In the realm of industrial machinery, the extractor stands out as a cornerstone piece of equipment across a wide range of sectors. From the pharmaceutical to the food and chemical industries, the role of an extractor is pivotal in separating components efficiently and effectively. This article aims to demystify extractors, shedding light on their operation, types, maintenance, safety considerations, and future trends. By understanding these aspects, users can make informed decisions tailored to their specific needs, ensuring optimal performance and longevity of their machinery.
Table of Contents:
– What is an extractor and how does it work?
– Different types of extractors and their applications
– Maintenance tips for long-lasting extractor performance
– Safety considerations when operating an extractor
– Future trends in extractor technology
What is an extractor and how does it work?
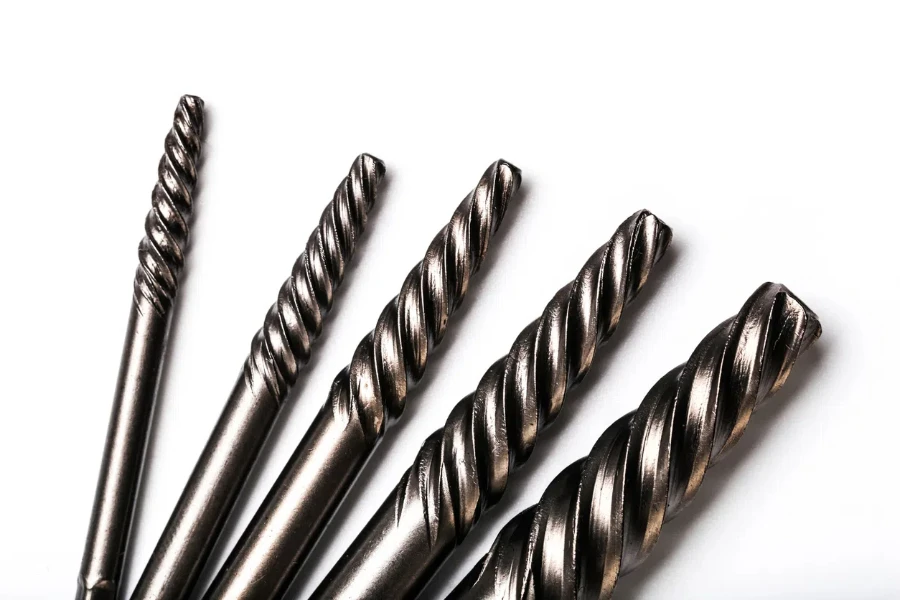
Extractors are specialized machinery designed for the separation of mixtures. They operate on the principle of transferring a solute from one solvent to another, a process that is fundamental in numerous manufacturing and processing industries. The effectiveness of an extractor hinges on its ability to capitalize on differences in solubility, density, or chemical affinity, allowing for precise separation and purification tasks.
The core mechanism involves two phases: the feed, containing the mixture to be separated, and the solvent, which is chosen based on its ability to dissolve the desired component. The interaction between these two phases, facilitated by the extractor’s design, results in the transfer of the targeted solute into the solvent phase. This process not only highlights the versatility of extractors but also underscores their efficiency in extracting valuable components from complex mixtures.
Understanding the operational intricacies of extractors is crucial for optimizing their performance. Factors such as temperature, pressure, and the nature of the solute and solvent play significant roles in determining the outcome of the extraction process. By mastering these variables, users can enhance the efficiency and yield of their extraction operations.
