In 2025, the wire feed welding market continues to grow, driven by technological advancements and increased automation. This article provides an in-depth analysis of the market, offering valuable assistance for professional buyers in selecting the right equipment to meet their business needs. Explore key factors, latest technologies, and industry trends that will help make informed purchasing decisions.
Table of Contents:
– Market Overview: Wire Feed Welding
– Detailed Introduction and Analysis of the Wire Feed Welding Market
– Key Factors When Selecting Wire Feed Welding Equipment
– Considerations for Wire Feed Welding
– Trends in Wire Feed Welding Technology
– Future Outlook for Wire Feed Welding
– Final Thoughts on Wire Feed Welding
Market Overview: Wire Feed Welding
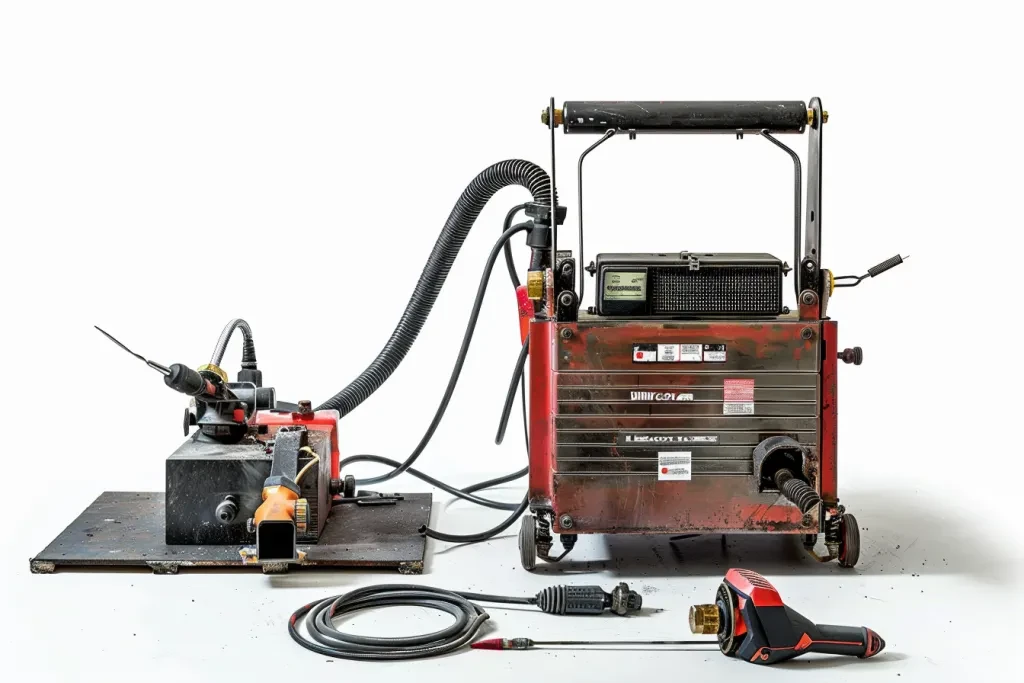
The wire feed welding market has seen substantial growth. The global electric welding machine market expanded from USD 5.52 billion in 2023 to USD 5.93 billion in 2024, and it is expected to reach USD 9.35 billion by 2030, with a compound annual growth rate (CAGR) of 7.81%. Wire feed welding, including Metal Inert Gas (MIG) welding machines, significantly contributes to this growth.
In 2023, the welding machinery market was worth USD 28.56 billion. It is projected to grow to USD 30.58 billion in 2024 and reach USD 47.52 billion by 2030, maintaining a CAGR of 7.54%. This growth is driven by increasing demand for precision welding in industries such as automotive, construction, and manufacturing. The market for welding equipment, accessories, and consumables is also rising, with an estimated size of USD 31.00 billion in 2023, expected to grow to USD 32.86 billion in 2024 and USD 47.15 billion by 2030, at a CAGR of 6.17%.
The Asia-Pacific region is a significant player in the wire feed welding market due to expansive infrastructure projects and a booming automotive industry. Innovations in technology and increased investments in regional research and development have produced high-efficiency and cost-effective welding solutions. The Americas and EMEA regions also contribute to market growth with robust industrial sectors and a strong emphasis on advanced welding technologies.
