5-axis CNC machining represents a technical paradigm for precision manufacturing. It takes traditional machining processes to the next level by increasing design complexity and improving the efficacy of the process. The article is all about 5-axis CNC machining and its spawning consequences – some of which may surprise you.
Table of Contents:
1. Understanding 5-axis CNC machining
2. Advantages of 5-axis CNC machining
3. Applications in various industries
4. Technical specifications and capabilities
5. Choosing the right 5-axis CNC machine
Understanding 5-axis CNC machining
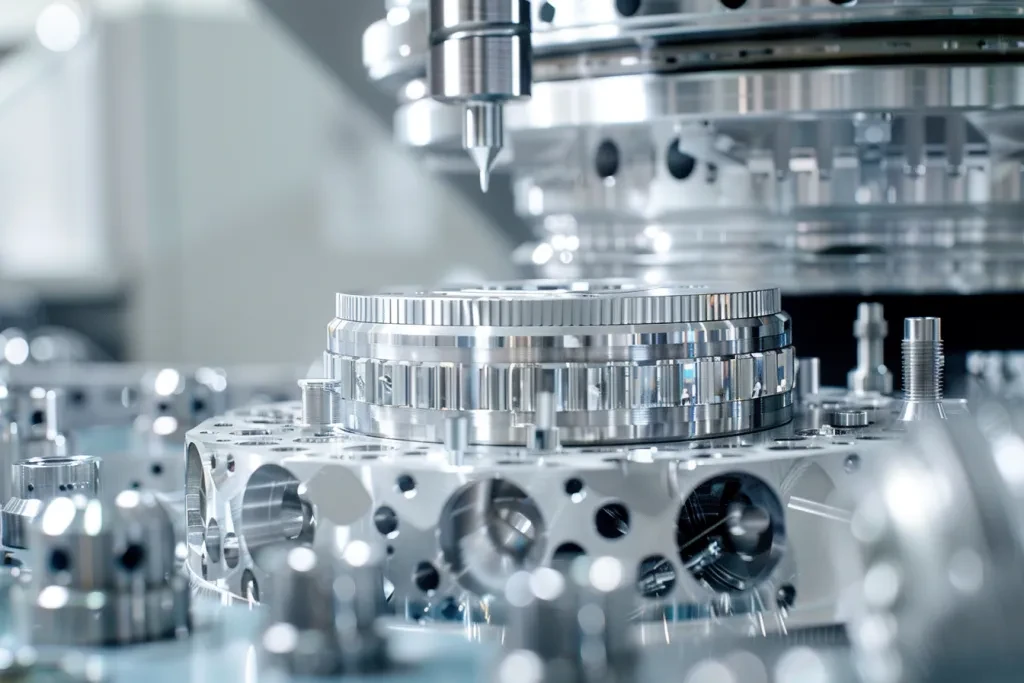
5-axis CNC machining, or five-axis machining, is the computer numerical control (CNC) of a machine tool that moves along five different axes (X, Y, Z, A and B) simultaneously. Unlike three-axis machining where the workpiece is positioned along the three axes X, Y and Z, in the case of 5-axis machines these axes are complemented by two rotational movements along the axes A and B. The tool can approach the workpiece from any direction, making it possible to produce complex shapes in a single setup.
The extra axes allow precise positioning, and reduce the need for separate setups and repositioning by hand, which is especially useful for parts and components that need fine tolerances and surface finish.
Manufacturers who want to harness the full potential of 5-axis CNC machining therefore need to understand some fundamentals such as how to optimise tool paths in the software and in the control systems, improve cutting efficiency and minimise error to be able to deliver to their customers.
