In an era where technology evolves at an unprecedented pace, Industry 4.0 stands as a beacon of transformative change, heralding a new age of industrialization. This digital revolution, characterized by the fusion of leading-edge technologies, is not just reshaping manufacturing landscapes but also redefining how industries operate. Understanding Industry 4.0 is crucial for businesses aiming to stay competitive in this dynamic environment. Through this exploration, we’ll delve into the core components, benefits, challenges, real-world applications, and future trends of Industry 4.0, offering insights into its comprehensive impact.
Table of Contents:
– Core components of Industry 4.0
– Benefits of adopting Industry 4.0
– Challenges in implementing Industry 4.0
– Real-world applications of Industry 4.0
– Future trends in Industry 4.0
Core components of Industry 4.0
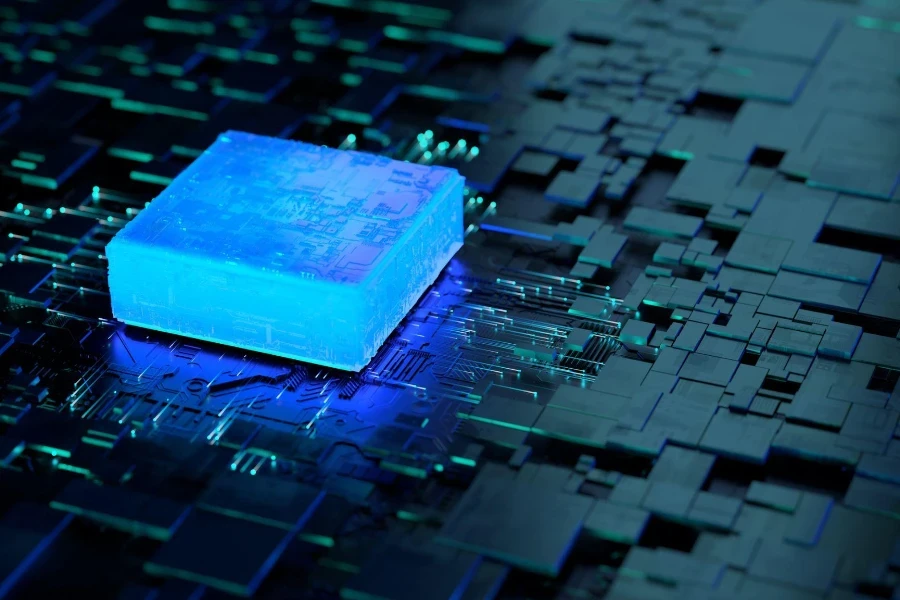
Industry 4.0 is built upon four foundational pillars: interconnectivity, data analytics, automation, and human-machine interaction. Interconnectivity through the Internet of Things (IoT) devices enables seamless communication across various components of the manufacturing process. Data analytics, powered by big data and AI, allows for predictive maintenance and decision-making insights. Automation, facilitated by robotics and cyber-physical systems, enhances efficiency and reduces human error. Lastly, human-machine interaction is elevated through augmented reality (AR) and virtual reality (VR), improving training and operational precision.
These components are interconnected, each playing a crucial role in creating a smart factory environment. This ecosystem thrives on data, with IoT devices collecting vast amounts of information from every corner of the manufacturing floor. Analyzing this data provides actionable insights, driving optimizations that lead to significant efficiency gains and cost reductions.
The integration of these technologies fosters a highly flexible and responsive production system. It enables manufacturers to customize products on a large scale and adapt to changing market demands with agility, marking a departure from traditional manufacturing paradigms.
Benefits of adopting Industry 4.0
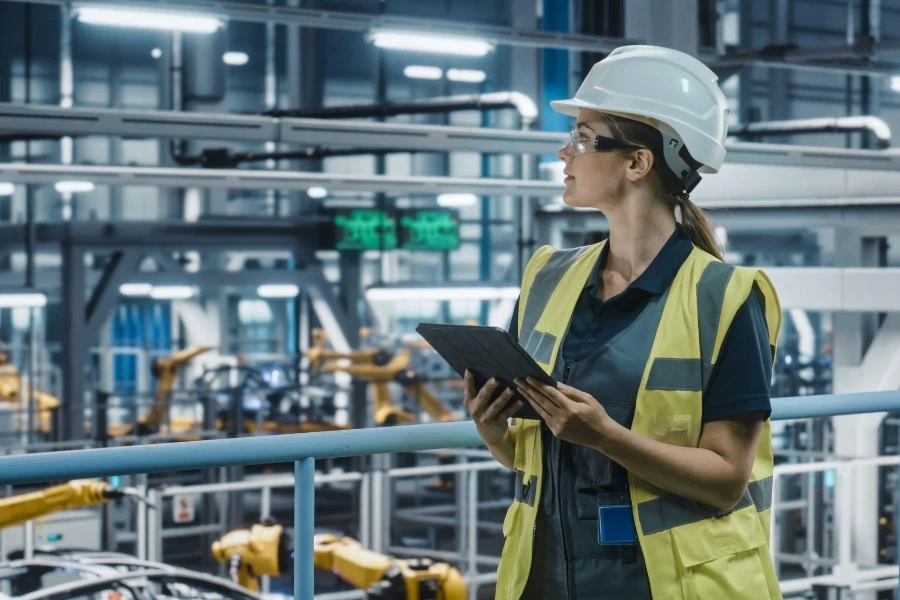
Adopting Industry 4.0 technologies offers a multitude of benefits, including increased operational efficiency, enhanced product quality, and improved worker safety. By automating routine tasks, businesses can allocate human resources to more complex and creative tasks, thereby boosting productivity and innovation. Moreover, predictive maintenance, a hallmark of Industry 4.0, minimizes downtime by forecasting equipment failures before they occur.
