A recent surge in demand for extruded products across industries has highlighted the importance of selecting the right extrusion machine. This article delves into an in-depth analysis of key factors, market trends, and advanced features, providing valuable guidance for professional buyers to make informed decisions and enhance their production capabilities.
Table of Contents:
-Extrusion Machine Market Overview
-In-depth Market Analysis of Extrusion Machines
-Key Factors When Selecting an Extrusion Machine
-Advanced Features of Modern Extrusion Machines
-Safety and Compliance Standards
-Cost Considerations and ROI
-Quality and Performance Metrics
-Packaging and Shipping Considerations
-Final Thoughts
Extrusion Machine Market Overview
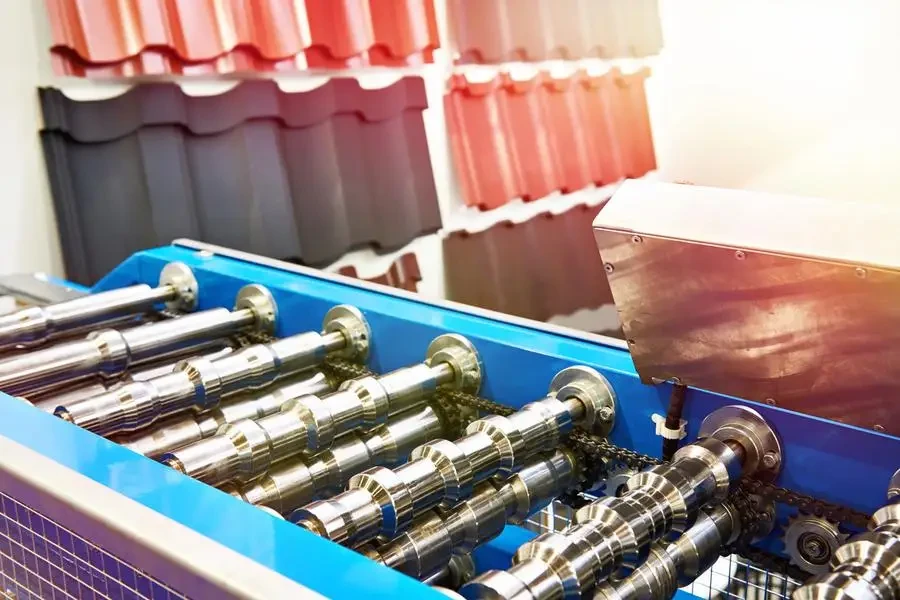
The global extrusion machinery market is experiencing significant growth, expanding from USD 8.26 billion in 2023 to USD 8.63 billion in 2024. Projections indicate that the market will continue to grow at a compound annual growth rate (CAGR) of 4.76%, reaching USD 11.45 billion by 2030. This growth is driven by increasing demand for extruded products across industries such as automotive, construction, and packaging. The extrusion process, which transforms raw materials into finished or intermediate forms through high pressure and controlled temperatures, is integral in manufacturing products with consistent cross-sectional profiles like pipes, tubing, and window frames.
In-depth Market Analysis of Extrusion Machines
Key Performance Benchmarks
Extrusion machines are evaluated on several performance benchmarks, including output rate, energy efficiency, and precision in maintaining product dimensions. Twin-screw extruders are increasingly adopted due to their greater process flexibility and higher output rates compared to single-screw extruders. These machines are particularly favored in industries requiring complex material formulations and high throughput.
Market Share Dynamics
The extrusion machinery market shows significant regional variations. The Americas, particularly the United States, dominate due to robust manufacturing infrastructure and technological advancements. Meanwhile, the Asia Pacific region, led by China and India, is experiencing rapid industrial growth and increasing investments in extrusion technology. Europe remains a key player with a strong emphasis on sustainability and recycling, driving demand for advanced extrusion machinery.
Economic Influences and Consumer Behavior Shifts
The expansion of the construction and automotive sectors has significantly increased the demand for extruded products. The growing emphasis on lightweight and high-performance materials in these industries is a major driver. Additionally, consumer preferences are shifting towards sustainable and recyclable products, encouraging the adoption of advanced extrusion machinery that supports eco-friendly manufacturing practices.