Detailed Introduction and Analysis of the Wire Feed Welding Market
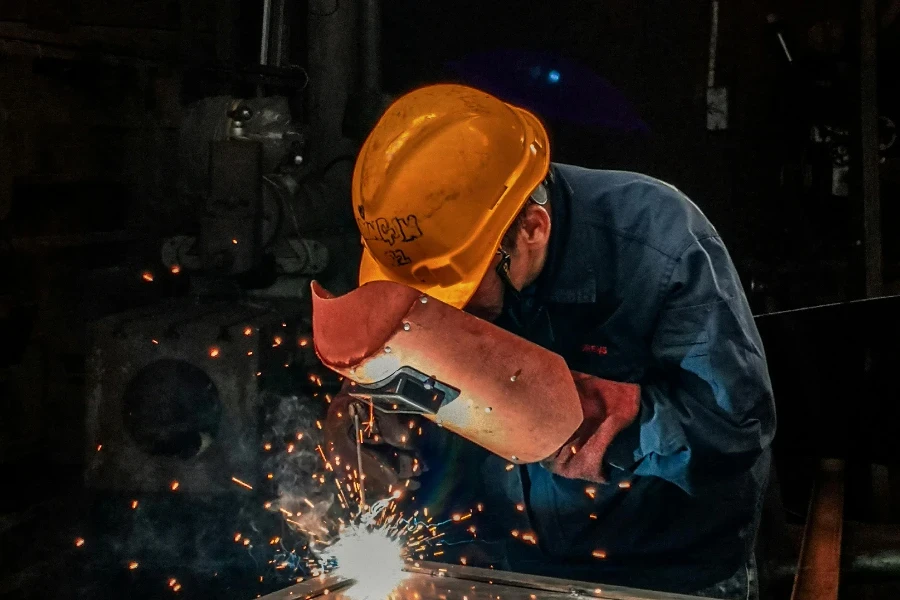
Wire feed welding, particularly MIG welding, is known for its versatility and efficiency in welding various metals. Key performance benchmarks include high deposition rates, excellent weld quality, and reduced welding time. MIG welding machines are in high demand due to their ease of use and ability to weld thin to medium-thickness metals, making them suitable for industries such as automotive and construction.
Economic factors such as global infrastructure expansion and the growing need for precision in welding advanced metals are significant market drivers. Consumer behavior has shifted towards adopting automated and semi-automated welding machines to improve efficiency and productivity. Distribution channels include both online and offline sales, with a growing trend towards digital platforms for purchasing welding equipment.
Recent innovations in wire feed welding include advanced auto-set controls, as seen in Miller’s Millermatic 142 MIG welder. These innovations simplify setup and usage, enhancing efficiency across various applications. Product lifecycle stages for wire feed welding machines range from introduction to maturity, with continuous technological improvements driving the market forward. Digitalization and automation are key trends, with manufacturers integrating smart technologies and robotics into welding processes.
Customer pain points include the high initial investment and ongoing maintenance costs of welding machines. Brand positioning strategies emphasize reliability, efficiency, and advanced technology to stand out in a competitive market. Niche markets such as aerospace and renewable energy sectors offer significant growth opportunities for wire feed welding machines, driven by the need for high-precision welding solutions.
The wire feed welding market is expected to continue growing, driven by technological advancements, increased automation, and expanding applications in various industries. The development of new welding techniques and materials, along with a focus on sustainability and energy efficiency, will shape the future of the wire feed welding market.
Key Factors When Selecting Wire Feed Welding Equipment
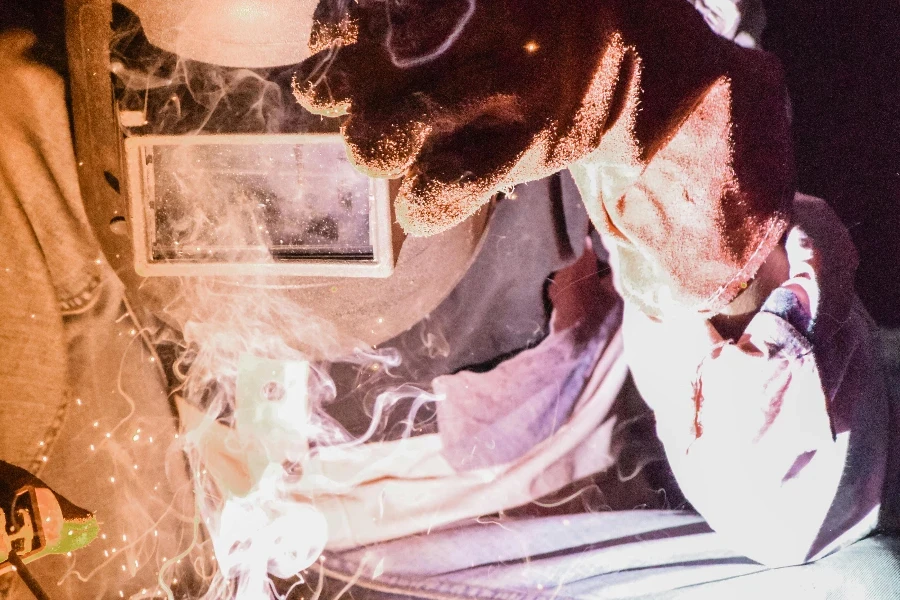
Choosing the right wire feed welding equipment is crucial for achieving optimal performance and efficiency in welding operations. Here are several key factors to consider:
Types of Wire Feed Welding
Wire feed welding encompasses various techniques, each suited for specific applications and materials. The most common types are Gas Metal Arc Welding (GMAW), Flux-Cored Arc Welding (FCAW), and Submerged Arc Welding (SAW). GMAW, often referred to as MIG welding, uses a continuous solid wire electrode fed through a welding gun, along with a shielding gas to protect the weld pool from contaminants. This method is versatile and suitable for welding thin to thick materials, including aluminum and steel.
