As of 2024, the global electric welding machine market, including TIG welders, is projected to grow at a CAGR of 7.81%, reaching USD 9.35 billion by 2030. This growth is driven by the increasing demand for precision welding in various industries. For business buyers, selecting the right TIG welder is crucial to meet the specific needs of their customers and ensure high-quality welds.
Table of Contents:
– Understanding the Importance of TIG Welders in the Machinery Industry
– Key Factors to Consider When Choosing a TIG Welder
– Types of TIG Welders and Their Applications
– Emerging Trends in TIG Welding Technology
– Assessing the Total Cost of Ownership for TIG Welders
– Rounding up
Understanding the Importance of TIG Welders in the Machinery Industry
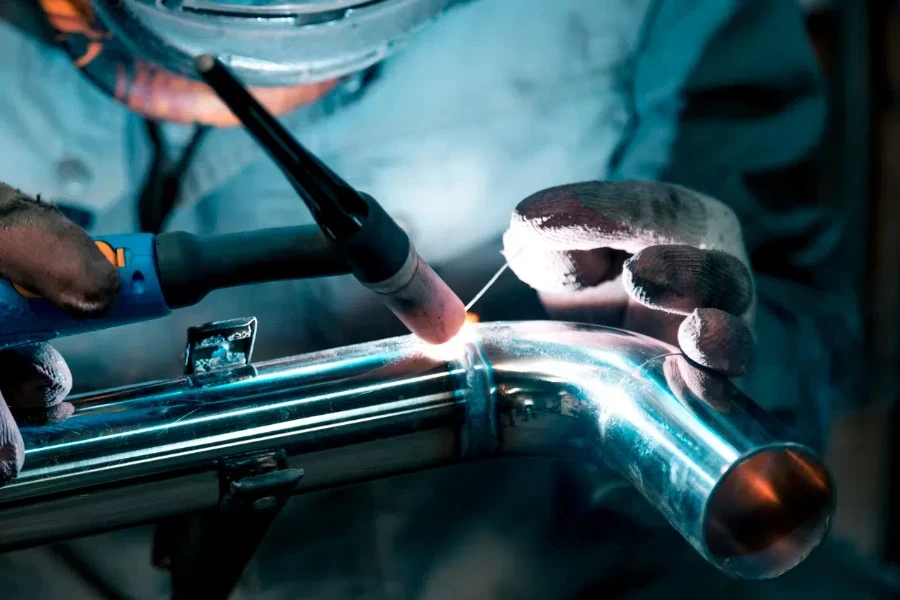
Key Applications of TIG Welding in Various Sectors
TIG welding, or Tungsten Inert Gas welding, is crucial in sectors requiring high precision and clean welds. In the aerospace industry, TIG welding is used extensively for its ability to produce high-quality, defect-free welds on thin materials. This precision is essential for the structural integrity of aircraft components. The automotive industry also relies heavily on TIG welding for assembling critical parts, such as exhaust systems and chassis components, where strength and durability are paramount.
In the medical device industry, TIG welding is indispensable due to its ability to create clean, contamination-free welds. This is vital for ensuring the safety and functionality of medical instruments and implants. Additionally, the food and beverage industry utilizes TIG welding for fabricating stainless steel equipment, which must meet stringent hygiene standards. The ability to produce smooth, crevice-free welds helps prevent bacterial growth, ensuring compliance with health regulations.
The construction sector benefits from TIG welding’s versatility in joining various metals, including aluminum and stainless steel. This capability is particularly useful in architectural applications where aesthetic quality and structural integrity are both critical. Moreover, TIG welding is employed in the manufacturing of pressure vessels and pipelines, where the quality of welds directly impacts safety and performance.
Growth and Demand for TIG Welders Globally
The global demand for TIG welders is on the rise, driven by the expansion of key industries and infrastructure projects. According to the latest market analysis, the electric welding machine market, which includes TIG welders, grew from USD 5.52 billion in 2023 to USD 5.93 billion in 2024. This growth is expected to continue at a compound annual growth rate (CAGR) of 7.81%, reaching USD 9.35 billion by 2030. This surge is attributed to the increasing need for precision welding in advanced manufacturing processes.
In the Asia-Pacific region, countries like China, India, and Japan are witnessing significant growth in the TIG welder market. This is fueled by large-scale infrastructure projects, a booming automotive industry, and a flourishing manufacturing sector. Innovations in welding technology and increased investments in regional research and development have led to the production of high-efficiency and cost-effective welding solutions, further driving market growth.
The Americas, particularly the United States, also represent a substantial market for TIG welders. The robust industrial sectors, including automotive, construction, and manufacturing, are key drivers of demand. The adoption of advanced welding technologies, such as automated and semi-automated systems, is enhancing efficiency and productivity, contributing to the market’s expansion. Additionally, infrastructure projects and energy sector developments in Canada and Brazil are fueling the demand for TIG welding equipment.