Another significant advantage is the ability to create highly customized products at mass production rates. This level of customization, achieved through flexible manufacturing systems, meets the growing consumer demand for personalized products, providing a competitive edge in the marketplace.
Furthermore, Industry 4.0 practices contribute to sustainability by optimizing resource usage and reducing waste. Smart factories can adjust energy consumption in real-time, significantly lowering the environmental footprint of manufacturing activities.
Challenges in implementing Industry 4.0
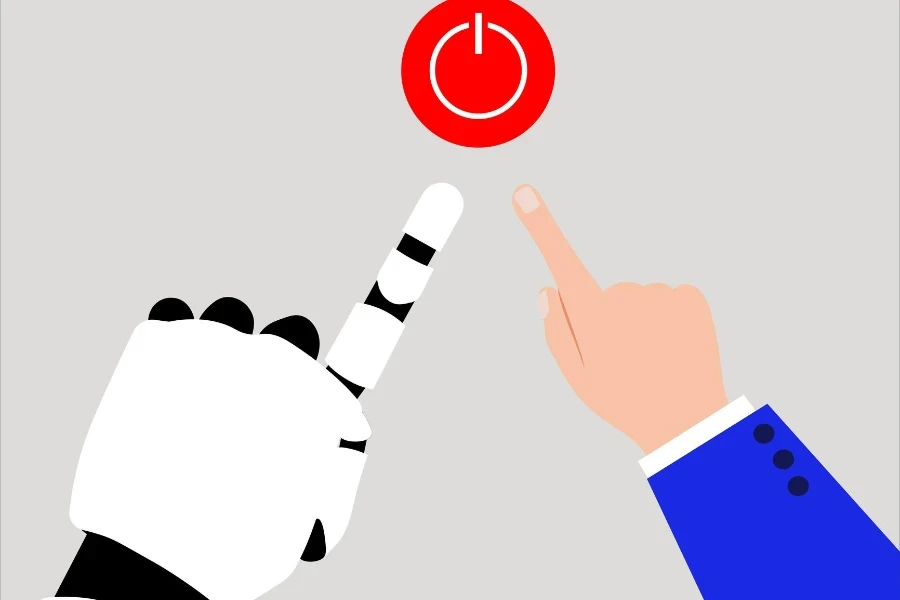
Despite its benefits, transitioning to Industry 4.0 is fraught with challenges. The high cost of implementing cutting-edge technologies can be a significant barrier for small and medium-sized enterprises (SMEs). Additionally, the complexity of integrating new systems with existing infrastructure requires substantial technical expertise and can lead to prolonged downtime if not managed properly.
Cybersecurity emerges as a critical concern in an interconnected environment. The proliferation of IoT devices increases the attack surface, exposing businesses to heightened risks of cyber threats. Ensuring robust security measures are in place is paramount to protect sensitive data and maintain operational integrity.
Moreover, the shift towards automation and digital technologies necessitates workforce reskilling. Employees must be trained to navigate these new tools and processes, which can be a time-consuming and resource-intensive endeavor.
