In 2025, the market for line boring equipment is booming, with new innovations and increasing demands in precision machining. This article provides a comprehensive analysis of the market, covering essential factors for selecting the best line boring equipment. Professional buyers will find valuable insights and guidance to make informed purchasing decisions.
Table of Contents:
1. Market Overview of Line Boring Equipment
2. Detailed Introduction and Analysis of the Line Boring Equipment Market
3. Key Factors When Selecting Line Boring Equipment
4. Innovations in Line Boring Equipment
5. Cost Considerations and Budgeting
6. Regulatory Compliance and Standards
7. Durability and Maintenance
8. Future Trends in Line Boring Equipment
9. Conclusion
Market Overview of Line Boring Equipment
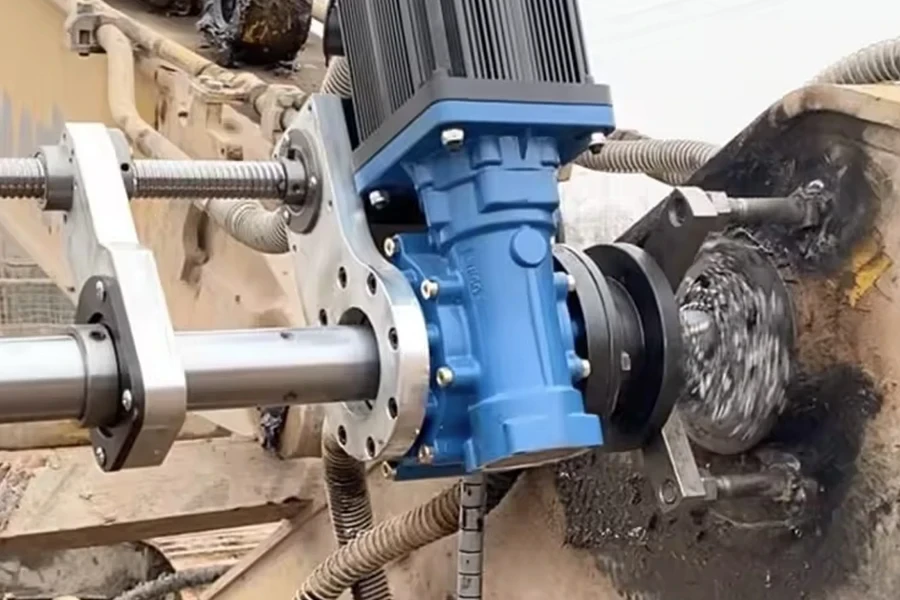
The global market for line boring equipment has been experiencing steady growth, driven by the increasing demand for precision machining in various industries. As of the end of 2024, the market size for line boring equipment was estimated at USD 1.3 billion. Projections indicate that the market will reach USD 1.8 billion by 2030, growing at a compound annual growth rate (CAGR) of 5.7%. The demand for line boring equipment is primarily fueled by the automotive, aerospace, and heavy machinery sectors, where high precision and accuracy are critical.
In terms of regional distribution, North America holds a significant share of the market, accounting for approximately 35% of the total revenue. The Asia-Pacific region is also a major player, with China and India leading the growth due to their expanding manufacturing capabilities and increasing investments in infrastructure. Europe follows closely, driven by advancements in automotive technology and the presence of key industry players. The market is highly competitive, with major players such as Advanced Carbide Tool Company, BIG KAISER Precision Tooling, and Sandvik AB dominating the landscape.
The line boring equipment market is segmented based on type, application, and end-user industry. Fine boring and rough boring are the primary types, with fine boring holding a larger market share due to its application in high-precision tasks. Key applications include automotive, general machinery, and precision engineering. The automotive sector is expected to continue leading the market, driven by the need for high-precision components in modern vehicles.
