In 2025, the concrete grinder disc market is set to evolve with new technological advancements and eco-friendly trends. This article provides an in-depth analysis of the market, types of discs, and essential selection criteria, offering valuable insights for professional buyers to make informed decisions.
Table of Contents:
– Understanding the Concrete Grinder Disc Market
– Different Types of Concrete Grinder Discs
– Factors to Consider When Selecting Concrete Grinder Discs
– How to Maintain and Replace Concrete Grinder Discs
– Benefits of Using High-Quality Concrete Grinder Discs
– Final Thoughts on Selecting Concrete Grinder Discs
Understanding the Concrete Grinder Disc Market
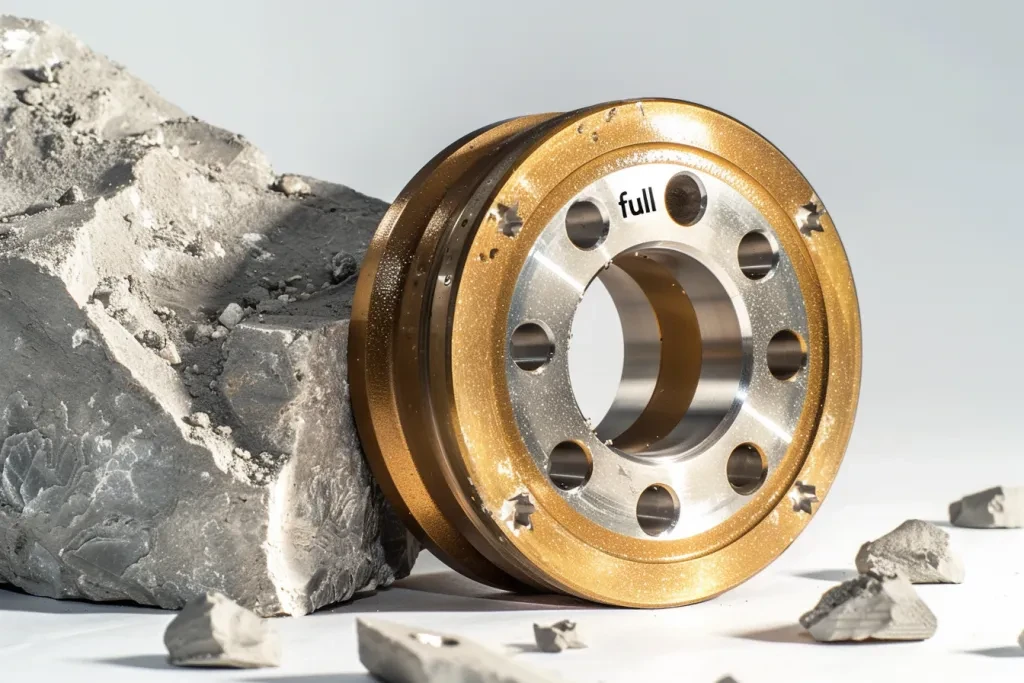
Key Players in the Concrete Grinder Disc Industry
The concrete grinder disc market is dominated by several key players who have established themselves through innovation and quality. Companies such as 3M Company, Carborundum Universal Ltd., and NORITAKE Co., Ltd. are leading the market with their advanced grinding solutions. These companies have a significant market presence across various geographies, including the U.S., China, and Europe. For instance, 3M Company has been at the forefront of developing high-performance grinding discs that cater to the needs of the construction and manufacturing industries.
In addition to these giants, other notable players include Camel Grinding Wheels Works Sarid Ltd. and DEERFOS Co., Ltd. These companies have been focusing on expanding their product portfolios to include a wide range of grinding discs suitable for different applications. The competitive landscape is characterized by continuous innovation, with companies investing heavily in research and development to enhance the performance and durability of their products. For example, NORITAKE Co., Ltd. has been developing custom-engineered grinding wheels tailored to specific applications, enabling superior results with less downtime and material waste.
The market is also witnessing the entry of new players who are leveraging advanced technologies to gain a competitive edge. Companies like DSA Products Ltd. and Kure Grinding Wheel are making significant strides by introducing innovative products that meet the evolving needs of the industry. These new entrants are focusing on niche markets and specialized applications, thereby creating a diverse and competitive market environment.
