In the realm of welding, the flux core welder emerges as a pivotal tool, offering a blend of versatility, efficiency, and accessibility that appeals to both seasoned welders and novices alike. This article delves into the essence of flux core welding, exploring its fundamentals, advantages, applications, maintenance tips, and safety guidelines. By breaking down complex concepts into digestible explanations, we aim to provide you with a comprehensive understanding of flux core welders, empowering you to make informed decisions about incorporating this tool into your projects.
Table of Contents:
– Understanding flux core welding
– Advantages of using a flux core welder
– Common applications of flux core welders
– Maintenance tips for your flux core welder
– Safety guidelines for flux core welding
Understanding flux core welding
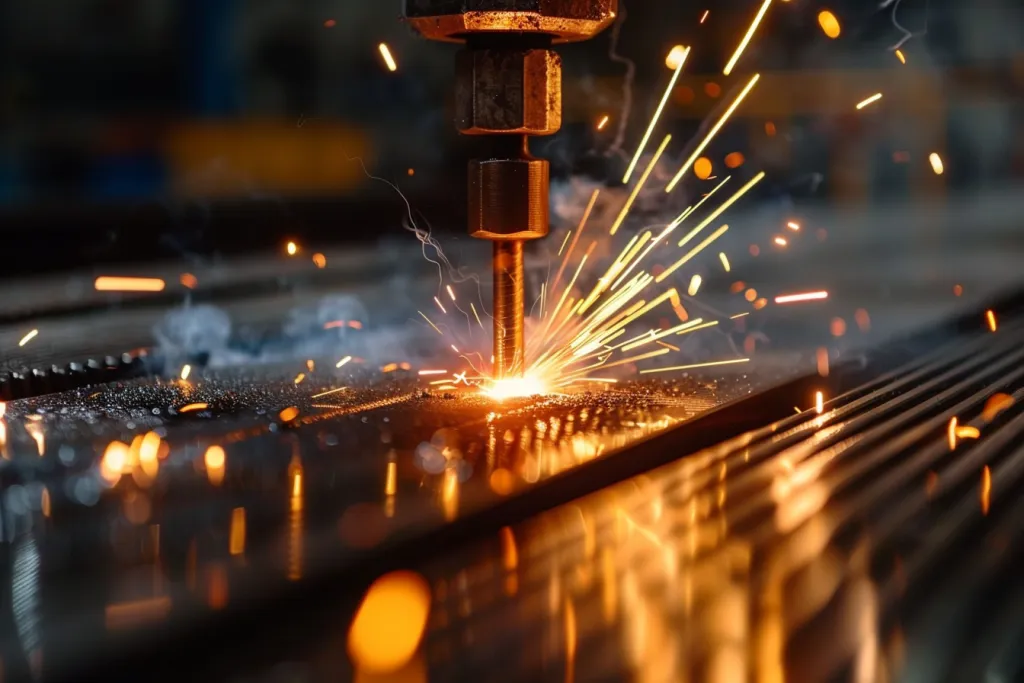
Flux core welding, a semi-automatic or automatic arc welding process, has gained prominence due to its efficiency and adaptability. This method utilizes a tubular wire filled with flux to facilitate the welding process, eliminating the need for a shielding gas. It’s particularly effective in outdoor conditions, where wind might disperse a gas shield, making it a reliable option in less than ideal environments.
The core of the wire contains various compounds that, when melted, form a gas shield around the weld, preventing contamination. This process also produces slag which covers the weld, offering further protection as it cools and solidifies. Understanding these mechanics is crucial for mastering flux core welding, as it influences the choice of materials and settings for optimal results.
Moreover, flux core welding is renowned for its deep penetration capabilities, making it suitable for welding thicker materials. Its efficiency in various positions – overhead, vertical, or flat – adds to its versatility, catering to a wide range of welding needs.
