Concrete mixers are the backbone of construction sites worldwide, blending cement, sand, water, and aggregates to produce concrete. This article aims to demystify the complexities surrounding concrete mixers, breaking down their types, functionalities, maintenance practices, safety considerations, and the latest technological advancements. Whether you’re a seasoned professional or new to the construction industry, understanding these aspects will enhance your knowledge and potentially your on-site efficiency.
Table of Contents:
– Types of concrete mixers
– How concrete mixers work
– Maintenance practices for longevity
– Safety considerations
– Technological advancements in concrete mixers
Types of concrete mixers
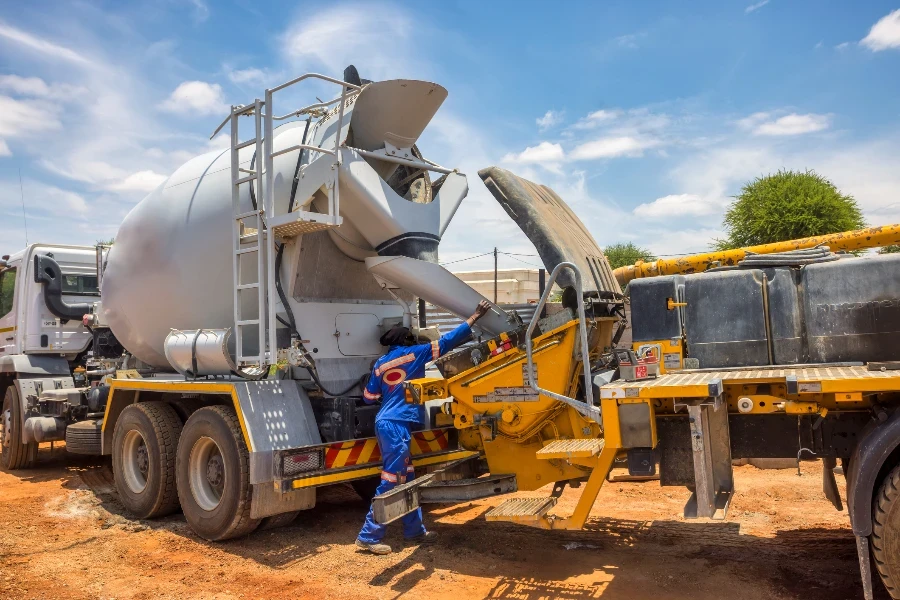
Concrete mixers come in various sizes and shapes, each designed to meet specific needs. The most common types include drum mixers, pan mixers, and continuous mixers. Drum mixers, which can be further categorized into tilting, non-tilting, and reversing drum mixers, are widely used for their efficiency in mixing large volumes of concrete. Pan mixers, known for their fixed or rotating pans, excel in mixing more homogeneously, making them ideal for color concrete and smaller batches. Continuous mixers, on the other hand, provide a steady stream of concrete, suitable for large-scale projects requiring consistent quality.
Understanding the differences between these types is crucial for selecting the right mixer for your project. Factors such as the volume of concrete needed, the nature of the work, and the project’s scale play significant roles in this decision. It’s not just about having a mixer but having the right one that can significantly impact your project’s success.
How concrete mixers work
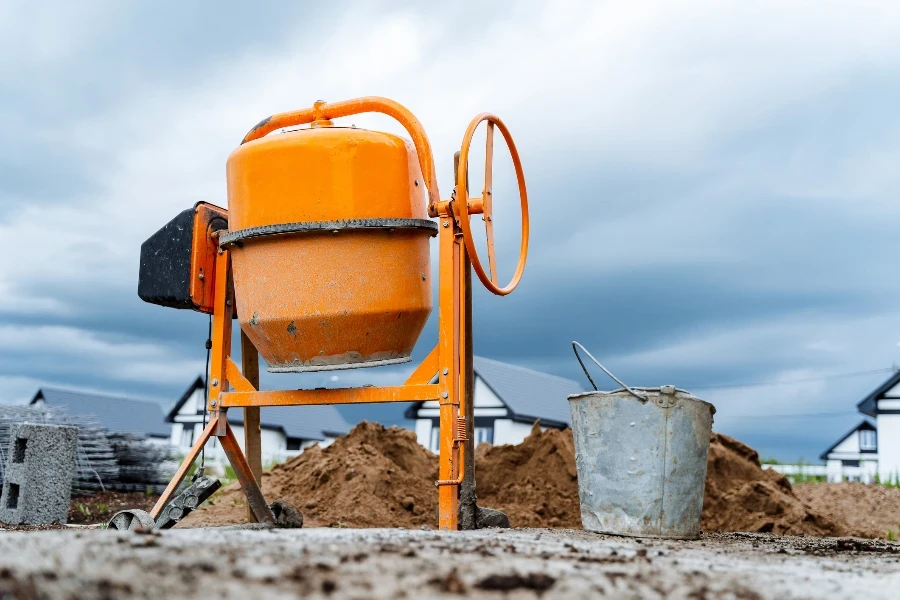
The principle behind concrete mixers is the combination of ingredients to create a uniform mixture. Regardless of the type, all mixers perform this basic function, though the process varies. In drum mixers, the drum rotates on an axis, either horizontally or slightly tilted, mixing the ingredients through agitation. Pan mixers use a stationary or rotating pan, where paddles or blades mix the concrete. Continuous mixers feed ingredients into one end as the mixed concrete exits the other, ensuring a constant flow.
