In 2025, the air cylinder market continues to thrive, driven by automation and smart manufacturing trends. This article explores critical factors such as cylinder stroke, operating pressure, bore size, body material, and force requirements. Professional buyers will gain valuable insights and guidance to make informed decisions, ensuring optimal performance and compatibility with their specific applications.
Table of Contents:
-Air Cylinders Market Overview
-In-Depth Analysis of the Air Cylinder Market
-Key Factors When Selecting an Air Cylinder
-Advanced Features and Technology in Air Cylinders
-Maintenance and Longevity of Air Cylinders
-Final Thoughts
Air Cylinders Market Overview
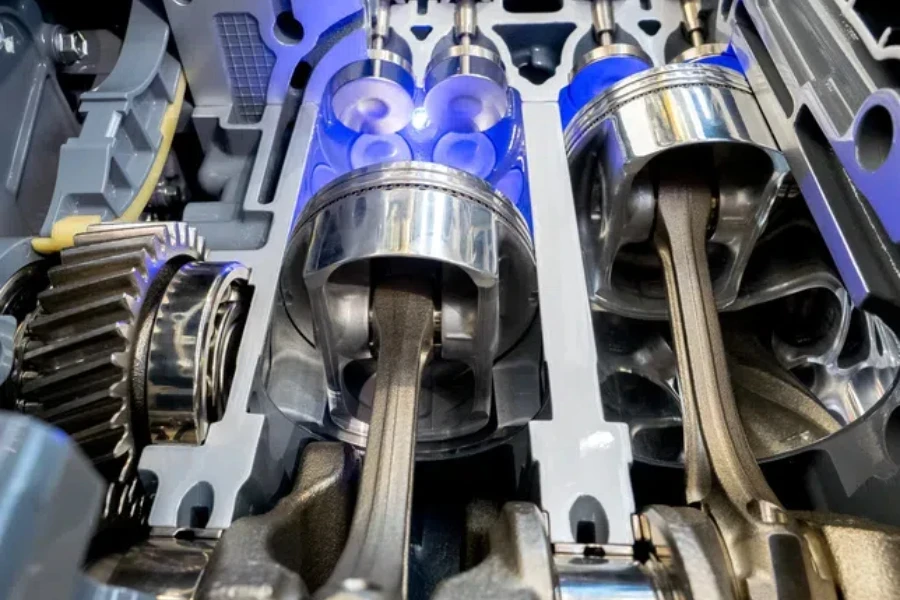
The global air cylinder market is experiencing significant growth, driven by advancements in automation and the rising demand for efficient motion control solutions across various industries. In 2023, the market was worth approximately USD 15.4 billion and is projected to reach USD 20.2 billion by 2030, growing at a compound annual growth rate (CAGR) of 4.0%. This growth is primarily due to the trend towards Industry 4.0 and smart manufacturing, which require advanced pneumatic systems.
In the U.S., the market was estimated at USD 4.2 billion in 2023. China is expected to grow at an impressive CAGR of 7.5%, reaching USD 4.3 billion by 2030. Other key regions, including Japan, Canada, and Germany, also contribute significantly to the market, supported by robust industrial activities and technological innovations in pneumatic systems. The Asia-Pacific region, in particular, is witnessing rapid industrialization and infrastructure development, further boosting the demand for air cylinders.
The market is segmented into single-acting and double-acting cylinders. The latter segment is expected to reach USD 13.2 billion by 2030, growing at a CAGR of 4.2%. Single-acting cylinders, while growing at a slower rate of 3.5% CAGR, still hold a substantial market share. This segmentation reflects the diverse applications and performance requirements in industries such as automotive, food and beverage, and packaging.
In-Depth Analysis of the Air Cylinder Market
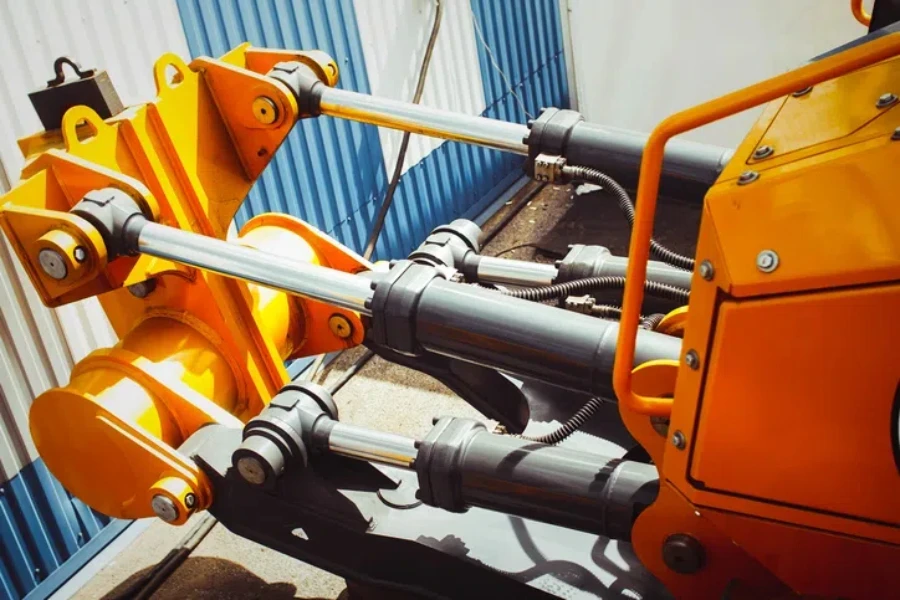
The air cylinder market is characterized by key performance benchmarks and market dynamics. Technological advancements, such as the integration of sensors for real-time monitoring and control, are enhancing the functionality and reliability of pneumatic systems. These innovations are crucial for industries aiming to reduce downtime and maintenance costs, thereby driving the adoption of high-performance air cylinders.
