The global pipe flanges market is projected to reach USD 8.52 billion by 2030, driven by innovations in materials and smart technologies. This article provides a comprehensive analysis of key factors to consider when selecting a pipe flange, emphasizing the importance of material compatibility, pressure and temperature ratings, and compliance with industry standards. This guide is invaluable for professional buyers seeking to make informed decisions in stocking and selling pipe flanges.
Table of Contents:
– Market Overview of Pipe Flanges in 2025
– In-depth Analysis of the Pipe Flange Market
– Key Factors When Selecting Pipe Flanges
– Advanced Features and Technology in Pipe Flanges
– Trends in Pipe Flange Industry
– Final Thoughts
Market Overview of Pipe Flanges in 2025

The global pipe flanges market has grown from USD 6.16 billion in 2023 to USD 6.45 billion in 2024. This market is expected to continue growing at a compound annual growth rate (CAGR) of 4.73%, reaching approximately USD 8.52 billion by 2030. The demand for pipe flanges is driven by their essential role in various industrial applications, particularly in the oil and gas, chemical processing, and water treatment sectors.
Pipe flanges facilitate the assembly and disassembly of piping systems, which is crucial for maintenance, inspection, and modifications. Their versatility, available in various sizes, materials, and pressure ratings, supports widespread use across multiple industries. However, challenges such as leakage risks due to improper installation or environmental degradation can hinder market growth. Innovations in durable, lightweight, and corrosion-resistant materials are expected to further propel the market, especially in emerging sectors like renewable energy and desalination plants.
Regionally, the Americas, particularly the United States and Canada, represent significant markets due to their robust oil and gas industries and stringent safety standards. The Asia-Pacific region, led by China, Japan, and India, is experiencing rapid industrial growth, driving substantial demand for pipe flanges. In Europe, the focus on sustainability and green policies influences the market, with a growing need for environmentally friendly products. The Middle East and Africa continue to rely heavily on flanges for oil and gas and infrastructure projects.
In-depth Analysis of the Pipe Flange Market
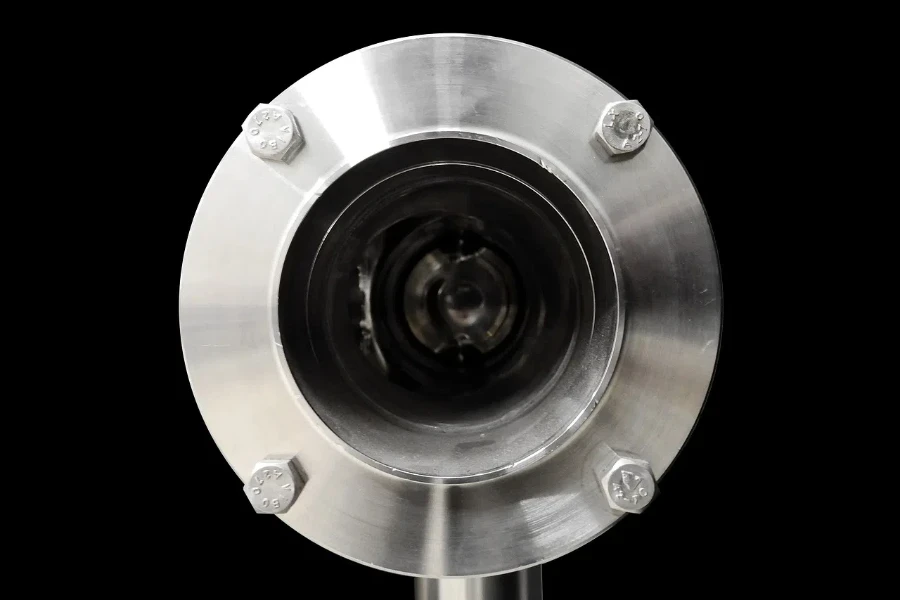
The pipe flange market offers a diverse range of product types and materials, each serving specific industrial needs. Key product types include blind flanges, lap joint flanges, orifice flanges, slip-on flanges, and socket weld flanges. These products cater to different requirements, from sealing off pipe ends to facilitating easy disassembly for maintenance purposes.