Market Demand and Trends
The demand for concrete grinder discs is driven by several key market trends, including the increasing focus on precision manufacturing and the growth of the construction industry. The global market for grinding wheels, which includes concrete grinder discs, was about USD 20.7 billion in 2023 and is projected to reach USD 25.0 billion by 2030, growing at a CAGR of 2.8%. This growth is attributed to the rising demand for high-quality and finely finished products in various industries, including automotive, aerospace, and construction.
Technological advancements are also playing a crucial role in shaping the market. Innovations in abrasive materials, such as diamond and cubic boron nitride (CBN), are enhancing the cutting capabilities of grinding discs, allowing them to work on harder materials with greater precision. Advances in bonding technologies are extending the lifespan of grinding discs, reducing wear and tear, and increasing their efficiency in high-speed and heavy-duty grinding operations. These technological advancements are driving the adoption of advanced grinding discs across various industries, supporting market growth.
Another significant trend is the increasing adoption of environmentally friendly grinding solutions. Manufacturers are focusing on developing grinding discs that produce less dust and noise, thereby reducing environmental impact and improving workplace safety. This trend is particularly evident in regions with stringent environmental regulations, such as Europe and North America. The ongoing focus on sustainability and environmental protection is expected to drive the demand for eco-friendly grinding discs in the coming years.
Different Types of Concrete Grinder Discs
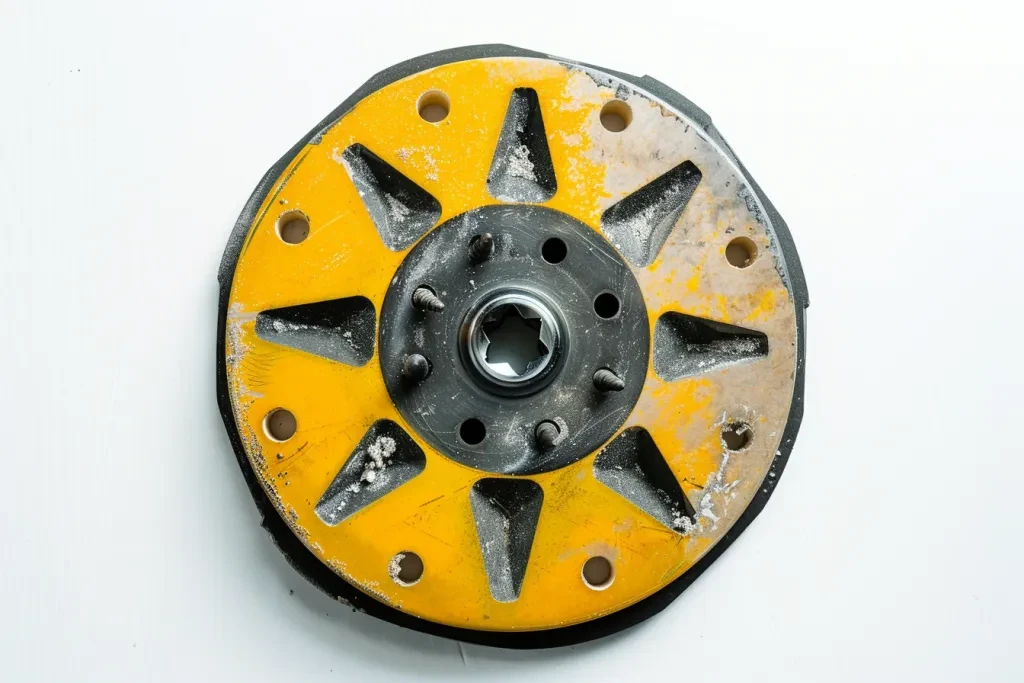
Diamond Discs
Diamond discs are among the most popular types of concrete grinder discs due to their superior cutting capabilities and durability. These discs are embedded with diamond particles, which provide exceptional hardness and wear resistance. Diamond discs are ideal for cutting and grinding hard materials such as concrete, granite, and marble. They are widely used in construction and renovation projects where precision and efficiency are crucial.