Economic influences, including the expansion of automated industrial processes and the rising emphasis on sustainability, are also shaping the market. The development of eco-friendly and energy-efficient pneumatic systems addresses the growing focus on reducing environmental impact and operational costs. This trend is particularly evident in regions with stringent environmental regulations, such as Europe and North America, where companies are increasingly investing in sustainable technologies.
Consumer behavior is shifting towards durable and reliable motion control solutions. This shift is supported by the increasing complexity of industrial applications, which demand precise and consistent performance from pneumatic systems. Additionally, the rise of digitalization and smart manufacturing is driving the need for advanced air cylinders that can integrate seamlessly with automated systems and provide real-time data for predictive maintenance and optimization.
Distribution channels for air cylinders are evolving, with a growing emphasis on online platforms and direct sales to end-users. This shift is facilitated by the increasing availability of digital tools that enable manufacturers to reach a broader customer base and provide customized solutions. Furthermore, strategic partnerships and collaborations among key players are enhancing market reach and product offerings, contributing to a competitive landscape.
Recent innovations in the air cylinder market include the development of lightweight and compact designs that offer enhanced performance and ease of installation. These products are particularly suited for applications in space-constrained environments, such as robotics and medical devices. The lifecycle stages of air cylinders are also evolving, with a focus on extending product durability and reducing total cost of ownership through improved materials and manufacturing processes.
Key Factors When Selecting an Air Cylinder
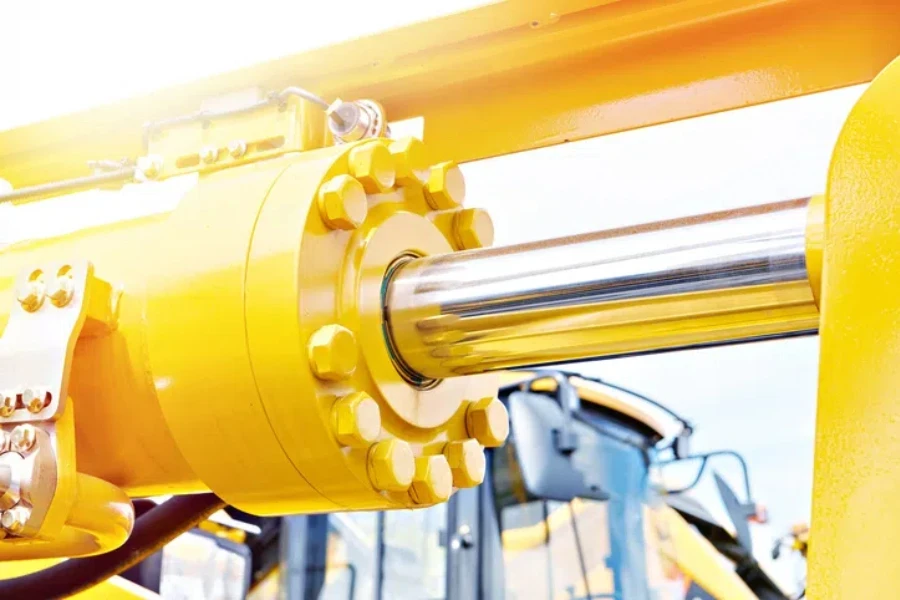
When selecting an air cylinder, various factors must be considered to ensure optimal performance and compatibility with your specific application. These include cylinder stroke, operating pressure, bore size, body material, and force requirements. Here, we delve into these elements to provide a comprehensive understanding of what to look for when choosing an air cylinder.
