Laser welding equipment represents a pinnacle of precision and efficiency in the modern manufacturing landscape. This technology, known for its ability to join materials with high accuracy and minimal distortion, has revolutionized industries. In this comprehensive guide, we’ll explore the ins and outs of laser welding equipment, covering its functionality, application, cost, and leading models available today.
Table of Contents:
– What is laser welding equipment?
– How does laser welding equipment work?
– How to use laser welding equipment
– How much does laser welding equipment cost?
– Top laser welding equipment
What is laser welding equipment?
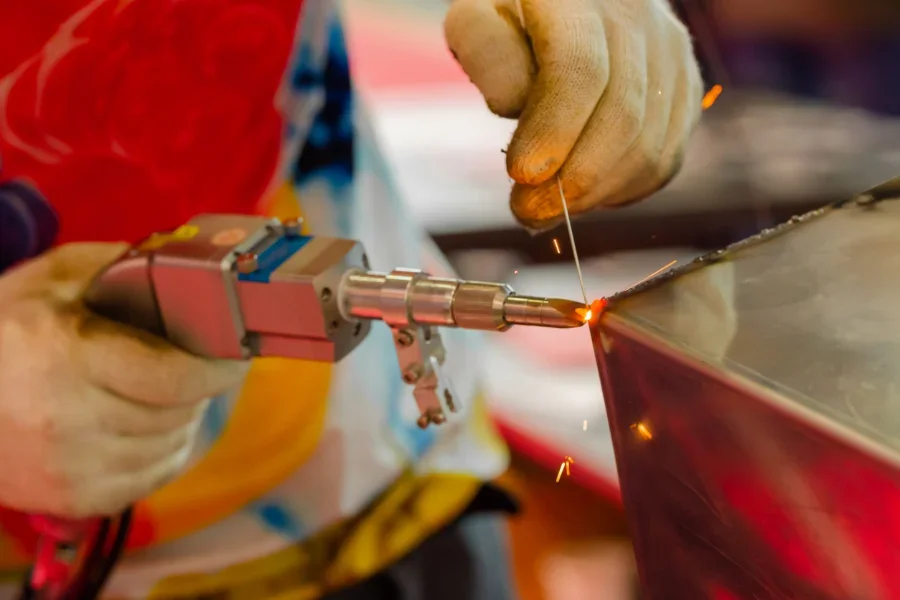
Laser welding equipment is a cutting-edge technology used in various industrial applications to join pieces of metal or thermoplastics through the use of a laser. The equipment generates a highly concentrated beam of light that delivers a focused heat source, allowing for deep weld penetration and high welding rates. This method is renowned for its precision, speed, and versatility, making it indispensable in sectors such as automotive, aerospace, and electronics manufacturing.
Unlike traditional welding techniques, laser welding offers a contactless process that minimizes mechanical stress and distortion of the workpiece. This is particularly beneficial for delicate or complex assemblies. Moreover, the equipment can be easily automated and integrated into existing manufacturing lines, enhancing productivity and ensuring consistent quality.
The core components of laser welding equipment include a laser source, a beam delivery system, focusing optics, and a control system. These elements work in harmony to produce welds that are not only aesthetically pleasing but also structurally sound, with minimal heat-affected zones (HAZ).
How does laser welding equipment work?
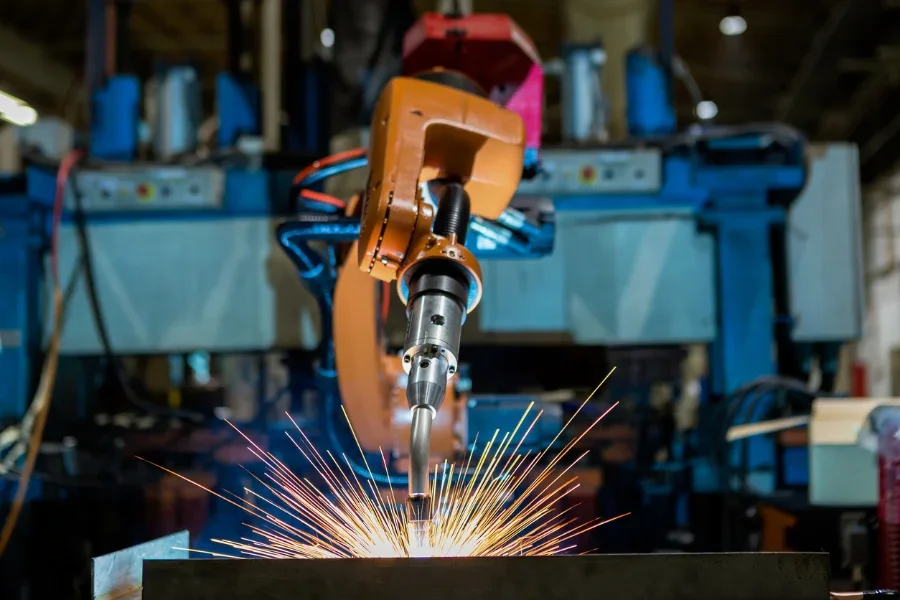
Laser welding equipment operates by emitting a laser beam that is focused onto a small area of the material to be joined. This concentrated energy is absorbed by the material, causing it to melt and form a weld pool. As the laser beam moves along the joint line, the molten material cools and solidifies, creating a strong, durable weld.
