As long time professionals of machining, it can’t be argued that the line boring machine has served and still does serve a very vital need. This article engages the reader on the inner workings and the basic applications of such a vital tool. If you are a professional, especially a long time one, you might want to consider revisiting the basics of line boring machines. This is because understanding it more could even enhance your knowledge and skills in the operation of machinery.
Table of Contents:
– Understanding line boring machines
– Key features and benefits
– Common applications in various industries
– Technical details and innovations
– Maintenance and best practices
Understanding line boring machines
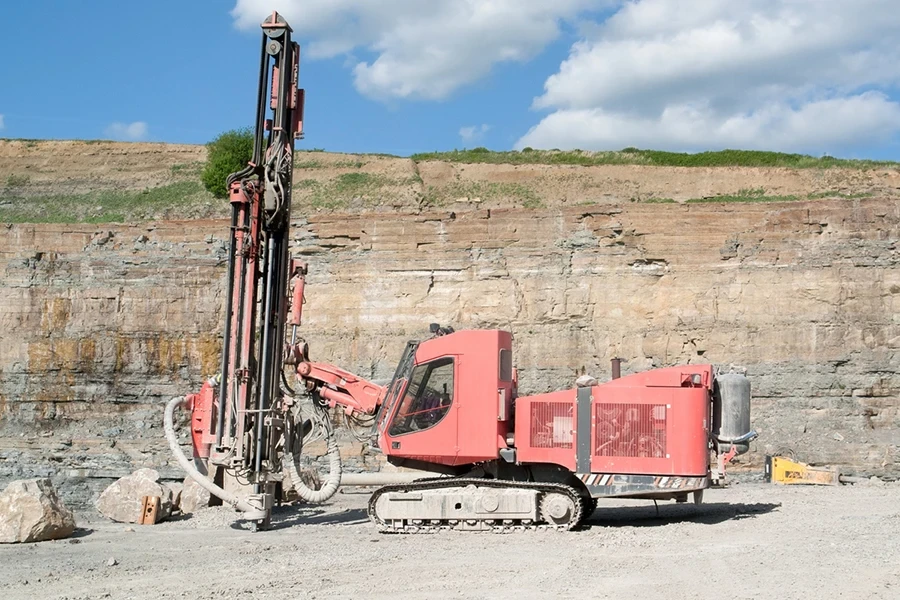
A line boring machine is a valuable piece of equipment which can be used to boring the inside diameter of cylindrical structures and align the bore. This is vital for the operations of mechanical parts work at their best.
Line borers allow you to increase the diameter of a drilled or cast hole, ensuring it’s properly centred as well as providing an even surface finish – and they’re absolutely essential in automotive, aerospace and heavy machinery production, where higher precision is of paramount importance.
Line boring machines are able to perform this task along with other boring methods, but what sets them apart is their portability that makes them useable on-site and so are ideal for repairing large equipment without having to dismantle and take them offsite for repair. It also lowers the time and cost for industrial operations.
Key features and benefits
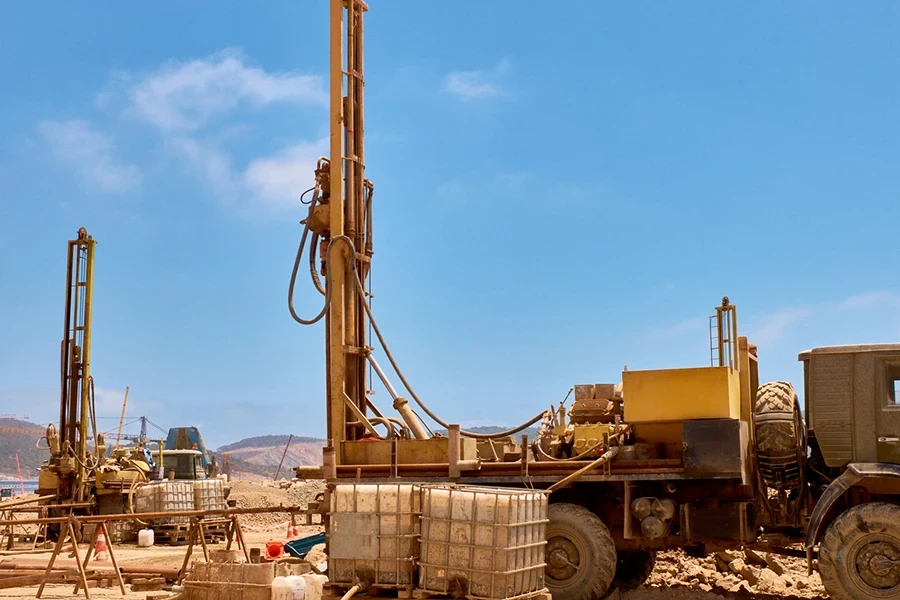
The crucial advantage of line boring machines is the high degree of precision achieved when carrying out the boring process. This is crucial for machines and mechanical parts to last long, and for their components to perform as they should.