Advantages of 5-axis CNC machining
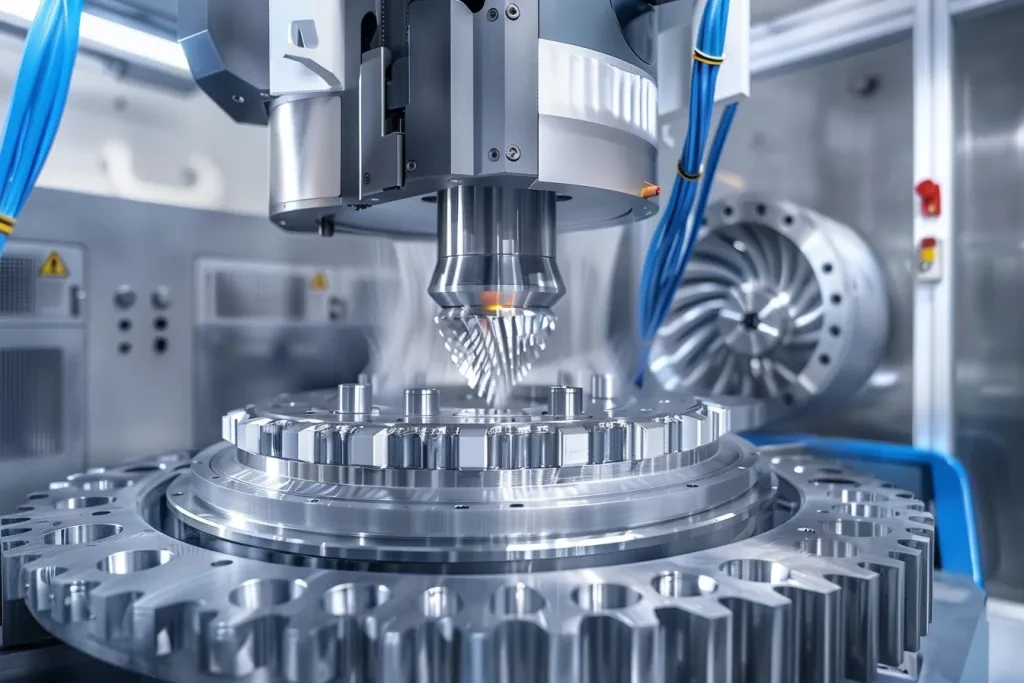
5-axis CNC machining delivers parts with complex geometries that ultimately lead to superior products, especially when precision is paramount and tolerances are tight. By moving the cutting tool along five different axes concurrently, 5-axis machining can achieve very complex detail and finishing that is simply not possible any other way. It is for this reason that the aerospace industry, the automotive industry and medical device makers – all sectors that require critical components and materials – demand the use of the 5-axis process. 5-axis machining is especially suited for parts requiring tight tolerances and exact surface finishes.
A large advantage is reduced setup time and fewer fixtures. 3-axis milling can require several setups for a single component shape, in turn requiring more time in production as well as increasing equipment and personnel costs. 5-axis machines can often perform multiple operations in single setups, increasing productivity by reducing production time.
Furthermore, 5-axis CNC machining also optimizes the tool positioning by reducing the cutting forces. This not only aids in the smooth operation of the machine, but it also extends the lifespan of the cutting tools since the forces are minimised during specific processes of the tool positioning. 5-axis CNC machining also enhances tool life and efficiency by diminishing tool overreach. Overreach occurs when the tool moves away from its precise point of contact with the workpiece, creating a greater amount of displacement than necessary. This reduces tool longevity, as more energy is used to complete the cut.
