The advent of metal 3D printing has marked a significant milestone in the evolution of manufacturing technologies. This groundbreaking method of production has not only enhanced the capabilities of designers and engineers but also opened up new avenues for innovation across various sectors. In this article, we delve into the core aspects of metal 3D printers, shedding light on their operational mechanisms, applications, benefits, types, and considerations for users. By breaking down these complex topics, we aim to provide a comprehensive understanding of metal 3D printing’s transformative potential.
Table of Contents:
– How metal 3D printers work
– Applications of metal 3D printing in various industries
– Benefits of using a metal 3D printer
– Types of metal 3D printers
– What to consider when choosing a metal 3D printer
How metal 3D printers work
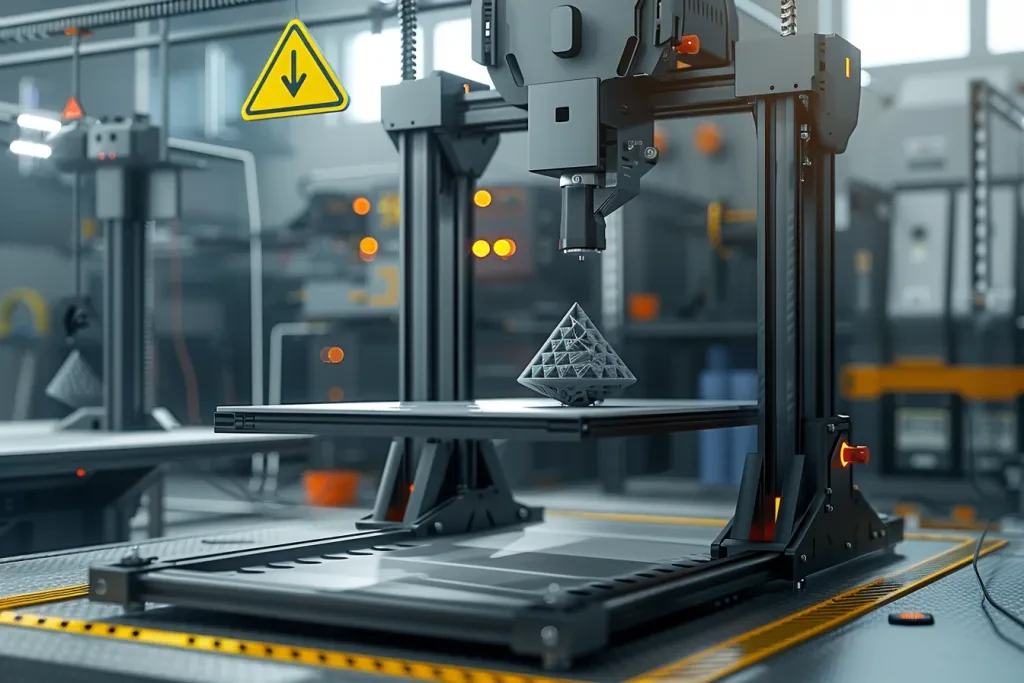
Metal 3D printing, also known as additive manufacturing, is a process that creates three-dimensional objects by adding material layer by layer. Unlike traditional manufacturing methods that often require cutting away material, this additive process allows for more complex designs with less waste. The technology primarily uses a laser or electron beam to melt metal powder or wire, layer by layer, to build the desired object. This method requires precise control and advanced software to manage the intricacies of the design and manufacturing process, ensuring high-quality output with remarkable detail.
The core of metal 3D printing lies in its digital flexibility. Engineers and designers can iterate designs quickly, moving from digital models to physical objects in a fraction of the time it would take with conventional methods. This rapid prototyping capability is not just about speed; it’s about the ability to explore more complex geometries and structures that were previously impossible or too costly to produce.
Moreover, the process of metal 3D printing involves a careful selection of materials and parameters to achieve the desired mechanical properties and surface finish. Metals commonly used include titanium, stainless steel, aluminum, and nickel-based alloys, each offering unique benefits for specific applications. The choice of material, along with the printer’s settings, plays a crucial role in the success of the final product.
