In the realm of machinery, mixers stand out as pivotal equipment across various industries, from food and beverage to construction. Understanding the intricacies of these machines can significantly impact productivity and efficiency. This article aims to demystify mixers, focusing on the aspects users care most about: types, features, applications, maintenance, and safety. By breaking down these complex concepts, we provide a clear, authoritative guide designed to empower you with knowledge and practical insights.
Table of Contents:
– Different types of mixers and their applications
– Key features to look for in a mixer
– The role of mixers in various industries
– Maintenance tips for long-lasting mixer performance
– Safety protocols for operating mixers
Different types of mixers and their applications
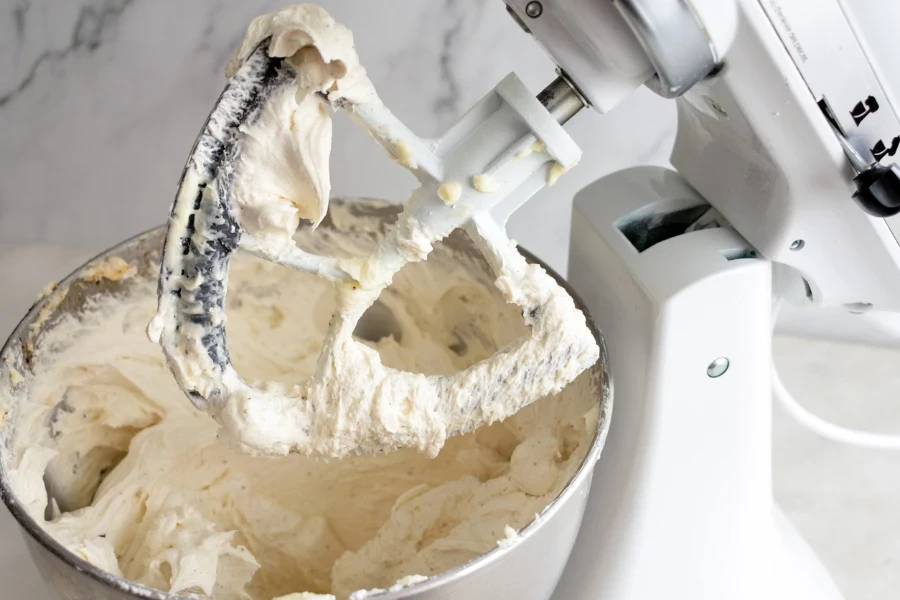
Mixers, while seemingly straightforward, come in a bewildering array of types, each suited to specific tasks. At their core, these machines aim to blend or amalgamate different materials to create a homogeneous mixture. The most common types include batch mixers and continuous mixers. Batch mixers are ideal for mixing precise quantities of materials for a set period, making them perfect for applications where consistency and control are paramount. Continuous mixers, on the other hand, are designed for operations where materials need to be mixed non-stop, offering efficiency and speed for large-scale productions.
Within these broad categories, further specialization exists. For instance, drum mixers are excellent for mixing large volumes of cement or mortar in construction, while planetary mixers are favored in the food industry for their ability to blend ingredients with precision and care. The choice of mixer type directly impacts the quality of the final product, making it crucial to select the right mixer for the right application.
Understanding the specific applications of each mixer type can significantly enhance operational efficiency. For example, high shear mixers are used in the chemical and pharmaceutical industries for their ability to efficiently mix substances at a molecular level, which is critical for creating emulsions and suspensions. This section aims to provide a clear understanding of how choosing the appropriate mixer type can lead to improved product quality and process efficiency.
Key features to look for in a mixer
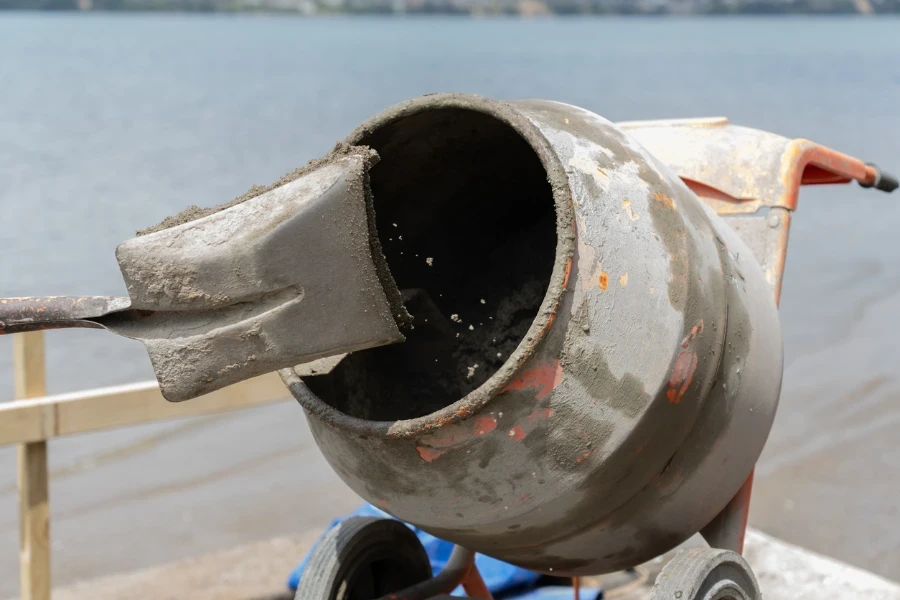
When selecting a mixer, several key features stand out as critical for ensuring optimal performance and durability. First and foremost, the mixer’s capacity should align with your operational needs. A mismatch in capacity can lead to inefficiencies or even damage to the machine. Secondly, the power source and consumption of the mixer are vital considerations, especially in industries where energy efficiency is a priority. Electric, pneumatic, and hydraulic mixers each offer different benefits and limitations, making it important to choose the one that best fits your operational environment.