Applications in various industries
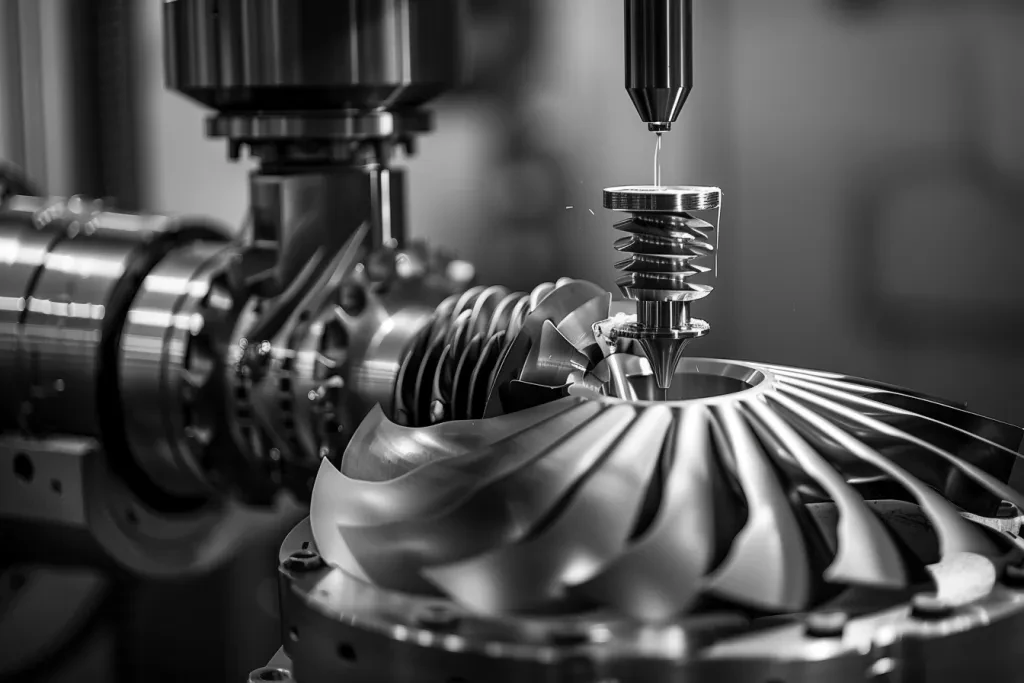
Due to its versatility, 5-axis CNC machining is used in a wide variety of industries, from aerospace where it is used to produce parts with a high safety and performance standard, such as turbine blades, aircraft structural parts and complex engine components, to other manufacturing sectors.
In the automotive industry, components such as engine blocks, gearboxes and less obvious but more intricate parts of bodywork are produced using five-axis machining processes. This allows the production of light but strong parts, which in turn improve the performance and efficiency of vehicles, as well as allow for bespoke parts in motorsports and prototyping of fresh designs.
5-axis CNC machining is also beneficial to the medical device industry. Surgical instruments, implants and prosthetics are produced using 5-axis technology. This is because the machining of such components requires high-precision and accuracy to ensure product quality and patient reliability.
Technical specifications and capabilities
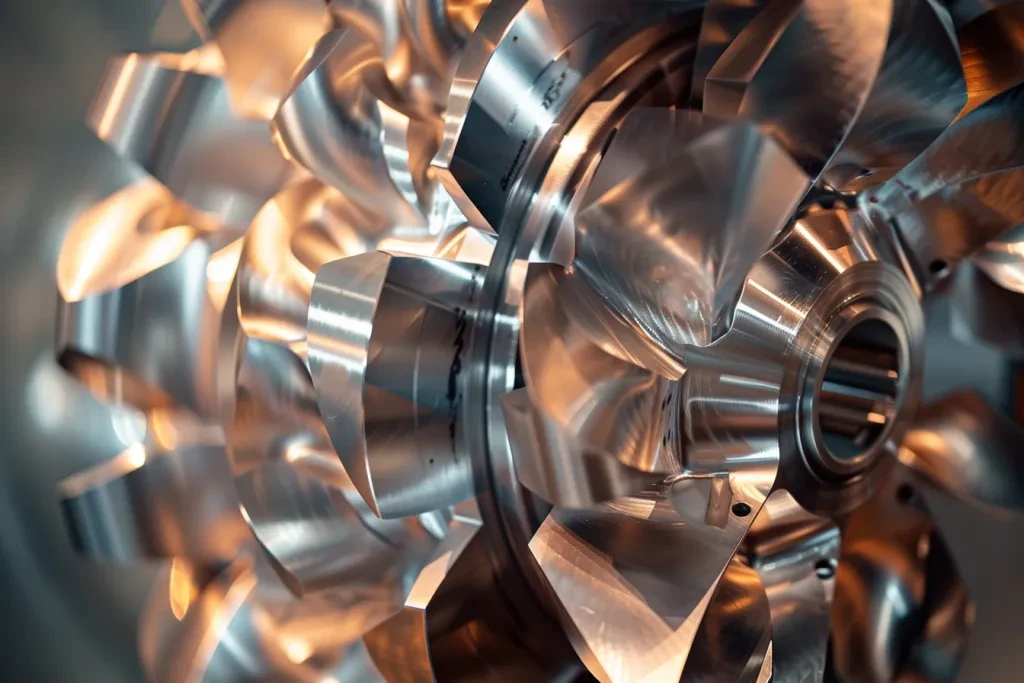
5-axis CNC machines have several different technical specifications that are important to consider for different types of manufacturing. These specifications include the size of the work envelope, the spindle speed, and the types of tool holders. The work envelope specifies the biggest size of workpiece that can be machined, while the spindle speed also influences the speed of the cutting and the surface finish.
