In the intricate world of manufacturing and machinery, maintaining the right temperature is not just beneficial; it’s imperative. A mould temperature controller plays a pivotal role in ensuring this precision. This article will explore the nuances of mould temperature controllers, shedding light on their importance, functionality, types, maintenance, and selection process. By demystifying these aspects, we aim to empower you with the knowledge to enhance your machinery’s performance and longevity.
Table of Contents:
– Importance of mould temperature control in machinery
– How do mould temperature controllers work?
– Types of mould temperature controllers
– Maintenance tips for mould temperature controllers
– Selecting the right mould temperature controller
Importance of mould temperature control in machinery
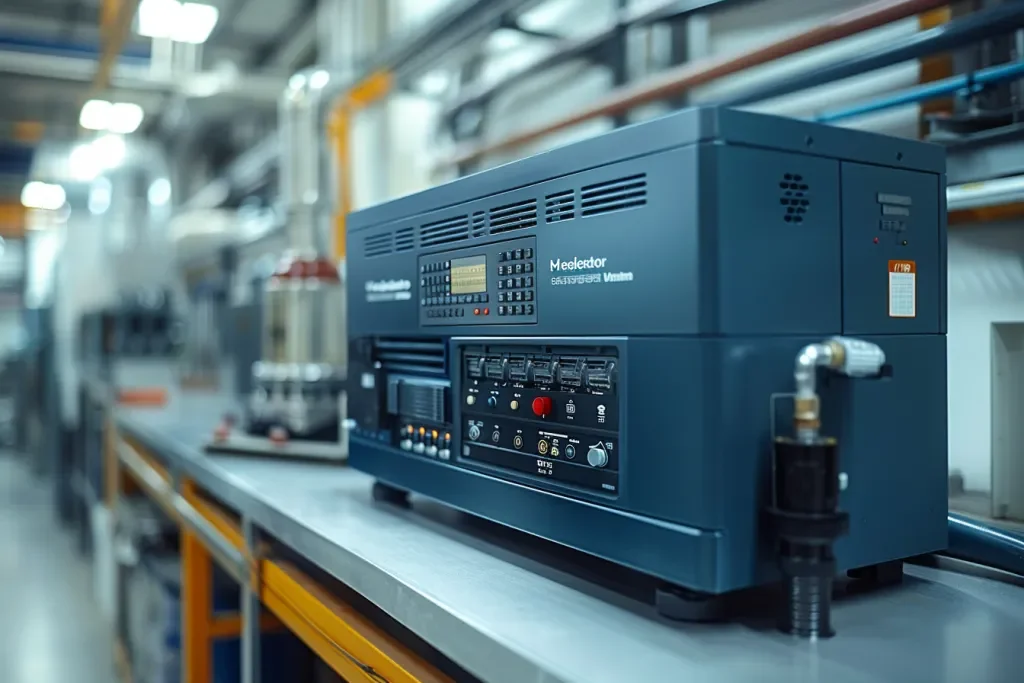
Temperature control in the moulding process is not just about keeping the materials at a manageable temperature; it’s about precision and the fine balance that leads to optimal product quality. The first paragraph dives into the critical role temperature plays in the consistency of the material properties during the moulding process. Uniform temperature distribution ensures minimal internal stress, reducing the risk of defects.
In the second paragraph, the focus shifts to the impact of temperature control on cycle times. Proper temperature regulation can significantly reduce cycle times, enhancing productivity and efficiency in manufacturing processes. This not only leads to a more streamlined operation but also contributes to energy savings and cost reduction.
The third paragraph explores the environmental aspect of efficient temperature control. By optimizing the moulding process, there is a notable reduction in waste production and energy consumption. This not only benefits the manufacturer in terms of cost savings but also contributes to environmental sustainability.
How do mould temperature controllers work?
