The realm of manufacturing and fabrication has witnessed a significant transformation with the advent of laser welders. These sophisticated tools have not only enhanced precision in various applications but have also opened new avenues for innovation in the machinery sector. This article aims to explore the five critical aspects of laser welders that users and industry professionals care most about, shedding light on their functionality, versatility, and the value they bring to modern manufacturing processes.
Table of Contents:
– Understanding laser welders and their working principle
– The unparalleled precision and quality of laser welding
– Versatility across industries: Exploring diverse applications
– Cost-effectiveness and efficiency: A comparative analysis
– Safety and environmental considerations in laser welding
Understanding laser welders and their working principle
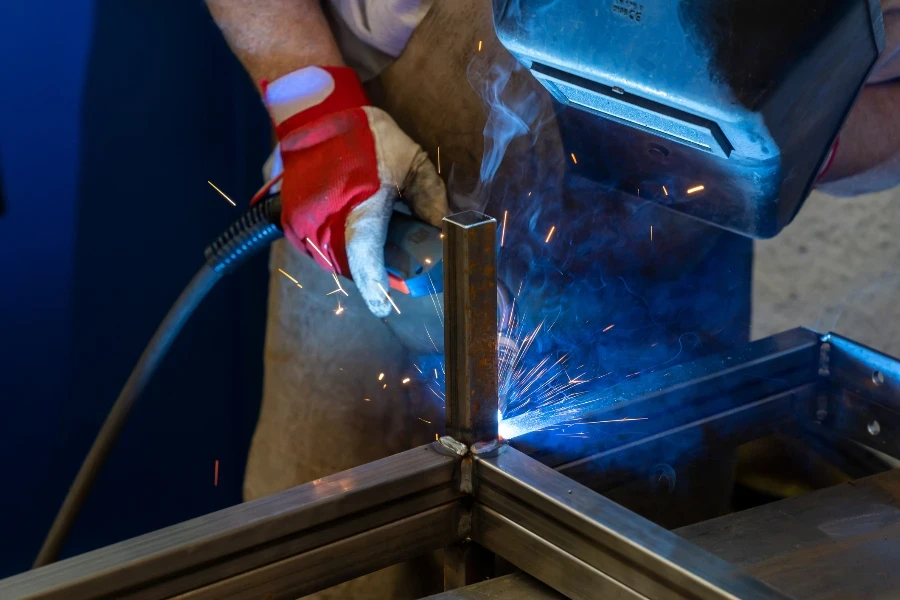
Laser welders operate on a straightforward yet powerful principle: concentrating a high-energy laser beam at a small, precise point on the material to be welded. This intense focus of energy causes the material to melt and fuse together, creating a strong, durable bond upon cooling. The process encompasses various types of lasers, including fiber, CO2, and Nd:YAG, each suited for different materials and applications.
The technology behind these devices has evolved to offer remarkable control over beam intensity, duration, and heat output. This advancement enables operators to adjust the welding process according to the specific requirements of the task at hand, ensuring optimal results every time. Furthermore, the integration of computer-controlled systems has facilitated the automation of laser welding, allowing for high precision and repeatability in complex welding tasks.
The unparalleled precision and quality of laser welding
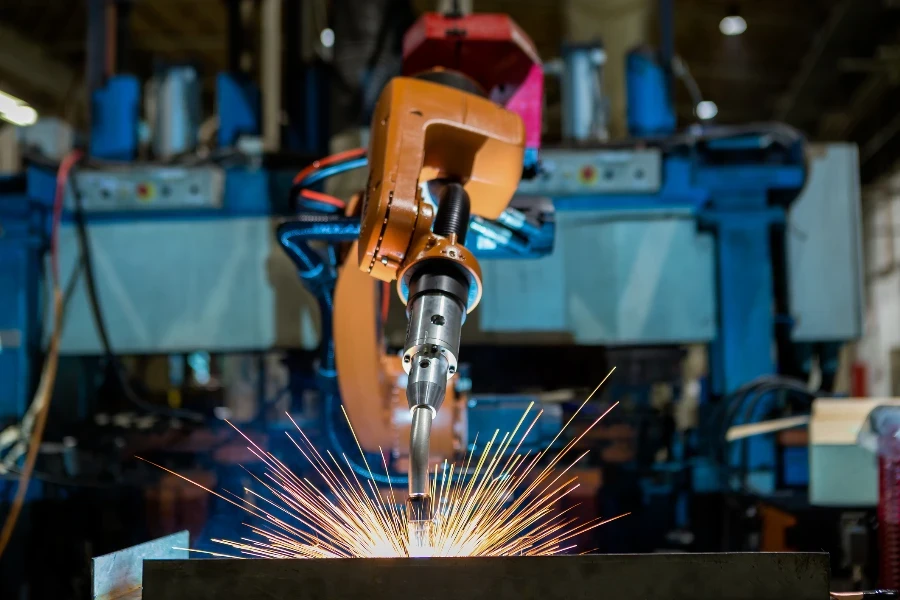
One of the most compelling advantages of laser welders is their ability to achieve unparalleled precision and quality in welding operations. Unlike traditional welding techniques, laser welding offers a minimal heat-affected zone (HAZ), reducing the risk of material distortion and weakening. This precision is particularly beneficial in applications requiring intricate welds on small or delicate components.