FCAW is similar to GMAW but uses a tubular wire filled with flux. This method can be used with or without an external shielding gas, making it ideal for outdoor applications where wind might disperse the shielding gas. SAW involves a continuously fed wire electrode and a blanket of granular flux, which covers the weld pool, protecting it from atmospheric contamination and resulting in deep penetration and high deposition rates.
Performance and Functionality
Performance metrics such as duty cycle, amperage range, and wire feed speed are critical when selecting wire feed welding equipment. The duty cycle indicates the percentage of time a welder can operate at a given output without overheating. For high-production environments, a higher duty cycle is essential to maintain efficiency and reduce downtime.
The amperage range determines the thickness of materials that can be welded. A wider amperage range provides greater flexibility in handling various welding tasks. Wire feed speed, measured in inches per minute (IPM), affects the deposition rate and the overall quality of the weld. Adjustable wire feed speed allows for precise control over the welding process, ensuring consistent and high-quality welds.
Latest Technology Features
Modern wire feed welding machines incorporate advanced technologies to enhance performance and user experience. Digital controls and displays enable precise adjustments of welding parameters, improving accuracy and repeatability. Some machines feature synergic settings, which automatically adjust the wire feed speed and voltage based on the selected material and thickness, simplifying the setup process and reducing the likelihood of errors.
Many contemporary machines offer multi-process capabilities, allowing users to switch between different welding methods such as GMAW, FCAW, and SAW without changing equipment. This versatility is particularly beneficial in diverse welding environments where multiple processes are required.
Safety Standards and Certifications
Compliance with safety standards and certifications is paramount when selecting wire feed welding equipment. Equipment should meet or exceed industry standards set by organizations such as the American Welding Society (AWS) and the International Organization for Standardization (ISO). These standards ensure that the equipment is safe to use and performs reliably under various conditions.
Certifications such as CE (Conformité Européenne) mark, UL (Underwriters Laboratories) listing, and CSA (Canadian Standards Association) certification indicate that the equipment has been tested and approved for safety and quality. Ensuring that the welding equipment complies with these standards helps protect operators from potential hazards and ensures consistent performance.
Durability and Build Quality
The durability and build quality of wire feed welding equipment are critical for long-term performance and reliability. High-quality materials and robust construction ensure that the equipment can withstand the rigors of daily use in demanding environments. Features such as reinforced chassis, durable wire feeders, and heavy-duty power cables contribute to the overall longevity of the equipment.
Regular maintenance and proper handling can extend the lifespan of welding equipment. Some machines come with self-diagnostic features that alert users to potential issues before they become significant problems, helping to minimize downtime and maintenance costs.
