Rack and pinions are fundamental components in the machinery world, translating rotational motion into linear motion with precision and efficiency. This guide aims to shed light on their design, applications, maintenance strategies, and the latest advancements in the field. By breaking down complex concepts into accessible explanations, we invite readers to explore the intricacies of rack and pinions, understanding their critical role in various industries.
Table of Contents:
– What are rack and pinions and how do they work?
– Key applications of rack and pinions in industry
– Design considerations for optimal performance
– Maintenance tips for longevity and reliability
– The future of rack and pinions: Innovations and advancements
What are rack and pinions and how do they work?
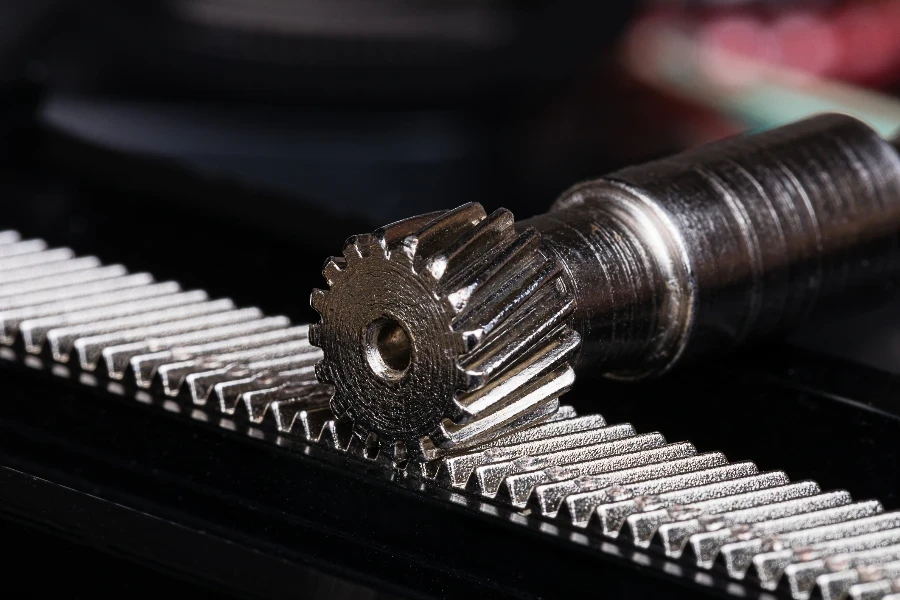
Rack and pinions are integral to converting rotational motion into linear motion. This mechanism involves a circular gear—the pinion—engaging with a linear gear—the rack. As the pinion rotates, its teeth mesh with those of the rack, moving it linearly. This simplicity in design belies the precision and efficiency with which rack and pinions operate, making them indispensable in many mechanical systems.
Understanding the mechanics involves appreciating the interplay between the rack’s linear movement and the pinion’s rotation. The size and shape of the teeth are crucial, as these factors directly influence the mechanism’s efficiency and the type of motion produced. The materials used in their construction also play a significant role, affecting durability and suitability for specific applications.
The elegance of rack and pinion systems lies in their versatility. By adjusting the gear ratio, one can control the speed and force of the linear motion, tailoring the system to meet various operational requirements. This adaptability, combined with the mechanism’s straightforward design, explains its widespread use across numerous fields.
Key applications of rack and pinions in industry
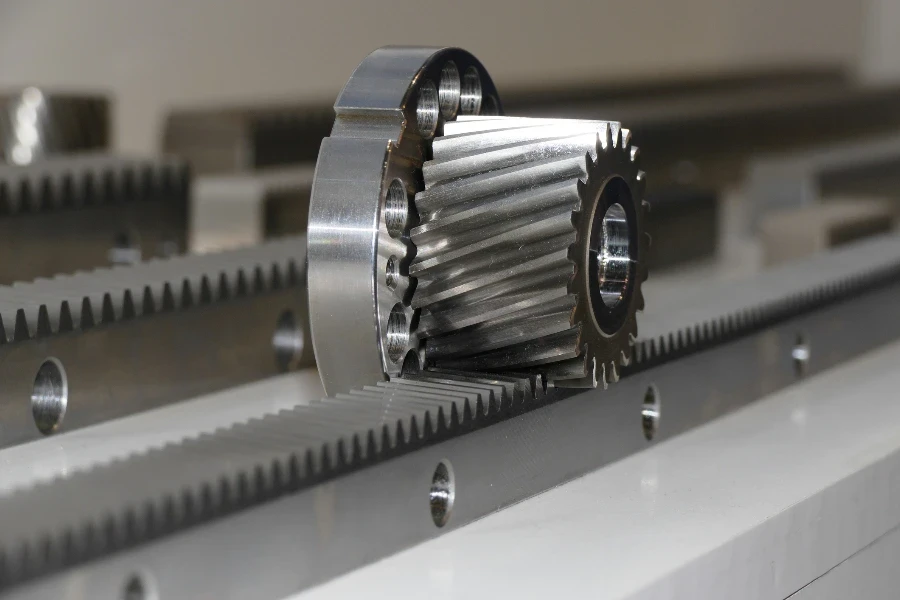
Rack and pinions find their place in a myriad of industrial applications, showcasing their versatility and efficiency. In the automotive industry, they are pivotal in steering systems, enabling drivers to maneuver vehicles with precision and ease. The linear motion produced by the rack and pinion allows for smooth steering, translating the rotational motion of the steering wheel into the lateral movement of the wheels.
