In 2025, the demand for dirt compactors is set to rise, driven by advancements in construction and mining industries. This article provides an in-depth analysis of the various types of dirt compactors, their applications, and the key features to consider when making a purchase. Professional buyers will find valuable insights to make informed decisions, ensuring they select the best equipment to meet their operational needs.
Table of Contents:
– Understanding the Demand and Applications of Dirt Compactors
– Types of Dirt Compactors and Their Specific Uses
– Key Features to Consider When Choosing a Dirt Compactor
– Evaluating the Total Cost of Ownership
– Trends and Innovations in Dirt Compactor Technology
– Making the Final Decision on the Right Dirt Compactor
Understanding the Demand and Applications of Dirt Compactors
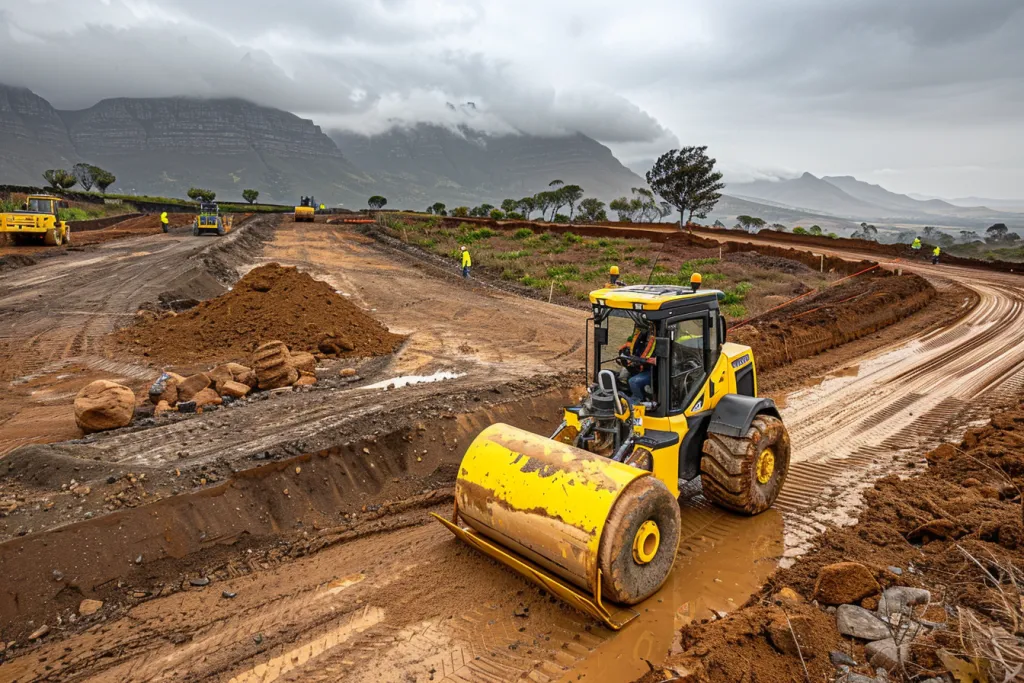
Key Industries Utilizing Dirt Compactors
Dirt compactors are essential in various industries, primarily in construction, mining, and waste management. In the construction sector, they are used to prepare foundations, ensuring soil stability and uniformity. The mining industry relies on dirt compactors to manage tailings and other waste materials, enhancing site safety and operational efficiency. Waste management facilities utilize these machines to compact landfill materials, optimizing space and reducing environmental impact.
The global construction industry, valued at USD 10.5 trillion in 2023, is projected to grow at a CAGR of 5.2% through 2028. This growth drives the demand for dirt compactors, particularly in infrastructure projects. In mining, the market for dirt compactors is bolstered by the increasing extraction activities, with the global mining equipment market expected to reach USD 150 billion by 2025. Waste management, another significant sector, is anticipated to grow due to rising urbanization and stringent environmental regulations.