Advantages of using a flux core welder
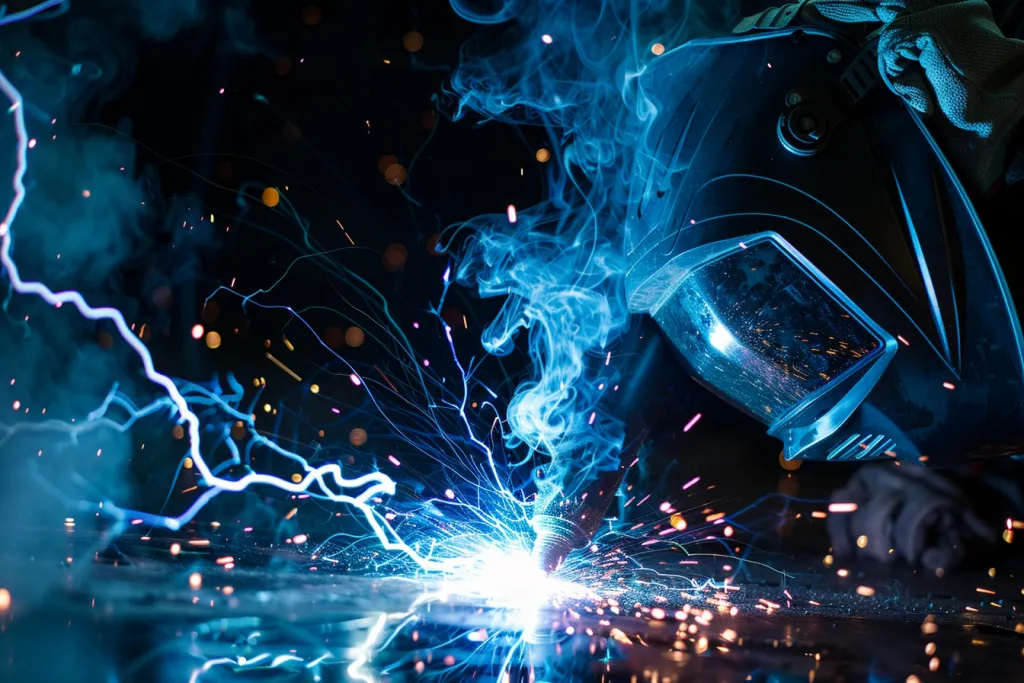
The flux core welder stands out for its numerous benefits, offering a compelling choice for many welders. One of its primary advantages is the high welding speed, which significantly boosts productivity. This is particularly beneficial in industrial settings where time is of the essence.
Another notable benefit is its portability. Unlike traditional welding methods that require gas tanks and complex setups, a flux core welder only needs power and its welding wire to operate. This makes it an ideal tool for on-site repairs and projects where mobility is crucial.
Furthermore, the ability to weld in challenging environments, including outdoors or in windy conditions, without the need for a gas shield, ensures that projects can proceed without delay, regardless of the weather. This resilience makes flux core welders a valuable asset in any welder’s toolkit.