Technological Innovations
Technological advancements are pivotal in the evolution of the extrusion machinery market. The integration of Internet of Things (IoT) technologies for predictive maintenance and operational efficiency is becoming increasingly prevalent. Innovations such as advanced extruder software modules and precision-driven machinery are enhancing the capabilities of extrusion processes, allowing for higher precision and efficiency.
Product Lifecycle Stages
Extrusion machines typically go through several stages in their product lifecycle, from introduction and growth to maturity and potential decline. Current trends indicate a strong focus on the growth stage, driven by continuous technological innovations and expanding applications in various industries. The introduction of more efficient and versatile machines is expected to prolong the growth phase.
Customer Pain Points
Despite positive growth trends, the high cost of extrusion machinery and technical limitations remain significant barriers. These challenges affect the adoption rate, particularly among small and medium-sized enterprises. Additionally, maintenance and operational challenges associated with complex machinery can hinder market expansion.
Brand Positioning and Differentiation Strategies
Leading brands in the extrusion machinery market, such as Davis-Standard and Hindalco, are focusing on strategic acquisitions and partnerships to enhance their technological capabilities and market presence. Differentiation strategies include offering customized solutions, integrating advanced technologies, and emphasizing sustainability to meet the evolving needs of consumers.
Niche Markets
Niche markets within the extrusion machinery sector include specialized applications such as high-speed rail coach components and precision medical devices. Companies are leveraging their expertise in specific areas to cater to these niche markets, offering tailored solutions that meet stringent industry requirements.
Key Factors When Selecting an Extrusion Machine
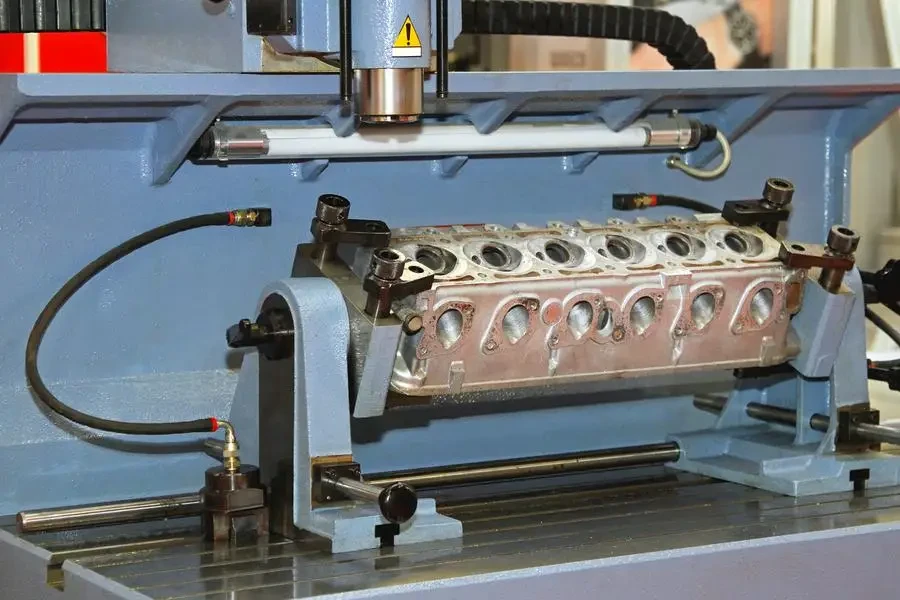
Choosing the right extrusion machine for your production needs involves evaluating various technical and functional aspects. These machines, pivotal in the plastics, metals, and composites industries, must be selected with precision to ensure efficiency, quality, and cost-effectiveness. Below are the key factors to consider:
Type of Extrusion Machine
The type of extrusion machine is a fundamental consideration. Extrusion machines are categorized based on the materials they process and the technology they use. For instance, plastic extruders are designed specifically for shaping plastic materials in applications such as pipe extrusion, profile extrusion, and sheet extrusion. Metal and rubber extrusion machines are also available, each tailored to handle their respective materials. The choice between hot and cold extrusion technologies must be made based on the production process requirements. Hot extrusion machines are suitable for materials that require preheating, whereas cold extrusion machines are used for materials processed at room temperature.