Key Factors to Consider When Choosing a TIG Welder
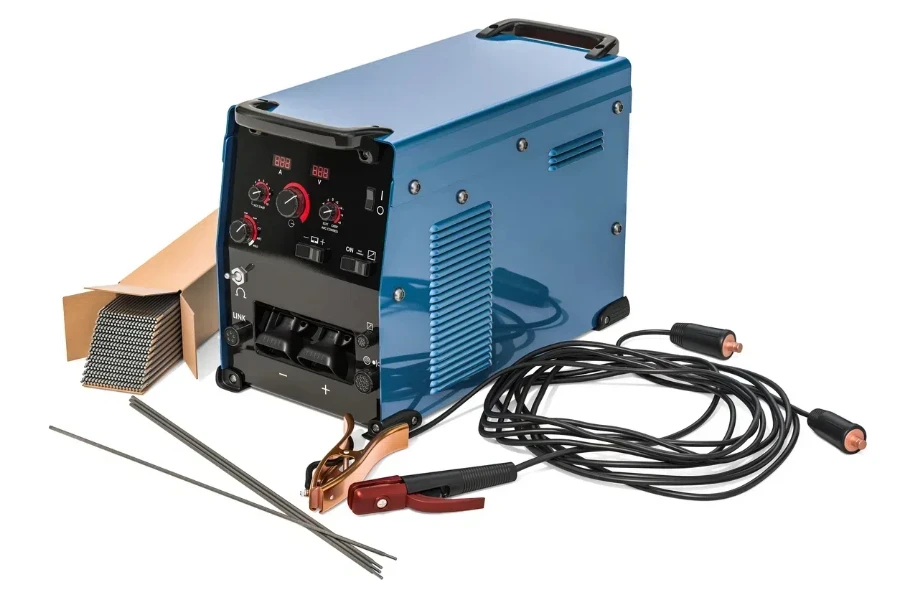
Power Output and Amperage Range
When selecting a TIG welder, power output and amperage range are critical factors to consider. The power output determines the welder’s capability to handle various thicknesses of materials. For instance, a welder with a higher amperage range can weld thicker materials, making it suitable for heavy-duty applications. Conversely, a lower amperage range is ideal for thin materials, ensuring precision and control.
The amperage range also affects the welder’s versatility. A wide amperage range allows the welder to be used for a broader range of applications, from delicate, thin materials to robust, thick metals. This flexibility is particularly beneficial in industries such as aerospace and automotive, where different components require varying welding specifications. Additionally, the ability to adjust the amperage precisely ensures optimal weld quality and reduces the risk of defects.
Furthermore, the power source type, whether AC or DC, plays a significant role in the welder’s performance. AC power is typically used for welding aluminum and magnesium, while DC power is preferred for welding steel and stainless steel. Understanding the specific requirements of the materials being welded is essential for choosing the appropriate power output and amperage range, ensuring efficient and high-quality welds.
AC/DC Capability and Its Benefits
The AC/DC capability of a TIG welder is a crucial feature that enhances its versatility and performance. AC (Alternating Current) is primarily used for welding non-ferrous metals like aluminum and magnesium. The alternating current helps break up the oxide layer on the surface of these metals, ensuring a clean and strong weld. This capability is essential for applications in the aerospace and automotive industries, where aluminum is commonly used.
DC (Direct Current), on the other hand, is used for welding ferrous metals such as steel and stainless steel. DC welding provides a stable arc and deeper penetration, making it ideal for thicker materials. The ability to switch between AC and DC modes allows welders to handle a wide range of materials and applications, increasing their utility in various industries. This flexibility is particularly beneficial in manufacturing and construction, where different projects may require welding different types of metals.
Moreover, the AC/DC capability enhances the welder’s efficiency and productivity. By using the appropriate current type for the material being welded, operators can achieve higher quality welds with fewer defects. This reduces the need for rework and increases overall productivity. Additionally, the ability to switch between AC and DC modes quickly and easily streamlines the welding process, saving time and effort.
Duty Cycle and Its Impact on Productivity
The duty cycle of a TIG welder is a critical factor that directly impacts productivity. The duty cycle refers to the amount of time a welder can operate continuously at a given amperage before needing to cool down. For example, a welder with a 60% duty cycle at 200 amps can weld continuously for 6 minutes out of a 10-minute period before requiring a 4-minute cooldown. A higher duty cycle allows for longer welding periods, increasing efficiency and reducing downtime.
In industrial applications, where large-scale welding projects are common, a high duty cycle is essential for maintaining productivity. Welders with a higher duty cycle can handle more extensive and demanding tasks without frequent interruptions. This is particularly important in sectors such as construction and manufacturing, where continuous welding is often required to meet project deadlines and maintain production schedules.
Additionally, the duty cycle affects the welder’s overall performance and longevity. Operating a welder beyond its duty cycle can lead to overheating and potential damage to the equipment. Therefore, choosing a welder with an appropriate duty cycle for the intended applications ensures reliable performance and extends the lifespan of the equipment. This consideration is crucial for businesses looking to maximize their return on investment and minimize maintenance costs.
Portability and Weight Considerations
Portability and weight are important factors to consider when choosing a TIG welder, especially for applications that require mobility. Lightweight and portable welders are ideal for fieldwork, repair jobs, and projects that involve moving between different locations. These welders are easier to transport and set up, making them convenient for on-site welding tasks in industries such as construction and maintenance.