The process begins with the generation of the laser beam, typically produced by either a solid-state laser (such as a neodymium-doped yttrium aluminum garnet, Nd:YAG) or a gas laser (such as a CO2 laser). The choice of laser type depends on the specific application and material characteristics.
Beam delivery is a critical aspect of laser welding equipment. The laser beam must be precisely focused and directed to the welding site. This is achieved through a series of mirrors or fiber optics that guide the beam from the laser source to the workpiece. Additionally, focusing optics are used to concentrate the laser beam to a fine point, enabling high power density and efficient energy transfer.
Control systems play a vital role in the operation of laser welding equipment. They regulate the laser’s power, duration, and spot size, as well as the movement of the laser head or workpiece. Advanced control systems can adjust parameters in real-time, optimizing the welding process for different materials and thicknesses.
How to use laser welding equipment
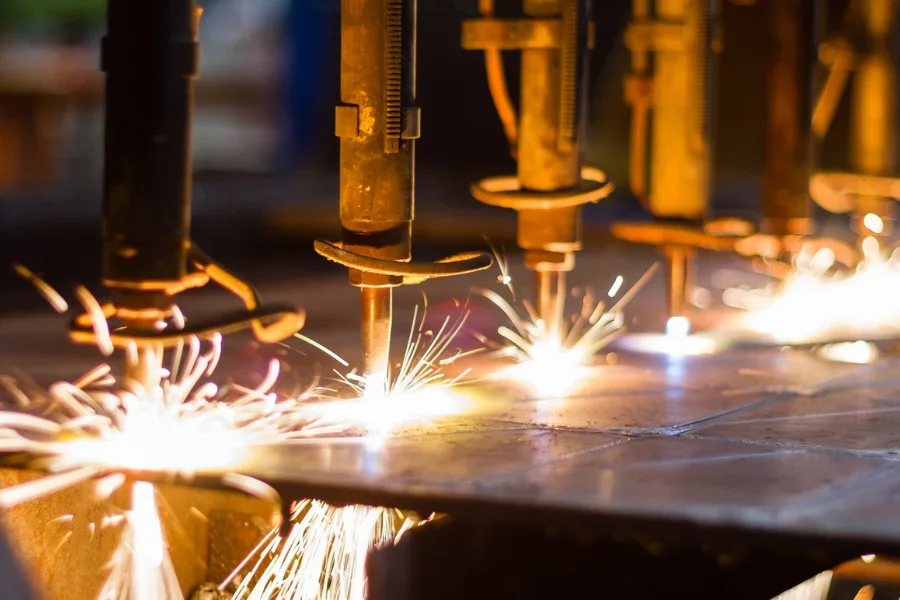
Using laser welding equipment effectively requires understanding its capabilities and limitations. The first step is to select the appropriate laser type and settings for the specific material and application. This involves considering factors such as material thickness, joint configuration, and desired weld characteristics.
Preparation of the workpieces is crucial for achieving high-quality welds. Surfaces should be clean and free of contaminants to ensure proper fusion. Additionally, proper fixture and alignment of the parts to be welded are essential to maintain joint integrity and prevent misalignment.
The actual welding process involves setting up the equipment according to the manufacturer’s instructions, including adjusting the laser power, speed, and focus. Operators must wear appropriate safety gear to protect against laser radiation and fumes. Monitoring the welding process is important to detect any issues early and make necessary adjustments.
How much does laser welding equipment cost?
