In the intricate world of machinery, the significance of filters cannot be overstated. These components, often overlooked, are fundamental in ensuring the smooth operation and longevity of machinery. This article delves into the essence of filters, shedding light on their types, maintenance practices, latest innovations, and how to choose the right one for your needs. By understanding these elements, machinery operators and owners can make informed decisions, leading to optimized performance and reduced downtime.
Table of Contents:
1. The critical role of filters in machinery
2. Types of filters and their applications
3. Best practices for filter maintenance
4. Latest innovations in filter technology
5. How to choose the right filter for your machinery
The critical role of filters in machinery
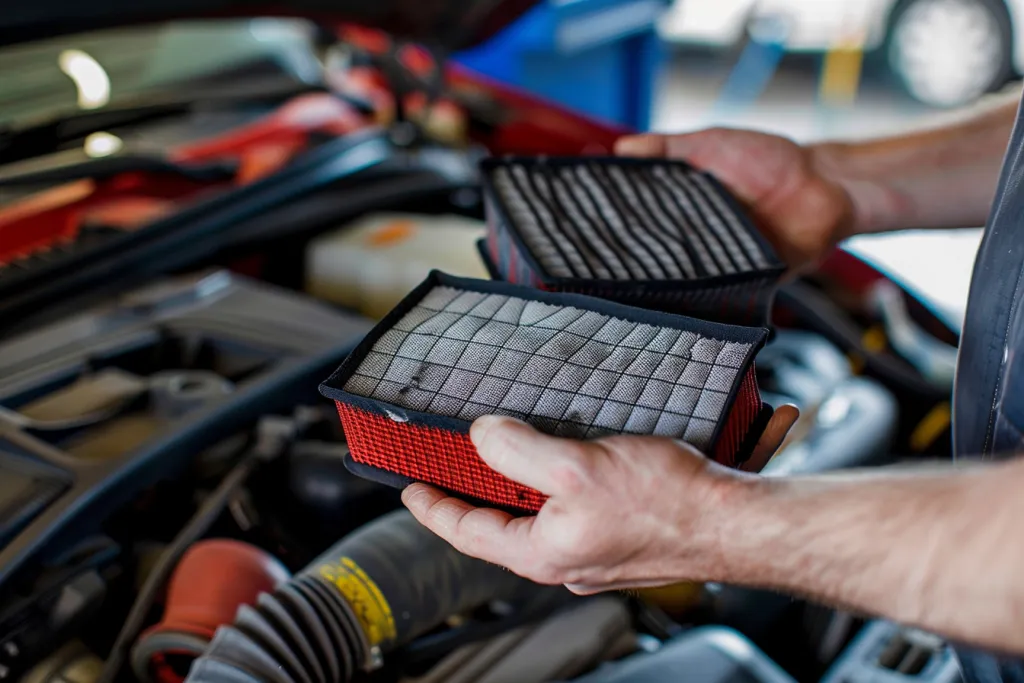
Filters serve as the guardians of machinery, protecting critical components from contamination and wear. They ensure the purity of fluids and air entering systems, which is paramount for maintaining optimal performance and preventing premature failure. Without effective filtration, contaminants can cause significant damage, leading to costly repairs and downtime.
In hydraulic systems, for instance, filters remove particulate matter and moisture, preserving the integrity of the hydraulic fluid and, consequently, the system’s performance. Similarly, in engines, air and oil filters play a crucial role in preventing contaminants from causing internal wear and tear. This protective function extends the life of machinery and ensures it operates at peak efficiency.
Moreover, the environmental impact of filters cannot be ignored. By trapping pollutants and preventing their release into the atmosphere, filters contribute to cleaner emissions, aligning with global efforts towards sustainability and environmental protection.