Technical Specifications
Technical specifications such as screw design, barrel construction, and die configurations play a crucial role in the performance of an extrusion machine. The material of the screw, commonly made from high-carbon, high-chrome tool steels, and surface treatments like nitriding or chrome plating, determine the machine’s durability and efficiency. The length-to-diameter ratio of the screw, flight depth, and pitch are vital parameters influencing the machine’s ability to provide consistent feeding, uniform melting, steady pumping, and homogeneous mixing. These specifications must align with the production process requirements to ensure optimal performance.
Energy Efficiency
Energy efficiency is a critical factor, especially in today’s environmentally conscious market. Modern extrusion machines are designed to minimize energy consumption while maximizing output. Features such as energy-efficient motors, advanced heating systems, and optimized screw designs contribute to reducing the overall energy footprint of the extrusion process. Investing in energy-efficient machines reduces operational costs and helps achieve sustainability goals.
Build Quality and Durability
The build quality and durability of an extrusion machine are paramount, given the demanding nature of extrusion processes. Machines constructed with high-quality materials and robust engineering are more likely to withstand continuous operation. Wear-resistant and corrosion-resistant liners in the barrel, along with durable screw materials, ensure the machine’s longevity. Regular maintenance and the availability of spare parts are essential to keep the machine running smoothly over its lifespan.
Compatibility with Future Upgrades
As technology evolves, the ability to upgrade extrusion machines becomes increasingly important. Machines designed with modular components and open interfaces allow for easier integration of new technologies and enhancements. This future-proofing capability ensures that the machine can adapt to changing production requirements and technological advancements, extending its useful life and maximizing return on investment.
Advanced Features of Modern Extrusion Machines
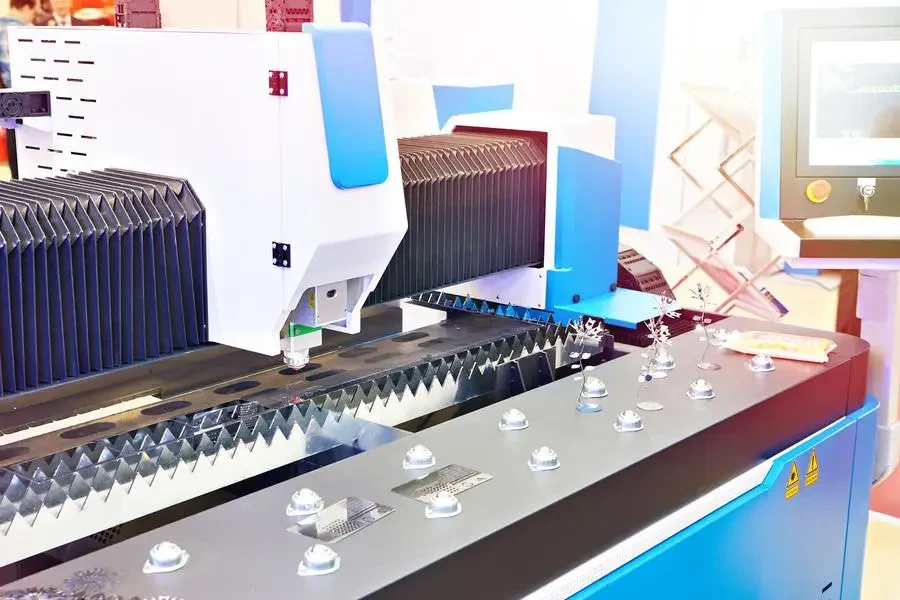
In the rapidly evolving field of extrusion technology, modern extrusion machines come equipped with advanced features that significantly enhance their performance and versatility.
Automation and Control Systems
Automation plays a crucial role in modern extrusion machines. Advanced control systems, often utilizing PLCs (Programmable Logic Controllers) or CNC (Computer Numerical Control), allow for precise control over various parameters such as temperature, pressure, and speed. These systems enable consistent product quality and reduce the need for manual intervention. Real-time monitoring and data logging capabilities provide valuable insights into the extrusion process, facilitating predictive maintenance and process optimization.
Multi-Layer Extrusion
Multi-layer extrusion technology is becoming increasingly popular, especially in the production of packaging materials and complex profiles. This technology allows for the extrusion of multiple layers of different materials simultaneously, resulting in products with enhanced properties such as improved barrier performance, mechanical strength, and aesthetic appeal. Multi-layer extruders are equipped with multiple extruder heads and sophisticated die systems to ensure precise layer distribution and adhesion.