The market for diamond discs is expected to grow significantly, driven by the increasing demand for high-performance grinding solutions. According to the Global Grinding Wheels Market report, the adoption of diamond and CBN abrasives is on the rise, as these materials offer enhanced cutting capabilities and longer lifespan. This trend is particularly evident in the construction industry, where the need for efficient and reliable grinding tools is paramount.
In addition to their cutting performance, diamond discs are also known for their versatility. They are available in various grit sizes and bond types, making them suitable for a wide range of applications. For instance, coarse-grit diamond discs are used for aggressive material removal, while fine-grit discs are used for polishing and finishing. This versatility makes diamond discs a preferred choice for professionals in the construction and manufacturing industries.
Silicon Carbide Discs
Silicon carbide discs are another popular type of concrete grinder disc, known for their hardness and sharpness. These discs are made from silicon carbide, a synthetic material that provides excellent cutting performance and durability. Silicon carbide discs are commonly used for grinding and cutting softer materials such as concrete, masonry, and stone. They are also used for surface preparation and finishing applications.
The market for silicon carbide discs is driven by the growing demand for cost-effective grinding solutions. Silicon carbide is relatively inexpensive compared to diamond, making it an attractive option for budget-conscious buyers. According to the Global Grinding Wheels Market report, the demand for silicon carbide discs is expected to grow steadily, supported by the increasing construction activities and infrastructure development projects worldwide.
Silicon carbide discs are available in various grit sizes and configurations, allowing users to choose the right disc for their specific needs. For example, coarse-grit silicon carbide discs are used for heavy material removal, while fine-grit discs are used for polishing and finishing. The availability of different grit sizes and configurations makes silicon carbide discs a versatile and cost-effective option for various grinding applications.
Tungsten Carbide Discs
Tungsten carbide discs are known for their exceptional hardness and wear resistance, making them ideal for heavy-duty grinding applications. These discs are made from tungsten carbide, a material that is significantly harder than steel and provides excellent cutting performance. Tungsten carbide discs are commonly used for grinding and cutting hard materials such as concrete, metal, and ceramics.
The market for tungsten carbide discs is expected to grow, driven by the increasing demand for high-performance grinding tools in various industries. According to the Global Grinding Wheels Market report, the adoption of advanced abrasive materials such as tungsten carbide is on the rise, as these materials offer superior cutting capabilities and longer lifespan. This trend is particularly evident in the metalworking and construction industries, where the need for durable and efficient grinding tools is critical.
Tungsten carbide discs are available in various grit sizes and bond types, making them suitable for a wide range of applications. For instance, coarse-grit tungsten carbide discs are used for aggressive material removal, while fine-grit discs are used for polishing and finishing. The versatility and durability of tungsten carbide discs make them a preferred choice for professionals in the construction, metalworking, and manufacturing industries.
Factors to Consider When Selecting Concrete Grinder Discs
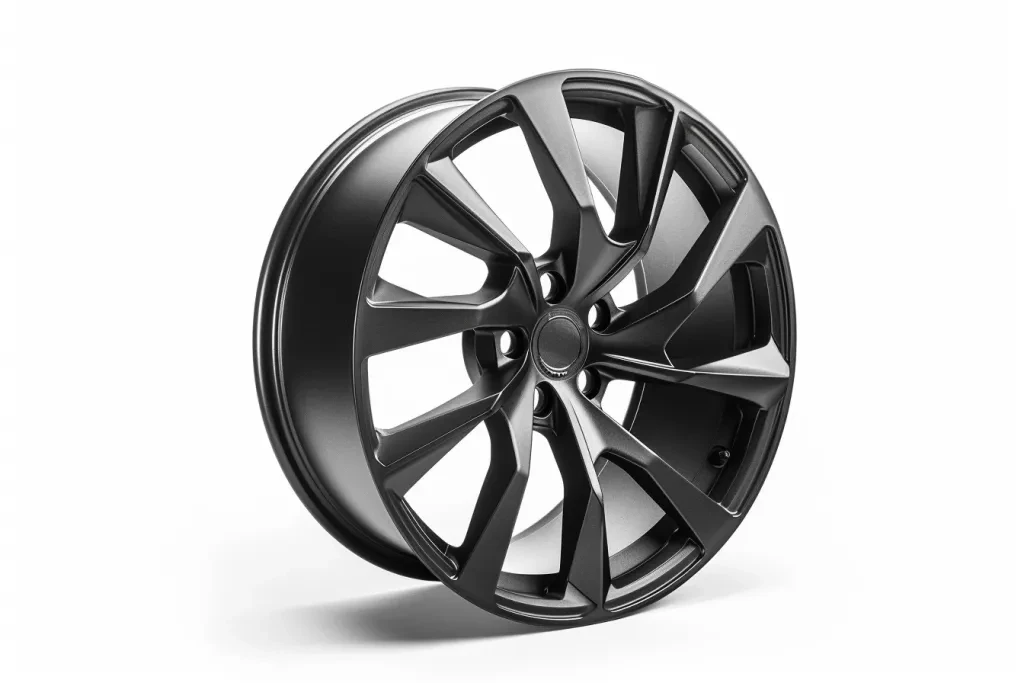
Material Hardness
Material hardness is a critical factor to consider when selecting concrete grinder discs. The hardness of the material being ground determines the type of abrasive material that should be used. For instance, diamond discs are ideal for grinding hard materials such as concrete and granite, while silicon carbide discs are suitable for softer materials such as masonry and stone. According to the Global Grinding Wheels Market report, the adoption of advanced abrasive materials such as diamond and CBN is on the rise, driven by the need for efficient and reliable grinding solutions.
