When JIT was first introduced in the 1970s by the Toyota employee Taiichi Ohno in Japan, nobody fathomed how it would revolutionize businesses. It reduces waste by only delivering what is required after customers have placed orders. Today, JIT is a widely popular concept embraced by old and new practices alike.
Table of Contents
What is JIT, by the way?
Examples of Just in Time in action
Advantages of Just in Time
Disadvantages of Just in Time
Polish the Just in Time strategy
What is JIT, by the way?
JIT is a management philosophy that seeks to align raw materials to specific production lines when needed to maintain the lowest possible volume of stock and raw material at hand. It is characterized by;
- Unique and flexible division of labor
- Continuous flow of goods and raw materials in small quantities
- Automated purchasing
- Short delivery time
- Preventive maintenance
- Close up ties with suppliers
- Local sourcing, in most cases
To ensure smooth processes, JIT is famous for using Kanban, a task management framework invented in the 1940s that aims at balancing demands with the available workforce. Employees are allocated to specific workstations and as goods flow through each stage, everyone can visualize the process on shared boards aiding in informed decision-making and prevention of shortages of raw materials on the production lines.
Examples of Just in Time in action
1. Toyota
Toyota started implementing the JIT system after World War II to get the best out of scarce resources, minimize waste, and cope with the competition. So, instead of producing thousands of specific models per time like the USA, Toyota opted for an “order before we manufacture” approach.
The model soon gained root taking advantage of Japan’s tiny landmass, which reduced transport time. Between 1960 and 1980, the efficient system, which was then producing cheap cars, pushed Toyota into the USA market with much success. In 1966, Toyota’s supplies tripled to 20,000, and the company became the third-best-selling import brand in that country.
2. Retailers
Retailers such as Walmart and Target use JIT to minimize inventories and clear up shelf spaces. Using forecasting techniques, they predict purchasing patterns and schedule the inflow of seasonal merchandise when the demand is high. Shelves are freed as the season fades away.
3. Apple
Redeemed from the verge of stalling into a profitless venture, Apple is one of the giants reaping JIT’s benefits. It all started when Apple hired Tim Cook as the worldwide operation’s vice president in 1998. He shut down international factories and warehouses while establishing close ties with independent, cheap, and reliable contractors from China, which inadvertently led to the company adopting JIT.
4. Kellogg’s
Given Kellogg’s over 100 years of producing snacks, it is unsurprising that Just in Time is at the heart of its tasty treats to efficiently manage perishable ingredients. The company always ensures it has enough to take care of ordered products.
5. Zara
With over 450 million items reaching the market annually, Zara manages an efficient production system by regularly meeting small batches of deliveries to its 2000+ stores biweekly.
Advantages of Just in Time
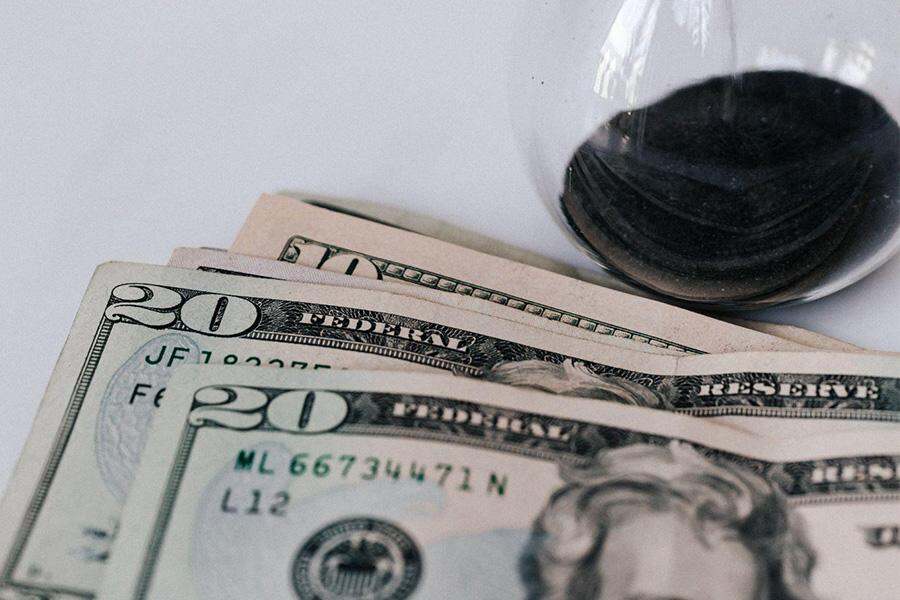
Just In Time is key to improving efficiency and productivity, and maximizing returns.
Reduced cost
Working on limited stock reduces costs by saving on rent, labor, electricity, and time required to man large warehouses.
- Low wastages
JIT prunes off waste management costs by keeping waste levels low.
- Reduced working capital flowing through the system
Working capital is the amount of money used to run the day-to-day operations. JIT reduces this by limiting warehousing expenses and minimizing inventory cycles.
- Less dead stock
When finished goods stay in the warehouse for long, they become dead stock or obsolete inventory. The longer the goods are stored, the more detrimental the effect is to businesses since they must be converted into cash to settle bills and earn profit. In a JIT system, because a company fulfills only pending orders, accumulation of dead stock is not likely.