The market’s growth is significantly influenced by the expansion of the oil and gas industry and the increasing adoption of renewable energy installations. Innovations in materials, particularly the development of lighter, stronger, and more corrosion-resistant alloys, are driving market dynamics. Companies are focusing on integrating smart technologies into flanges for real-time monitoring, which can minimize failure risks and extend operational lifespans.
Economic factors such as raw material price volatility and the need for regular maintenance present challenges. However, the opportunities in 3D printing for customized flange production and the integration of smart technologies are promising. The industry is also seeing a shift towards more sustainable practices, with increased demand for products that align with environmental standards.
Leading vendors like Alliance Engineering Company, Amco Metals, and Dynamic Forge & Fittings (I) P. Limited are at the forefront of innovation. The competitive landscape is shaped by technological advancements and strategic collaborations. For instance, GPT Industries’ alliance with AFES enhances flange management solutions, showcasing the trend towards comprehensive, integrated service offerings.
The distribution channels for pipe flanges are evolving, with a growing preference for digital platforms that offer enhanced accessibility and efficiency. This shift is driven by the need for rapid procurement and the convenience of online transactions. Customer behavior is also changing, with a greater emphasis on product quality, durability, and compliance with safety standards.
Recent innovations, such as igus’s sensor-equipped fixed flange bearings, highlight the industry’s move towards smart, predictive maintenance solutions. These advancements are crucial in reducing operational downtimes and maintenance costs, making them valuable across various industrial applications.
Key Factors When Selecting Pipe Flanges
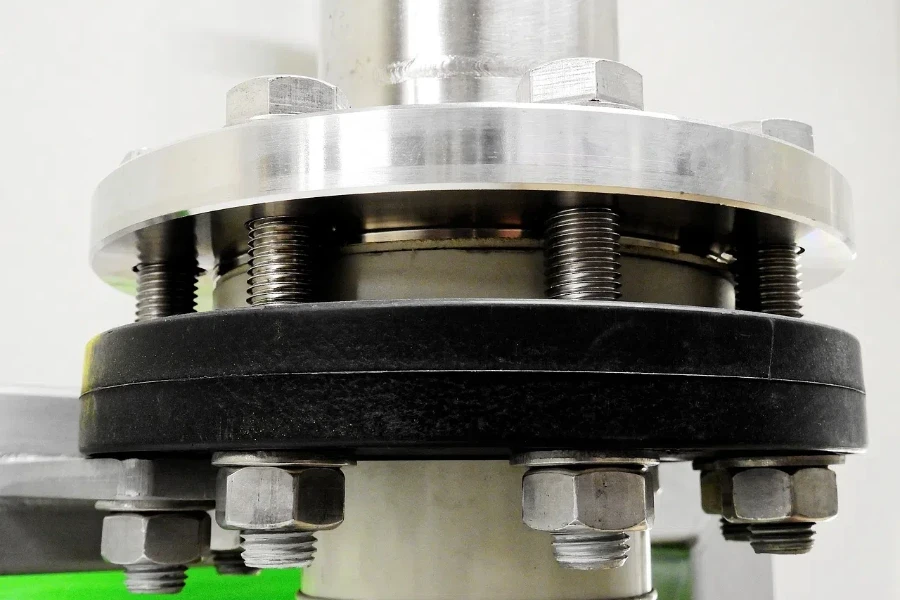
Choosing the right pipe flange is critical for ensuring the safety, reliability, and efficiency of piping systems across various industries. Below are the primary considerations to keep in mind:
Material Selection
The material of the pipe flange must be compatible with the pipe material and the type of fluid being transported. Common materials include stainless steel, carbon steel, and various alloys. Stainless steel flanges resist corrosion, making them ideal for chemical processing and marine applications. Carbon steel flanges are strong and durable, suitable for high-pressure applications. Alloy flanges, made from materials like nickel or titanium, resist extreme temperatures and corrosive environments.
Pressure and Temperature Ratings
Pipe flanges must withstand the operational pressure and temperature conditions of the system. The American National Standards Institute (ANSI) classifies flanges into different pressure classes, ranging from 150 to 2500. It’s crucial to select a flange with a pressure rating that matches or exceeds the system’s maximum operating pressure. Temperature ratings are equally important. For instance, stainless steel flanges generally operate at higher temperatures compared to carbon steel flanges. Always consult the manufacturer’s specifications to ensure the flange can handle the expected temperature range.