The hardness of the grinder disc itself is also important, as it affects the disc’s durability and performance. Harder discs, such as those made from diamond and tungsten carbide, offer superior wear resistance and longer lifespan, making them suitable for heavy-duty grinding applications. On the other hand, softer discs, such as those made from silicon carbide, are more cost-effective and suitable for lighter grinding tasks. Understanding the hardness of both the material being ground and the grinder disc is essential for selecting the right disc for the job.
In addition to material hardness, other factors such as the type of bond and grit size should also be considered. The bond type affects the disc’s cutting performance and durability, while the grit size determines the level of material removal and surface finish. By considering these factors, users can select the right grinder disc that meets their specific needs and ensures optimal performance and efficiency.
Disc Grit Size
Disc grit size is another important factor to consider when selecting concrete grinder discs. The grit size refers to the size of the abrasive particles on the disc, which determines the level of material removal and surface finish. Coarse-grit discs, with larger abrasive particles, are used for aggressive material removal and rough grinding, while fine-grit discs, with smaller abrasive particles, are used for polishing and finishing.
The choice of grit size depends on the specific application and the desired surface finish. For instance, coarse-grit discs are ideal for removing thick layers of material, such as old paint or coatings, while fine-grit discs are used for achieving a smooth and polished surface. According to the Global Grinding Wheels Market report, the demand for high-performance grinding discs with various grit sizes is on the rise, driven by the need for precision and efficiency in various industries.
In addition to the grit size, the type of abrasive material and bond type also play a crucial role in determining the disc’s performance. For example, diamond discs with fine grit sizes are used for polishing hard materials such as granite and marble, while silicon carbide discs with coarse grit sizes are used for grinding softer materials such as concrete and masonry. By considering the grit size, abrasive material, and bond type, users can select the right grinder disc that meets their specific needs and ensures optimal performance and efficiency.
Disc Bond Type
The bond type of a concrete grinder disc is a critical factor that affects its performance and durability. The bond type refers to the material that holds the abrasive particles together on the disc. Common bond types include resin, metal, and vitrified bonds, each offering different levels of performance and durability. For instance, resin bonds provide flexibility and are suitable for general-purpose grinding, while metal bonds offer superior durability and are ideal for heavy-duty grinding applications.
The choice of bond type depends on the specific application and the material being ground. For example, resin-bonded discs are commonly used for grinding softer materials such as concrete and masonry, while metal-bonded discs are used for grinding harder materials such as granite and metal. According to the Global Grinding Wheels Market report, the demand for advanced bonding technologies is on the rise, driven by the need for high-performance and durable grinding solutions.
In addition to the bond type, other factors such as the grit size and abrasive material should also be considered. The combination of these factors determines the disc’s cutting performance, durability, and efficiency. By selecting the right bond type, users can ensure that the grinder disc meets their specific needs and provides optimal performance and longevity.