Considerations for Wire Feed Welding
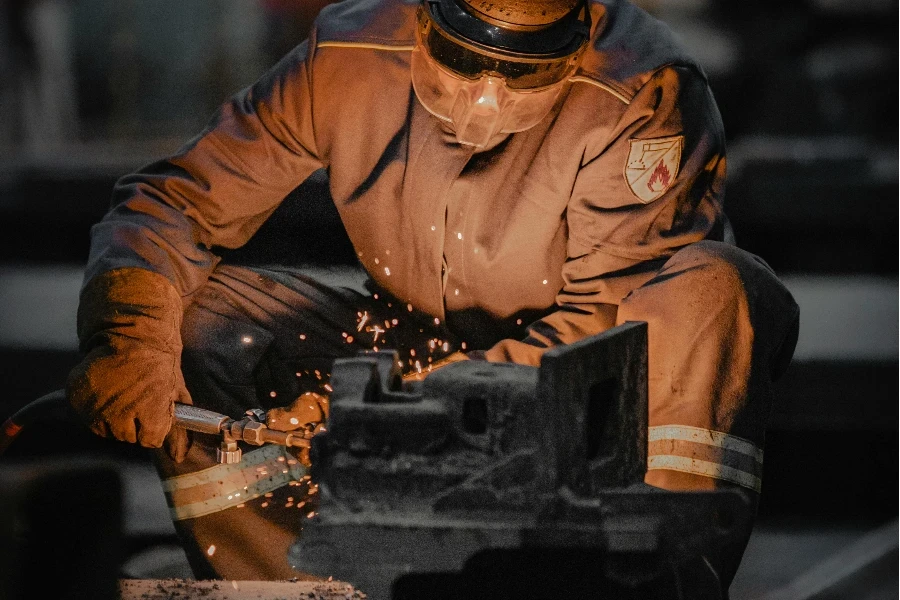
Material Compatibility
The compatibility of wire feed welding equipment with different materials is a crucial consideration. Various materials require specific welding parameters and techniques to achieve optimal results. For instance, welding aluminum necessitates the use of specialized wire and shielding gas to prevent oxidation and ensure a strong, clean weld. Similarly, stainless steel requires precise control over heat input to avoid warping and maintain the material’s corrosion resistance.
Choosing equipment that can easily adapt to different materials and thicknesses enhances versatility and reduces the need for multiple machines. Additionally, some modern welding machines offer pre-set programs for common materials, simplifying the setup process and ensuring consistent results.
Energy Efficiency
Energy efficiency is an important factor in reducing operational costs and minimizing environmental impact. Advanced wire feed welding machines are designed to optimize power consumption while maintaining high performance. Features such as inverter technology and power factor correction (PFC) improve energy efficiency by reducing power loss and ensuring stable output.
Energy-efficient machines not only lower electricity bills but also contribute to a greener welding operation. Selecting equipment with high energy efficiency ratings can provide long-term cost savings and support sustainability initiatives.
Ease of Use
The ease of use of wire feed welding equipment directly affects productivity and user satisfaction. Intuitive controls, clear displays, and ergonomic designs make it easier for operators to set up and use the equipment effectively. Machines with user-friendly interfaces reduce the learning curve, allowing operators to focus on producing high-quality welds rather than struggling with complex settings.
Features such as quick-change wire feeders, tool-less adjustments, and accessible maintenance points simplify routine tasks and reduce downtime. Equipment that is easy to use and maintain enhances overall efficiency and contributes to a safer working environment.
Trends in Wire Feed Welding Technology
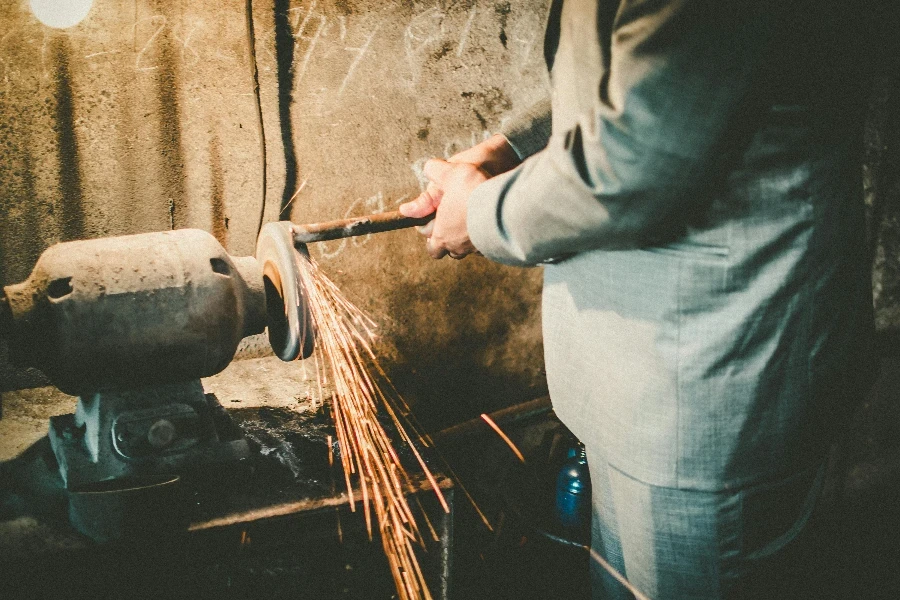
Automation and Robotics
Automation and robotics are transforming the wire feed welding industry, offering significant improvements in productivity, precision, and consistency. Automated welding systems use programmable logic controllers (PLCs) and robotic arms to perform repetitive welding tasks with high accuracy. These systems are ideal for high-volume production environments where consistency and speed are critical.