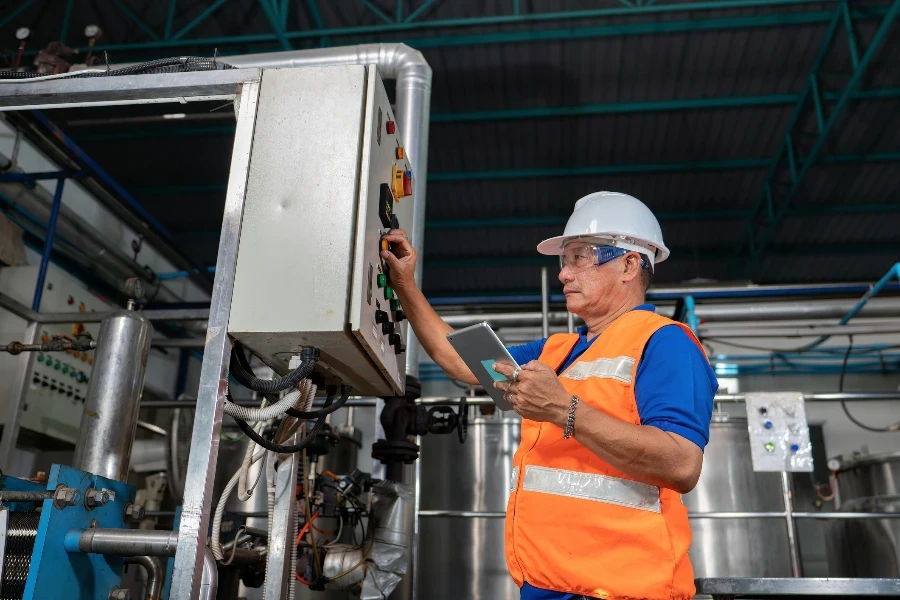
Understanding the functionality of mould temperature controllers is crucial for leveraging their benefits. In the first paragraph, we’ll break down the basic principle behind these controllers, which involves the transfer of heat to or from the mould to maintain a set temperature. This process is critical for ensuring the material within the mould is at the optimal temperature for solidification or curing.
The second paragraph delves into the components that make up a mould temperature controller, including the heating and cooling units, temperature sensors, and control unit. Each component plays a vital role in the accurate and efficient operation of the system, ensuring precise temperature control throughout the moulding process.
In the third paragraph, we discuss the advanced features found in modern mould temperature controllers. These include programmable settings, digital displays, and automated monitoring systems that enhance the user’s ability to maintain precise control over the moulding process, leading to improved product quality and operational efficiency.
Types of mould temperature controllers
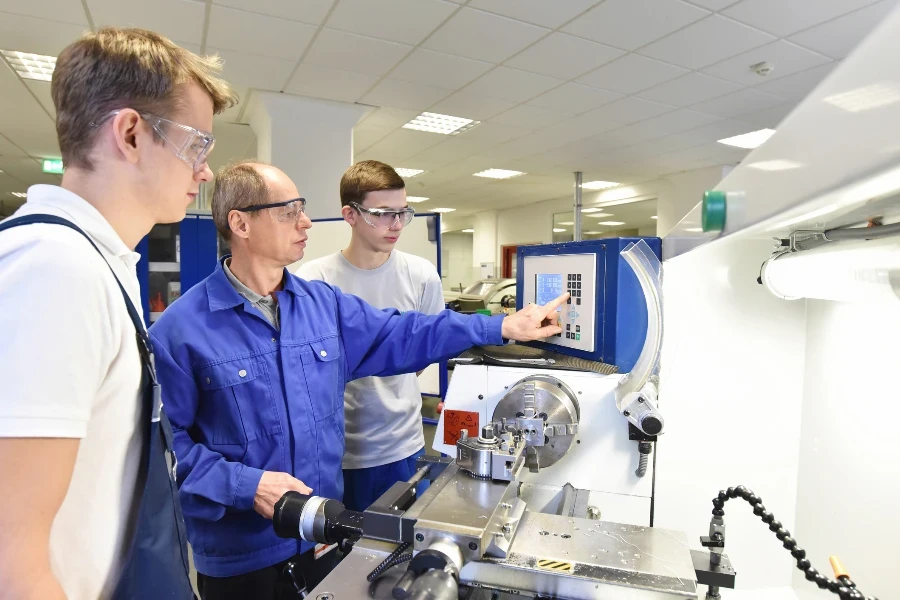
There are various types of mould temperature controllers available, each suited to different applications and materials. The first paragraph introduces water-based and oil-based temperature controllers, highlighting their respective advantages and ideal use cases. Water-based controllers are typically used for lower temperature applications, while oil-based controllers are suitable for higher temperature needs.
The second paragraph focuses on the technological advancements in mould temperature controllers, such as those that offer dual-zone control. This allows for the simultaneous control of two different temperatures, providing greater flexibility and precision in the moulding process.
In the third paragraph, the emphasis is on portable vs. stationary mould temperature controllers. Portable units offer flexibility and ease of movement around the manufacturing facility, whereas stationary units are often more robust and suitable for larger-scale operations.
