The demand for powder coating machines surged in 2025, driven by the need for eco-friendly and durable finishes in various industries. This article provides an in-depth analysis of the powder coating machine market, covering key factors to consider, technological advancements, and market trends. It offers valuable insights for professional buyers, ensuring informed decisions and optimized operations.
Table of Contents:
-Market Overview of Powder Coating Machines
-Detailed Introduction and Analysis of the Powder Coating Machine Market
-Key Factors to Consider When Choosing a Powder Coating Machine
-Advanced Features and Technological Innovations
-Market Trends and Future Developments
-Summary and Final Thoughts
Market Overview of Powder Coating Machine
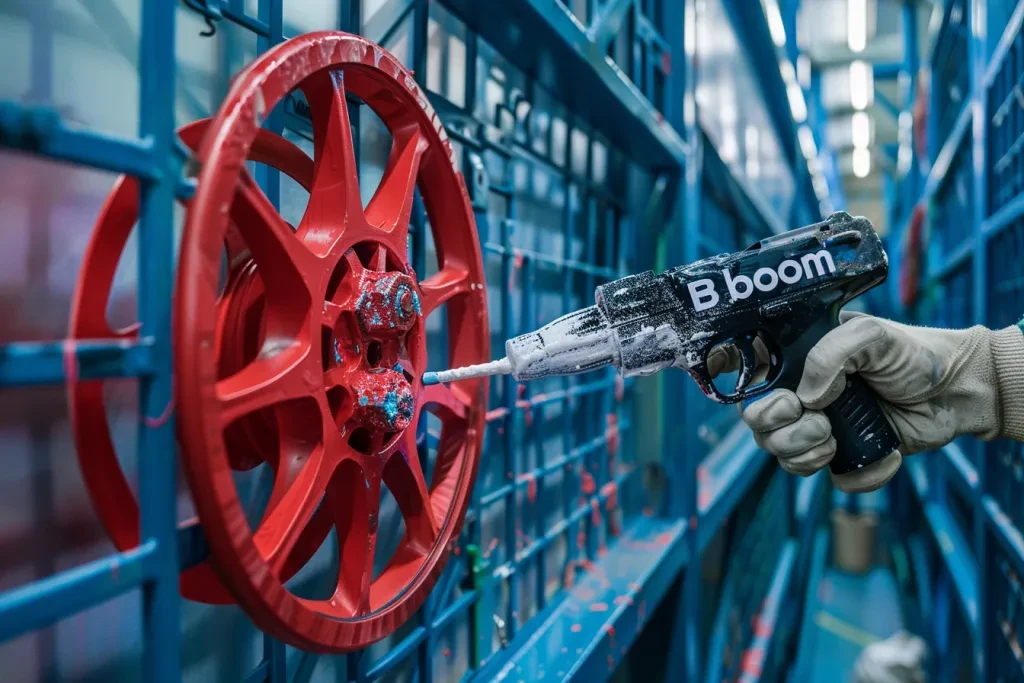
The global powder coating machine market is growing rapidly. Its market size is estimated to be USD 2.4 billion in 2024 and is projected to reach USD 3.9 billion by 2030, with a CAGR of 8.5%. This growth is driven by the rising demand for durable, high-quality finishes in industries like automotive, consumer appliances, and industrial machinery. Increased awareness and regulatory support for eco-friendly coating solutions have also boosted the adoption of powder coating technologies.
Powder coating machines are crucial for applying powder coatings, which are dry, free-flowing powders applied electrostatically and then cured under heat to form a hard finish. These machines are categorized based on their application processes, such as electrostatic spray guns, fluidized bed coating, and electrostatic fluidized bed coating. The electrostatic spray gun segment holds the largest market share, over 60% in 2024, due to its versatility and efficiency in coating various substrates.
Regionally, Asia-Pacific leads the market, with China and India being major contributors. The region accounted for over 40% of the global market share in 2024, driven by rapid industrialization, urbanization, and the booming automotive and consumer electronics industries. North America and Europe also hold significant market shares due to the increasing demand for sustainable and high-performance coatings.