Continuous improvement of a product’s quality
A well-trained and flexible workforce invests more time in improving quality, which is equal to a high satisfactory rate.
- Reduction of goods under work in progress
Employees worry less about clearing pending tasks, thus working more on delivering great results.
- Product uniformity
Product uniformity is crucial when promising customers consistent quality. JIT achieves that by standardizing operation procedures.
Improved efficiency
JIT eliminates excesses by opening up stations and smoothening delivery lines. It also does away with unneeded raw materials and finished goods, giving the company time to plan for the next orders.
- Local sourcing
Having suppliers a stone’s throw away increases response time and reliability, and eliminates transport-related breakages.
- Reduces obsolete stock
A high inventory turnover rate reduces the time goods stay in the warehouse, which in turn prevents stock obsolescence.
Disadvantages of Just in Time
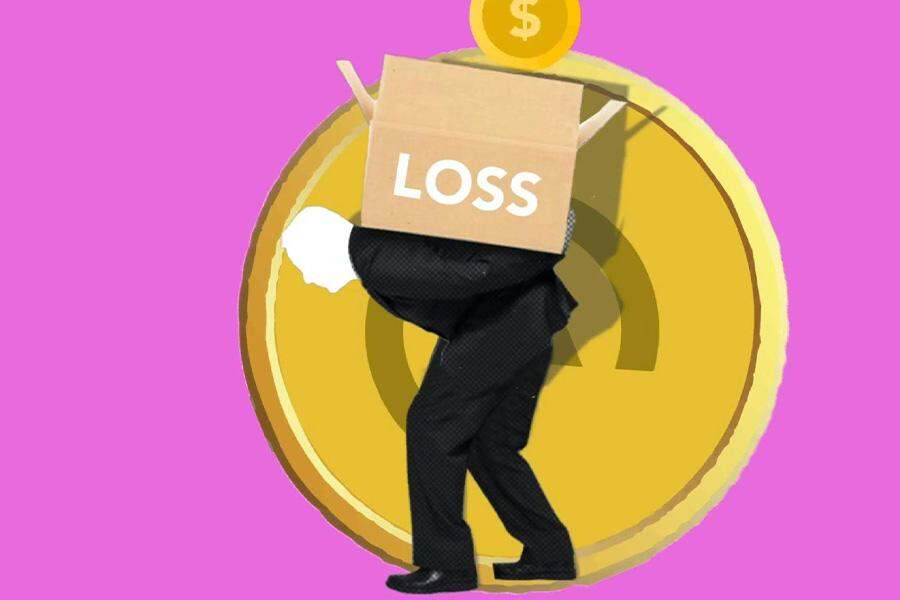
JIT counts on everyone in the production channel to work flawlessly. In business, there is no such thing; thus, breakdowns are common and affect the entire infrastructure.
Timeliness problems
It is quite difficult to implement timeliness in the entire system, especially if the management does not oversee supply chains.
- Over-reliance on suppliers’ timeliness
Over-dependence on suppliers’ timeliness is risky, and glitches are damaging and well-pronounced especially when working with large orders.
A business may, however, avert this danger by frequently vetting suppliers and having multiple go-to options.
Cost disadvantages
JIT often incurs high transaction and production rerun costs due to the inability to capitalize on economies of scale.
- High rerun costs
Correcting defects is expensive when there are no raw materials at hand.
- Diseconomies of scale
Diseconomies of scale results in the increased marginal cost of production.
- High transactions costs
Transaction costs cover the exchange of goods and services. They include commissions and bank charges, and in JIT, because there are so many exchanges, transaction costs are high.
Increased dependence on forecasts
Due to unpredictable customers’ behaviors, companies using JIT depend on forecasts to determine when demand will be high and prepare their teams and suppliers for that. Unfortunately, forecasts are not accurate; hence businesses end up pursuing false leads.
Unexpected price changes have a devastating effect
JIT adopters do not have the luxury of holding stock in anticipation of better prices. In fact, with a slight dip in price, businesses end up selling goods at the prevailing price despite acquiring raw materials at a higher cost.
Acts of nature
Natural disasters disrupt the inflow of raw materials, halting production. For example, the aftermath of the 2011 tsunami in Japan left Toyota scrambling for new supply lines to secure more than 1200 parts.
Large investments in developing communication networks
An investment in up-to-date computer technologies linking stakeholders is a must for Just in Time to run effortlessly. This requires a lump sum cash injection and may be unaffordable to many startups. Furthermore, businesses must hire trained IT personnel to run and protect shared information against hackers.
Polish the Just in Time strategy
JIT is an inventory management system invented in Japan for Toyota and has been adopted by many companies throughout its lifetime. The system takes orders from customers, requests what it needs, and processes that into finished products. Businesses benefit from JIT because it reduces warehousing expenses, smoothens production output, and ensures product uniformity.
Unfortunately, manufacturers can incur high transaction costs, deal with frequent delays, and bear the risk of price changes. Luckily, meticulous planning, fine-tuning supply chains, and pausing to consider risks will be useful in reducing JIT production inconsistencies.
As you continue polishing the Just in Time strategy, here are smart supplier management strategies.