Another significant application is in the manufacturing sector, particularly in CNC (Computer Numerical Control) machines. These machines rely on rack and pinion systems for precise linear movement, essential for cutting, engraving, and shaping materials with accuracy. The ability to produce consistent, high-quality results makes rack and pinions indispensable in this context.
Furthermore, rack and pinion setups are crucial in railway systems, especially in mountainous regions where traditional trains struggle. The rack and pinion engage to provide the necessary traction, allowing trains to ascend and descend steep inclines safely. This application underscores the system’s reliability and effectiveness in challenging environments.
Design considerations for optimal performance
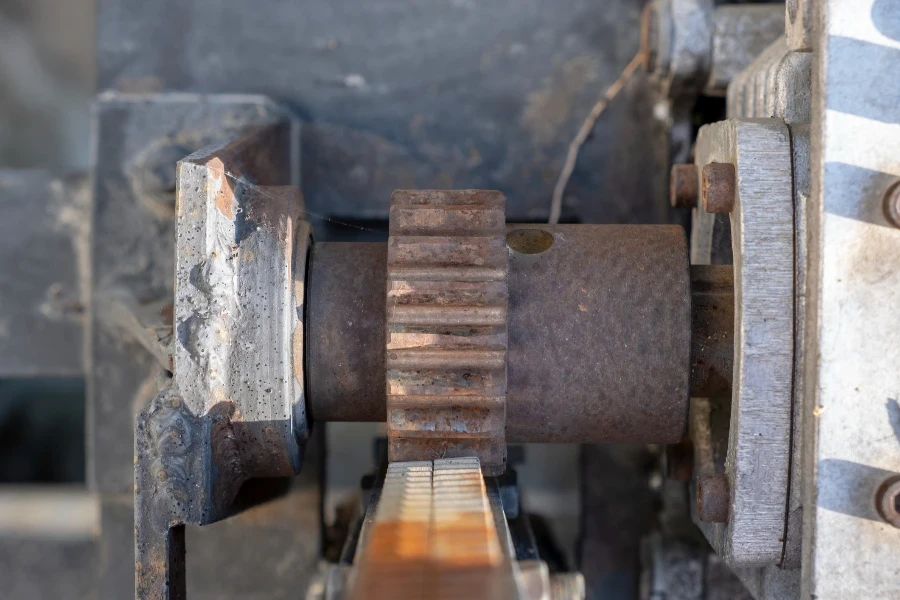
Designing a rack and pinion system requires careful consideration of various factors to ensure optimal performance. The choice of material is paramount, as it must withstand the operational stresses and environmental conditions. Metals like steel are commonly used for their durability and strength, but advances in materials science have introduced high-performance plastics and composites as viable alternatives for certain applications.
The geometry of the teeth is another critical aspect, influencing the efficiency of power transmission and the smoothness of the motion. The design must minimize backlash—the gap between the teeth when the direction of motion is reversed—to ensure precision and reduce wear.
Lubrication is also a key factor in the design process, essential for reducing friction and preventing premature wear. The selection of a suitable lubrication system, whether it’s grease, oil, or advanced synthetic lubricants, depends on the application’s specific requirements, including speed, load, and environmental conditions.