Detailed Introduction and Analysis of the Line Boring Equipment Market
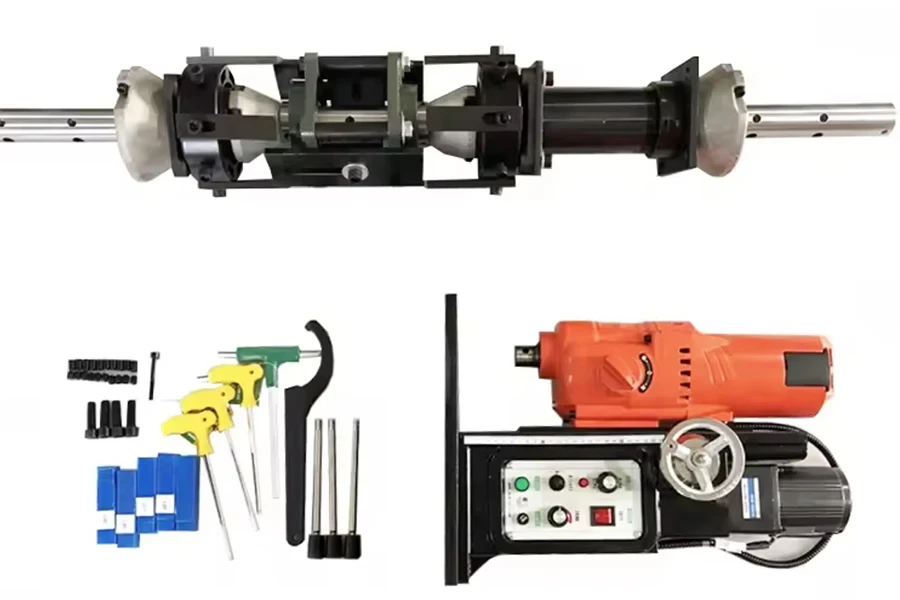
Line boring equipment is essential for the maintenance and repair of heavy machinery and large engines, ensuring the alignment and functionality of cylindrical bores. These tools are crucial in industries where precision and accuracy are paramount, such as automotive, aerospace, and heavy machinery manufacturing. The equipment is designed to perform operations such as enlarging and finishing pre-drilled or cast holes, ensuring that the diameter, surface finish, and tolerance meet exact specifications.
Key performance benchmarks for line boring equipment include precision, durability, and adaptability to various materials. Modern line boring machines are equipped with advanced features such as digital readouts, automated feeds, and real-time monitoring systems. These innovations enhance the accuracy and efficiency of boring operations, reducing downtime and improving overall productivity. The integration of computer numerical control (CNC) technology has further revolutionized the industry, allowing for more complex and precise machining tasks.
Market share dynamics reveal that established players like Advanced Carbide Tool Company and BIG KAISER Precision Tooling maintain a strong presence due to their extensive product portfolios and continuous innovation. Economic influences such as the increasing demand for electric vehicles and the growth of the aerospace sector are driving the need for more precise and durable line boring equipment. Consumer behavior is shifting towards automated and digitally controlled machinery, reflecting the broader trend of Industry 4.0 and smart manufacturing practices.
Distribution channel preferences are also evolving, with a growing emphasis on online sales and direct-to-consumer models. This shift is driven by the need for faster and more efficient procurement processes, as well as the increasing availability of detailed product information and customer reviews online. Recent innovations in the field include the development of high-speed boring machines and the use of advanced materials such as polycrystalline diamond (PCD) and cubic boron nitride (CBN) for cutting edges, offering superior wear resistance and longer tool life.
In terms of product lifecycle stages, line boring equipment is in the growth phase, with continuous advancements and increasing adoption across various industries. Digitalization is playing a significant role, with the integration of sensor technology enabling predictive maintenance and real-time performance monitoring. Social trends such as the focus on sustainability and reducing carbon footprints are also influencing the market, with manufacturers exploring eco-friendly materials and energy-efficient designs.
Customer pain points include the high initial cost of advanced line boring equipment and the need for skilled operators to handle complex machinery. To address these challenges, companies are investing in training programs and offering financing options to make their products more accessible. Brand positioning strategies focus on reliability, precision, and innovation, with differentiation strategies highlighting unique features such as advanced coatings and automated systems.
Niche markets within the line boring equipment industry include the medical device manufacturing sector, where precision and small-scale operations are critical. The growing demand for customized solutions and the ability to handle a wide range of materials are key factors driving the adoption of line boring equipment in these specialized applications.