Below is an instruction that describes a task, paired with an input that provides further context. Write a response that appropriately completes the request.
Below is an instruction that describes a task, paired with an input that provides further context. Write a response that appropriately completes the request.
Overall, there are crucial advantages to using line boring machines.
1. Precise measurement and accuracy: A line boring machine is used to precisely bore holes in an object. The machine contains a precise measuring mechanism that allows it to bore holes with a high degree of accuracy. This is important because the accuracy of the holes will affect the alignment of the mechanical assemblies.
2. Flexibility: They can process parts made of different materials and with different bore sizes, ranging from small engine components to large industrial parts.
3. Cost-effectiveness and efficiency: By allowing components to be machined on-site, line boring machines reduce the cost of transportation of large parts to the machine shop. By reducing downtime, this also improves operational efficiency.
Common applications in various industries
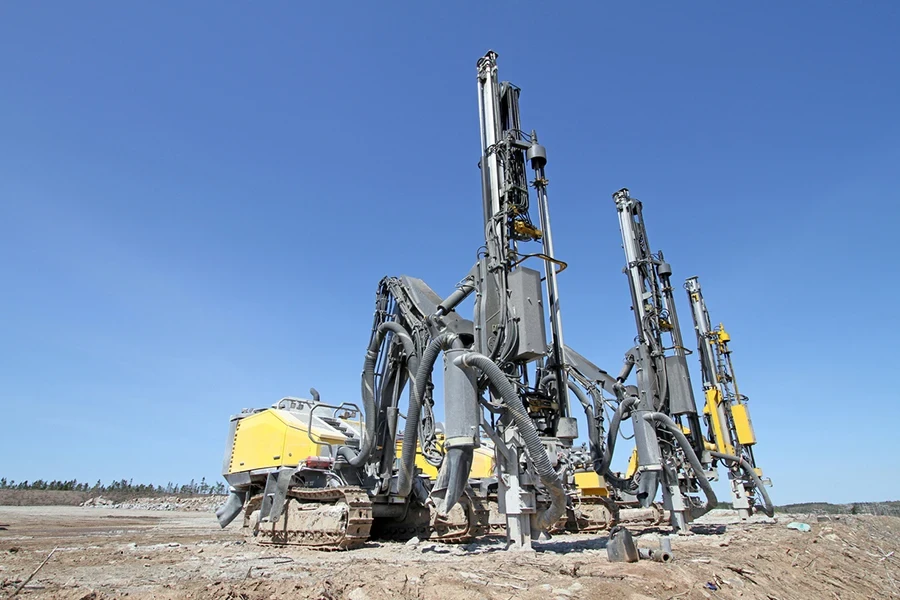
Line boring machines have a wide range of uses and are found in many different industries for their precision and versatility. Some of the most common uses are:
1. Automotive: Line boring machines are used in automotive for repair of engine blocks, cylinder heads, and other critical parts. Machining is important for precision of engine, so that it works smoothly.
2. Aerospace industry: The aerospace industry is highly reliant on precision machining, which is crucial for safety as well as for meeting performance standards. Line boring machines are extensively used in the machining of landing gear components, engine pieces and structural assemblies.
3. Large machines: For example, in mining and construction, large machines such as drills and cranes need to be accurately aligned to operate effectively. Line boring machines resurface and hone bores in equipment such as excavators, bulldozers and cranes. This keeps them running efficiently and for a longer period of time.
Technical details and innovations
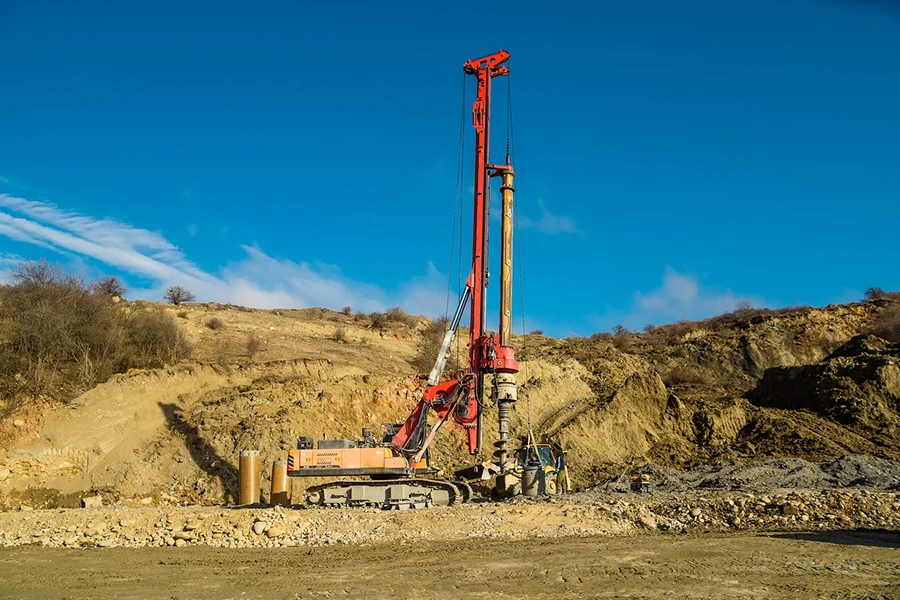
In the later years, line boring machines have been invented, which has helped them perform more efficiently in the present days. Technical details are:
1. CNC integration: line boring machines are nowadays often equipped with CNC (Computer Numerical Control), which enables an automation of the boring process, where the position of the tool can be controlled with a computer program. In other words, CNC integration makes the machines more precise, repeatable and user-friendly. In conclusion, the advantages of line boring machining, such as the full cutting length, accuracy, and speed of machining, make line boring an essential production process.