Maintenance tips for longevity and reliability
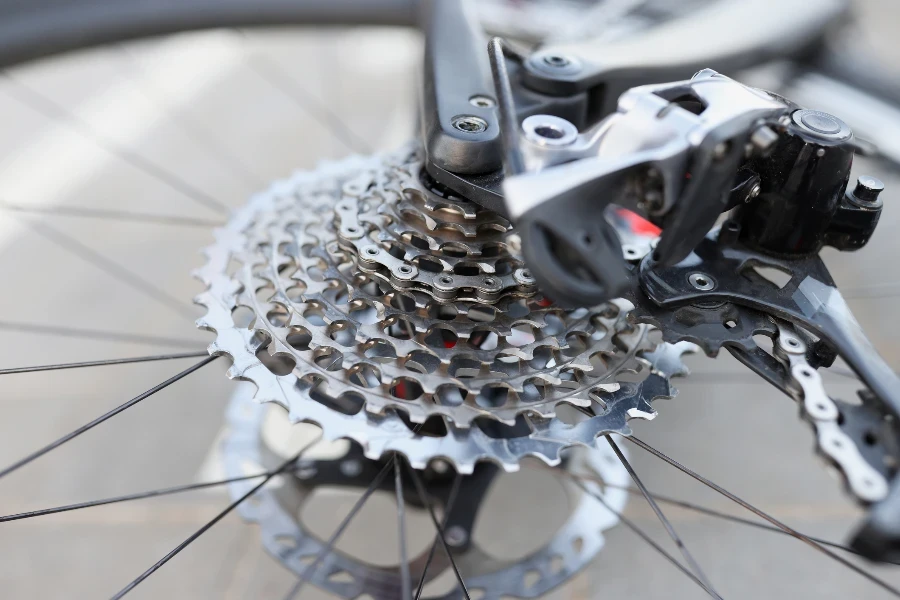
Maintaining rack and pinion systems is crucial for ensuring their longevity and reliability. Regular inspections are necessary to identify wear and tear, particularly on the teeth, where damage can lead to inefficiencies and potential system failure. Early detection and replacement of worn components can prevent costly downtime.
Lubrication plays a vital role in maintenance, reducing friction and wear. Establishing a routine lubrication schedule, tailored to the system’s operational demands and environmental conditions, is essential. Additionally, keeping the system clean from debris and contaminants will prolong its life and maintain optimal performance.
Adjustments may be required to address backlash and ensure the system operates smoothly. This involves realigning the rack and pinion to minimize gaps between the teeth, a process that requires precision and expertise.
The future of rack and pinions: Innovations and advancements
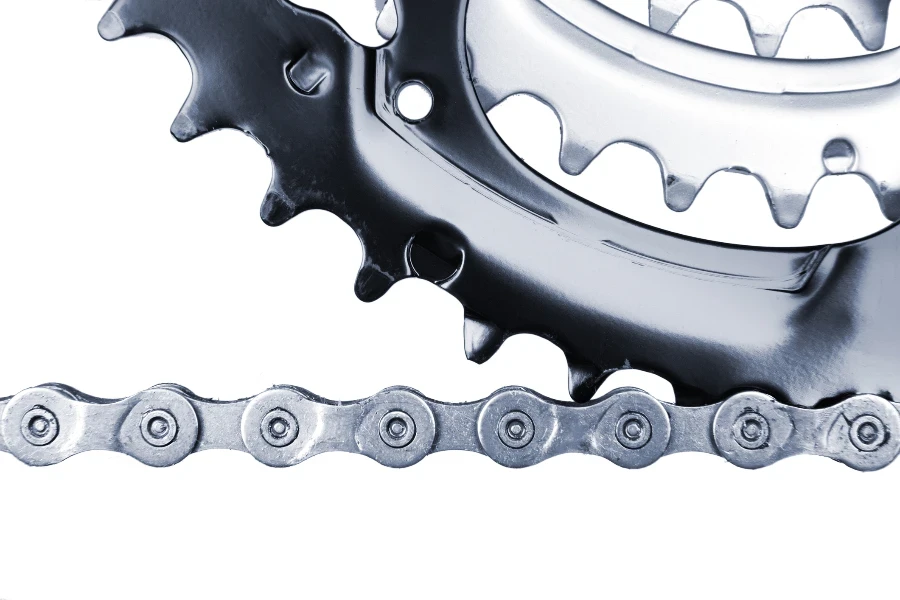
The future of rack and pinions looks promising, with ongoing innovations and advancements enhancing their performance and applications. Material science developments are leading to lighter, stronger, and more durable components, expanding their use in demanding environments. Additionally, the integration of smart technologies, such as sensors and IoT (Internet of Things) devices, is enabling predictive maintenance, reducing downtime and extending the life of the systems.
Advancements in manufacturing techniques, such as 3D printing, are revolutionizing the production of rack and pinion systems. This allows for the creation of complex geometries and customized solutions, opening new possibilities in design and application.
As industries continue to evolve, the demand for efficient, reliable motion control systems grows. Rack and pinions, with their simplicity, versatility, and efficiency, are well-positioned to meet these challenges, driving innovation and progress across various sectors.
Conclusion:
Rack and pinions are more than just mechanical components; they are the backbone of motion in countless applications across industries. Understanding their design, applications, and maintenance is crucial for harnessing their full potential. As we look to the future, the ongoing advancements in materials, technology, and manufacturing promise to expand their capabilities even further. Embracing these innovations will enable industries to achieve greater efficiency, precision, and reliability, solidifying the role of rack and pinions in the machinery of tomorrow.