In an era where consumer expectations are sky-high, and the marketplace is more competitive than ever, understanding and implementing effective quality control (QC) has become a cornerstone for any business aiming to thrive. Quality control, a term often heard but not always fully grasped, is the linchpin in ensuring product excellence, customer satisfaction, and operational efficiency. This article aims to demystify quality control, breaking it down into its fundamental components, and exploring why it’s not just important but essential in today’s business landscape.
Table of Contents:
– What is quality control?
– The importance of quality control in manufacturing
– How quality control impacts customer satisfaction
– Quality control techniques and tools
– The future of quality control in business
What is quality control?
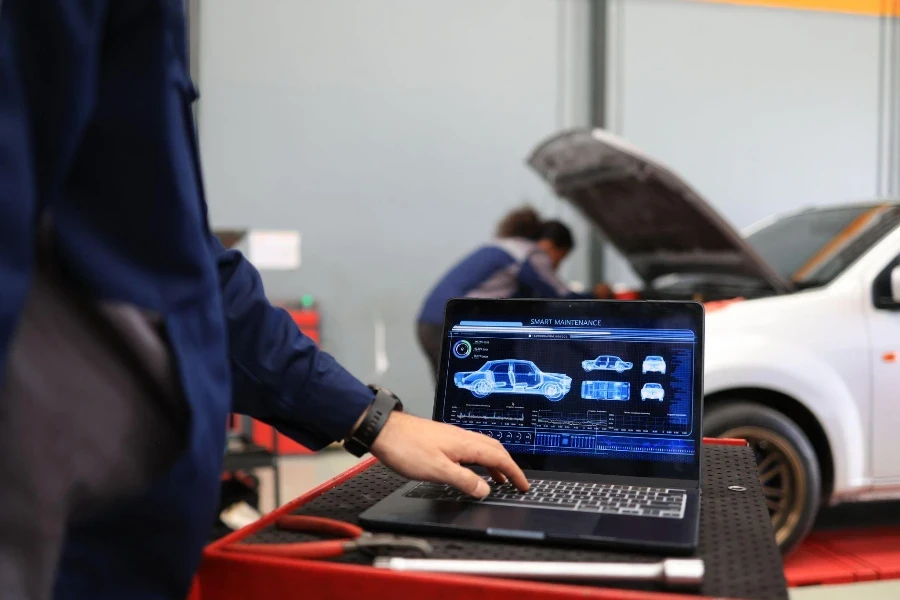
Quality control is a process designed to ensure that a product or service meets certain standards of quality or complies with a specific set of regulations. It involves the systematic inspection, testing, and verification of various aspects of a product or service to ascertain its quality. The goal is to identify and correct defects before the product reaches the customer, ensuring that only high-quality products leave the production line.
Quality control is not a one-off activity but a continuous process that involves every stage of production, from the sourcing of materials to the final inspection before delivery. It requires a collaborative effort across various departments within an organization, including procurement, manufacturing, and logistics, to name a few.
Implementing effective quality control measures can significantly reduce waste, lower costs, and improve the overall efficiency of production processes. It’s a proactive approach that not only addresses issues as they arise but also anticipates potential problems and puts measures in place to prevent them.
The importance of quality control in manufacturing
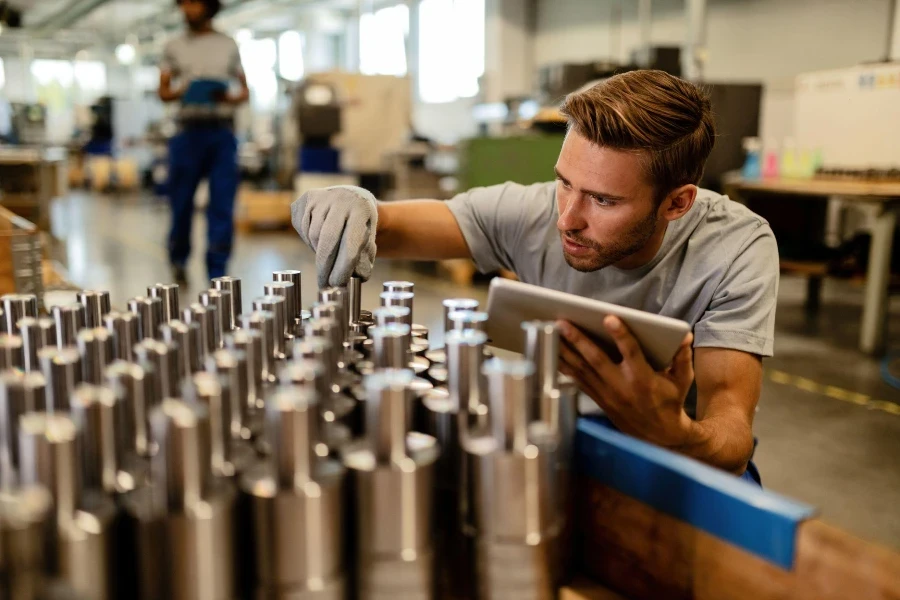
In the manufacturing sector, quality control is paramount. It’s the backbone that supports the production of goods that meet or exceed customer expectations. A strong QC process ensures consistency, which in the eyes of the consumer, translates to reliability. This consistency is what builds brand loyalty and trust over time.