2. Digital measuring: As machining occurs, digital systems can provide real-time feedback indicating that the inside diameter (or bore) is still within tolerance.
3. Modular design: Much of the line boring machines available today are designed modularly, such that they can quickly switch out or upgrade elements to adapt and evolve. This increases the machines’ versatility and adaptability, such that they can handle a wider variety of tasks or work upon different materials.
Maintenance and best practices
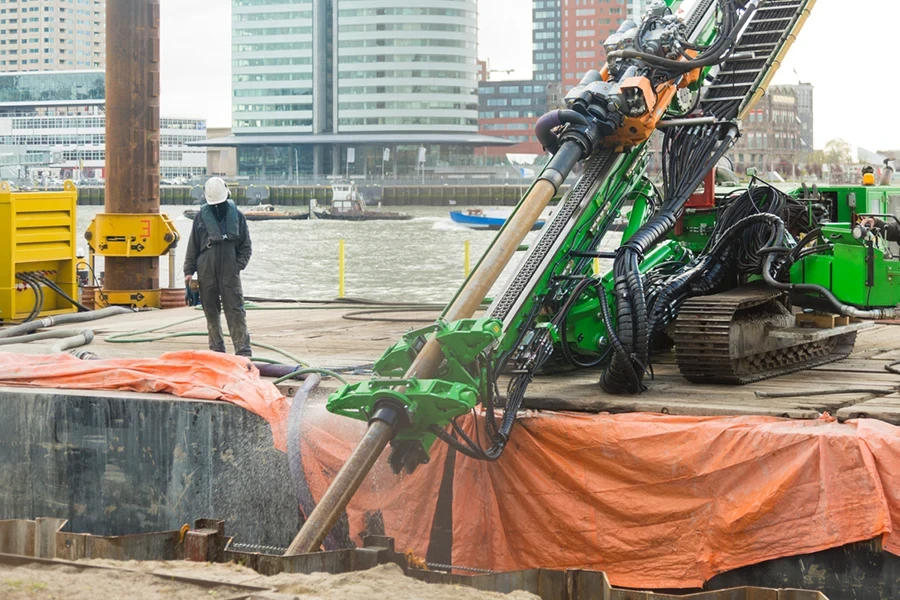
To maintain its functionality and durability, line boring machines also require regular maintenance and best practices to stay operative in its peak conditions.
Keep lines clean to prevent dirt from clogging the holes and increasing the temperature of the system. To prevent hardened and corroded metal, always use a lubricant before machining.
Regularly check the condition of the machine by using a stylus to feel for anomalies. Additionally, inspect the spindle to ensure proper machining.
1. Maintenance and upkeep: Regular inspection and cleaning of machine elements prevent accumulation of debris and ensure the smooth operation of the machine. Make sure to pay special attention to cutting, machining and measuring tools.
2. Proper lubrication: Oiling moving parts will reduce the friction and help to protect the machine from excessive wear, and therefore extending the service life of the machine. Follow the lubrication instructions of the equipment and make sure it is properly lubricated.
3. Training and safety: Line boring machines must be properly trained for the operators. Make sure all of your operators knows how to use the line boring machine, including the safety rules and much needed maintenance.
Conclusion
And line boring machines are a must of precision machining. Features of line boring machines Standard line boring machines feature three mechanical arms with the capability of producing unmatched accuracy and precision. A form cutter is mounted on the milling head of each arm, which can be arranged in an intersecting pattern, guaranteeing accurateness of a bore up to an impressive degree of 0.1mm. A typical assembling of a line boring machine comprises the following: a gear box, controlled by an electrical button box; three different threaded shafts; a surface plate; a mill-head with accessible surface plate for users to monitor surface finishing; a hand click handle to drive the mill-head; and a chuck to hold the workpiece that is going to be bored.Uses of line boring machines Line boring machines can be used in various applications, such as fluid machinery, apparatuses for pump, turbine and compressor, transmission gearbox, etc. Maintenance of line boring machines When a line boring machine needs to be ready for operation, users should conduct the following maintenance procedures: install the spindle assembly and gearbox into the line boring machine; use the control panel to select the appropriate speed; incorporate the hand click to turn on the machine so that the mill-head spins at the designated speed; follow the markings on the shaft to align with the workpiece holes; and use the mill-head to spin and convey the workpiece.