The world of metal fabrication is elaborate. Press brake machinery plays a critical role in this world. This article will enlighten you on all you need to know about the press brake – from the basics to its types, features, maintenance tips, and the latest innovations in this field. Whether you’re a beginner or an expert in the metalworking industry, this article will provide you with insight so you can appreciate the functioning of this sophisticated piece of machinery.
Table of Contents:
– What is a press brake?
– Types of press brakes
– Key features to look for
– Maintenance tips for longevity
– Latest technological advancements
What is a press brake?
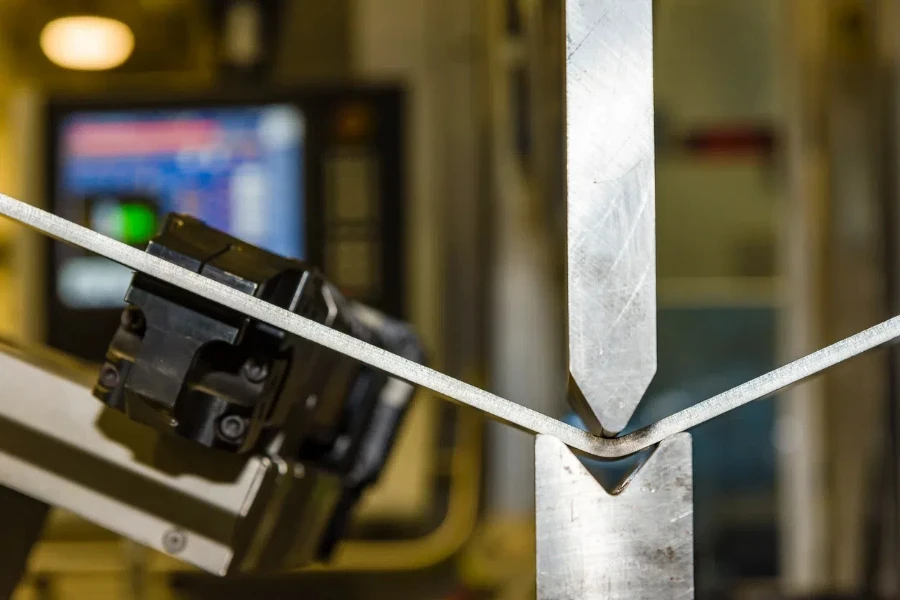
The press brake is a key component of sheet metal fabrication machinery which allows for the bending and shaping of metal sheets. At its simplest, a press brake uses a punch and die set to form a predefined bend by clamping the metal sheet between them. This hold, in concert with the force of the hydraulic press, is what forms the metal into shape. But the press brake isn’t about just changing the shape of a piece of metal – it involves fine details and a whole lot of accuracy that reduces a precision component to mathematical terms.
To anyone involved in metalworking, it is vital to understand how press brakes operate – what forces are delivered, how much the material is bent, and what metal properties matter. Only an intricate interplay of physics and engineering allows us to shape steel and aluminium parts used in automobiles, structural steelworks, and everything in between.
The press brakes have become much more sophisticated than earlier versions, and safer to use. They are also more productive and precise, thanks to CNC (Computer Numerically Controlled) technology. This relies on software to control the movement of the ram or forming axis, and the pneumatic or hydraulic power used to apply force.
Types of press brakes
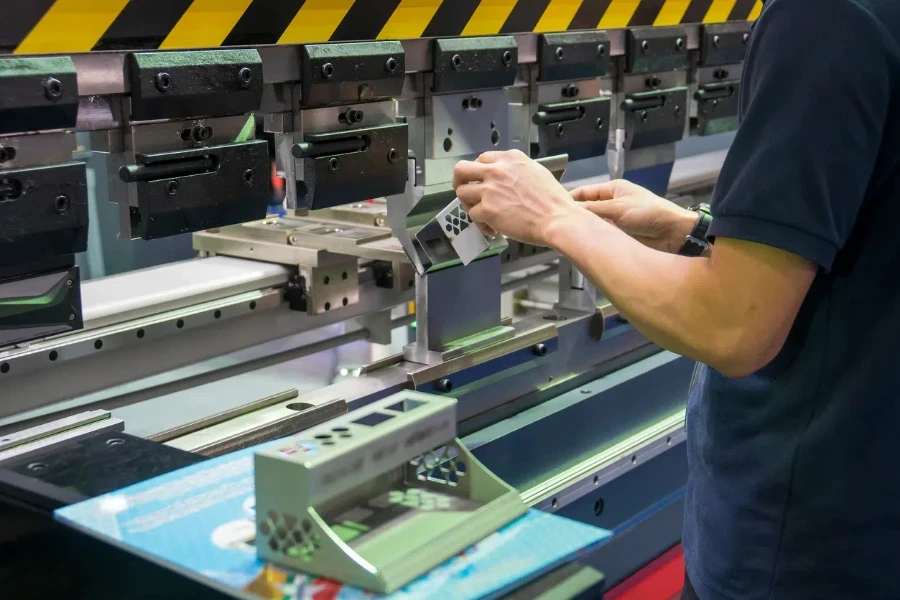
Press brake types are many. Depending on the application, you will choose one over another, from a manual press brake for small, custom jobs to hydraulic and electric press brakes designed for high-volume productions. This guide illustrates the differences between these types to help you decide the right press brake for your needs.