Technological advancements in dirt compactors, such as GPS and IoT integration, are enhancing their efficiency and appeal across these industries. For instance, smart compactors equipped with real-time monitoring systems are becoming increasingly popular. These innovations not only improve operational efficiency but also ensure compliance with environmental standards, further driving market demand.
Geographic Regions with High Demand
North America and Asia-Pacific are the leading regions in the dirt compactor market, driven by extensive construction and mining activities. In North America, the United States dominates the market, with significant investments in infrastructure and urban development. The U.S. construction market alone was valued at USD 1.3 trillion in 2023, with a projected growth rate of 4.5% annually.
Asia-Pacific, particularly China and India, is experiencing rapid urbanization and industrialization, leading to increased demand for dirt compactors. China’s construction industry, valued at USD 2.5 trillion in 2023, is expected to grow at a CAGR of 6.1% through 2028. Similarly, India’s infrastructure development projects are driving the market, with the construction sector projected to grow at 7.1% annually.
Europe also presents a significant market for dirt compactors, driven by stringent environmental regulations and infrastructure modernization projects. Germany and the UK are key players, with the European construction market expected to reach USD 2.2 trillion by 2025. The adoption of advanced technologies and sustainable practices in these regions further propels the demand for efficient dirt compactors.
Market Growth Drivers
Several factors are driving the growth of the dirt compactor market, including increasing infrastructure development, urbanization, and technological advancements. The global push for sustainable construction practices and efficient waste management solutions is also a significant driver. Governments worldwide are investing heavily in infrastructure projects, with global infrastructure spending expected to reach USD 94 trillion by 2040.
Urbanization is another critical factor, with the global urban population projected to reach 6.7 billion by 2050. This rapid urban growth necessitates extensive construction and waste management efforts, boosting the demand for dirt compactors. Additionally, the integration of advanced technologies such as GPS, IoT, and AI in dirt compactors enhances their efficiency and appeal, driving market growth.
Environmental regulations and the need for sustainable practices are also influencing the market. Governments and organizations are increasingly focusing on reducing environmental impact, leading to the adoption of advanced, eco-friendly dirt compactors. These factors collectively contribute to the robust growth of the dirt compactor market, with a projected CAGR of 6.8% from 2023 to 2028.
Types of Dirt Compactors and Their Specific Uses
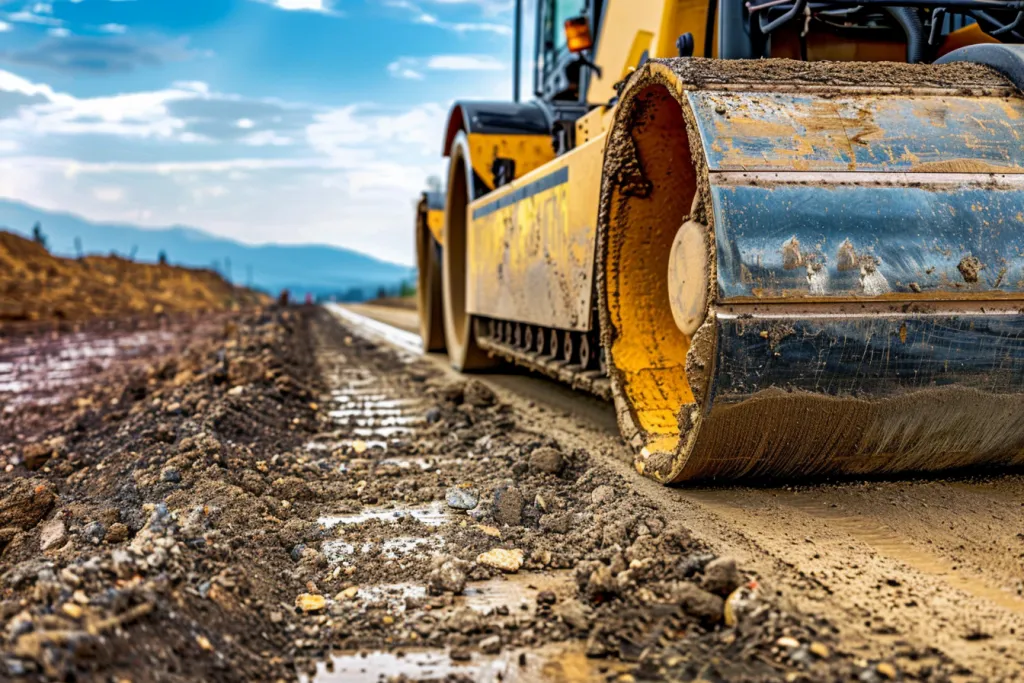
Vibratory Plate Compactors
Vibratory plate compactors are widely used in small to medium-sized construction projects, particularly for compacting granular soils and asphalt. These machines use a vibrating plate to create a downward force, effectively compacting the soil or asphalt beneath. They are ideal for tasks such as road repair, landscaping, and paving.