Key Factors When Selecting Line Boring Equipment
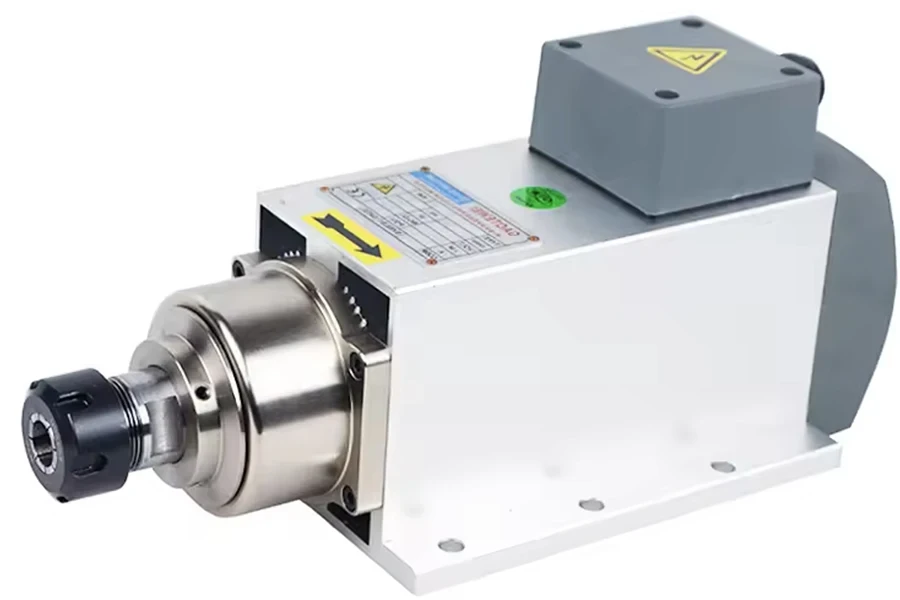
When choosing line boring equipment, several critical factors must be taken into account. These factors ensure that the selected equipment meets the specific needs of the operation and delivers optimal performance and efficiency.
Type of Line Boring Machine
Line boring machines come in various types, each suited for different applications. The two primary types are portable line boring machines and stationary line boring machines. Portable machines are ideal for field operations and repair work, as they can be easily transported to the job site. They are typically lightweight and designed for easy setup. Stationary line boring machines, on the other hand, are used in a controlled environment, such as a workshop, where precision and stability are paramount. These machines are often more robust and capable of handling larger and more complex projects.
Portable line boring machines are essential for industries such as construction and mining, where equipment downtime can be costly. These machines can be quickly set up on-site to repair worn-out bores without the need to disassemble large machinery. Stationary machines, however, are preferred in manufacturing settings where high precision and repeatability are required. They are equipped with advanced features such as CNC controls, which allow for automated and highly accurate boring operations.
Another consideration is the range of the machine. Some machines are designed to handle small to medium-sized bores, while others are capable of boring large diameters. It’s crucial to select a machine that can accommodate the size of the bores typically encountered in your operations.
Performance and Functionality
The performance of line boring equipment is a critical factor. Key performance indicators include the machine’s boring speed, accuracy, and the quality of the finished bore. High-performance machines are equipped with powerful motors and precision controls that ensure consistent and accurate boring operations.
Accuracy is particularly important in applications where tight tolerances are required. High-precision line boring machines can achieve tolerances of up to +/- 0.0001 inches, making them suitable for critical applications such as aerospace and automotive manufacturing. The quality of the finished bore is also influenced by the machine’s rigidity and stability. Machines with robust construction and high-quality components are less prone to vibrations, which can negatively impact the bore’s surface finish.
Functionality refers to the machine’s ability to perform various tasks beyond boring. Some advanced line boring machines come with additional features such as facing heads, which allow for the machining of flange faces and other surfaces. This versatility can be a significant advantage in reducing the need for multiple machines and setups, thereby increasing efficiency.
Technical Specifications
Understanding the technical specifications of line boring equipment is essential for making an informed decision. Key specifications to consider include the machine’s power requirements, spindle speed, feed rate, and travel length. The power requirements will determine the machine’s ability to handle different materials and bore sizes. Machines with higher power ratings can bore through harder materials and larger diameters more efficiently.