Types of filters and their applications
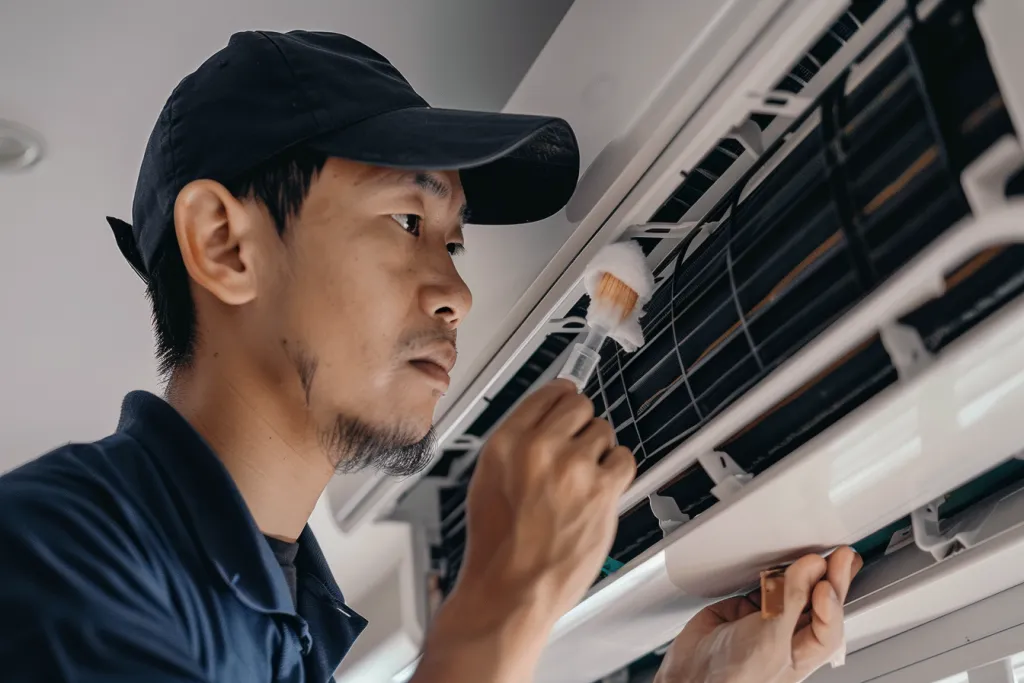
Filters come in various types, each designed for specific applications within machinery. Understanding these types allows machinery owners to ensure they are using the most appropriate filter for their equipment, enhancing protection and efficiency.
Air filters, for example, are essential in preventing particulate matter from entering engines and ventilation systems. They are critical in maintaining clean combustion processes and protecting sensitive components from dust and debris. Oil filters, on the other hand, clean the oil circulating through engines and hydraulic systems, removing contaminants that can cause wear and tear.
Fuel filters play a vital role in ensuring the purity of fuel entering combustion engines. By removing impurities, these filters prevent blockages and ensure efficient fuel combustion, contributing to optimal engine performance and fuel efficiency. Each filter type, from air to fuel and oil, is tailored to meet the specific requirements of different machinery systems, ensuring comprehensive protection across applications.
Best practices for filter maintenance
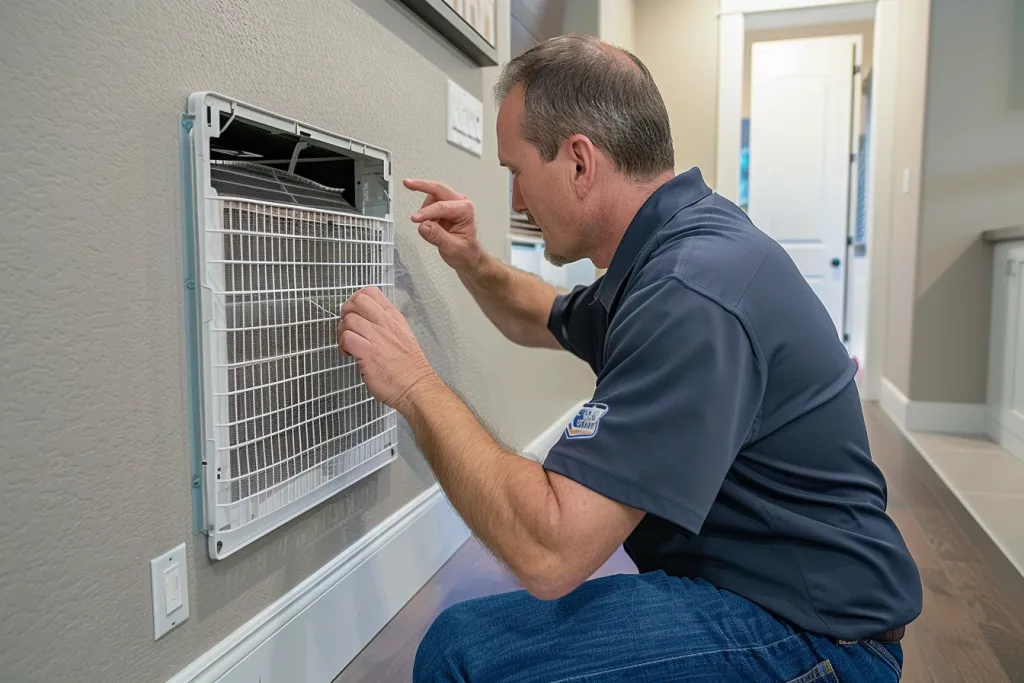
Regular maintenance of filters is essential for sustaining machinery performance and longevity. Neglecting filter maintenance can lead to increased wear, reduced efficiency, and even system failures. Therefore, adopting best practices for filter maintenance is crucial.