The market for vibratory plate compactors is driven by their versatility and efficiency in compacting various materials. In 2023, the global market for these compactors was valued at USD 1.2 billion, with a projected growth rate of 5.5% annually. Their ease of use and ability to deliver high compaction force make them a preferred choice for many construction projects.
Technological advancements, such as the integration of GPS and remote monitoring systems, are enhancing the functionality of vibratory plate compactors. These innovations allow for precise control and monitoring of compaction processes, improving efficiency and reducing operational costs. The adoption of these advanced features is expected to drive market growth further.
Jumping Jack Compactors
Jumping jack compactors, also known as rammers, are designed for compacting cohesive soils in confined areas. These machines use a high-impact force to compact soil, making them ideal for trench work, pipeline construction, and backfilling. Their ability to deliver powerful compaction in tight spaces makes them indispensable in certain construction applications.
The global market for jumping jack compactors was valued at USD 800 million in 2023, with a projected CAGR of 4.8% through 2028. The demand for these compactors is driven by their effectiveness in compacting cohesive soils and their suitability for use in confined spaces. Their robust design and high-impact force make them a preferred choice for many construction projects.
Recent advancements in jumping jack compactors include the development of lighter, more efficient models with enhanced safety features. These improvements not only increase the machines’ efficiency but also reduce operator fatigue and improve safety. The adoption of these advanced models is expected to drive market growth in the coming years.
Smooth Drum Rollers
Smooth drum rollers are primarily used for compacting granular soils, asphalt, and other materials in large-scale construction projects. These machines use a large, smooth drum to apply pressure and compact the material beneath. They are commonly used in road construction, airport runways, and large foundation projects.
The market for smooth drum rollers is driven by the increasing demand for infrastructure development and road construction projects. In 2023, the global market for these rollers was valued at USD 2.5 billion, with a projected growth rate of 6.2% annually. Their ability to deliver high compaction force and cover large areas quickly makes them essential for many construction projects.
Technological advancements, such as the integration of GPS and automated control systems, are enhancing the functionality of smooth drum rollers. These innovations allow for precise control and monitoring of compaction processes, improving efficiency and reducing operational costs. The adoption of these advanced features is expected to drive market growth further.
Padfoot Rollers
Padfoot rollers, also known as sheepsfoot rollers, are designed for compacting cohesive soils and clay. These machines use a drum with protruding pads to apply pressure and compact the soil beneath. They are ideal for tasks such as landfill compaction, road construction, and dam construction.
The global market for padfoot rollers was valued at USD 1.1 billion in 2023, with a projected CAGR of 5.7% through 2028. The demand for these rollers is driven by their effectiveness in compacting cohesive soils and their suitability for use in various construction applications. Their robust design and high compaction force make them a preferred choice for many projects.
Recent advancements in padfoot rollers include the development of models with enhanced safety features and improved fuel efficiency. These improvements not only increase the machines’ efficiency but also reduce operational costs and improve safety. The adoption of these advanced models is expected to drive market growth in the coming years.