Spindle speed and feed rate are critical factors that influence the boring process’s efficiency and quality. Adjustable spindle speeds allow the operator to optimize the cutting conditions for different materials, while variable feed rates ensure a smooth and consistent bore. The travel length of the machine determines the maximum bore length that can be achieved in a single setup. It’s important to select a machine with a travel length that matches the typical bore lengths encountered in your operations.
Another important specification is the machine’s portability and ease of setup. Portable line boring machines should be lightweight and designed for quick and easy setup, while stationary machines should have features that facilitate precise alignment and stability.
Compatibility with Other Devices and Systems
Compatibility with other devices and systems is an important consideration, especially in automated and integrated manufacturing environments. Modern line boring machines are often equipped with CNC controls that allow for seamless integration with other machinery and production systems. This compatibility enables automated and synchronized operations, reducing the need for manual intervention and increasing overall efficiency.
It’s also important to consider the availability of compatible tooling and accessories. High-quality tooling is essential for achieving precise and consistent boring results. Some line boring machines come with a range of standard and optional tooling, allowing for customization based on specific requirements. Additionally, the availability of compatible accessories such as facing heads, support bearings, and boring bars can enhance the machine’s versatility and functionality.
In industries where traceability and documentation are important, compatibility with digital measurement and inspection systems is crucial. Some advanced line boring machines come with integrated measurement systems that allow for real-time monitoring and recording of bore dimensions. This data can be used for quality control and documentation purposes, ensuring compliance with industry standards and customer requirements.
Safety Standards and Certifications
Safety is a paramount consideration when selecting line boring equipment. Machines must comply with relevant safety standards and regulations to ensure the safety of operators and other personnel. Key safety features to look for include emergency stop buttons, safety guards, and automatic shut-off mechanisms. These features help prevent accidents and injuries by providing quick and effective responses to potential hazards.
Certifications from recognized organizations such as OSHA (Occupational Safety and Health Administration) and CE (Conformité Européene) indicate that the machine meets stringent safety and quality standards. It’s important to verify that the machine has the necessary certifications and complies with industry-specific safety regulations.
In addition to safety features and certifications, proper training and documentation are essential for safe operation. Manufacturers should provide comprehensive training programs and detailed user manuals to ensure that operators are fully knowledgeable about the machine’s operation and safety procedures. Regular maintenance and inspection are also important to keep the machine in safe working condition.
Innovations in Line Boring Equipment
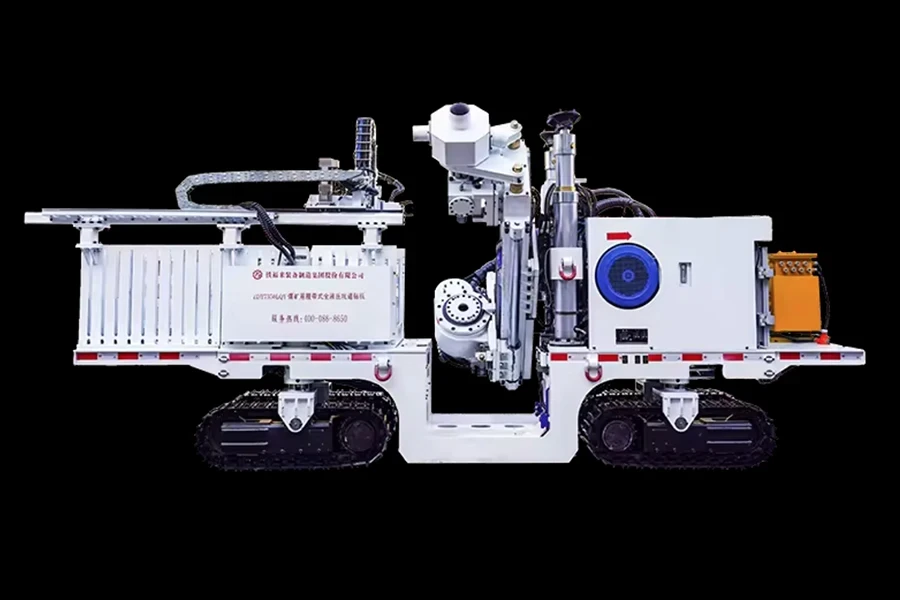
The line boring equipment industry has seen significant advancements in recent years, driven by the need for increased efficiency, precision, and automation. One of the most notable innovations is the integration of CNC (Computer Numerical Control) technology. CNC line boring machines offer unparalleled precision and repeatability, making them ideal for applications that require tight tolerances. These machines can be programmed to perform complex boring operations with minimal manual intervention, reducing the risk of human error and increasing productivity.