Detailed Introduction and Analysis of the Powder Coating Machine Market
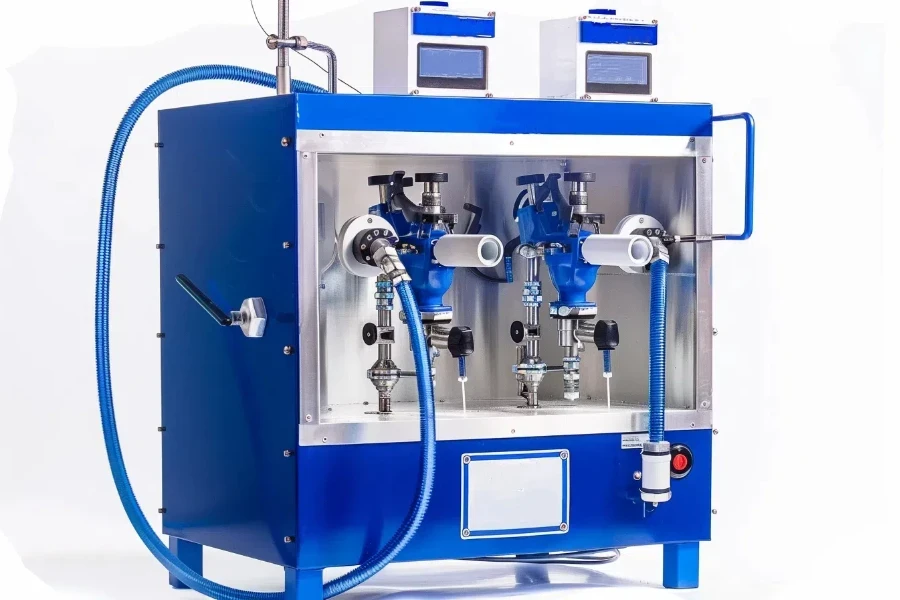
Powder coating machines are essential for achieving high-quality, durable, corrosion-resistant, and aesthetically appealing finishes. These machines are extensively used in the automotive industry, where the market for automotive paints and coatings was worth USD 24.28 billion in 2024 and is expected to reach USD 39.86 billion by 2030. The demand for powder coatings in this sector is driven by the need for eco-friendly solutions that comply with stringent environmental regulations.
Key performance benchmarks for powder coating machines include transfer efficiency, coating uniformity, and curing time. High transfer efficiency reduces material wastage, making the process more cost-effective and environmentally friendly. Coating uniformity ensures consistent quality, crucial for industries like automotive and consumer electronics, where aesthetic and functional properties are vital. Innovations such as digitalization and automation in powder coating processes have enhanced these performance benchmarks, leading to improved productivity and reduced operational costs.
Market share dynamics in the powder coating machine industry are influenced by technological advancements, product lifecycle stages, and consumer behavior shifts. The increasing preference for powder coatings over liquid coatings, due to their environmental benefits and superior performance, has driven market growth. Additionally, the shift towards digitalization and automation has led to the development of advanced powder coating machines equipped with IoT and AI capabilities, enabling real-time monitoring and control of the coating process. These innovations have positioned leading brands like Nordson Corporation, Gema Switzerland GmbH, and Wagner Group as key players in the market.
Customer pain points in the powder coating machine market include high initial investment costs, maintenance requirements, and the need for skilled operators. To address these challenges, manufacturers are developing cost-effective machines with user-friendly interfaces and automated features that reduce the need for manual intervention. Differentiation strategies such as offering customized solutions and value-added services like training and technical support have also helped companies strengthen their market position and cater to the diverse needs of their customers.