Moreover, laser welding produces cleaner and more aesthetically pleasing welds, eliminating the need for post-weld finishing in many cases. The process is also highly controllable, allowing for adjustments in real-time to accommodate different material thicknesses and compositions. This level of control and quality assurance is critical in industries where the integrity of welds is paramount.
Versatility across industries: Exploring diverse applications
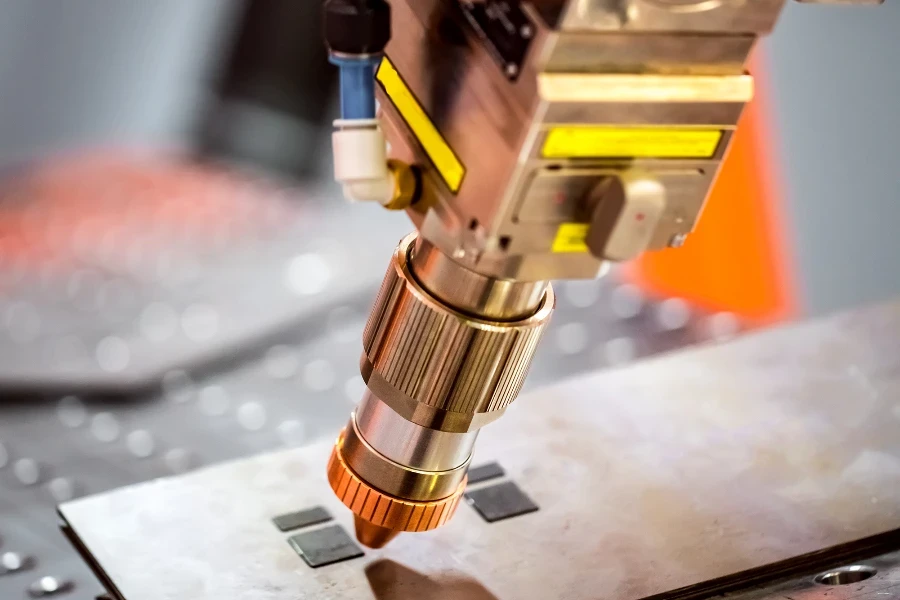
Laser welders are not confined to a single industry or application; their versatility extends across various sectors, including automotive, aerospace, medical devices, and electronics. In the automotive industry, for example, laser welding is used to assemble lightweight vehicle components, contributing to enhanced fuel efficiency and performance.
In aerospace, the precision of laser welding is instrumental in the fabrication of high-strength, critical components. The medical device sector benefits from the ability to produce sterile, high-quality welds for sensitive equipment. Meanwhile, in electronics, laser welders facilitate the miniaturization of components by enabling the precise welding of small parts. This wide-ranging applicability underscores the flexibility and adaptability of laser welding technology.