Another innovation is the development of portable line boring machines with advanced features such as digital readouts and wireless connectivity. These features allow operators to monitor and control the boring process remotely, enhancing convenience and efficiency. Digital readouts provide real-time feedback on bore dimensions, allowing for immediate adjustments and ensuring consistent quality. Wireless connectivity enables remote diagnostics and troubleshooting, reducing downtime and maintenance costs.
The use of advanced materials and coatings in tooling has also improved the performance and durability of line boring equipment. High-performance materials such as carbide and ceramic offer superior wear resistance and cutting efficiency, extending tool life and reducing the need for frequent replacements. Coatings such as titanium nitride (TiN) and diamond-like carbon (DLC) further enhance the hardness and lubricity of cutting tools, improving their performance in demanding applications.
Cost Considerations and Budgeting
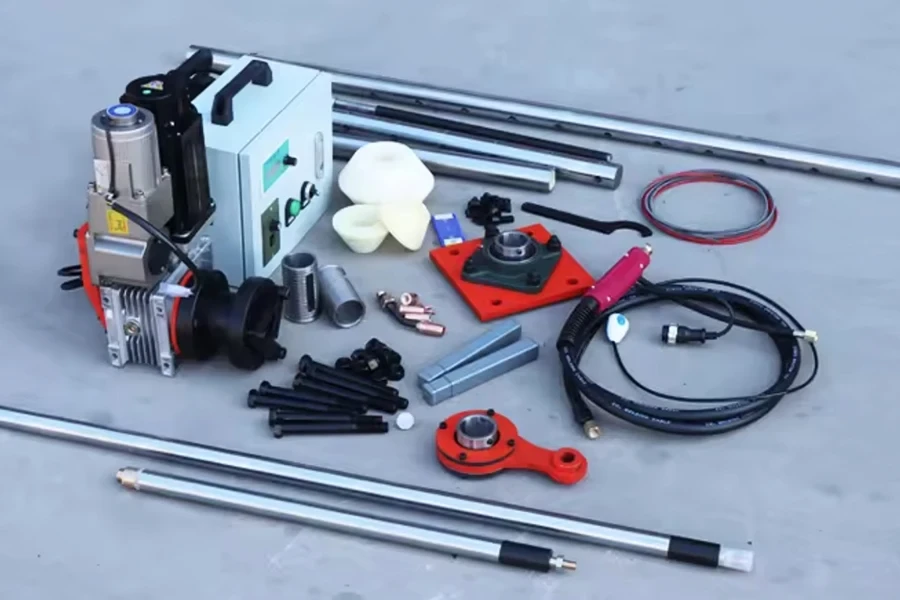
When selecting line boring equipment, cost considerations and budgeting play a crucial role. The initial purchase price of the machine is a significant factor, but it’s important to consider the total cost of ownership. This includes operating costs, maintenance expenses, and the cost of consumables such as cutting tools and lubricants. High-quality machines with advanced features may have a higher upfront cost, but they can offer long-term savings through increased efficiency and reduced downtime.
It’s also important to consider the potential return on investment (ROI) when budgeting for line boring equipment. Machines that offer higher precision and efficiency can improve the quality of the finished product and reduce rework and scrap rates. This can lead to significant cost savings and increased profitability over time. Additionally, machines with versatile features and capabilities can reduce the need for multiple machines and setups, further enhancing ROI.
Financing options and leasing programs are available from many manufacturers and suppliers, making it easier to manage the cost of acquiring line boring equipment. These options can provide flexibility and help spread the cost over time, making it more manageable for businesses with limited budgets.