Cylinder Stroke
The stroke of an air cylinder defines the distance the piston rod travels from its fully retracted to fully extended position. This parameter directly influences the range of motion the cylinder can achieve in your application. For instance, applications requiring long-distance travel, such as conveyor systems or large-scale lifting operations, need a longer stroke cylinder. Conversely, for precise, short-range movements, a shorter stroke is more appropriate. The stroke length must be matched to the required movement to avoid underperformance or mechanical strain. Additionally, the stroke length impacts the overall size of the cylinder, which can affect space constraints within the installation environment.
Operating Pressure
Operating pressure dictates the force generated by the air cylinder. Measured in pounds per square inch (psi), it represents the pressure of the compressed air driving the piston. Different applications require varying pressure levels. For example, high-pressure applications like heavy-duty lifting or industrial automation may need cylinders capable of handling pressures upwards of 150 psi. Light-duty tasks might only need cylinders operating at lower pressures, around 30-60 psi. Ensuring the air cylinder can operate within the required pressure range is essential for maintaining system efficiency and avoiding component failure.
Bore Size
The bore size of an air cylinder refers to the internal diameter of the cylinder barrel. This dimension determines the surface area on which the compressed air acts, influencing the force output. A larger bore size typically results in greater force output, suitable for applications requiring significant pushing or pulling forces. Bore sizes range from 2.5 mm for miniature applications to 400 mm for heavy industrial tasks. The selection of the bore size should align with the load requirements to ensure effective performance without excessive wear. Additionally, the bore size affects the overall dimensions and weight of the cylinder.
Body Material
The material used to construct the air cylinder body plays a significant role in its durability, weight, and suitability for specific environments. Common materials include aluminum, steel, stainless steel, and plastic, each with distinct advantages and drawbacks. Aluminum cylinders are lightweight and resistant to corrosion, ideal for applications where weight is a concern. Steel and stainless steel cylinders offer superior strength and durability, suitable for heavy-duty and high-pressure applications. Stainless steel provides excellent corrosion resistance, making it ideal for harsh or corrosive environments. Plastic cylinders are used where chemical resistance and lightweight are paramount. The choice of body material should consider the environmental conditions, load requirements, and specific industry standards or regulations.
Force Requirements
The force exerted by an air cylinder is a function of the bore size, operating pressure, and specific application requirements. Calculating the necessary force involves understanding the load the cylinder needs to move and any additional factors such as friction or acceleration. For example, the force can be calculated using the formula Fτ = P(∏r²), where Fτ is the resultant force, P is the pressure, and r is the radius of the piston. This calculation helps determine the appropriate cylinder size and pressure rating needed to achieve the desired performance. In applications requiring precise control and varying force levels, it might be necessary to use cylinders with adjustable force capabilities or incorporate external control mechanisms.
Advanced Features and Technology in Air Cylinders
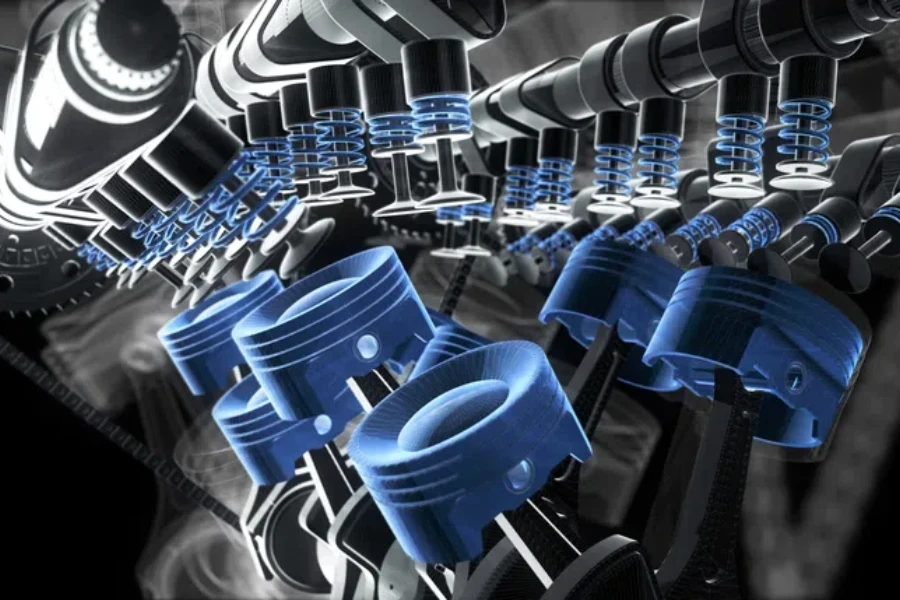
As technology advances, air cylinders have evolved to include various features and enhancements that improve performance, safety, and ease of use. Understanding these advanced features can help in selecting the right cylinder for your application.
Adjustable Stroke and Cushions
Many modern air cylinders come with adjustable stroke capabilities, allowing for fine-tuning of the end points of the piston travel. This adjustability is useful in applications requiring precise positioning and control. Cushions, or bumpers, help in decelerating the piston before it reaches the end of its stroke, reducing impact and noise. Adjustable cushions allow for customization of the deceleration rate, providing smoother operation and prolonging the cylinder’s lifespan.