Key Features to Consider When Choosing a Dirt Compactor
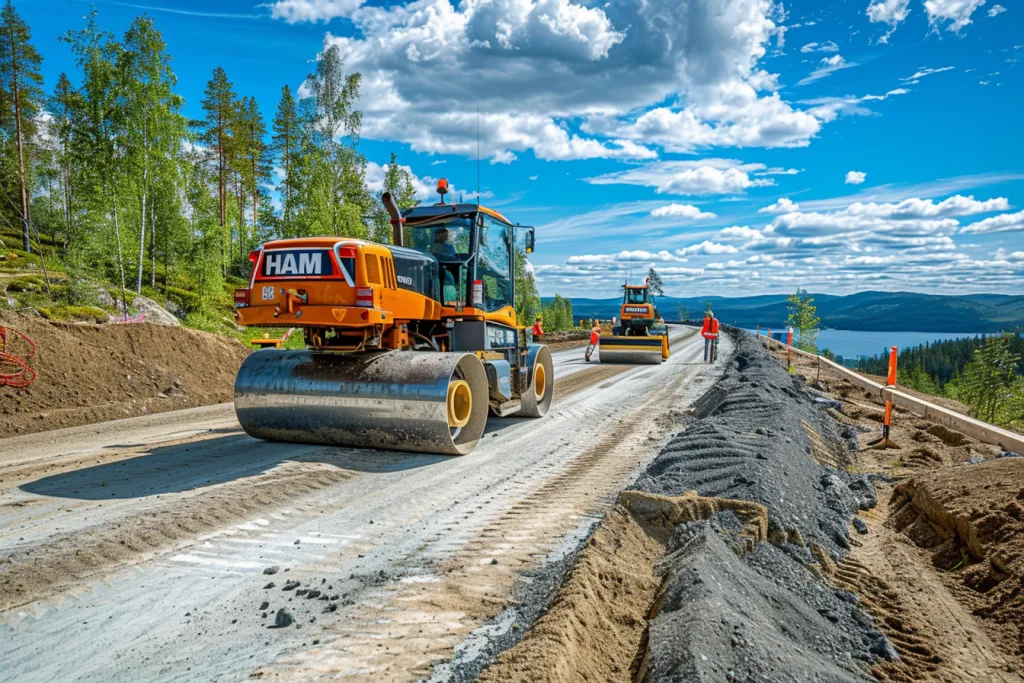
Compaction Force and Frequency
When selecting a dirt compactor, the compaction force and frequency are critical factors to consider. The compaction force determines the machine’s ability to compact soil effectively, while the frequency affects the speed and efficiency of the compaction process. For instance, vibratory plate compactors typically offer a compaction force of up to 5,000 pounds and a frequency of 4,000 vibrations per minute.
Higher compaction force and frequency are essential for projects requiring deep and thorough compaction, such as road construction and large foundation projects. In contrast, lower force and frequency may be sufficient for smaller tasks like landscaping and paving. Understanding the specific requirements of your project will help you choose a compactor with the appropriate force and frequency.
Technological advancements have led to the development of compactors with adjustable force and frequency settings. These features allow operators to customize the compaction process based on the material and project requirements, enhancing efficiency and effectiveness. The adoption of these advanced models is expected to drive market growth in the coming years.
Machine Size and Weight
The size and weight of a dirt compactor are crucial factors that influence its maneuverability and suitability for different projects. Smaller, lighter compactors are ideal for confined spaces and small-scale projects, while larger, heavier machines are better suited for extensive construction and mining operations. For example, jumping jack compactors typically weigh around 60-80 kg, making them suitable for trench work and backfilling.
Larger machines, such as smooth drum rollers, can weigh up to 20 tons, providing the necessary weight and force for large-scale projects like road construction and airport runways. The choice of machine size and weight should be based on the specific requirements of your project and the type of material being compacted.
Recent advancements in machine design have led to the development of compactors with enhanced maneuverability and weight distribution. These improvements allow for more efficient operation in various environments, reducing operator fatigue and improving overall productivity. The adoption of these advanced models is expected to drive market growth in the coming years.