The mixing process is critical to achieving the desired strength and durability of the concrete. It ensures that the cement coats all the aggregate particles and allows the chemical reaction (hydration) to happen efficiently. The quality of the mix significantly affects the concrete’s final strength, workability, and durability.
Maintenance practices for longevity
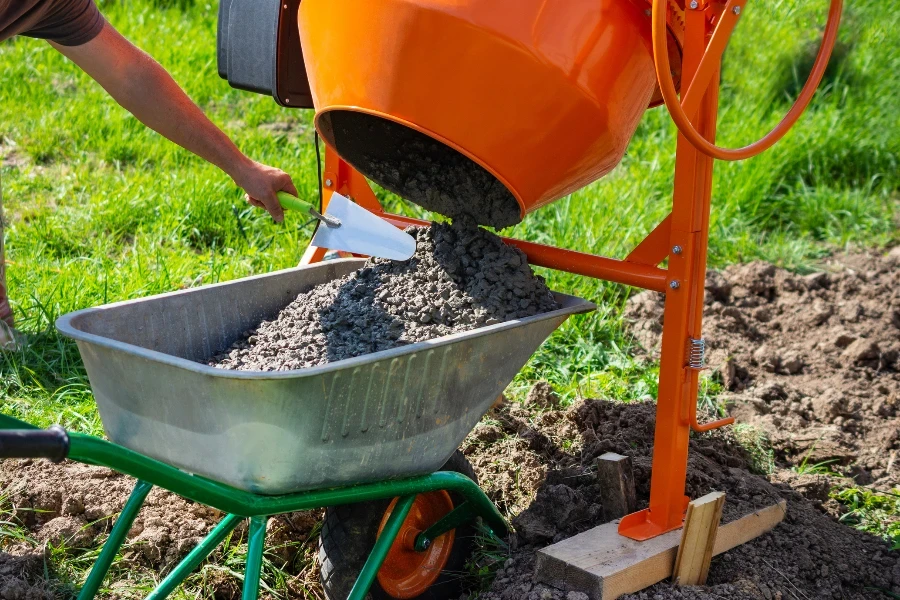
Maintaining concrete mixers is paramount to ensure their longevity and reliability. Regular cleaning is essential to prevent concrete from hardening inside the mixer, which can be labor-intensive to remove and can cause damage over time. Lubrication of moving parts, checking for wear and tear, and replacing worn-out components are also critical maintenance practices.
Scheduled maintenance should not be overlooked. Following the manufacturer’s guidelines for service intervals can prevent breakdowns and extend the mixer’s lifespan. Keeping a maintenance log can help track the health of your mixer and predict when parts might need replacement.