Regulatory Compliance and Standards
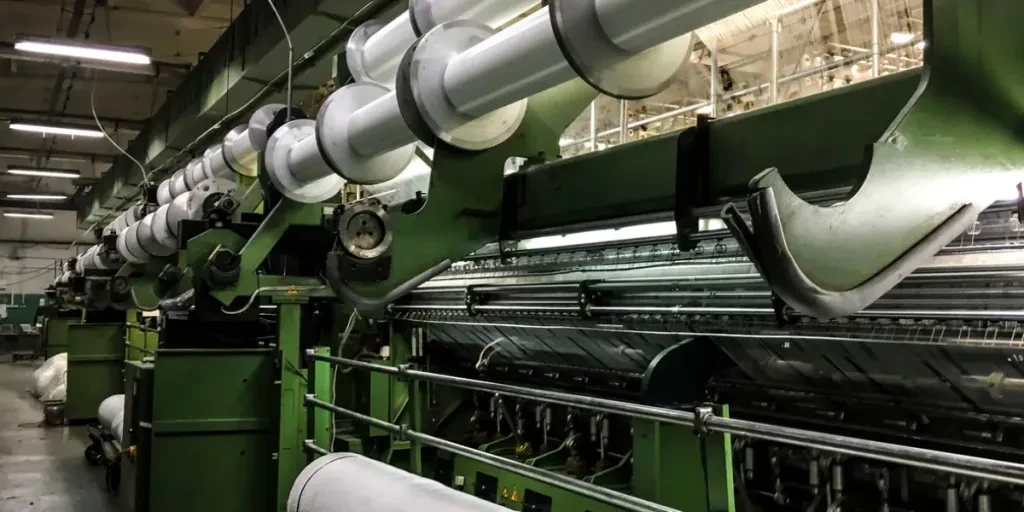
Compliance with regulatory standards and industry-specific requirements is essential when selecting line boring equipment. Machines must adhere to relevant regulations and standards to ensure safety, quality, and performance. Key standards to consider include ISO (International Organization for Standardization) standards, ASME (American Society of Mechanical Engineers) standards, and industry-specific certifications.
ISO standards, such as ISO 9001, provide guidelines for quality management systems and help ensure that the machine meets consistent quality and performance criteria. ASME standards, such as ASME B5.54, provide guidelines for the design and manufacturing of machine tools, ensuring that the machine meets specific safety and performance requirements. Industry-specific certifications, such as those required for aerospace or automotive applications, provide additional assurance that the machine meets the stringent requirements of these industries.
Manufacturers should provide documentation and certification to verify that the machine complies with relevant standards and regulations. It’s important to thoroughly review this documentation and ensure that the machine meets all necessary requirements before making a purchase.
Durability and Maintenance
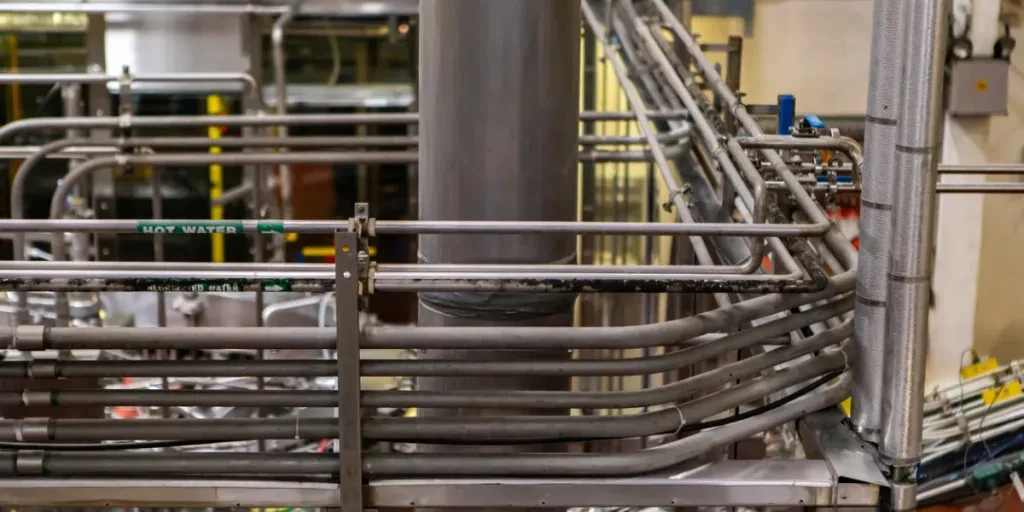
The durability and maintenance requirements of line boring equipment are critical factors to consider. Machines with robust construction and high-quality components are more likely to withstand the rigors of demanding applications and provide long-term reliability. It’s important to select a machine that is built to last and can handle the specific requirements of your operations.