The hydraulic press brake, being a powerful electric press brake is equipped with a hydraulic fluid to push ram for big scale application in order to provide a more smoothy and accurate bending cycle. Meanwhile, being an electric powered press brake, electric press brake has a specialty in energy saving and short clamping times which are leading to be the right choice for all those companies which are keen on cutting carbon footprint and work cost.
One of the less common types of press brake is the mechanical press brake, which utilises a flywheel and crank mechanism to drive its punch. Mechanical press brakes are relatively inexpensive, and simple to operate. They are particularly appropriate for certain bending operations. Each of these press brake types has advantages and disadvantages depending on what you need to do.
Key features to look for
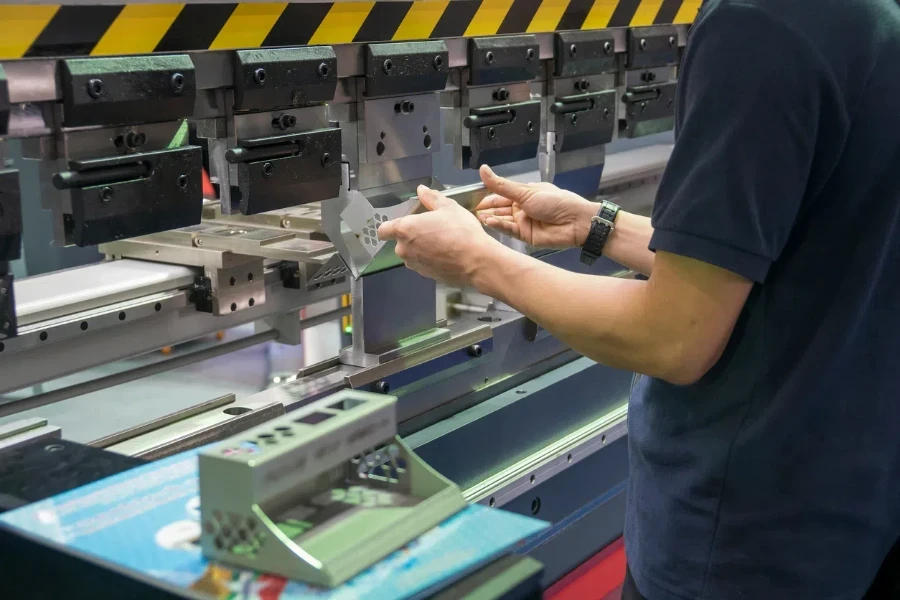
When selecting a press brake for one’s needs, some of its most important features include, but are not limited to, its capacity: maximum bending length and pressing force, which determines the machine’s capability for processing metal sheets of different sizes and thicknesses. The machine must be able to handle your smallest and thickest parts.
Another element to consider is the system of control. Modern press brakes fitted with CNC controls allow for extraordinarily exact bending operations to be set and performed with minimal human intervention, with multiple programs stored for repeated runs to ensure consistency of part quality.
Compatibility with tooling is also important. The more dies and punches that are compatible with your press brake, the more things you can bend. Buying a press brake that allows you to use more tooling means you can take on more jobs.