Energy Recovery Systems
Energy recovery systems are an innovative feature in modern extrusion machines. These systems capture and reuse waste heat generated during the extrusion process, improving overall energy efficiency. By reducing the need for external heating sources, energy recovery systems help lower operational costs and minimize the environmental impact of the extrusion process.
Safety and Compliance Standards
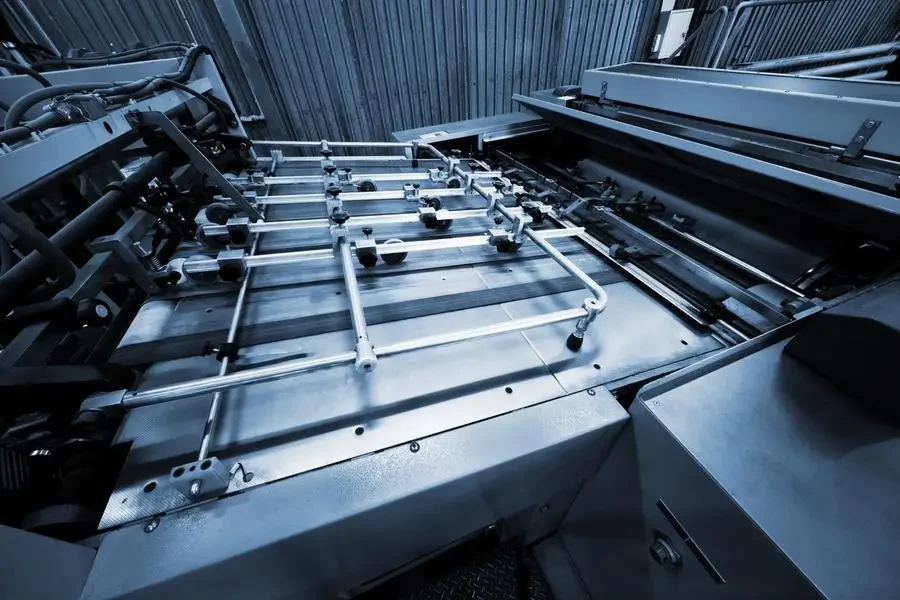
Ensuring safety and regulatory compliance is paramount when selecting an extrusion machine. Machines must adhere to industry-specific safety standards and certifications to protect operators and ensure safe operation.
Safety Features
Modern extrusion machines are equipped with a range of safety features such as emergency stop buttons, safety guards, and interlock systems. These features are designed to prevent accidents and ensure the safety of operators. Advanced monitoring systems can detect anomalies and shut down the machine automatically to prevent damage and ensure safety.
Regulatory Compliance
Compliance with regulatory standards is essential for ensuring that the extrusion machine meets industry requirements. Standards such as ISO, CE, and UL certifications provide assurance that the machine adheres to established safety, quality, and performance criteria. Regular audits and inspections help maintain compliance and ensure that the machine operates within the required guidelines.
Environmental Regulations
Extrusion machines must also comply with environmental regulations, including guidelines on emissions, waste management, and energy consumption. Machines designed with eco-friendly features such as energy-efficient motors, low-emission heating systems, and waste recycling capabilities help meet these regulations and promote sustainable manufacturing practices.
Cost Considerations and ROI
The cost of an extrusion machine is a significant factor in the decision-making process. It is important to consider not just the initial purchase price but also the total cost of ownership and return on investment (ROI).
Initial Purchase Price
The initial purchase price of an extrusion machine can vary widely depending on its specifications, features, and brand. It is essential to evaluate the machine’s capabilities and ensure that it meets the production process requirements. While cheaper machines may seem attractive, they may lack the advanced features and durability required for long-term operation.
Operational Costs
Operational costs, including energy consumption, maintenance, and labor, must be factored into the total cost of ownership. Energy-efficient machines, while potentially more expensive upfront, can result in significant savings over time. Machines with low maintenance requirements and user-friendly interfaces can reduce labor costs and downtime.
Return on Investment
Calculating the ROI involves assessing the machine’s productivity, efficiency, and lifespan. A machine that produces high-quality products consistently and operates efficiently will provide a better ROI. Considering the potential for future upgrades and the machine’s resale value can further enhance the ROI.