Safety considerations
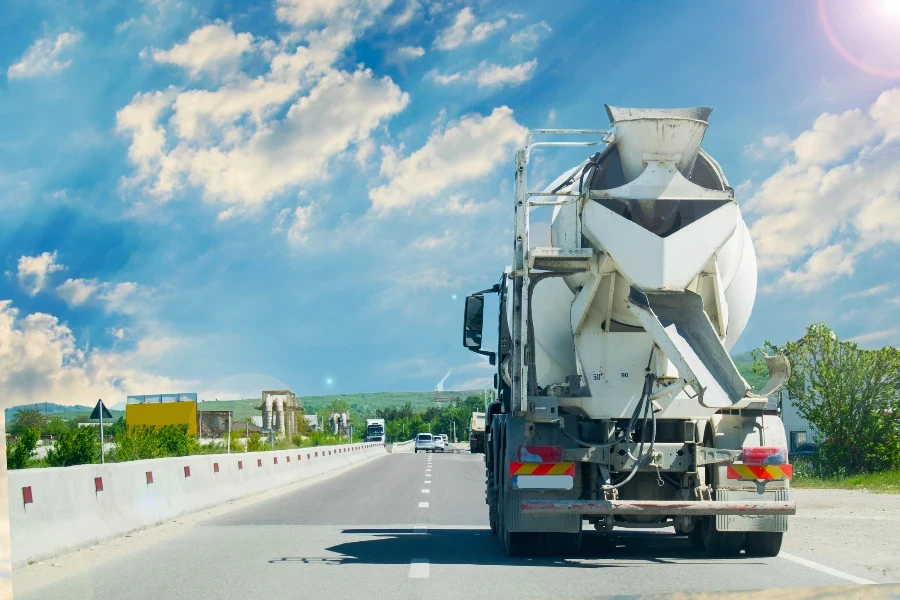
Operating concrete mixers involves several safety considerations to protect the operator and bystanders. First and foremost, wearing appropriate personal protective equipment (PPE) such as gloves, safety goggles, and hearing protection is non-negotiable. Additionally, ensuring that all safety guards and devices are in place and functional before operation is crucial.
Training is another critical aspect. Operators should be thoroughly trained in the safe operation of the mixer, including emergency stop procedures. Regular safety meetings can help reinforce these practices and keep safety at the forefront of everyone’s mind.
Technological advancements in concrete mixers
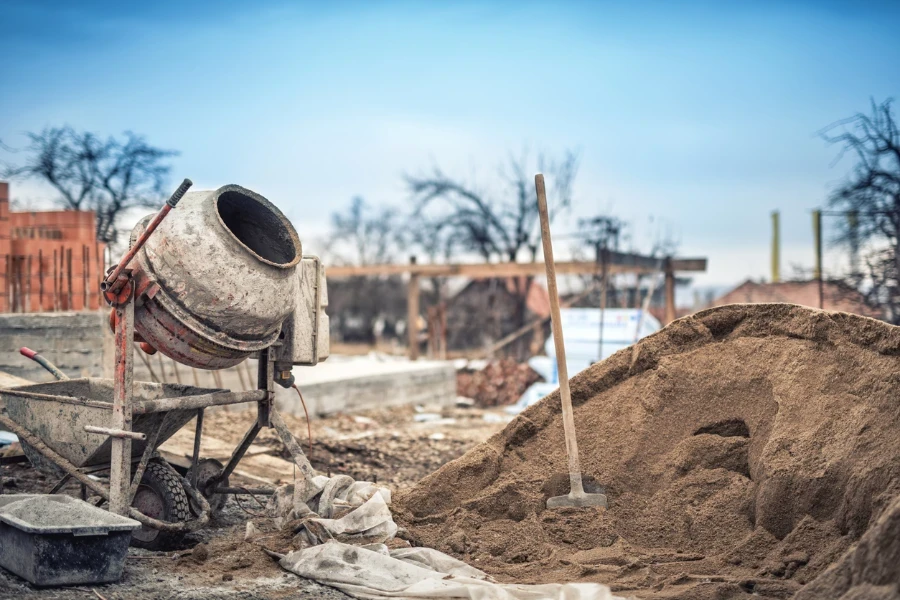
The world of concrete mixers is not static; technological advancements continue to revolutionize how these machines operate. Modern mixers now boast improved efficiency, reduced emissions, and enhanced safety features. For example, some mixers come equipped with GPS tracking and monitoring systems, allowing fleet managers to optimize routes and monitor usage.
Automation is another area of significant advancement. Some contemporary models feature automated loading and mixing processes, reducing manual labor and improving consistency. The integration of electric and hybrid systems is also gaining traction, offering a greener alternative to traditional diesel-powered mixers.
Conclusion
Concrete mixers play a pivotal role in construction, blending the essential components of concrete to build structures around us. Understanding the types of mixers, how they work, and their maintenance and safety considerations is crucial for anyone involved in construction. With technological advancements continually shaping the industry, staying informed is key to leveraging these machines’ full potential.