Manufacturers face the challenge of balancing cost, efficiency, and quality. Quality control plays a critical role in this balancing act, providing a framework that helps identify inefficiencies and areas for improvement. By catching defects early, manufacturers can avoid costly recalls and reputational damage, which can have long-term financial implications.
Furthermore, in a global market, adherence to international standards of quality is crucial. Quality control processes enable manufacturers to comply with these standards, facilitating smoother entry into new markets and fostering competitive advantage.
How quality control impacts customer satisfaction
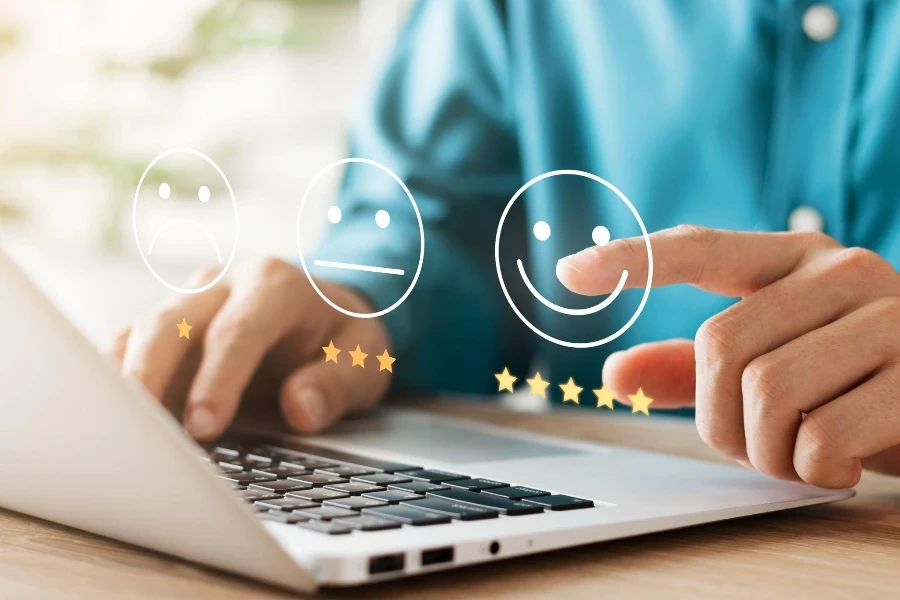
Customer satisfaction hinges on the quality of the product they receive. In today’s digital age, a single negative review can significantly impact a brand’s reputation. Quality control acts as the first line of defense against this, ensuring that products meet customer expectations right from the outset.
Quality control also plays a vital role in product development. By gathering and analyzing data from QC processes, businesses can gain insights into customer preferences and areas for product improvement. This customer-centric approach not only enhances satisfaction but also drives innovation.
Moreover, the transparency of quality control processes can strengthen customer trust. Businesses that openly share their commitment to quality and the measures they take to ensure it can build deeper, more meaningful relationships with their customers.