Common applications of flux core welders
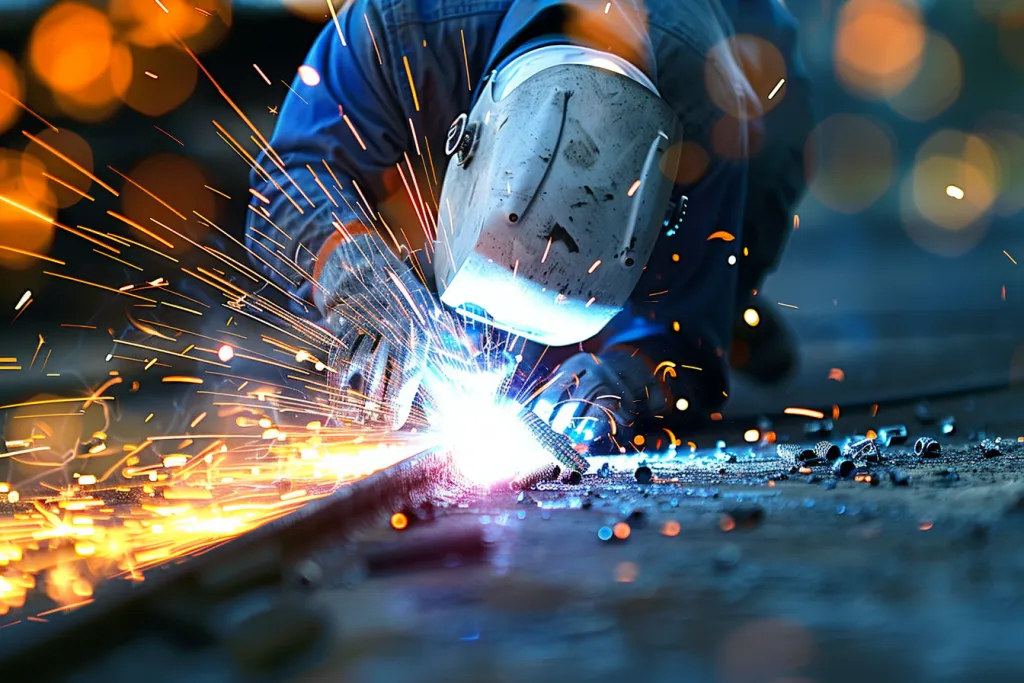
Flux core welders find their place in a variety of applications, showcasing their adaptability across industries. In the construction sector, they are instrumental in fabricating and repairing heavy machinery and steel structures, thanks to their deep penetration and strong welds.
Automotive repair is another area where flux core welding shines. It allows for quick and efficient repairs of vehicle frames and body parts, making it a preferred method for many mechanics.
Additionally, in the realm of art and custom fabrication, the versatility of flux core welders enables artists and fabricators to work with a range of materials and thicknesses, bringing their creative visions to life with precision and durability.
Maintenance tips for your flux core welder
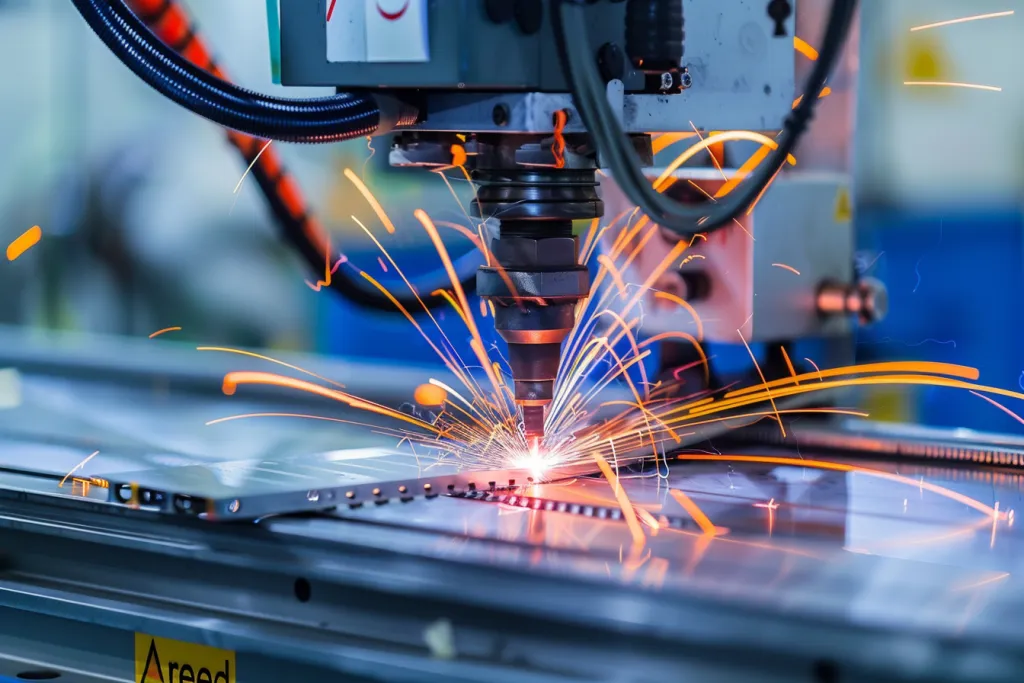
Maintaining a flux core welder is essential for ensuring its longevity and performance. Regularly cleaning the welder, especially the wire feeder and gun, is crucial for preventing blockages and ensuring smooth operation. It’s also important to check and replace the contact tip and nozzle as needed, as wear and tear can affect welding quality.