Compatibility with Grinder
Compatibility with the grinder is another important factor to consider when selecting concrete grinder discs. The grinder disc must be compatible with the specific type and model of the grinder being used. This includes factors such as the disc size, arbor size, and maximum operating speed. Using an incompatible disc can result in poor performance, damage to the grinder, and potential safety hazards.
The disc size refers to the diameter of the grinder disc, which must match the size of the grinder’s wheel guard. Common disc sizes include 4.5 inches, 7 inches, and 9 inches, with larger discs being used for heavy-duty grinding applications. The arbor size refers to the diameter of the hole in the center of the disc, which must match the size of the grinder’s spindle. Common arbor sizes include 5/8 inch and 7/8 inch.
The maximum operating speed of the grinder disc must also be compatible with the grinder’s speed rating. Using a disc with a lower speed rating than the grinder can result in disc failure and potential safety hazards. By ensuring compatibility with the grinder, users can ensure optimal performance, safety, and efficiency.
Cost and Budget
Cost and budget are important considerations when selecting concrete grinder discs. The cost of grinder discs can vary significantly depending on factors such as the type of abrasive material, bond type, grit size, and brand. For instance, diamond discs are generally more expensive than silicon carbide discs due to their superior cutting performance and durability. However, the higher cost of diamond discs can be justified by their longer lifespan and reduced need for frequent replacements.
When considering cost and budget, it is important to balance the initial cost of the grinder disc with its performance and longevity. Investing in high-quality grinder discs can result in cost savings in the long run by reducing the need for frequent replacements and improving overall efficiency. According to the Global Grinding Wheels Market report, the demand for high-performance and cost-effective grinding solutions is on the rise, driven by the need for improved productivity and reduced operational costs.
In addition to the cost of the grinder disc, other factors such as the specific application, material being ground, and desired surface finish should also be considered. By carefully evaluating these factors, users can select the right grinder disc that meets their specific needs and provides the best value for their budget.
How to Maintain and Replace Concrete Grinder Discs
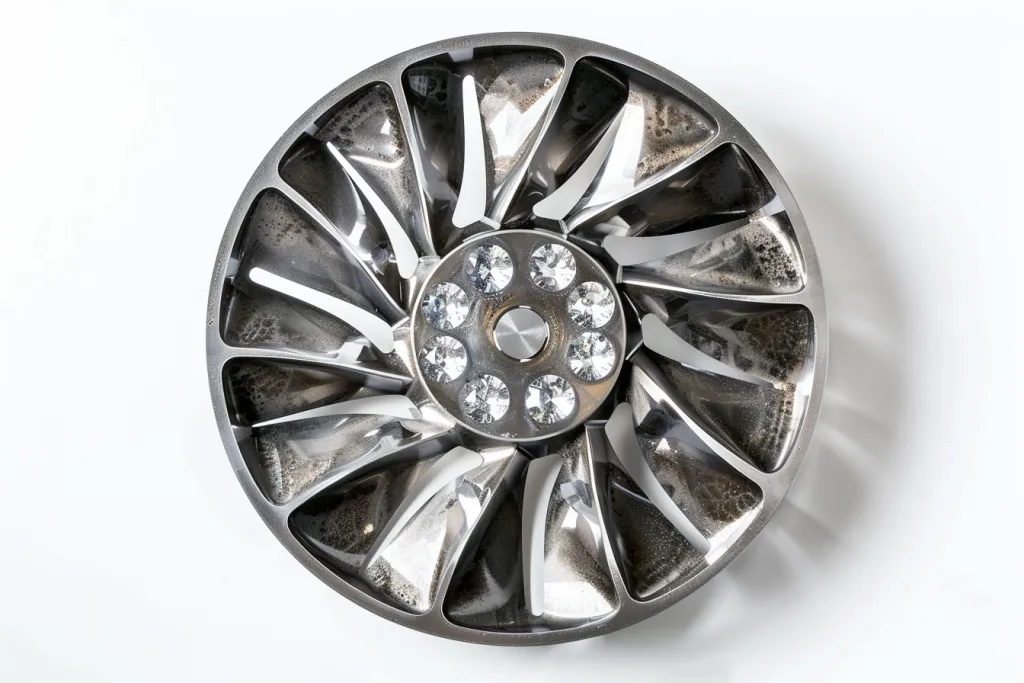
Proper Cleaning Techniques
Proper cleaning of concrete grinder discs is essential for maintaining their performance and longevity. Start by disconnecting the grinder from the power source to ensure safety. Use a wire brush or a specialized cleaning tool to remove any debris or buildup from the disc surface. For more thorough cleaning, consider using a mild detergent solution and a soft cloth to wipe down the disc, ensuring all residues are removed.
