwhile, the bimetallic oxides are stable at high temperatures and have strong catalytic ability, which helps to make the PP/expanded flame retardant composite form a dense and uniform char layer and improve the thermal stability of the char layer and char residue.
In addition, the flower-like NiCo2O4 structure has a large number of folds on the surface and a large and rough contact area with the polymer, which enhances the bonding. This flower-like structure has strong stability, which helps to avoid damage during processing and maintains the integrity of the structure. During the combustion process, the charcoal-forming substances can be fixed between the flower-like structure, which improves the stability of the charcoal layer and effectively performs the role of barrier to achieve the flame retardancy and protection of the substrate.
In addition to NiCo2O4, there are a number of other key components that play an important role in the flame retardant effect. The SiO2 gel-treated OS-MCAPP acts as both a gas and acid source and helps PP to form a protective char layer that protects the PP matrix from further decomposition. PEIC, as an excellent char source, plays a key role in the formation of high-quality expanded char and facilitates the acquisition of flame-retardant composites.
PPA-C reacts with PER during combustion to form P-O-C bonds and P-C bonds, which contribute to the formation of a virtually defect-free char layer. In addition, PPA-C can cause PP to thermally decompose earlier and produce more char residue at higher temperatures. There is a good synergy between PPA-C and PER, and the flame retardancy of the PPA-C/PER system is superior to that of the conventional APP/PER system. When the content of PPA-C/PER (3:1) reaches 18wt%, the PP/intumescent flame retardant composite material reaches V-0 rating by UL-94 test, and the ultimate oxygen index can reach 28.8%.
Flame retardant PP materials for packaging applications
PP plastic has low density, good transparency, non-toxic and odourless, easy processing and moulding, low price and other characteristics, which makes it has a huge potential for application in the field of packaging. However, the defects of PP plastic such as flammability and poor high temperature resistance have limited its development in the field of packaging. Therefore, in recent years, many scholars have devoted themselves to the study of PP packaging materials with high flame retardant properties.
Car battery housing
Batteries are one of the key components of new energy vehicles, so a battery casing that protects the battery safely is crucial. Traditional battery packaging mainly uses metal materials and sheet moulding compound (SMC) materials, but the complexity and density of the moulding process of these materials affect the lightweighting of new energy vehicles. Therefore, attention is being paid to PP materials with low density and good impact resistance.
A PP material with flame-retardant properties prepared from a PP resin matrix, an ammonium polyphosphate/triazine complex system as a flame retardant, an ethylene-octene copolymer, a propylene-based elastomer, and an EPDM adhesive as a toughening agent was used in new energy automobile battery housings. This PP material maintains low density and has good flame retardant properties and impact strength, as well as good sealing and waterproofing properties.
Component packaging
PP/MHSH/Al2O3/N-P composites were prepared by melt blending method by modifying alkaline magnesium sulfate whisker (MHSH) and alumina (Al2O3) with cross-linking agent KH-550, and adding nitrogen-phosphorus complex flame retardant and PP matrix, and further processed to form films.
The nitrogen-phosphorus complex flame retardant not only promotes the formation of an expanded carbon layer in the PP matrix at high temperature, but also reacts with MHSH to generate magnesium phosphate salt, which improves the strength of the expanded carbon layer.The addition of Al2O3 improves the thermal conductivity of the material, so that the internal heat is rapidly transferred to the surface, which serves as heat dissipation and improves the heat resistance. In addition, MHSH and Al2O3 acted as rigid fillers to improve the mechanical properties of the PP/MHSH/Al2O3/N-P composite film. Therefore, the PP/MHSH/Al2O3/N-P composite film has excellent flame retardant properties and high mechanical strength.
Food container
PP composites with high flame retardant properties were prepared by melt blending of IFR consisting of ammonium polyphosphate, triazine carbon forming agent and co-effector with clean treated recycled polypropylene lunch boxes, demonstrating the potential of recycling PP lunch boxes.
Issues with PP flame retardancy
Although more and more people are beginning to study flame retardant PP composites, there are currently some problems:
1. flame retardant additive, poor compatibility with the matrix, affecting the mechanical properties of the material;
2. Efficient flame retardants mostly contain halogens and do not meet the environmental requirements;
3. Flame retardants are expensive, increasing production costs.
Disclaimer: The information set forth above is provided by Shanghai Qishen Plastic Industry independently of Alibaba.com. Alibaba.com makes no representation and warranties as to the quality and reliability of the seller and products.