Real-world applications of Industry 4.0
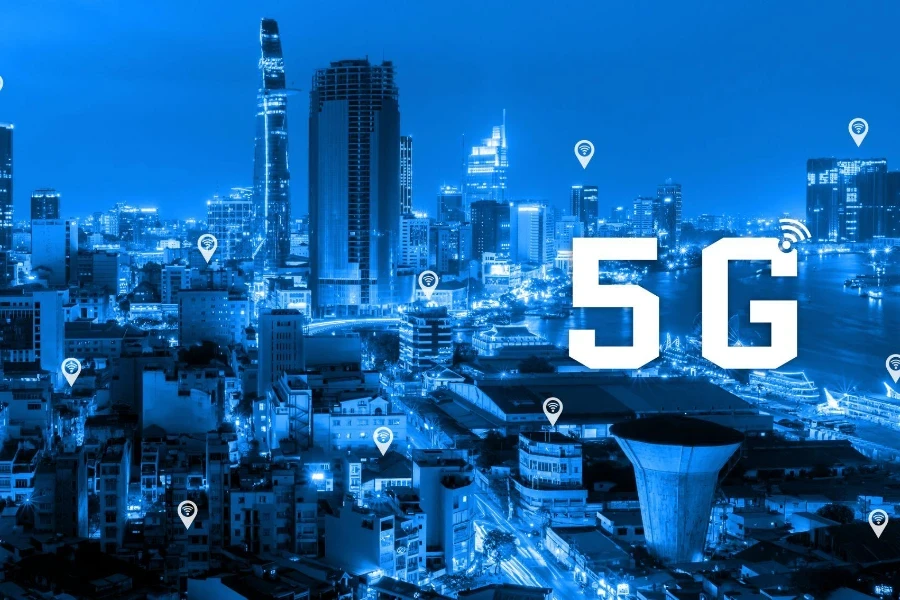
Industry 4.0 is making its mark across various sectors, from automotive to healthcare. In automotive manufacturing, for example, smart factories leverage robotics and IoT to streamline assembly lines, enhancing precision and efficiency. This integration allows for real-time monitoring and adjustments, reducing errors and increasing production rates.
In healthcare, wearable devices and embedded sensors collect patient data continuously, enabling personalized medicine and improving patient outcomes. This data, analyzed through AI algorithms, can predict health issues before they become critical, offering a proactive approach to healthcare.
Agriculture has also embraced Industry 4.0 technologies. Precision farming, powered by drones and satellite imagery, allows for optimized irrigation, fertilization, and pest control, significantly increasing crop yields while conserving resources.
Future trends in Industry 4.0
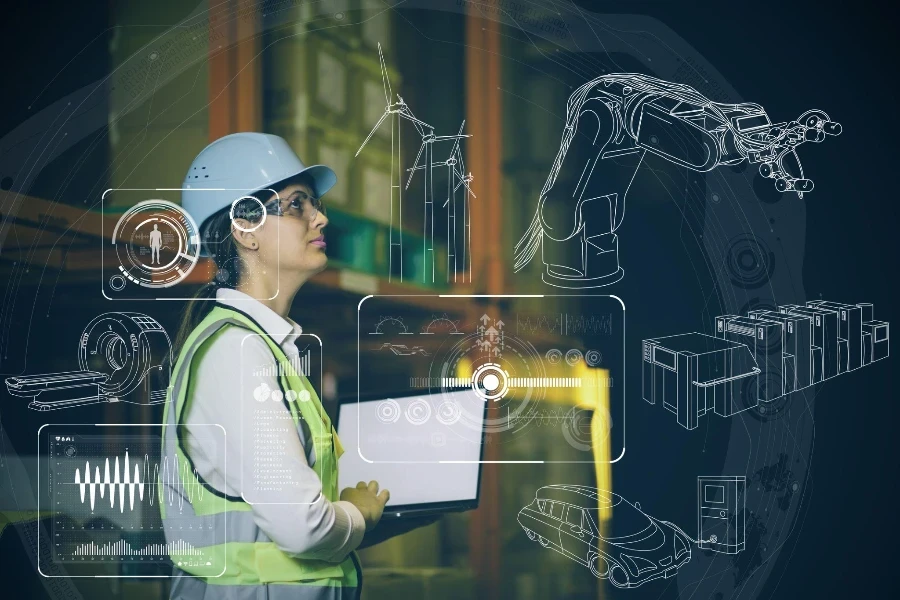
As Industry 4.0 continues to evolve, several trends are shaping its future. The integration of AI and machine learning is expected to deepen, leading to more autonomous and intelligent systems. This advancement will further enhance predictive analytics, making manufacturing processes more efficient and reducing waste.
Blockchain technology is poised to play a pivotal role in supply chain management, offering greater transparency and security. Through decentralized ledgers, businesses can trace the origin and journey of products with unparalleled accuracy, fostering trust among consumers and stakeholders.
Moreover, the advent of 5G technology will accelerate the capabilities of IoT devices, enabling faster and more reliable data transfer. This leap in connectivity will unlock new possibilities for remote operations and real-time analytics, pushing the boundaries of what smart factories can achieve.
Conclusion
Industry 4.0 represents a paradigm shift in manufacturing and beyond, driven by technological advancements that offer unprecedented opportunities for efficiency, customization, and sustainability. While challenges exist, the potential benefits make the journey towards digital transformation a compelling proposition for businesses. As we look to the future, the continuous evolution of Industry 4.0 technologies promises to further revolutionize industries, shaping a smarter, more connected world.