After cleaning, it is crucial to dry the disc completely to prevent rust or corrosion. Use a clean, dry cloth to wipe off any moisture, and allow the disc to air dry if necessary. Regular cleaning should be performed after each use to maintain optimal performance. Additionally, inspect the disc for any signs of damage or wear during the cleaning process.
For heavily soiled discs, consider using a chemical cleaner specifically designed for abrasive tools. Follow the manufacturer’s instructions carefully to avoid damaging the disc. Proper storage of the cleaned discs in a dry, dust-free environment will further extend their lifespan and ensure they are ready for use when needed.
Signs of Wear and Tear
Identifying signs of wear and tear on concrete grinder discs is crucial for maintaining effective grinding operations. One common sign is a noticeable decrease in grinding efficiency, which can indicate that the abrasive surface has worn down. Additionally, inspect the disc for visible cracks, chips, or uneven wear patterns, which can compromise its structural integrity and performance.
Another indicator of wear is the presence of unusual vibrations or noises during operation. These symptoms can suggest that the disc is no longer balanced or that it has developed irregularities. Regularly checking the disc’s thickness is also important, as excessive thinning can lead to breakage under stress.
Monitoring the disc’s performance and conducting routine visual inspections can help detect wear early. Replacing worn or damaged discs promptly will prevent potential safety hazards and ensure consistent grinding quality. Keeping a log of disc usage and wear patterns can also aid in predicting replacement intervals and maintaining a steady supply of functional discs.
Replacement Guidelines
Replacing concrete grinder discs involves several key steps to ensure safety and proper installation. Begin by disconnecting the grinder from its power source to prevent accidental activation. Use the appropriate tool, such as a wrench or spanner, to remove the locking nut or flange that secures the disc in place. Carefully remove the old disc, taking note of its orientation and any washers or spacers used.
Before installing the new disc, inspect the grinder’s spindle and mounting hardware for any signs of damage or wear. Clean these components to remove any debris or residue that could affect the disc’s alignment. Position the new disc onto the spindle, ensuring it is seated correctly and securely. Reattach the locking nut or flange, tightening it according to the manufacturer’s specifications.
After installation, perform a brief test run to verify that the disc is properly aligned and balanced. Listen for any unusual noises and check for excessive vibrations, which could indicate improper installation. Regularly replacing worn discs and following these guidelines will help maintain optimal grinding performance and extend the life of your equipment.