This advanced control system (as in Figure 2 above) is vital for 5-axis machining, with advanced software used to track tool paths in real time and to correct for tool breakage or tool path errors. Other advanced features, such as collision detectors and automatic tool changers, further improve the efficiency and safety of machining 5-axis parts.
With a 5-axis CNC machine, parts can be made from a wide variety of materials: aluminium, titanium, stainless steel, plastics, composites – whatever the project calls for.
Choosing the right 5-axis CNC machine
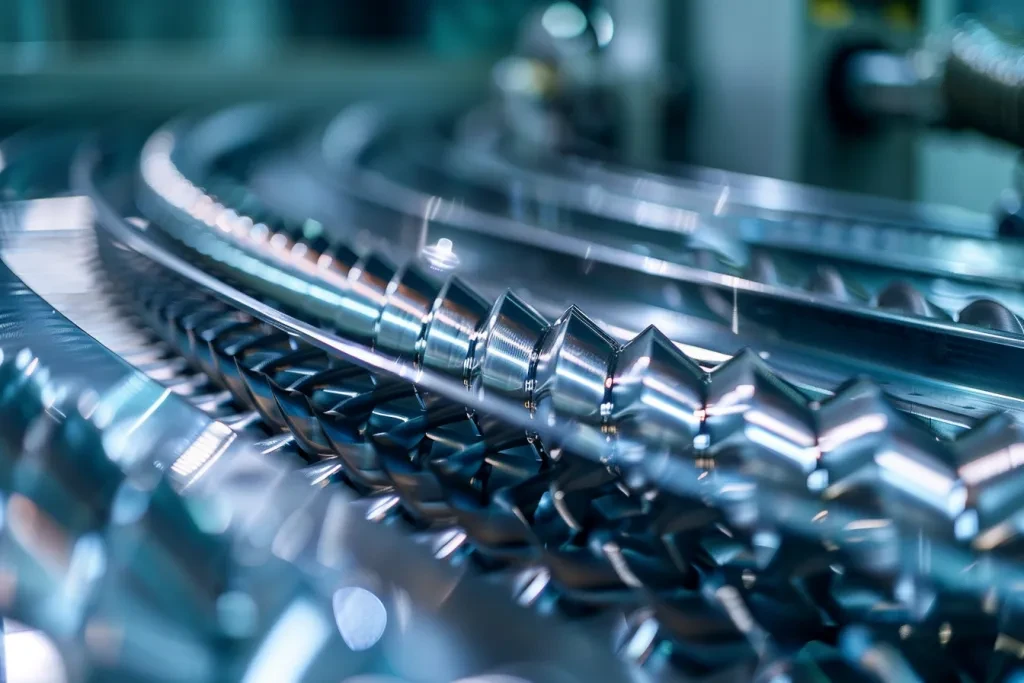
As you can imagine, there are different types of 5-axis CNC machining. The choice of the buying company partly depends on what are needed by the specific production process, but one must also give particular attention to how precise the machine will be. A manufacturing company has to evaluate the following features in order to select the right 5-axis CNC machine: axis configuration, power of the spindle and the features of the control system.
There are also issues in regard to ‘ergonomics’, which is how the machine performs out of the box interactively, including ease of software use, data and tooling compatibility, and the ability to be integrated with and controlled by other systems, especially CAD/CAM. Finally, consider the support and maintenance offered by the machine builder.
The second key factor is cost. Although 5-axis CNC machines come with a considerable capital outlay, the increased efficiency and improved product quality can help to cover the initial investment. Manufacturers would do well to calculate the return on investment by looking at factors such as reduced setup times, increased tool life and improved capacity.
Conclusion
5-axis CNC machining is a valuable manufacturing technology that allows for precision and efficiency in the production of complex parts. Knowing the benefits of the technology, the applications, the technical specifications and the factors that need to be considered when choosing it, manufacturers can leverage the technology to improve operations and meet the needs of modern industries.