Maintenance tips for mould temperature controllers
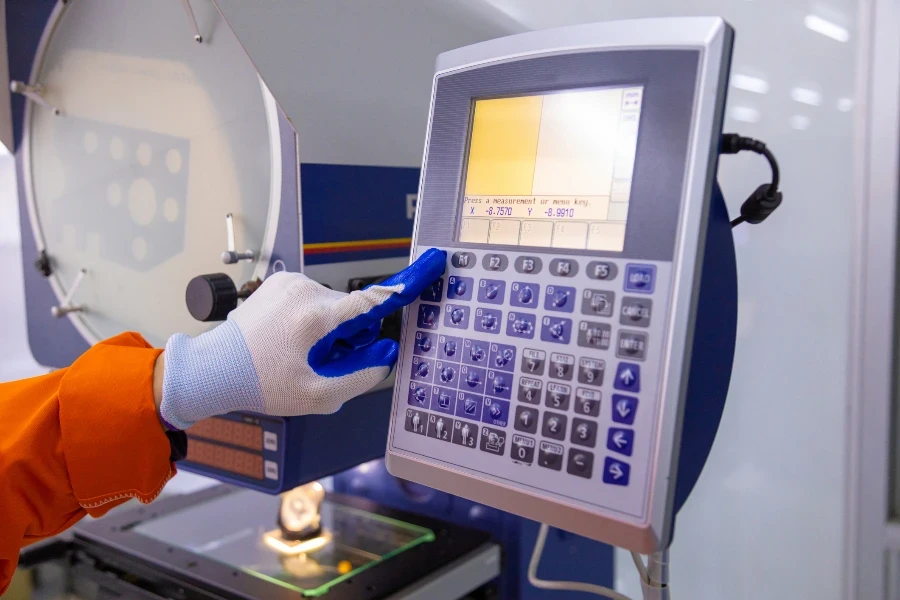
Proper maintenance is key to the longevity and efficiency of mould temperature controllers. The first paragraph provides an overview of regular maintenance tasks, such as cleaning the system, checking for leaks, and ensuring all components are functioning correctly. These tasks help prevent downtime and extend the life of the controller.
The second paragraph offers tips for troubleshooting common issues, such as temperature inaccuracies or system failures. Understanding how to quickly identify and address these problems can save valuable time and resources.
The third paragraph stresses the importance of professional maintenance and inspection. Regular check-ups by a qualified technician can help identify potential issues before they become major problems, ensuring the mould temperature controller operates at peak efficiency.
Selecting the right mould temperature controller
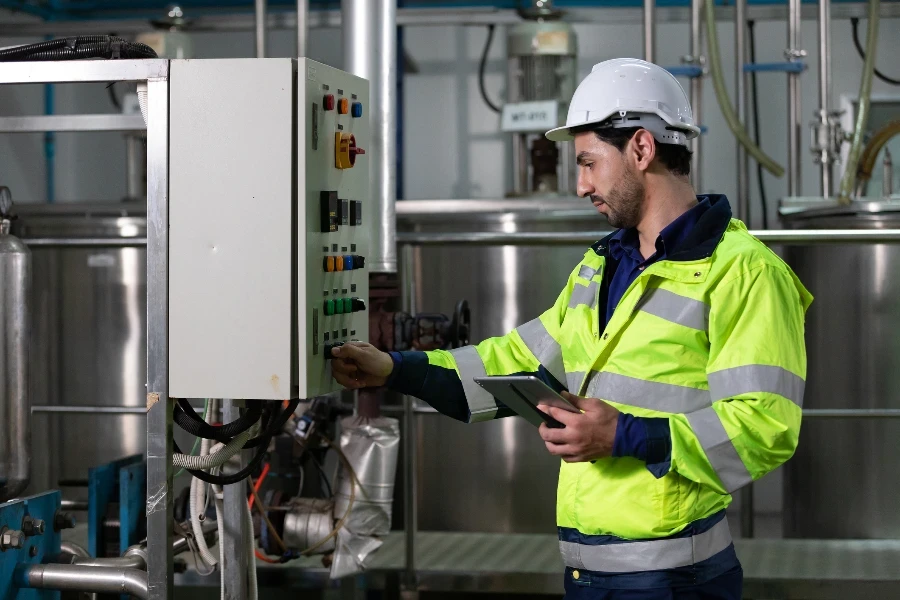
Choosing the right mould temperature controller can be a daunting task, given the variety of options available. The first paragraph outlines the key factors to consider, including the type of material being moulded, the required temperature range, and the specific features needed for your application.
The second paragraph discusses the importance of compatibility with existing machinery and systems. Ensuring the mould temperature controller can be seamlessly integrated into your current setup is crucial for maintaining efficiency and productivity.
The third paragraph encourages consultation with industry experts and manufacturers. Their insights can be invaluable in selecting a mould temperature controller that meets your needs and enhances your manufacturing process.
Conclusion:
Mould temperature controllers are indispensable in the realm of machinery, offering precision, efficiency, and quality in the moulding process. Understanding their functionality, types, and maintenance, along with selecting the right controller, can significantly impact your operations. By considering the insights shared in this article, you’re well on your way to optimizing your machinery’s performance and extending its lifespan.