Applications of metal 3D printing in various industries
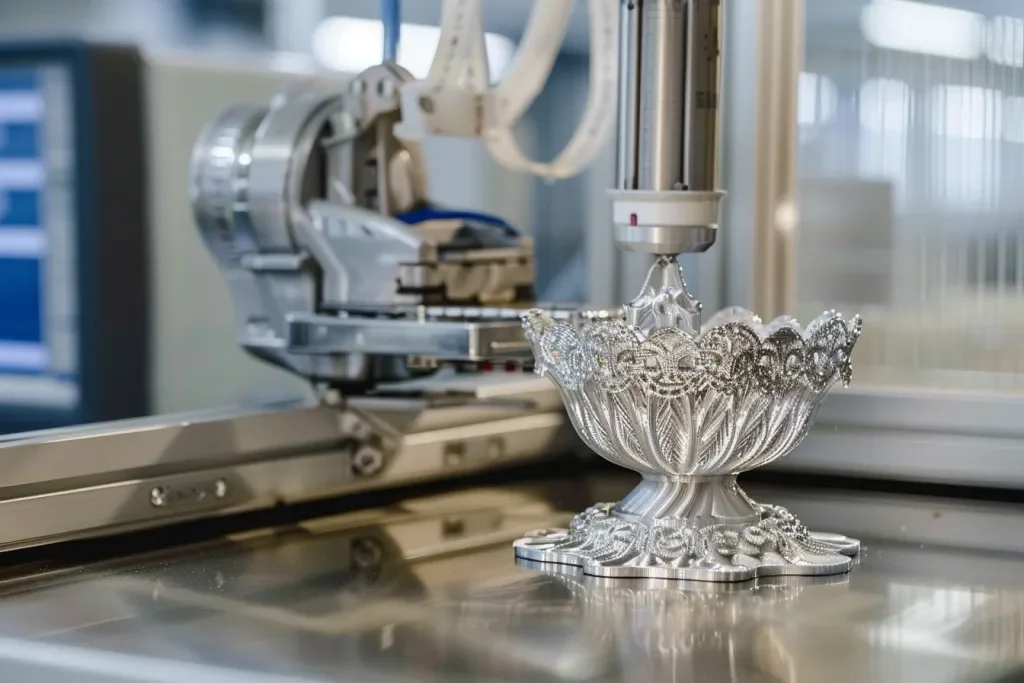
Metal 3D printing has found applications across a wide range of industries, from aerospace to medical, automotive, and beyond. In the aerospace sector, the technology is used to produce lightweight, complex components that can withstand high temperatures and stresses, contributing to more fuel-efficient aircraft. The medical field benefits from the ability to create custom implants and surgical tools tailored to individual patient needs, improving outcomes and recovery times.
In the automotive industry, metal 3D printing is revolutionizing the way components are manufactured, offering the potential for lighter, stronger parts that lead to more efficient vehicles. Furthermore, the technology’s ability to produce parts on demand reduces inventory costs and waste, making the manufacturing process more sustainable.
The versatility of metal 3D printing also extends to sectors like energy, where it’s used to create parts for turbines and fuel cells, and even to the realm of fashion and jewelry, where designers leverage its precision to craft unique, intricate pieces. This wide-ranging applicability underscores the technology’s transformative impact, driving innovation and efficiency across diverse fields.