Robotic welding systems can be programmed to handle complex welding patterns and difficult-to-reach areas, reducing the need for manual intervention and minimizing the risk of human error. The integration of advanced sensors and artificial intelligence (AI) enables real-time monitoring and adjustments, further enhancing the quality and efficiency of the welding process.
Advanced Materials
The development of advanced materials is driving innovation in wire feed welding technology. New alloys and composites with enhanced properties such as increased strength, corrosion resistance, and lightweight characteristics are being used in various industries. Welding equipment manufacturers are responding to these trends by developing machines and consumables specifically designed to handle these advanced materials.
For example, high-strength steel and aluminum alloys used in the automotive and aerospace industries require precise control over welding parameters to achieve optimal results. Equipment that can accommodate these materials and provide consistent, high-quality welds is essential for meeting industry standards and performance requirements.
Digital Connectivity and IoT
The integration of digital connectivity and the Internet of Things (IoT) is revolutionizing wire feed welding by enabling remote monitoring, diagnostics, and control. Connected welding machines can transmit data to centralized systems, allowing operators to monitor performance, track usage, and identify potential issues in real-time. This data-driven approach enhances decision-making and supports predictive maintenance, reducing downtime and improving overall efficiency.
IoT-enabled welding systems can also facilitate remote support and troubleshooting, allowing technicians to diagnose and resolve issues without being physically present. This capability is particularly valuable in large-scale operations where minimizing downtime is critical.
Future Outlook for Wire Feed Welding
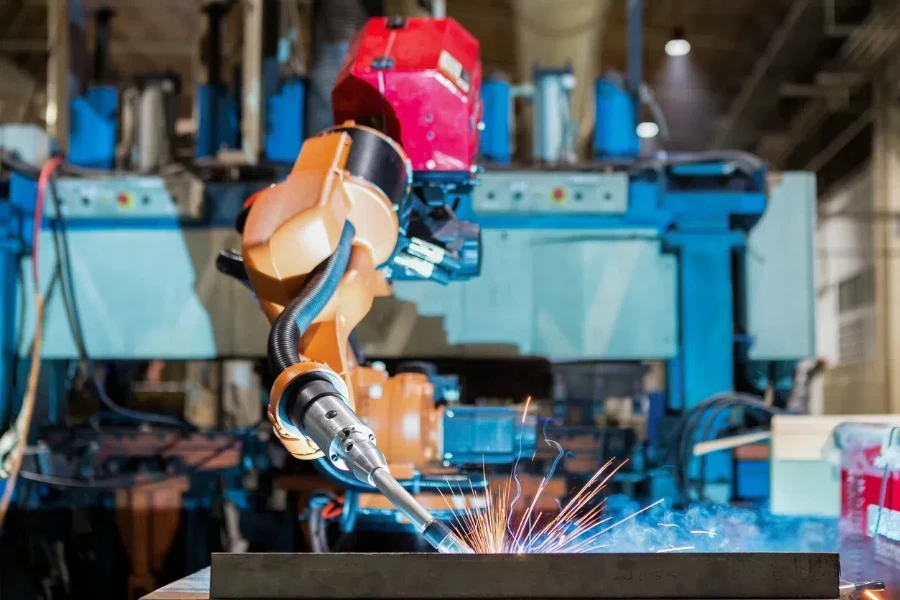
Increased Adoption of Automation
The trend towards automation in wire feed welding is expected to continue, with more industries adopting robotic welding systems to improve productivity and quality. The development of more affordable and user-friendly robotic solutions will make automation accessible to a broader range of businesses, including small and medium-sized enterprises (SMEs).
Advancements in Welding Consumables
Ongoing research and development in welding consumables, such as wires and shielding gases, will lead to improved performance and efficiency. New formulations that offer better arc stability, reduced spatter, and enhanced mechanical properties will contribute to higher-quality welds and greater process reliability.
Sustainability and Environmental Considerations
Sustainability and environmental considerations will play an increasingly important role in the wire feed welding industry. Manufacturers will focus on developing energy-efficient equipment and eco-friendly consumables to reduce the environmental impact of welding operations. Additionally, initiatives to recycle and repurpose welding materials will gain traction, supporting a circular economy.
Final Thoughts on Wire Feed Welding
Wire feed welding remains a versatile and efficient welding method, widely used across various industries. By carefully considering factors such as material compatibility, energy efficiency, ease of use, and the latest technology features, businesses can select the right equipment to meet their specific needs. As the industry continues to evolve with advancements in automation, materials, and digital connectivity, wire feed welding will continue to be a critical process in modern manufacturing and construction.