Regular maintenance is essential to keep the machine in optimal working condition and prevent unexpected breakdowns. Manufacturers should provide detailed maintenance schedules and guidelines, as well as training programs for operators and maintenance personnel. It’s also important to consider the availability of spare parts and technical support. Machines from reputable manufacturers with a strong support network are more likely to have readily available spare parts and responsive technical support, reducing downtime and maintenance costs.
Preventive maintenance programs can help identify potential issues before they become major problems, further enhancing the machine’s durability and reliability. Regular inspections, lubrication, and calibration are key components of a preventive maintenance program and can extend the machine’s lifespan and improve its performance.
Future Trends in Line Boring Equipment
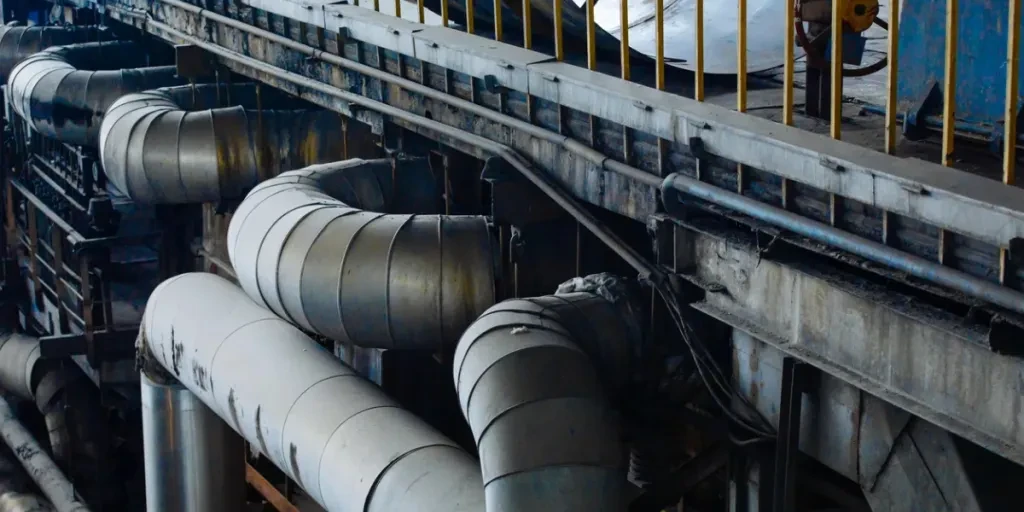
The future of line boring equipment is likely to be shaped by advancements in technology and increasing demands for efficiency and precision. One of the key trends is the continued integration of automation and digital technologies. Smart line boring machines equipped with sensors and IoT (Internet of Things) connectivity can provide real-time data on machine performance and condition. This data can be used for predictive maintenance, optimizing machine settings, and improving overall efficiency.
Another trend is the development of more advanced and durable materials for cutting tools and machine components. Innovations in materials science are likely to lead to the creation of cutting tools with even higher wear resistance and cutting efficiency, reducing the need for frequent replacements and improving overall productivity.
Sustainability is also becoming an important consideration in the manufacturing industry. Line boring equipment that is designed with energy efficiency and environmental impact in mind is likely to become more prevalent. Machines that use less energy and produce less waste can help businesses reduce their environmental footprint and comply with increasingly stringent environmental regulations.
Conclusion
In summary, selecting the right line boring equipment requires careful consideration of various factors, including the type of machine, performance and functionality, technical specifications, compatibility, safety standards, cost, regulatory compliance, durability, and future trends. By thoroughly evaluating these factors and staying informed about the latest advancements in technology, businesses can make informed decisions and select equipment that meets their specific needs and delivers long-term value.