Using high-quality flux-cored wire and ensuring it’s properly stored to avoid moisture absorption will also contribute to optimal welding results. Moreover, periodically checking the welder’s electrical connections and cables for signs of wear can prevent potential hazards and downtime.
Safety guidelines for flux core welding
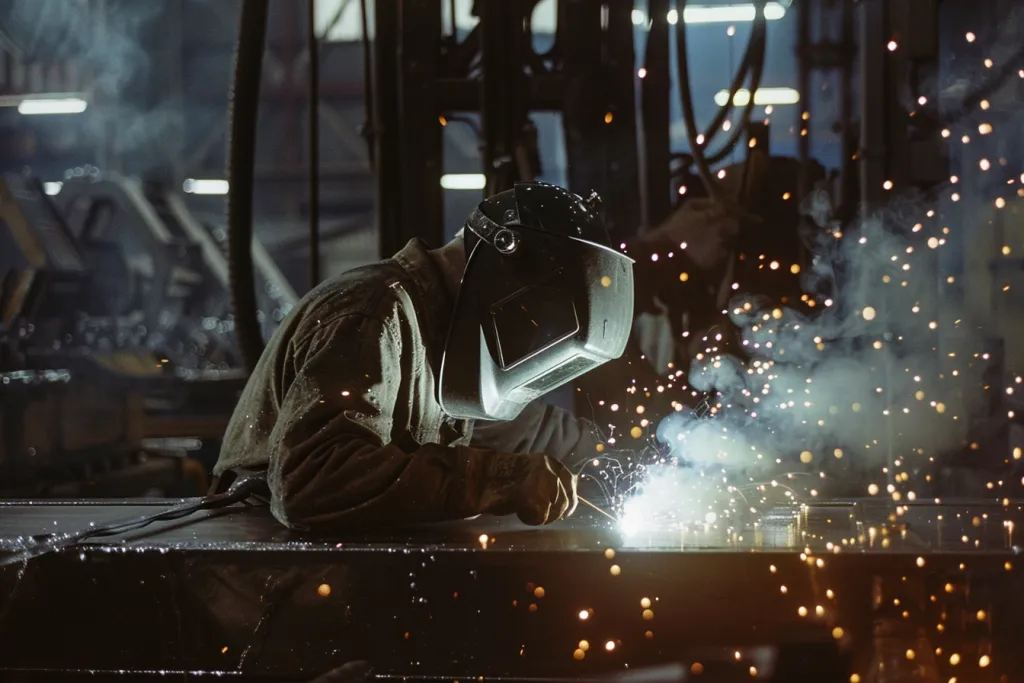
Safety is paramount in welding, and flux core welding is no exception. Wearing the appropriate personal protective equipment (PPE), including a welding helmet with proper shading, gloves, and fire-resistant clothing, is non-negotiable. Ensuring good ventilation in the workspace is also critical to avoid inhaling fumes and gases produced during welding.
Being aware of your surroundings and removing any flammable materials from the vicinity can prevent accidents. Additionally, regularly inspecting the welder for any signs of damage and adhering to the manufacturer’s guidelines will further enhance safety during operation.
Conclusion:
Flux core welders offer a compelling blend of versatility, efficiency, and ease of use, making them a valuable tool in various welding applications. By understanding their operation, benefits, and maintenance requirements, and adhering to safety guidelines, you can harness the full potential of flux core welding in your projects. Whether you’re a seasoned professional or a beginner, incorporating a flux core welder into your toolkit can elevate your welding capabilities and open up new possibilities in your work.