Another essential feature is the mixer’s material compatibility. The materials used in the construction of the mixer, such as stainless steel or plastic, need to be compatible with the substances being mixed to avoid contamination and ensure longevity. Furthermore, the ease of cleaning and maintenance is a crucial factor, particularly in industries where hygiene and cleanliness are paramount, such as the food and pharmaceutical sectors.
Finally, the mixer’s design and ergonomics can significantly impact user experience and safety. Features like programmable controls, safety guards, and easy-to-use interfaces can enhance operational efficiency and reduce the risk of accidents. By prioritizing these key features, users can ensure they select a mixer that meets their specific needs and standards.
The role of mixers in various industries
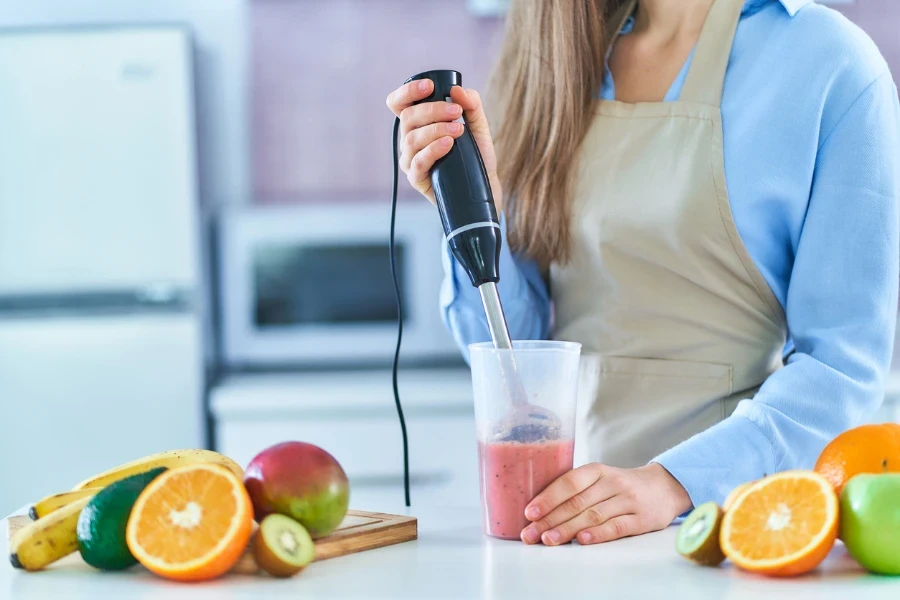
Mixers play a pivotal role in numerous industries, demonstrating their versatility and importance. In the food industry, mixers are essential for combining ingredients to create everything from doughs and batters to sauces and dressings. The precise control over mixing speed and intensity ensures that the final products meet the desired quality standards.
In the construction industry, mixers are indispensable for preparing concrete, mortar, and other building materials. The ability to mix large volumes quickly and uniformly is critical for keeping projects on schedule and ensuring the structural integrity of the construction.
The pharmaceutical industry relies on mixers for blending active ingredients with excipients to create medications with the correct dosage and consistency. This precision mixing is crucial for patient safety and the efficacy of the medications.