Magnetic and Non-Rotating Rods
Magnetic rods equipped with sensors can provide position feedback, enabling real-time monitoring and control of the cylinder’s position. This feature is essential in automated systems where precise positioning is critical. Non-rotating rods are designed to prevent the piston from rotating, ensuring consistent and accurate linear motion. This is particularly important in applications requiring precise alignment, such as assembly lines or robotic systems.
Integrated Sensors and Control Systems
The integration of sensors and control systems into air cylinders has significantly enhanced their functionality. Sensors can detect the position, speed, and load on the cylinder, providing valuable data for monitoring and control. Control systems can use this data to adjust the cylinder’s operation in real-time, optimizing performance and ensuring safety. For example, closed-loop control systems continuously compare the cylinder’s performance with the desired parameters and make adjustments to maintain optimal operation.
Energy Efficiency and Environmental Protection
Energy efficiency is a growing concern in industrial applications, and air cylinders have been designed to address this issue. Features such as low-friction seals and efficient air distribution systems help reduce energy consumption and improve overall efficiency. Environmental protection features, such as water-resistant seals and corrosion-resistant materials, ensure that air cylinders can operate reliably in harsh conditions. These features are particularly important in industries such as marine, chemical processing, and outdoor applications.
Maintenance and Longevity of Air Cylinders
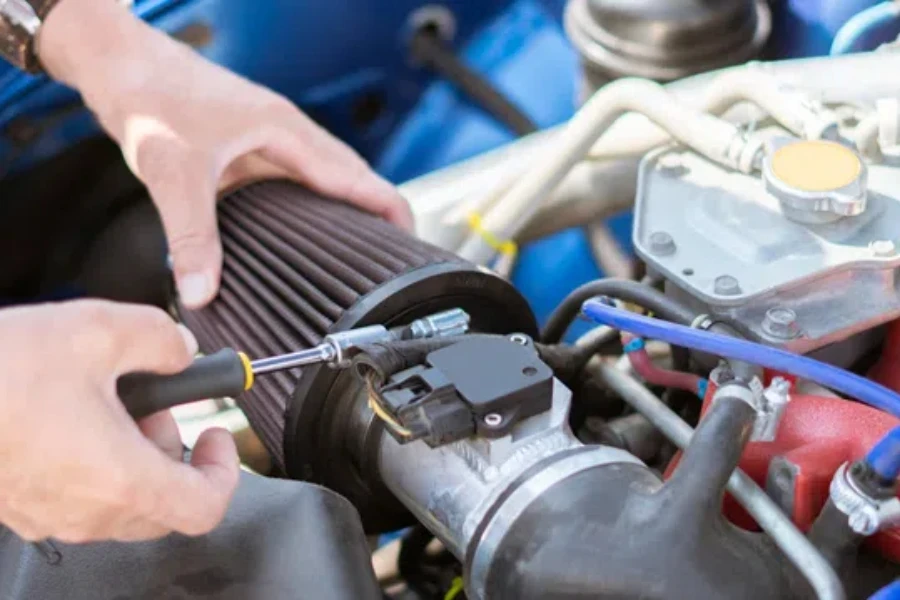
Proper maintenance is crucial for ensuring the longevity and reliable performance of air cylinders. Regular inspection and servicing can prevent common issues such as leaks, wear, and contamination.
Regular Inspection and Lubrication
Regular inspection of air cylinders involves checking for signs of wear, damage, and leaks. Components such as seals, rods, and bearings should be inspected and replaced if necessary. Lubrication is essential for reducing friction and wear on moving parts. Using the appropriate lubricant and following the manufacturer’s recommended maintenance schedule can significantly extend the cylinder’s lifespan.
Contamination Control
Contamination from particles, moisture, and other impurities can cause significant damage to air cylinders. Using filters and dryers in the air supply system can help prevent contamination. Regularly cleaning the cylinder and its components can also reduce the risk of contamination-related issues.
Proper Storage and Handling
Proper storage and handling of air cylinders are crucial for preventing damage and ensuring their longevity. Cylinders should be stored in a clean, dry environment and protected from physical damage. Handling should be done with care to avoid dropping or striking the cylinder, which can cause damage to the internal components.
Final Thoughts
In conclusion, selecting the right air cylinder involves a thorough understanding of the application requirements, including stroke length, operating pressure, bore size, body material, and force requirements. Advanced features and technology, such as adjustable stroke, magnetic rods, and integrated sensors, can enhance performance and provide additional functionality. Proper maintenance and contamination control are essential for ensuring the longevity and reliable operation of air cylinders. By considering these factors and following best practices, you can select an air cylinder that meets your needs and provides optimal performance.