Size and Dimensions
The size and dimensions of the flange must match the piping system’s specifications, including the nominal pipe size (NPS), the flange’s outer diameter (OD), and the bolt circle diameter (BCD). The thickness of the flange and the diameter of the bolt holes are also critical to ensure a proper fit and reliable sealing. Flanges are typically available in standard sizes, but custom dimensions can be manufactured for specific applications. Proper alignment of the flange with the piping system is essential to prevent leaks and ensure efficient operation.
Type of Flange
There are several types of flanges, each designed for specific applications and installation methods. Common types include Weld Neck Flanges, known for their high strength and stress distribution, suitable for high-pressure and high-temperature applications; Slip-On Flanges, easier to install and ideal for lower pressure applications; Blind Flanges, used to close the end of a piping system, providing easy access for maintenance; Socket Weld Flanges, suitable for small-diameter, high-pressure pipes; and Threaded Flanges, used in systems where welding is not possible, providing a simple connection.
Standards and Certifications
Compliance with industry standards and certifications is crucial for ensuring the quality and reliability of pipe flanges. Standards such as ANSI, ASME (American Society of Mechanical Engineers), and ISO (International Organization for Standardization) provide guidelines for manufacturing, testing, and performance. Certifications from recognized bodies, such as the Pressure Equipment Directive (PED) and the American Petroleum Institute (API), indicate that the flanges meet stringent quality and safety requirements. Always verify that the flanges are certified for their intended use.
Advanced Features and Technology in Pipe Flanges
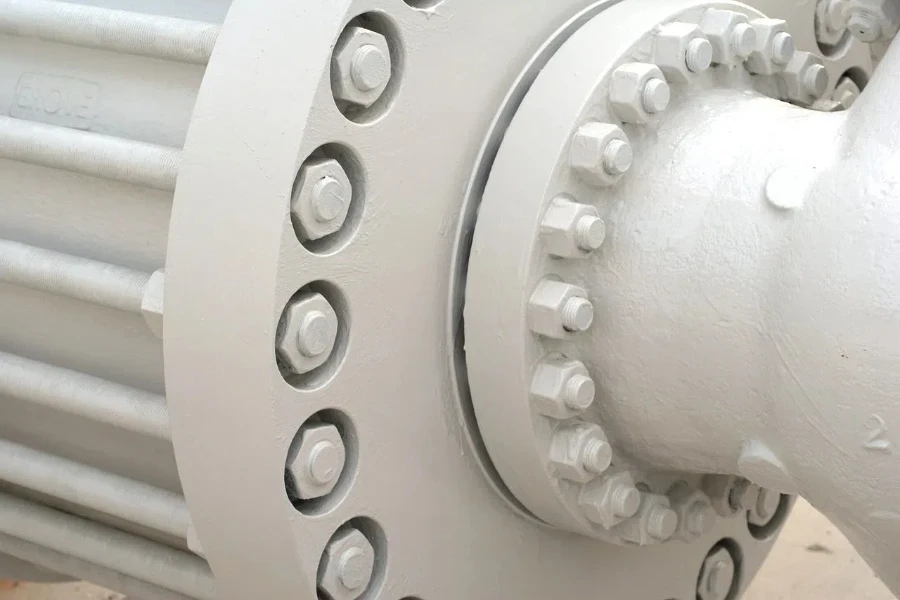
Advanced Coatings and Linings
Modern pipe flanges often come with advanced coatings and linings that enhance their performance and longevity. Coatings like epoxy, PTFE (Polytetrafluoroethylene), and zinc provide additional protection against corrosion, chemical exposure, and wear. PTFE linings resist a wide range of chemicals and can operate at high temperatures, making them ideal for aggressive environments. Epoxy coatings offer excellent adhesion and durability, suitable for both internal and external protection.
Integration with Smart Technologies
The integration of smart technologies into pipe flanges is an emerging trend that offers significant advantages in monitoring and maintenance. Smart flanges equipped with sensors provide real-time data on pressure, temperature, and flow rates, enabling predictive maintenance and reducing the risk of unexpected failures. These smart flanges can be connected to a centralized monitoring system, allowing for remote diagnostics and real-time alerts. This technology is particularly beneficial in critical applications such as oil and gas, where downtime can be costly.