Quality and Performance Metrics
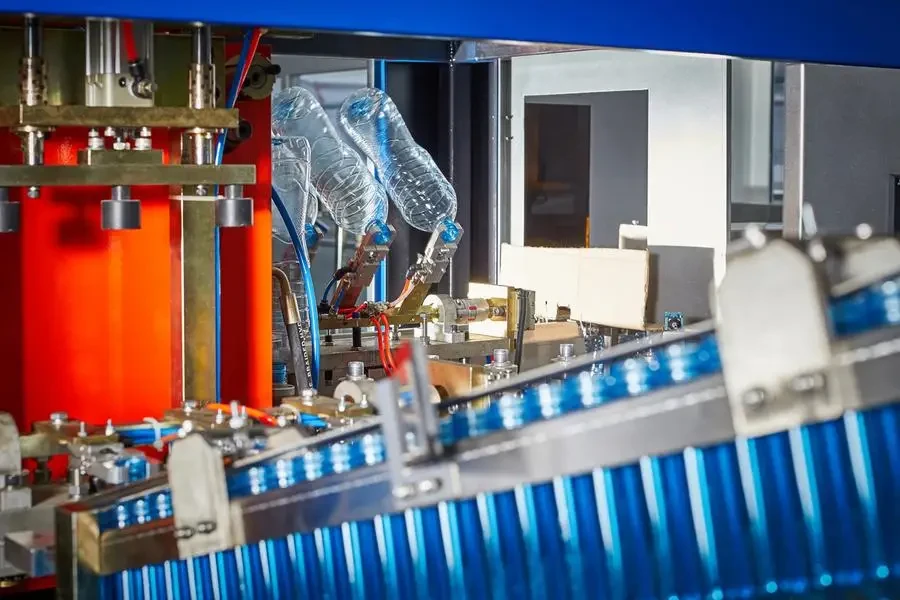
The quality and performance of an extrusion machine are critical determinants of its suitability for a given application. Evaluating these metrics ensures that the machine can meet the desired production standards and deliver consistent results.
Product Quality
The ability of the extrusion machine to produce high-quality products is a key performance metric. Factors such as dimensional accuracy, surface finish, and material properties must be assessed. Machines with advanced control systems and precise die configurations are better equipped to deliver consistent product quality.
Throughput and Efficiency
Throughput, or the rate at which the machine can produce finished products, is an important performance metric. High-throughput machines enable faster production cycles and increased output. Efficiency, measured in terms of energy consumption and material utilization, also plays a crucial role in determining the machine’s overall performance.
Reliability and Uptime
The reliability of the extrusion machine, including its ability to operate continuously without frequent breakdowns, is essential for maintaining production schedules. Machines with robust construction, high-quality components, and regular maintenance schedules ensure maximum uptime and minimize disruptions.
Packaging and Shipping Considerations
Packaging and shipping of extrusion machines are often overlooked but are crucial aspects that can impact the overall investment.
Packaging Quality
Proper packaging ensures that the machine is protected during transit and arrives in optimal condition. High-quality packaging materials, such as reinforced crates and protective coverings, help prevent damage during shipping.
Shipping Logistics
Shipping logistics, including the choice of carrier, shipping method, and delivery timeline, must be carefully planned. Working with reputable logistics providers and ensuring proper documentation can help avoid delays and additional costs.
Installation and Setup
Once the machine arrives, the installation and setup process must be managed efficiently. This includes ensuring that the machine is installed correctly, calibrated, and tested before commencing production. Professional installation services and technical support from the manufacturer can facilitate a smooth setup process.
Final Thoughts
Selecting the right extrusion machine involves a comprehensive evaluation of various factors, from technical specifications and advanced features to cost considerations and quality metrics. By taking a holistic approach and considering both immediate and long-term requirements, businesses can make informed decisions that enhance their production capabilities and ensure a positive return on investment.
In conclusion, choosing an extrusion machine is a complex process that requires careful consideration of numerous factors. By focusing on key aspects such as machine type, technical specifications, energy efficiency, build quality, and regulatory compliance, businesses can select a machine that meets their specific needs and delivers optimal performance.