Benefits of using a metal 3D printer
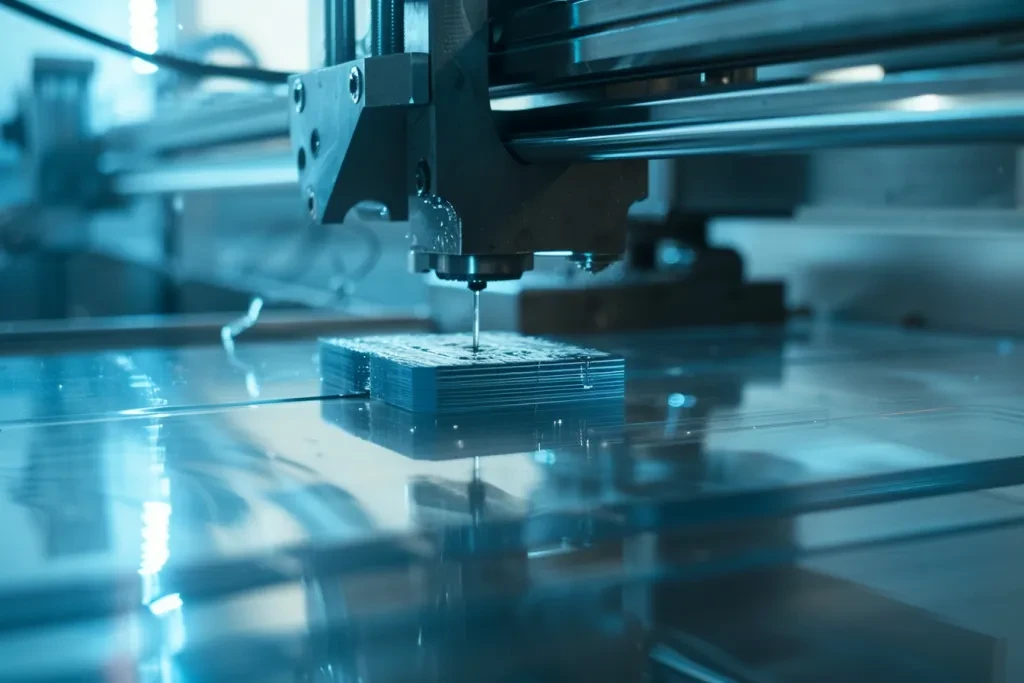
The benefits of using a metal 3D printer are manifold, including increased design flexibility, reduced waste, faster production times, and the ability to produce parts on demand. This technology allows for the creation of complex geometries that are difficult or impossible to achieve with traditional manufacturing methods, opening up new possibilities for innovation and design.
Moreover, metal 3D printing offers significant environmental advantages by minimizing material waste and reducing the energy consumption associated with traditional manufacturing processes. The ability to produce lightweight components also contributes to energy efficiency in applications like transportation, where reducing the weight of vehicles can lead to lower fuel consumption and emissions.
Another key benefit is the potential for cost savings, particularly for low-volume production and prototyping. By eliminating the need for expensive molds and tooling, metal 3D printing allows for cost-effective customization and short-run production, making it an attractive option for businesses looking to stay competitive in a rapidly evolving market.
Types of metal 3D printers
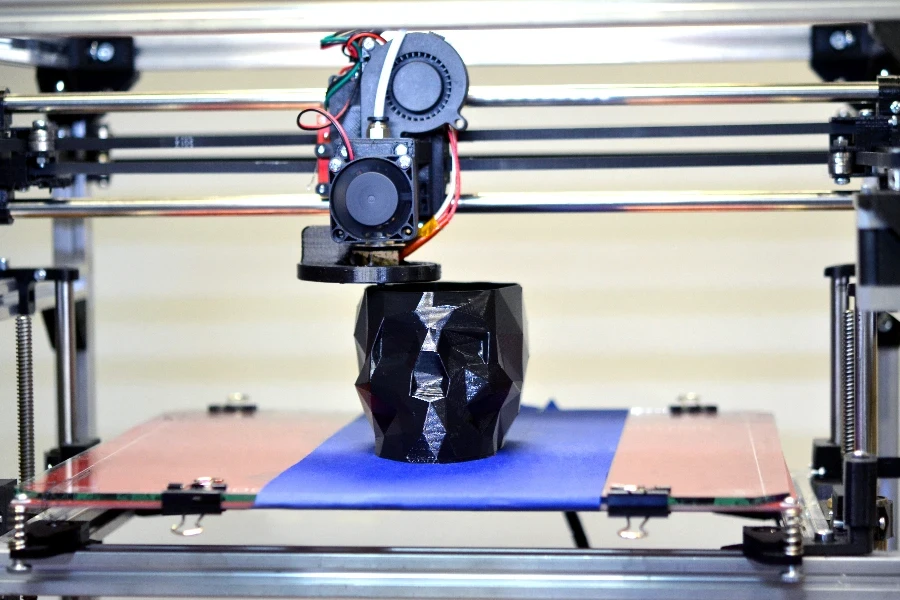
There are several types of metal 3D printers, each employing different technologies to fuse metal particles into solid objects. The most common methods include Direct Metal Laser Sintering (DMLS), Electron Beam Melting (EBM), and Binder Jetting. DMLS uses a laser to sinter powdered metal, building parts layer by layer, while EBM employs an electron beam in a vacuum to melt the metal powder. Binder Jetting, on the other hand, involves spreading a layer of metal powder and selectively depositing a liquid binding agent to form each layer of the part.