Enhanced Sealing Mechanisms
Innovations in sealing mechanisms have led to the development of flanges with enhanced sealing capabilities. For instance, spiral wound gaskets and kammprofile gaskets offer superior sealing performance under varying pressure and temperature conditions. Spiral wound gaskets combine metal and filler material, providing flexibility and strength. Kammprofile gaskets have a serrated metal core with a soft sealing layer, ensuring a tight and reliable seal. These gaskets are particularly effective in high-temperature and high-pressure applications.
Customization and Modular Designs
Customization and modular designs are becoming more prevalent in the pipe flange industry. Custom flanges can be designed to meet specific application requirements, including unique dimensions, materials, and coatings. Modular flange systems allow for easy assembly and disassembly, making them ideal for applications that require frequent maintenance or reconfiguration. These systems can be quickly adapted to changing operational needs, providing flexibility and efficiency.
Trends in Pipe Flange Industry
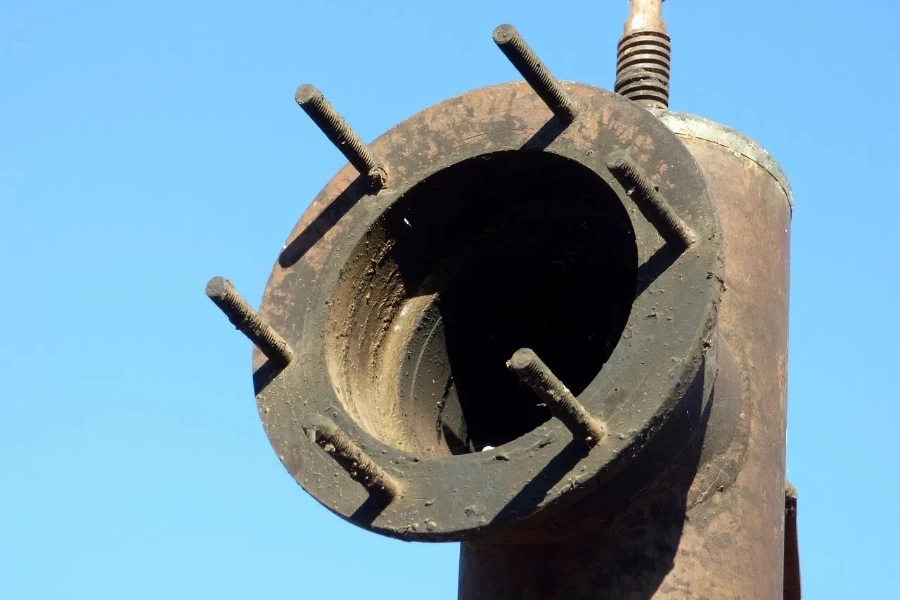
Sustainable Materials
The use of sustainable materials in the manufacturing of pipe flanges is gaining traction. Recycled metals and eco-friendly coatings are being adopted to reduce the environmental impact of production processes. This trend aligns with the growing emphasis on sustainability and corporate social responsibility in the industry.
Digital Twin Technology
Digital twin technology is revolutionizing the way pipe flanges are designed, tested, and maintained. By creating a virtual replica of the flange, manufacturers can simulate various operating conditions and optimize the design for performance and durability. This technology also facilitates predictive maintenance by providing real-time insights into the flange’s condition.
Additive Manufacturing
Additive manufacturing, or 3D printing, is being increasingly used to produce complex flange designs that are difficult to achieve with traditional manufacturing methods. This technology allows for rapid prototyping and customization, reducing lead times and costs. Additive manufacturing also enables the production of lightweight and high-strength flanges, enhancing their performance.
Final Thoughts
In summary, the selection of pipe flanges involves careful consideration of material, pressure and temperature ratings, size and dimensions, type, and compliance with standards and certifications. Advanced features such as smart technologies, enhanced sealing mechanisms, and customization options are driving innovation in the industry. Staying abreast of trends like sustainable materials, digital twin technology, and additive manufacturing will ensure that you make informed decisions and optimize the performance of your piping systems.