Maintenance tips for long-lasting mixer performance
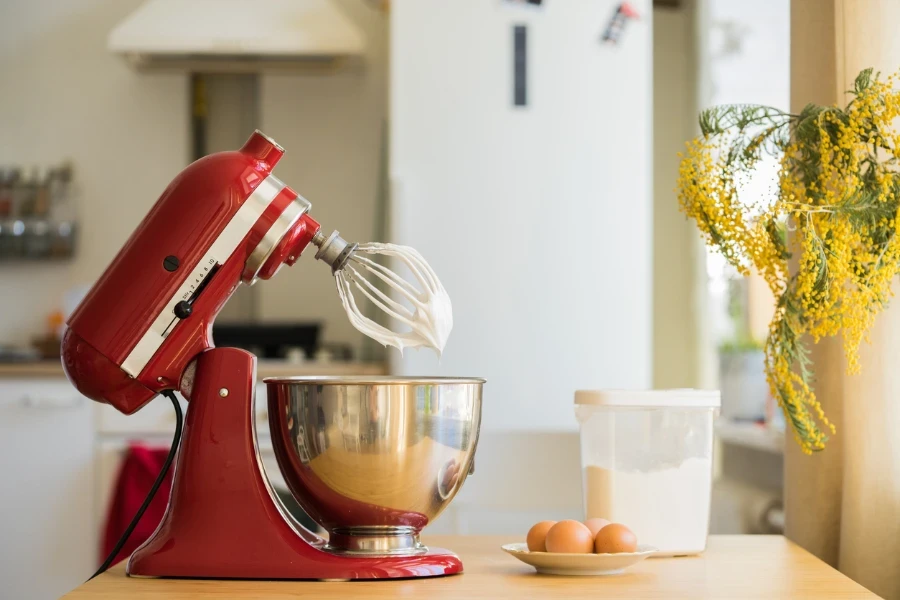
Maintaining a mixer in optimal condition is essential for ensuring its longevity and performance. Regular cleaning is the first step in preventing build-up of materials that can lead to contamination or damage. Following the manufacturer’s guidelines for cleaning and using the recommended cleaning agents can help maintain the mixer’s integrity.
Lubrication of moving parts is another critical maintenance task. Proper lubrication reduces friction, wear, and tear, extending the life of the mixer. It’s also important to regularly check and replace worn-out parts, such as blades or seals, to prevent breakdowns and maintain efficiency.
Scheduling regular maintenance checks can help identify potential issues before they become serious problems. Keeping a maintenance log can also provide valuable insights into the mixer’s performance and maintenance needs over time.
Safety protocols for operating mixers
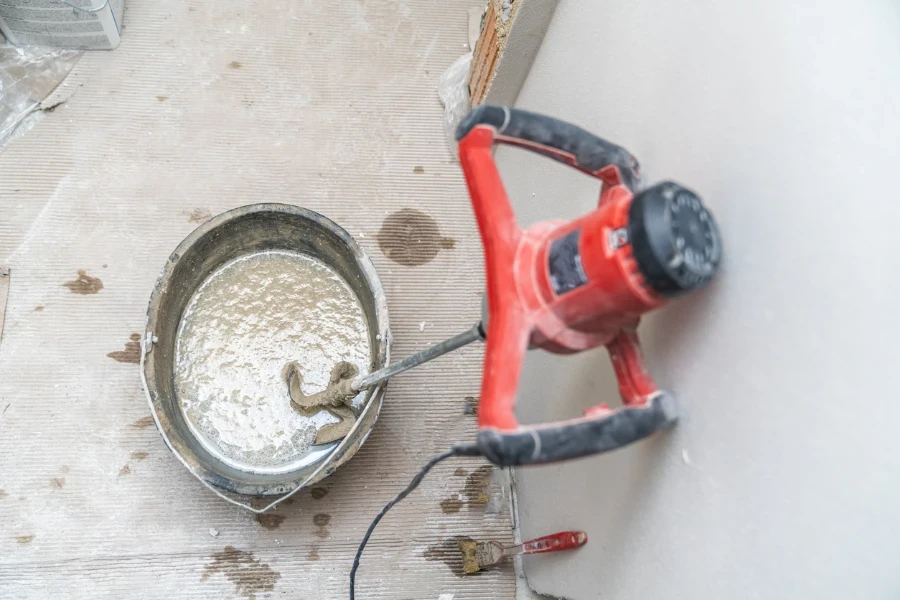
Safety is paramount when operating mixers. Always start by reading and understanding the manufacturer’s safety guidelines. Personal protective equipment, such as gloves and eye protection, should be worn at all times to prevent injury.
Training is essential for anyone operating a mixer. Understanding how to use the controls, what to do in case of an emergency, and how to properly clean and maintain the machine can significantly reduce the risk of accidents.
Ensuring that safety guards and emergency stop features are in place and functional is also critical. These features can prevent serious injuries in case of an accident or malfunction.
Conclusion:
Mixers are indispensable tools in many industries, each type and feature tailored to specific applications. Understanding the various types of mixers, their applications, key features, maintenance, and safety protocols can empower users to make informed decisions, ensuring efficiency, safety, and quality in their operations. By prioritizing these aspects, the longevity and performance of your mixer can be significantly enhanced, contributing to the overall success of your projects.