Different types of extractors and their applications
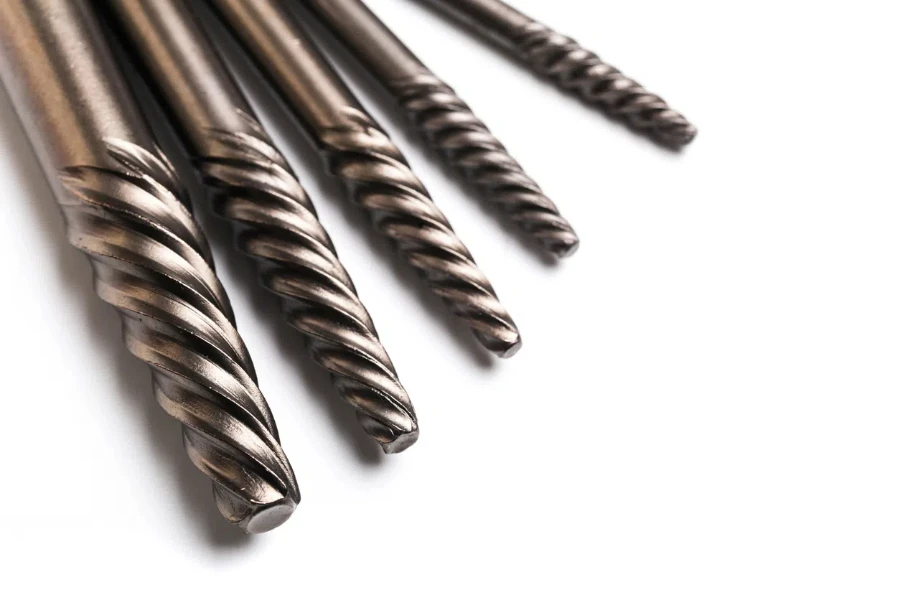
Extractors come in various designs, each tailored to specific applications and industries. The most common types include rotary, Soxhlet, and centrifugal extractors, among others. Each type has its unique mechanism and is chosen based on the specific requirements of the task at hand.
Rotary extractors, for instance, are favored in industries where large volumes of liquid need to be processed continuously. Their design allows for the efficient separation of solutes from liquids, making them ideal for the food, beverage, and pharmaceutical sectors. On the other hand, Soxhlet extractors are indispensable in laboratories for the selective extraction of compounds from solid materials, demonstrating the adaptability of extractors to diverse operational needs.
The choice of an extractor type is influenced by several factors, including the nature of the mixture, desired purity levels, and the scale of operation. By selecting the appropriate extractor, users can achieve optimal results, whether in research and development settings or large-scale industrial applications.
Maintenance tips for long-lasting extractor performance
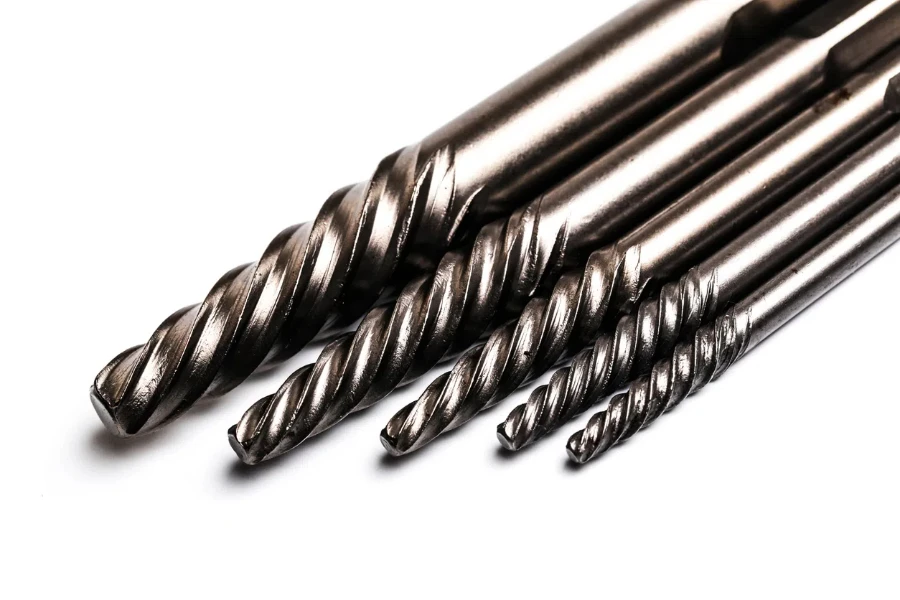
Maintaining an extractor in optimal condition is essential for ensuring its longevity and reliability. Regular maintenance routines can prevent breakdowns, extend the equipment’s life span, and maintain its efficiency. Key maintenance practices include regular cleaning, inspection, and replacement of worn-out parts.
Cleaning is paramount, as residue buildup can affect the extractor’s performance and the quality of the extracted product. Depending on the type of extractor and the materials processed, specific cleaning protocols should be followed to ensure thorough removal of residues and contaminants.