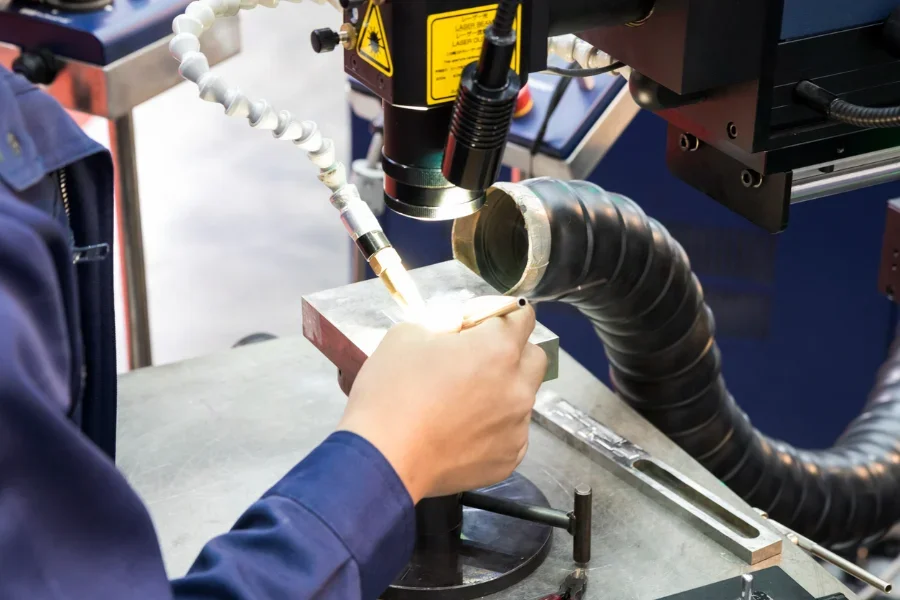
The cost of laser welding equipment can vary widely depending on the type, power, and features. Entry-level systems may start at around $10,000, while high-end models equipped with advanced capabilities can exceed $100,000. Factors that influence the price include the laser source, control system sophistication, and additional functionalities such as automation or custom tooling.
When considering the purchase of laser welding equipment, it’s important to evaluate the total cost of ownership, which includes not only the initial investment but also ongoing expenses such as maintenance, consumables, and training. Investing in a high-quality system from a reputable manufacturer can lead to lower long-term costs due to higher efficiency, reliability, and durability.
Financing options and leasing arrangements may be available to help mitigate the upfront cost of acquiring laser welding equipment. Additionally, some suppliers offer refurbished or used equipment at a reduced price, providing a cost-effective alternative for smaller operations or those with limited budgets.
Top laser welding equipment
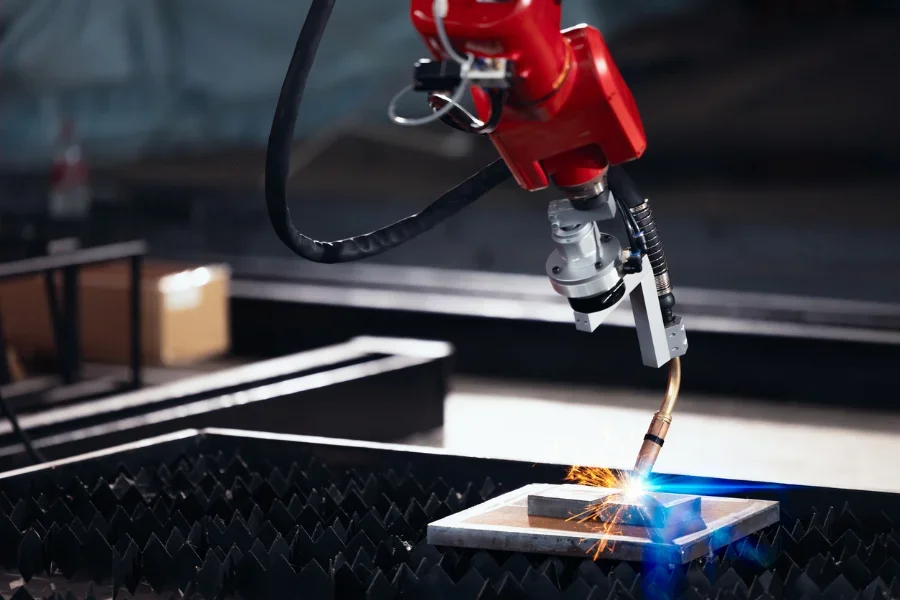
When it comes to selecting the best laser welding equipment, several brands and models stand out for their performance, reliability, and user satisfaction. Among the top contenders are:
- Trumpf TruLaser Weld Series – Known for its versatility and high-quality welds, Trumpf’s laser welding systems are suitable for a wide range of applications, from delicate medical devices to robust automotive components.
- IPG Photonics’ YLS Series – IPG offers fiber laser welding systems that are highly efficient and capable of handling complex welding tasks with precision. Their equipment is renowned for low maintenance requirements and long service life.
- Amada Miyachi LW Series – Amada Miyachi specializes in laser welding equipment designed for precision applications. Their systems are favored for electronic component manufacturing and other industries requiring intricate welds.
Selecting the right laser welding equipment involves careful consideration of your specific needs, including material types, production volume, and quality requirements. Consulting with manufacturers or distributors can provide valuable insights and help identify the most suitable system for your operations.
Conclusion: Laser welding equipment is a transformative technology that offers unparalleled precision, efficiency, and versatility in joining materials. Understanding how it works, how to use it effectively, and the costs involved are crucial steps in leveraging this technology to its full potential. With a range of options available, selecting the right equipment can elevate your manufacturing capabilities and ensure high-quality outcomes in your projects.