Each of these technologies has its strengths and is suited to different applications. DMLS is widely used for its fine detail and precision, making it ideal for complex components in aerospace and medical devices. EBM offers advantages in terms of material properties, as the high temperatures involved can result in parts with superior mechanical characteristics. Binder Jetting stands out for its speed and the ability to produce parts with unique material combinations.
Choosing the right type of metal 3D printer depends on the specific requirements of the application, including the desired material properties, part complexity, and production volume. Understanding the capabilities and limitations of each technology is crucial for making an informed decision.
What to consider when choosing a metal 3D printer
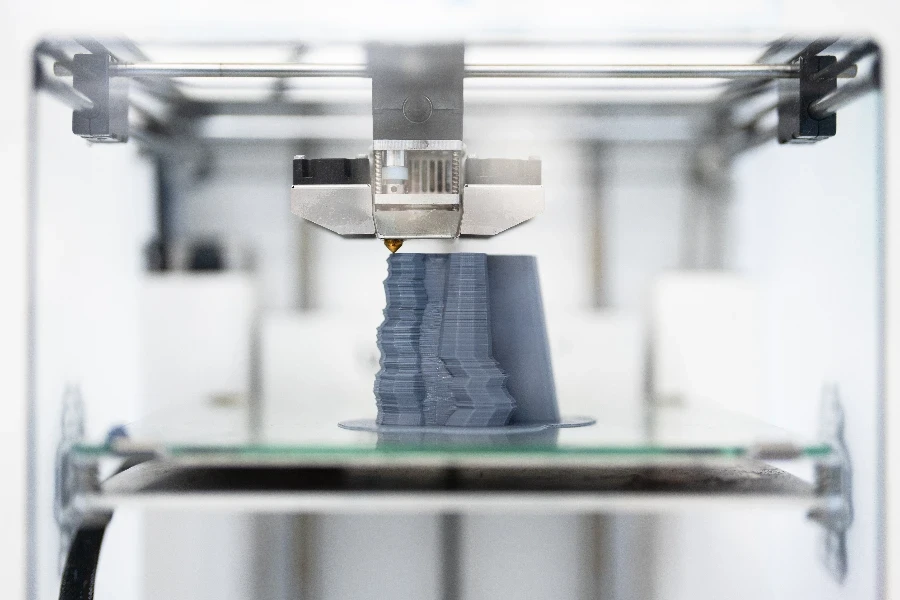
Selecting a metal 3D printer involves several considerations, from the types of materials it can process to its build volume, speed, and resolution. It’s important to assess the specific needs of your application, including the complexity of the parts you intend to produce and their mechanical requirements. The choice of material is also critical, as different metals offer varying strengths, temperatures, and corrosion resistance properties.
Another key factor is the level of precision and detail the printer can achieve. This is particularly important for applications requiring intricate designs or tight tolerances. Additionally, the overall cost, including the initial investment, operating expenses, and maintenance, should be taken into account to ensure the technology is economically viable for your operations.
Support and training are also essential, as metal 3D printing involves complex technology that requires specialized knowledge to operate effectively. Choosing a provider that offers comprehensive support and training can help maximize the benefits of your investment.
Conclusion
Metal 3D printing is reshaping the landscape of manufacturing, offering unprecedented flexibility, efficiency, and innovation across a wide range of industries. By understanding how these printers work, their applications, benefits, types, and selection criteria, businesses and individuals can leverage this technology to its full potential. As we continue to explore the capabilities of metal 3D printing, its role in driving progress and efficiency in manufacturing processes is set to grow, marking a new era in industrial production.