Inspection and monitoring of the extractor’s components allow for the early detection of potential issues, such as wear and tear or operational anomalies. Timely intervention can prevent minor problems from escalating into major failures, safeguarding the extractor’s functionality.
Adhering to a scheduled maintenance plan, tailored to the extractor’s operational demands and environmental conditions, is crucial. This proactive approach not only enhances the extractor’s performance but also contributes to safety and regulatory compliance.
Safety considerations when operating an extractor
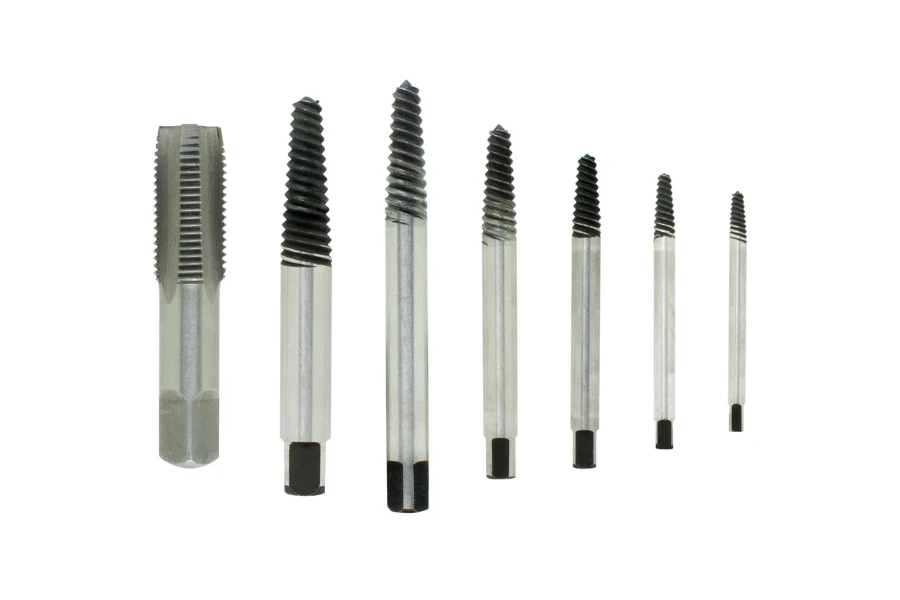
Operating extractors, like any industrial machinery, involves inherent risks. Awareness and adherence to safety protocols are vital for protecting operators and ensuring a safe working environment. Key safety considerations include proper training, use of personal protective equipment (PPE), and adherence to operational guidelines.
Proper training ensures that operators are familiar with the extractor’s functions, potential hazards, and emergency procedures. This knowledge is fundamental in preventing accidents and responding effectively in case of emergencies.
The use of appropriate PPE, such as gloves, goggles, and protective clothing, is essential for minimizing exposure to hazardous materials and protecting operators from injuries. Ensuring that safety equipment is readily available and in good condition is a responsibility that cannot be overlooked.
Adherence to operational guidelines and safety regulations is mandatory. This includes conducting regular safety audits, maintaining clear and accessible emergency exits, and keeping fire extinguishers and other safety equipment in strategic locations.
Future trends in extractor technology

The evolution of extractor technology is driven by the pursuit of efficiency, sustainability, and adaptability. Innovations in design, materials, and control systems are shaping the future of extractors, making them more versatile, energy-efficient, and environmentally friendly.
Advancements in materials science are leading to the development of extractors that can withstand harsher conditions, such as extreme temperatures and corrosive environments. This enhances their applicability across a broader range of industries and processes.
Control systems are becoming more sophisticated, allowing for precise manipulation of operational parameters. This not only improves the efficiency and yield of the extraction process but also enables real-time monitoring and automation, reducing the need for manual intervention.
Sustainability is a driving force behind recent innovations, with a focus on reducing energy consumption, minimizing waste, and utilizing eco-friendly materials. These developments reflect a growing recognition of the environmental impact of industrial processes and a commitment to mitigating these effects.
Conclusion:
Extractors play a critical role in numerous industries, facilitating the efficient separation of components with precision and reliability. Understanding the operation, types, maintenance, safety considerations, and future trends of extractors empowers users to optimize their use and adapt to evolving demands. As technology advances, the versatility and efficiency of extractors will continue to expand, offering new opportunities for innovation and sustainability in industrial processes.