Key Factors to Consider When Choosing a Powder Coating Machine
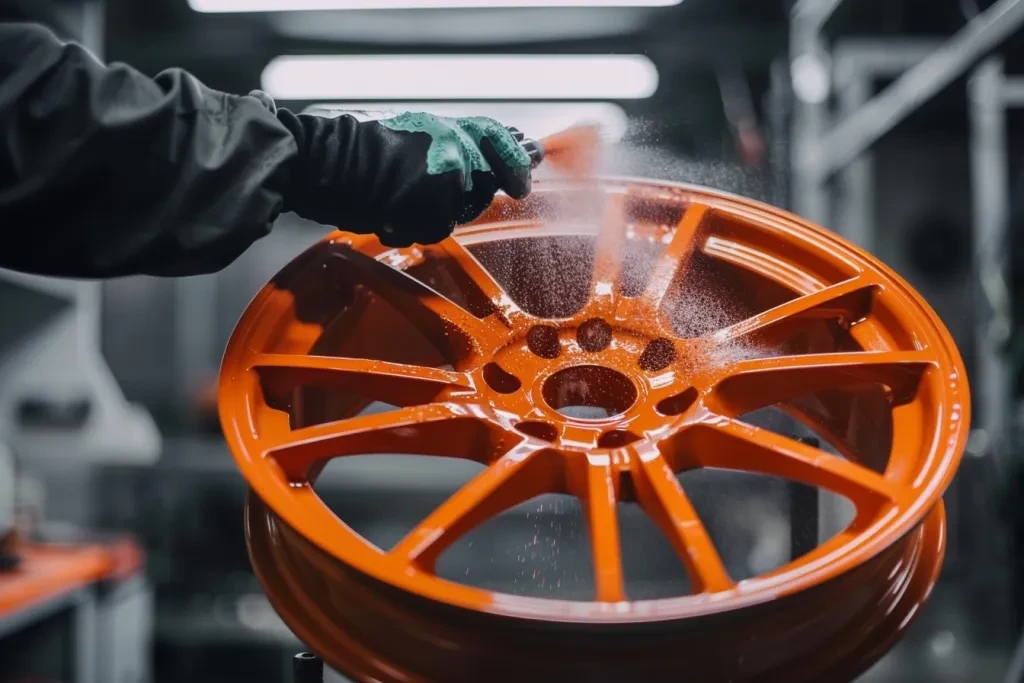
When selecting the ideal powder coating machine for your business, several critical factors must be considered to ensure optimal performance and efficiency. These factors range from the type of technology employed to the specific features of the machine. Below, we delve into these key considerations in detail.
Type of Coating Technology
There are primarily two types of powder coating technologies: electrostatic coating and fluidized bed coating. Each technology has its unique benefits and applications.
Electrostatic Coating involves charging paint droplets or coating powder particles and spraying them toward a part with an opposite electric charge. This method helps minimize overspray and waste, making it highly efficient. Within electrostatic coating, there are two subtypes: corona charging and tribostatic charging.
Corona Charging utilizes a high-voltage generator to produce a stream of ions, charging the powder cloud. This method is suitable for various applications due to its high efficiency in powder transport.
Tribostatic Charging charges the powder through friction with a non-conductive material. This method is particularly beneficial for achieving uniform coatings on complex shapes.
Fluidized Bed Coating suspends coating particles in a fluidized bed using air. Hot parts are inserted into the bed, allowing the powder to stick and fuse to the surfaces. This method is advantageous for applying thicker coatings and is often used for parts requiring robust protection.
Machine Features and Specifications
The features and specifications of a powder coating machine significantly impact its performance and suitability for specific applications. Key aspects to consider include:
Size and Capacity: The machine’s size and capacity should align with the volume of work and the size of the parts being coated. For high-volume production, machines with larger capacities and faster processing speeds are essential.
Portability: Portable powder coating machines are beneficial for on-site applications, allowing flexibility in various work environments. These machines typically include all necessary components such as spray guns, pressure tanks, hoses, and nozzles.
Energy Efficiency: Energy-efficient machines reduce operational costs and environmental impact. Look for machines with advanced energy management systems that optimize power usage during the coating process.
Material Compatibility
The compatibility of the powder coating machine with different coating materials is crucial. Powder coatings can be made from various materials, including thermosets, fluoropolymers, epoxies, and polyurethanes. Each material has distinct properties and suitability for different applications.
Thermoset Coatings cure through a chemical reaction, providing high resistance to heat and durability. They are ideal for applications requiring robust performance under extreme conditions.