Fuel Efficiency and Engine Power
Fuel efficiency and engine power are critical considerations when choosing a dirt compactor, as they directly impact operational costs and machine performance. Higher engine power provides the necessary force for effective compaction, while fuel efficiency ensures cost-effective operation. For instance, modern smooth drum rollers are equipped with engines delivering up to 200 horsepower, ensuring high performance and efficiency.
Fuel-efficient models are becoming increasingly popular due to rising fuel costs and environmental concerns. These machines are designed to optimize fuel consumption, reducing operational costs and minimizing environmental impact. The global market for fuel-efficient dirt compactors was valued at USD 1.8 billion in 2023, with a projected CAGR of 6.5% through 2028.
Technological advancements, such as hybrid and electric engines, are further enhancing the fuel efficiency and performance of dirt compactors. These innovations not only reduce fuel consumption but also lower emissions, aligning with global sustainability goals. The adoption of these advanced models is expected to drive market growth in the coming years.
Evaluating the Total Cost of Ownership
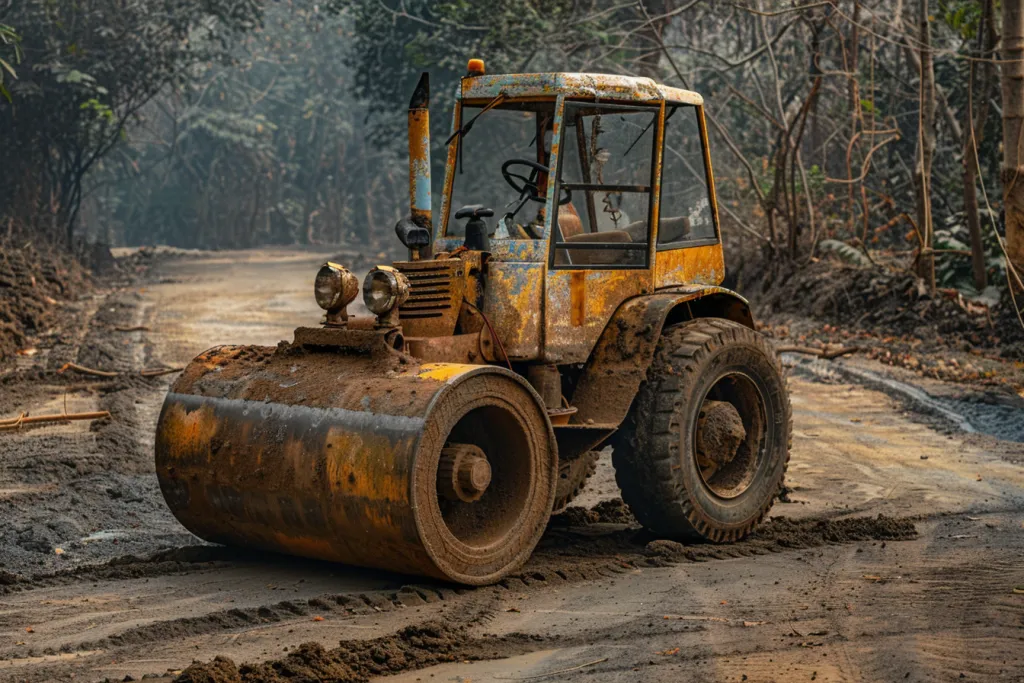
Initial Purchase Price
The initial purchase price of a dirt compactor is a significant factor in the total cost of ownership. High-end models with advanced features can cost upwards of $150,000, while basic models may start around $50,000. It’s essential to consider the specific needs of your operation to determine the appropriate investment level.
When evaluating the initial purchase price, consider the machine’s specifications, such as compaction force, operating weight, and engine power. For instance, a compactor with a higher compaction force and greater operating weight will typically be more expensive but may offer better performance and efficiency. Additionally, the brand and model reputation can influence the price, with well-known manufacturers often commanding higher prices due to their reliability and after-sales support.