Benefits of Using High-Quality Concrete Grinder Discs
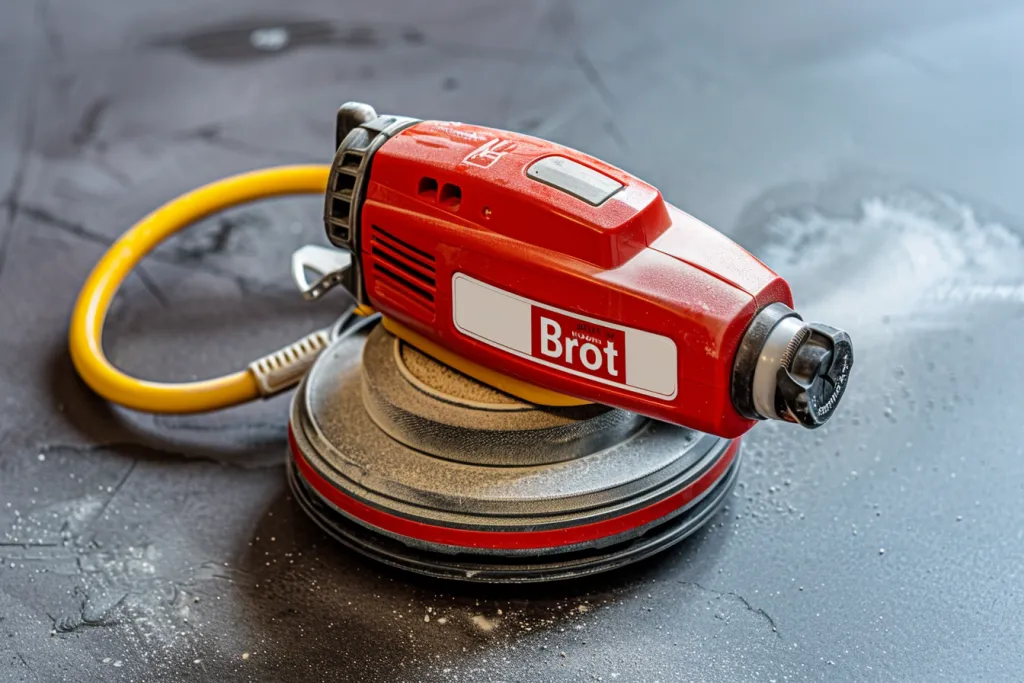
Enhanced Performance
High-quality concrete grinder discs significantly enhance performance by providing superior cutting and grinding capabilities. These discs are typically made from premium materials, such as industrial-grade diamonds or advanced ceramics, which offer exceptional hardness and durability. This results in faster material removal rates and more efficient grinding processes.
The precision manufacturing of high-quality discs ensures consistent performance and uniform wear patterns. This consistency allows for smoother operation and reduces the likelihood of disc failure during use. Additionally, high-quality discs often feature advanced bonding technologies that enhance their cutting efficiency and lifespan.
Using high-quality discs also minimizes downtime associated with frequent disc changes and maintenance. The improved performance and reliability of these discs contribute to increased productivity and cost savings over time. Investing in high-quality concrete grinder discs is a strategic decision that can yield significant benefits in both performance and operational efficiency.
Increased Longevity
The longevity of concrete grinder discs is greatly enhanced when using high-quality products. These discs are designed to withstand the rigors of heavy-duty grinding applications, offering extended service life compared to standard discs. The use of superior abrasive materials and advanced bonding techniques ensures that high-quality discs maintain their cutting edge for longer periods.
Increased longevity translates to fewer replacements and reduced operational costs. High-quality discs are less prone to premature wear and damage, which means they can handle more grinding cycles before needing replacement. This durability is particularly beneficial in demanding environments where consistent performance is critical.
Moreover, the extended lifespan of high-quality discs contributes to better overall equipment efficiency. Operators can rely on these discs to perform consistently without the need for frequent adjustments or replacements. This reliability enhances workflow continuity and reduces the likelihood of unexpected downtime, ultimately improving project timelines and outcomes.
Better Surface Finish
Using high-quality concrete grinder discs results in a superior surface finish, which is essential for many construction and renovation projects. These discs are engineered to provide precise and even grinding, minimizing surface imperfections and achieving a smooth, polished finish. The high-quality abrasive materials used in these discs ensure consistent cutting action, reducing the risk of gouging or uneven grinding.
A better surface finish not only enhances the aesthetic appeal of the concrete but also improves its functional properties. Smooth surfaces are easier to clean and maintain, and they provide better adhesion for coatings and sealants. High-quality discs are particularly effective in achieving the fine finishes required for decorative concrete applications and high-precision tasks.
Additionally, the improved surface finish achieved with high-quality discs can reduce the need for additional finishing steps, such as sanding or polishing. This efficiency saves time and labor costs, making the overall grinding process more cost-effective. Investing in high-quality concrete grinder discs is a practical choice for achieving professional-grade results with minimal effort.
Final Thoughts on Selecting Concrete Grinder Discs
Selecting the right concrete grinder discs is crucial for achieving optimal performance and longevity. High-quality discs offer enhanced cutting efficiency, increased durability, and superior surface finishes, making them a valuable investment for any grinding application. Prioritizing quality and proper maintenance will ensure consistent results and long-term cost savings.