Maintenance tips for longevity
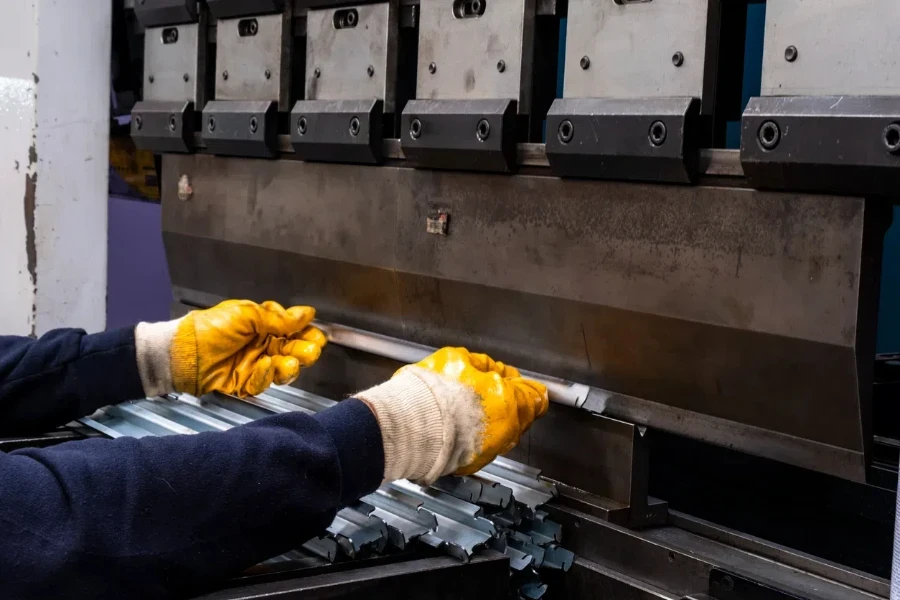
It is necessary to perform maintenance on your press brake as this will prolong the life of your machine and keep it in good working order. There are a few basic maintenance tasks in which you can perform on your machine which will reduce the risk of your machine breaking down and allow you to produce optimal bends.
Clean the machine on a regular basis to remove any dirt or debris that could interfere with the machine.
Lubricate moving parts in order to reduce wear on the machine which will extend the life of your machine and reduce maintenance costs.
You must also periodically inspect the hydraulic system for leaks and the electrical components for wear, and fix these problems before they get worse. Moreover, if the tooling is good and properly set up, it will prevent the machine from being damaged and the workpiece from being ruined.
Training your operators to understand how it’s supposed to operate and what maintenance requirements it has is a great compliment to the press brake and will improve its up time and stamina. A properly maintained press brake is a great tool to have in your metal fabrication shop.
Latest technological advancements
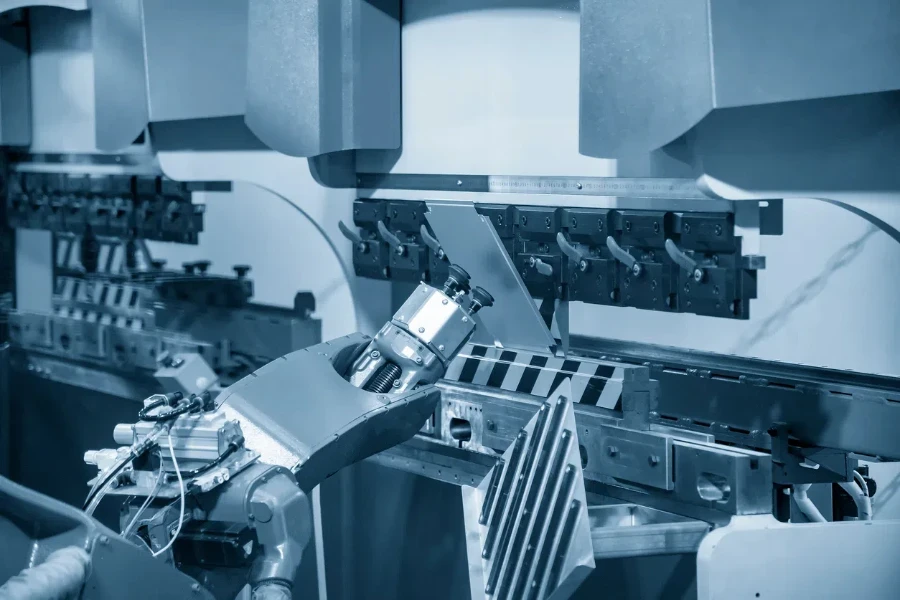
The press brake industry is constantly growing through technological advancement to improve productivity, accuracy and safety. One of the main advancements in technology is the integration of Internet of Things (IoT) ability for the presses, which enables real time monitoring and tracking data for analysis and in turn could lead to predictive maintenance leading to less downtime and more productivity.
The second major field is automation: robotic press brakes can handle the whole process, from sheet loading and unloading to bending , which is more efficient and requires labour. The systems are able to adjust to different workpiece sizes and shapes.
Another innovation to note is adaptive bending technology, which compensates in real-time for material variation in the strip, and corrects for it, so the angle of bending is constant regardless of material variations.
Conclusion:
Press brakes play a vital role in the metal working industry as they provide the precision and flexibility to keep up with modern manufacturing needs. By grasping the different types of press brakes and its components, knowing how to maintain them properly, and keeping up with new technologies; all these concerns have a direct impact on your manufacturing processes and product quality. Continuously evolving in its methodologies and technological advancements, anyone looking to dominate the metal working industry must be literate in these insights and innovations.