Firstly, it’s important to follow the manufacturer’s recommendations for filter replacement intervals. These guidelines are based on extensive testing and are designed to ensure optimal performance. Additionally, visual inspections can help identify signs of wear or clogging, prompting timely replacements.
Keeping a log of filter replacements and inspections can also aid in predicting maintenance needs, allowing for proactive rather than reactive maintenance. This approach minimizes downtime and ensures machinery operates efficiently. Furthermore, using high-quality filters and ensuring they are correctly installed is paramount. Poor-quality filters may not provide adequate protection, and incorrect installation can lead to leaks or bypasses, compromising the filtration process.
Latest innovations in filter technology
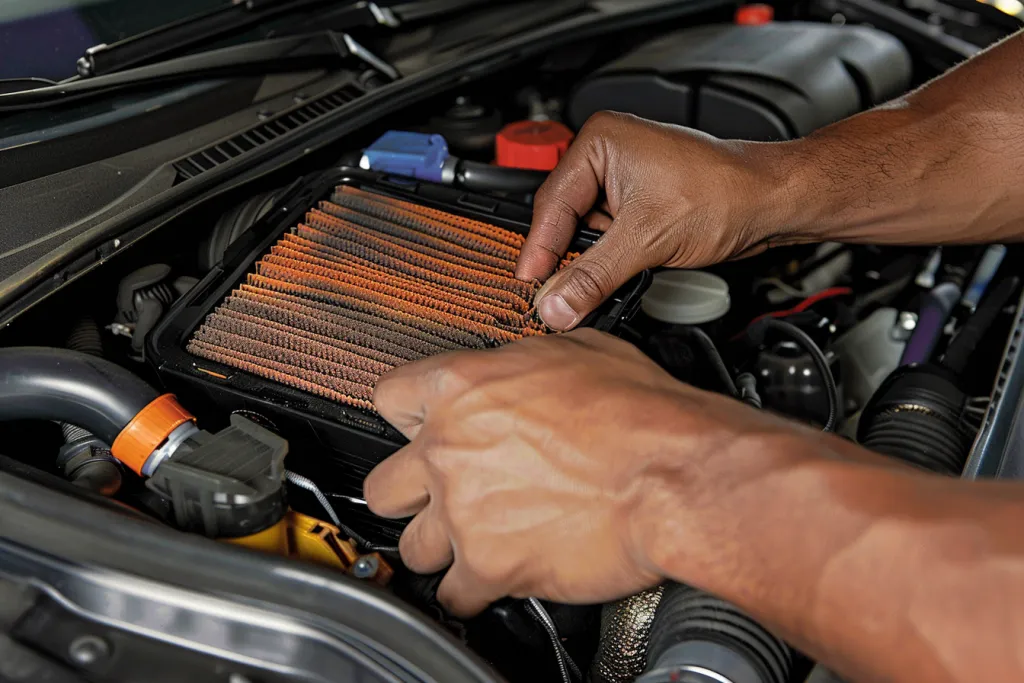
The field of filter technology is continuously evolving, with innovations aimed at enhancing efficiency, sustainability, and adaptability. These advancements promise to revolutionize how machinery is protected and maintained.