Fluoropolymer Coatings are known for their excellent resistance to solvents, acids, and bases, making them suitable for harsh chemical environments.
Epoxy Coatings offer excellent adhesion and resistance to environmental degradation, making them suitable for protective applications.
Polyurethane Coatings are flexible and impact-resistant, often used for automotive and industrial applications.
Safety Standards and Certifications
Adherence to safety standards and certifications is paramount in ensuring the safe operation of powder coating machines. Machines should comply with relevant industry standards such as ISO, CE, and other local regulations. Safety features like automatic shut-off, pressure relief valves, and proper ventilation systems are essential to prevent accidents and ensure a safe working environment.
Initial Setup and Maintenance
The complexity of the initial setup and the ease of maintenance are critical factors in the long-term usability of powder coating machines.
Setup Complexity: Machines with straightforward setup procedures reduce downtime and allow quicker integration into production lines. Comprehensive user manuals and technical support from the manufacturer can facilitate the setup process.
Maintenance Requirements: Regular maintenance is necessary to ensure the longevity and optimal performance of the machine. Machines with easily accessible components and clear maintenance guidelines reduce the time and effort required for upkeep.
Advanced Features and Technological Innovations
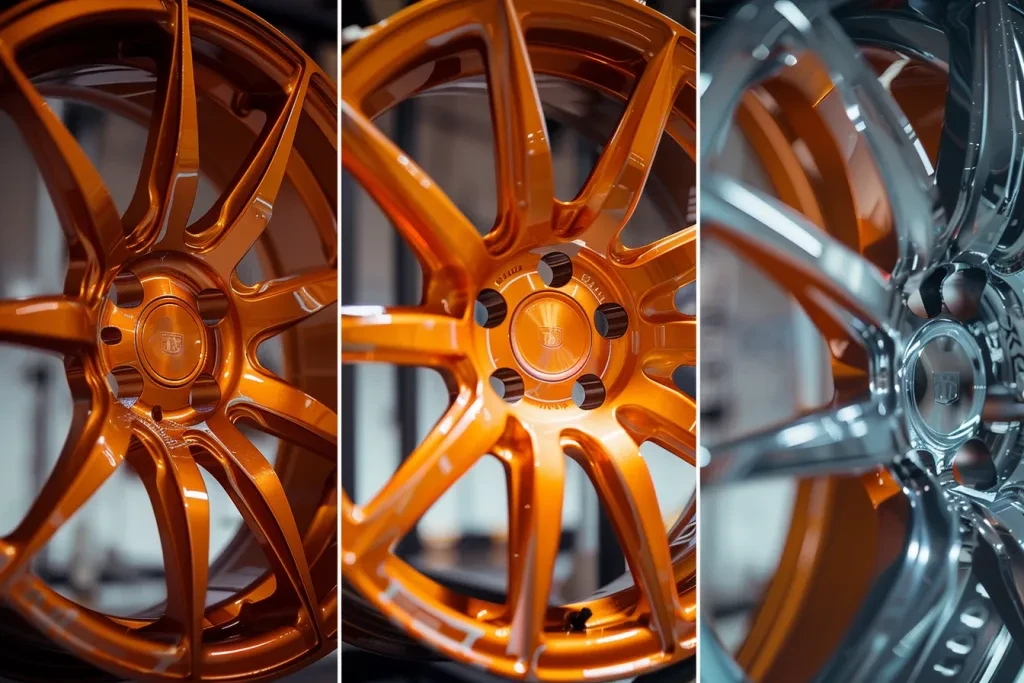
As technology advances, powder coating machines are equipped with innovative features that enhance their functionality and efficiency. These advancements include automation, smart controls, and improved spraying techniques.
Automation and Smart Controls: Modern powder coating machines often feature automation capabilities, allowing for precise control over the coating process. Automated systems can adjust parameters such as spray pressure, temperature, and coating thickness, ensuring consistent results. Smart controls with touchscreens and programmable settings enhance user convenience and operational efficiency.