Financing options can also impact the initial purchase price. Leasing or financing the equipment can spread the cost over several years, making it more manageable for businesses with limited upfront capital. However, it’s crucial to factor in interest rates and potential fees associated with financing to understand the true cost.
Maintenance and Repair Costs
Maintenance and repair costs are critical components of the total cost of ownership for dirt compactors. Regular maintenance, such as oil changes, filter replacements, and hydraulic system checks, is necessary to keep the machine running efficiently. These routine services can cost between $1,000 and $3,000 annually, depending on the machine’s usage and condition.
Unexpected repairs can significantly impact the total cost of ownership. For example, replacing a hydraulic pump can cost between $5,000 and $10,000, while engine repairs can range from $10,000 to $20,000. It’s essential to budget for these potential expenses and consider purchasing an extended warranty or service contract to mitigate the financial impact of major repairs.
The availability of spare parts and the expertise of service technicians also play a role in maintenance and repair costs. Machines from well-known manufacturers typically have better parts availability and a larger network of certified technicians, which can reduce downtime and repair costs. Conversely, lesser-known brands may have limited parts availability and fewer qualified technicians, leading to higher repair costs and longer downtimes.
Fuel and Operational Costs
Fuel and operational costs are ongoing expenses that contribute to the total cost of ownership for dirt compactors. Fuel consumption varies based on the machine’s engine size, operating conditions, and workload. On average, a dirt compactor can consume between 5 to 10 gallons of diesel per hour, with fuel costs ranging from $3 to $5 per gallon, depending on market conditions.
Operational costs also include labor expenses, as skilled operators are required to run the machinery efficiently. The average hourly wage for a heavy equipment operator in the United States is around $25 to $35, depending on experience and location. Additionally, training costs for operators should be considered, as proper training can improve efficiency and reduce the likelihood of accidents and equipment damage.
Other operational costs include insurance, which can range from $1,000 to $5,000 annually, depending on the machine’s value and the coverage level. It’s also essential to factor in the cost of consumables, such as lubricants, filters, and tires, which can add up over time. Properly maintaining and operating the machine can help minimize these costs and extend the equipment’s lifespan.
Resale Value
The resale value of a dirt compactor is an important consideration when evaluating the total cost of ownership. Well-maintained machines from reputable manufacturers tend to retain their value better than lesser-known brands. On average, a dirt compactor can retain 50% to 70% of its original value after five years, depending on its condition and market demand.
Factors that influence resale value include the machine’s age, hours of operation, maintenance history, and overall condition. Machines with lower hours and a documented maintenance history typically command higher resale prices. Additionally, models with advanced features and technology may have better resale value due to their increased demand in the market.
Market conditions also play a role in determining resale value. During periods of high construction activity, demand for used equipment may increase, leading to higher resale prices. Conversely, during economic downturns, the demand for used equipment may decrease, resulting in lower resale values. It’s essential to monitor market trends and plan the timing of equipment sales to maximize resale value.