One notable innovation is the development of smart filters, equipped with sensors that monitor filter condition and contamination levels in real-time. This technology enables predictive maintenance, alerting operators before filters reach critical levels of clogging or wear. Such advancements not only extend the life of the filter but also reduce unnecessary replacements, saving costs and reducing environmental waste.
Additionally, new materials and designs are being explored to increase filter efficiency and durability. For example, nanofiber technology offers superior filtration capabilities, trapping smaller particles than traditional materials. These innovations ensure that filters can meet the demands of modern machinery, providing enhanced protection against an ever-increasing range of contaminants.
How to choose the right filter for your machinery
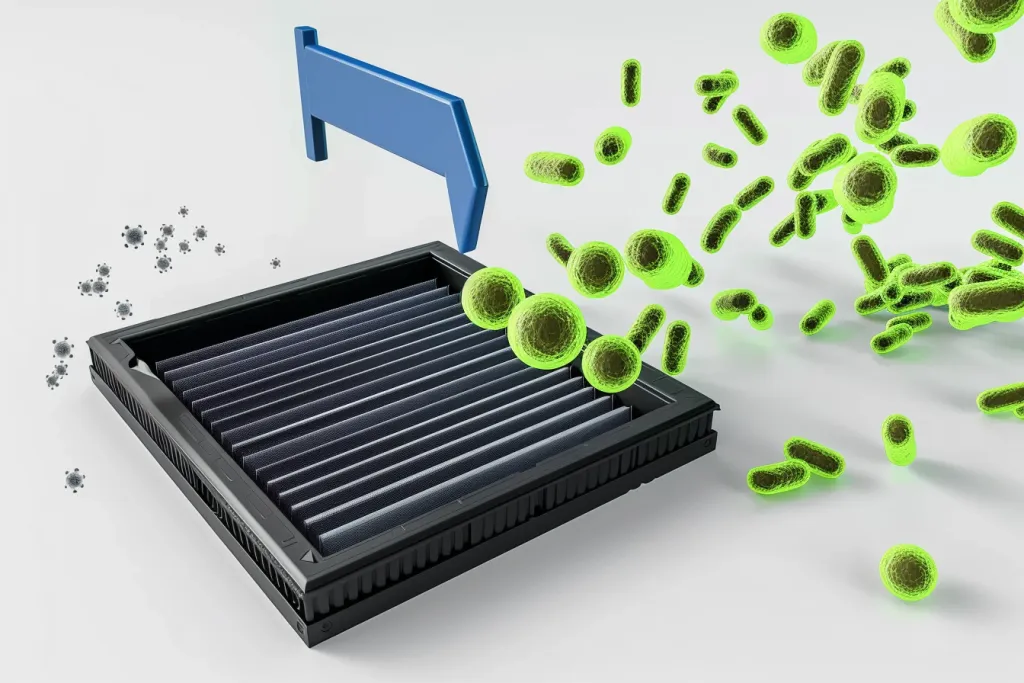
Selecting the appropriate filter for machinery is a decision that should not be taken lightly. It involves considering several factors to ensure compatibility and efficiency. Firstly, understanding the specific requirements of your machinery, including the types of contaminants it is exposed to and the filtration efficiency required, is essential.
Consulting the machinery’s manual or manufacturer for filter specifications and recommendations is a good starting point. Additionally, considering the operating environment is crucial. Machinery operating in harsh or polluted environments may require filters with higher filtration efficiency or specific designs to handle the conditions.
Lastly, evaluating the total cost of ownership, including the filter’s initial cost, replacement frequency, and potential savings in terms of reduced wear and maintenance, can guide the selection process. By carefully considering these factors, machinery owners can ensure they choose the right filter, optimizing their equipment’s performance and longevity.
Conclusion:
Filters play a pivotal role in the maintenance and performance of machinery, acting as a first line of defense against contaminants. Understanding the types of filters, adhering to maintenance best practices, keeping abreast of technological innovations, and selecting the right filter are all critical steps in ensuring machinery operates efficiently and lasts longer. By prioritizing filtration, machinery owners can protect their investments and contribute to a more sustainable, efficient future.