Quality control techniques and tools
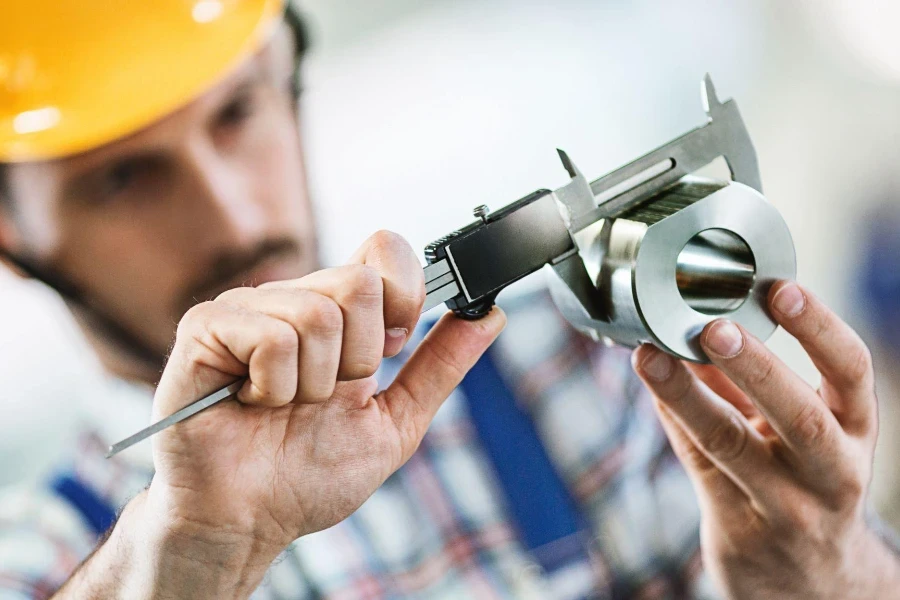
There are various techniques and tools employed in quality control, each suited to different types of products and industries. Common techniques include statistical process control (SPC), which uses statistical methods to monitor and control production processes, and Total Quality Management (TQM), a holistic approach that focuses on long-term success through customer satisfaction.
Tools such as control charts, which graphically display process data over time, and Pareto charts, which highlight the most significant factors in a dataset, are instrumental in identifying trends and pinpointing areas for improvement.
The choice of technique and tool depends on the specific requirements of the product and the goals of the quality control process. Regardless of the method, the aim is always to improve product quality, reduce variation, and eliminate waste.
The future of quality control in business
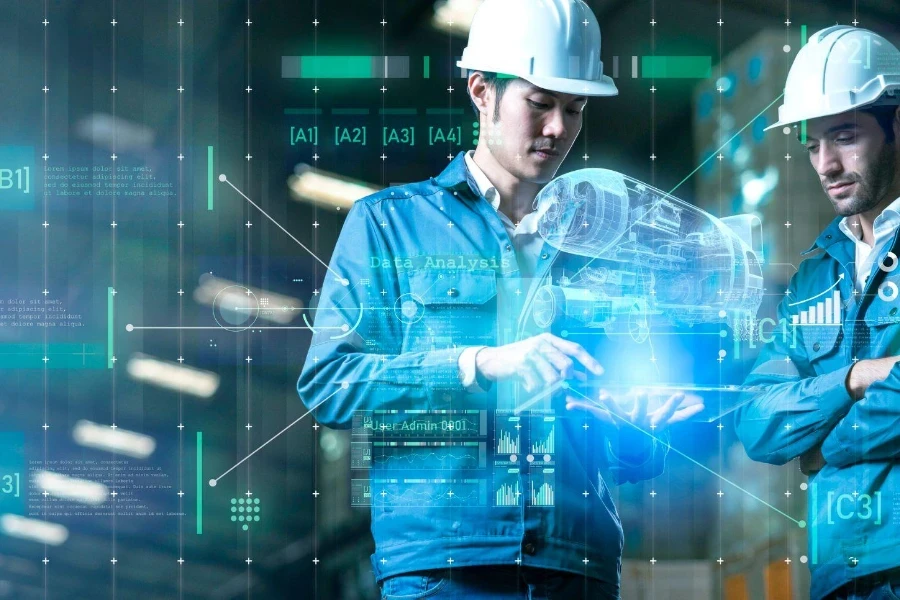
As technology advances, so too does the landscape of quality control. The integration of artificial intelligence (AI) and machine learning (ML) into QC processes is set to revolutionize how businesses monitor and maintain quality. These technologies offer the potential for real-time monitoring and predictive analytics, enabling businesses to anticipate and address quality issues before they occur.
Moreover, the rise of the Internet of Things (IoT) allows for greater connectivity and data collection across the production chain. This data can be used to enhance quality control measures, streamline operations, and improve product design.
The future of quality control is dynamic and promising, with new technologies paving the way for more efficient, effective, and innovative QC processes. As businesses continue to navigate the complexities of the modern marketplace, quality control will remain a critical factor in achieving success and maintaining competitive edge.
Conclusion
Quality control is more than a set of procedures; it’s a philosophy that permeates every aspect of a business, influencing its operations, its products, and its relationships with customers. As we look to the future, the role of quality control in ensuring product excellence and customer satisfaction will only grow in importance. By embracing new technologies and continuing to prioritize quality, businesses can position themselves for long-term success in an ever-evolving marketplace.