Trends and Innovations in Dirt Compactor Technology
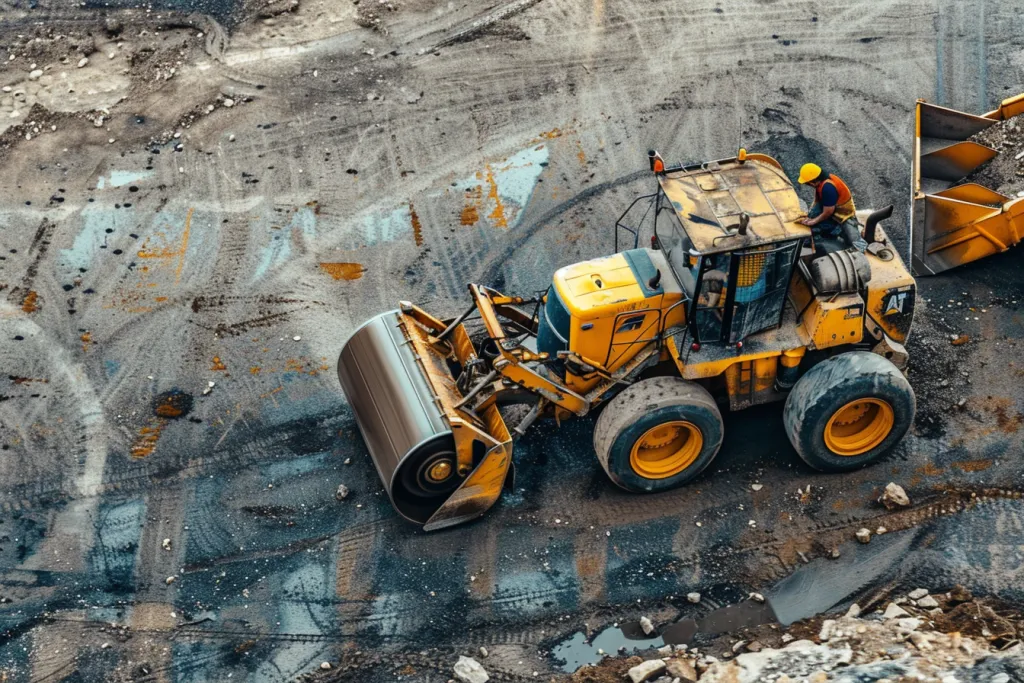
Advancements in Automation
Automation is revolutionizing the dirt compactor industry, with advancements aimed at improving efficiency and reducing operational costs. Autonomous compactors equipped with GPS and sensor technology can operate with minimal human intervention, ensuring precise compaction and reducing the risk of human error. These machines can follow pre-programmed routes and adjust their compaction force based on real-time data, resulting in consistent and high-quality compaction.
Telematics systems are another significant advancement in automation. These systems provide real-time data on machine performance, fuel consumption, and maintenance needs, allowing operators to monitor and optimize their fleet remotely. By analyzing this data, operators can identify inefficiencies, schedule preventive maintenance, and reduce downtime, ultimately lowering operational costs.
Integration with Building Information Modeling (BIM) is also becoming more common in the construction industry. BIM allows for the creation of detailed 3D models of construction sites, which can be used to plan and optimize compaction operations. By integrating dirt compactors with BIM, operators can ensure that compaction is performed accurately and efficiently, reducing the risk of over or under-compaction and improving overall project quality.
Eco-Friendly and Fuel-Efficient Models
The push for sustainability is driving the development of eco-friendly and fuel-efficient dirt compactors. Manufacturers are increasingly focusing on reducing the environmental impact of their machines by incorporating advanced engine technologies and alternative power sources. For example, hybrid compactors that combine diesel engines with electric motors can reduce fuel consumption and emissions by up to 30%, making them an attractive option for environmentally conscious operators.
Electric compactors are another emerging trend in the industry. These machines produce zero emissions and operate more quietly than their diesel counterparts, making them ideal for use in urban areas and environmentally sensitive sites. While the initial cost of electric compactors may be higher, the long-term savings in fuel and maintenance costs can offset the investment, making them a cost-effective and sustainable choice.
In addition to alternative power sources, manufacturers are also focusing on improving the fuel efficiency of traditional diesel compactors. Advanced engine technologies, such as turbocharging and electronic fuel injection, can enhance fuel efficiency by optimizing combustion and reducing energy loss. Additionally, features like automatic idle control and eco-mode can further reduce fuel consumption by adjusting engine speed based on workload, ensuring that the machine operates at peak efficiency.
Making the Final Decision on the Right Dirt Compactor
Choosing the right dirt compactor involves evaluating various factors, including the initial purchase price, maintenance and repair costs, fuel and operational costs, and resale value. It’s essential to consider the specific needs of your operation and the machine’s specifications to determine the best investment. Additionally, staying informed about the latest trends and innovations in dirt compactor technology can help you make a more informed decision and ensure that your equipment remains efficient and competitive in the long term.