Cost-effectiveness and efficiency: A comparative analysis
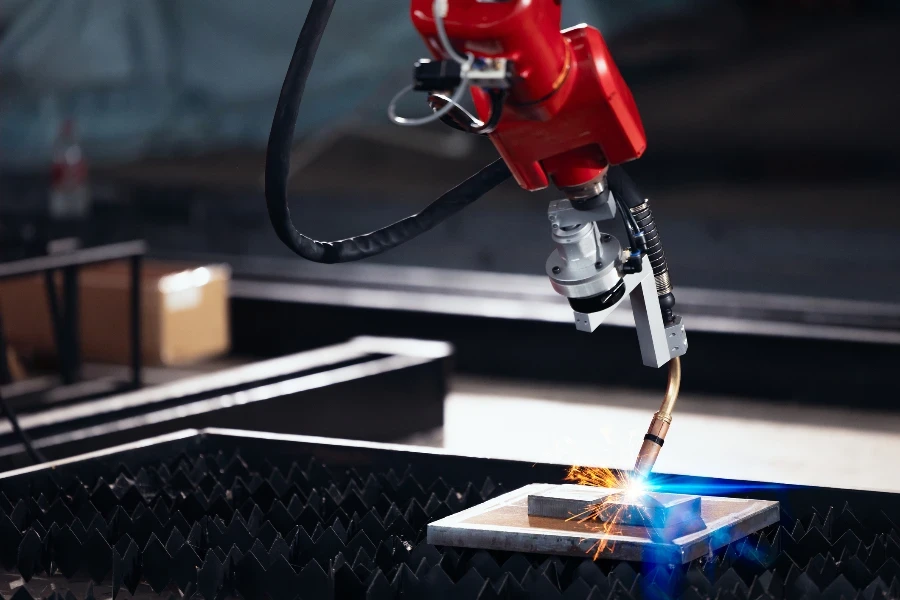
When evaluating the cost-effectiveness and efficiency of laser welders, it’s essential to consider both the upfront investment and the long-term benefits. Initially, laser welding equipment may represent a significant investment compared to traditional welding methods. However, the efficiency, speed, and precision of laser welding can lead to substantial savings over time.
Laser welding’s ability to produce high-quality welds at a faster rate than conventional methods reduces labor costs and increases production throughput. Additionally, the minimal heat input and precision of laser welding result in fewer defects and less material wastage, further enhancing the cost-effectiveness of the process. In the long run, the investment in laser welding technology can offer a compelling return on investment for businesses looking to optimize their manufacturing processes.
Safety and environmental considerations in laser welding
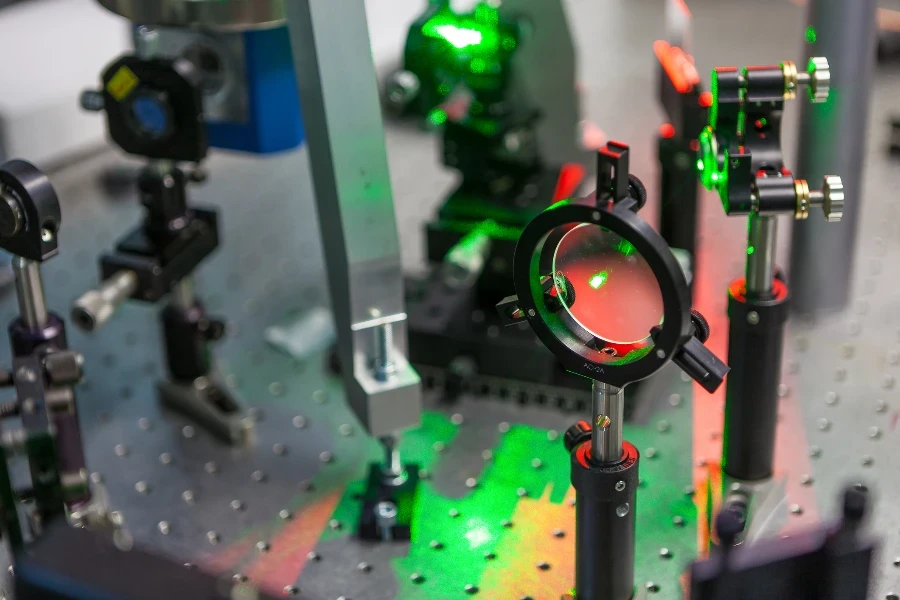
Safety and environmental considerations are paramount in any industrial operation, and laser welding is no exception. Proper safety measures must be in place to protect operators from potential hazards, such as laser radiation and fumes generated during the welding process. Adequate ventilation, protective equipment, and adherence to safety protocols are essential to ensure a safe working environment.
From an environmental perspective, laser welding offers several advantages over traditional welding techniques. The process is cleaner, producing fewer emissions and requiring less energy. Additionally, the precision and efficiency of laser welding reduce material wastage, contributing to more sustainable manufacturing practices. By addressing these considerations, businesses can ensure that their use of laser welding technology aligns with safety and environmental standards.
Conclusion:
Laser welders represent a pivotal advancement in the machinery sector, offering unmatched precision, versatility, and efficiency across a wide range of applications. From enhancing product quality to optimizing production processes, the benefits of laser welding technology are clear. As industries continue to evolve, the adoption of laser welding is set to increase, driven by its potential to meet the demands of modern manufacturing. By understanding the key aspects of laser welders, businesses can leverage this technology to stay competitive and innovative in today’s dynamic market.