Improved Spraying Techniques: Advances in spraying technology, such as high-velocity airless spraying and electrostatic rotary atomizers, improve coating uniformity and reduce material waste. These techniques are particularly beneficial for complex geometries and large surface areas.
Environmental Considerations: Eco-friendly powder coating machines minimize environmental impact through efficient material usage and reduced emissions. Features like closed-loop systems and advanced filtration ensure that excess powder is recycled, and air quality is maintained within the workspace.
Market Trends and Future Developments
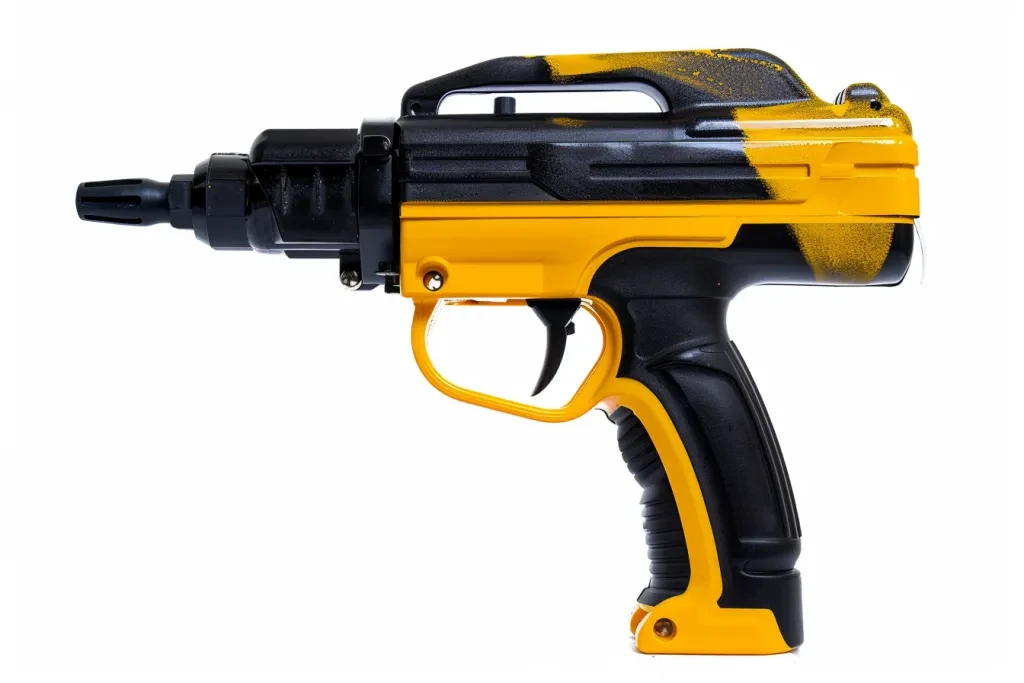
The powder coating industry is evolving, with emerging trends and future developments shaping the market landscape. Staying abreast of these trends can help businesses make informed decisions and stay competitive.
Sustainability and Green Coating Solutions: There is a growing emphasis on sustainable coating solutions that reduce environmental impact. Powder coating machines designed to minimize waste and energy consumption are gaining popularity. Additionally, the development of biodegradable and non-toxic powder materials is on the rise.
Integration with Industry 4.0: The integration of Industry 4.0 technologies, such as the Internet of Things (IoT) and artificial intelligence (AI), is revolutionizing powder coating processes. These technologies enable real-time monitoring, predictive maintenance, and data-driven decision-making, enhancing overall efficiency and productivity.
Customization and Flexibility: The demand for customized powder coating solutions is increasing. Machines that offer flexibility in terms of coating materials, colors, and finishes are becoming more sought after. This trend is driven by industries such as automotive, aerospace, and consumer goods, where unique and high-quality finishes are essential.
Summary and Final Thoughts
In conclusion, selecting the right powder coating machine involves evaluating various factors, including the type of coating technology, machine features, material compatibility, safety standards, and maintenance requirements. Advanced features and market trends also play a significant role in shaping the future of powder coating processes. By considering these aspects, businesses can make informed decisions that enhance their coating operations and achieve superior results.