The weight of the welder also affects its usability and ergonomics. Lighter welders are easier to handle and maneuver, reducing operator fatigue and improving overall efficiency. This is particularly beneficial for tasks that require prolonged welding or working in confined spaces. Additionally, portable welders often come with features such as carrying handles or wheels, further enhancing their mobility and ease of use.
However, it is important to balance portability with performance. While lightweight welders are convenient, they should still provide sufficient power and functionality for the intended applications. Ensuring that the welder meets the required specifications for power output, duty cycle, and other performance factors is essential for achieving high-quality welds and maintaining productivity. Therefore, businesses should carefully evaluate their specific needs and choose a welder that offers the right combination of portability and performance.
Control Features and User Interface
The control features and user interface of a TIG welder significantly impact its ease of use and precision. Advanced control features, such as pulse welding, allow operators to control the heat input and reduce the risk of warping or burning through thin materials. This is particularly useful in applications that require high precision, such as aerospace and medical device manufacturing. Additionally, features like pre-flow and post-flow gas control help protect the weld area from contamination, ensuring high-quality welds.
A user-friendly interface enhances the operator’s ability to adjust settings quickly and accurately. Digital displays and intuitive controls make it easier to set and monitor parameters such as amperage, voltage, and gas flow. This reduces the learning curve for new operators and increases overall efficiency. In industrial settings, where multiple welders may be used, a consistent and easy-to-use interface ensures that all operators can achieve the desired results with minimal training.
Moreover, programmable settings and memory functions allow operators to save and recall specific welding parameters for different applications. This feature is particularly beneficial in production environments where consistency and repeatability are crucial. By storing preferred settings, operators can quickly switch between different welding tasks without the need for manual adjustments, saving time and reducing the risk of errors. Overall, advanced control features and a user-friendly interface contribute to improved weld quality, efficiency, and operator satisfaction.
Safety Features and Compliance Standards
Safety features and compliance standards are paramount when choosing a TIG welder, as they ensure the protection of operators and adherence to industry regulations. Key safety features include thermal overload protection, which prevents the welder from overheating and reduces the risk of equipment damage and operator injury. Additionally, features like high-frequency start and arc stability help minimize the risk of accidental arc strikes and improve overall safety during operation.
Compliance with industry standards and certifications, such as CE, UL, and ISO, is essential for ensuring the welder meets safety and performance requirements. These standards provide assurance that the equipment has been tested and verified for safe operation under various conditions. In industries such as construction and manufacturing, where safety regulations are stringent, using certified equipment is crucial for maintaining compliance and avoiding potential legal and financial repercussions.
Furthermore, personal protective equipment (PPE) and safety accessories, such as welding helmets, gloves, and protective clothing, should be used in conjunction with the welder to enhance operator safety. Ensuring that the welder is compatible with these accessories and provides adequate protection against hazards such as UV radiation, sparks, and fumes is essential for creating a safe working environment. By prioritizing safety features and compliance standards, businesses can protect their workforce, reduce the risk of accidents, and maintain a safe and productive workplace.
Types of TIG Welders and Their Applications
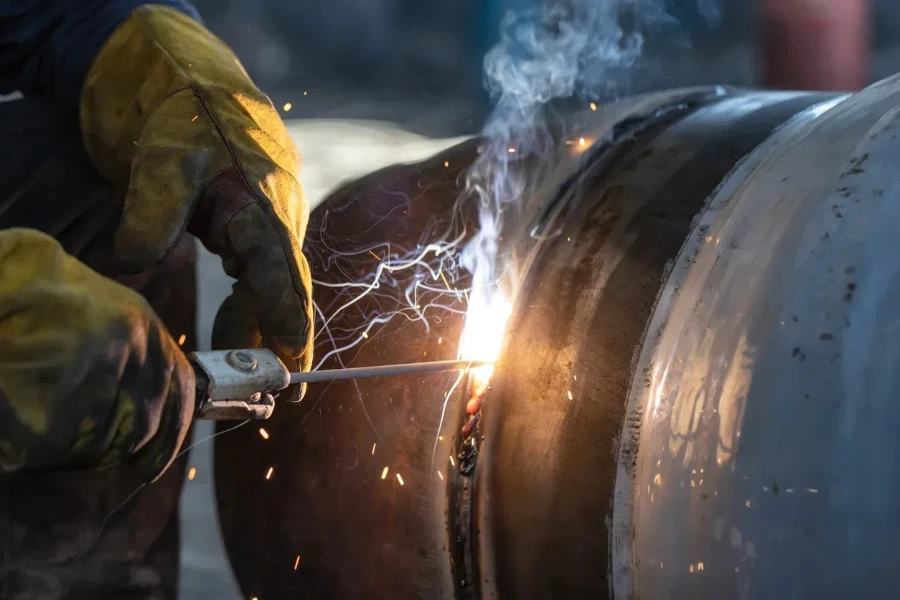
Inverter-Based TIG Welders
Inverter-based TIG welders are known for their efficiency and versatility. These welders use advanced electronic components to convert power more efficiently, resulting in a compact and lightweight design. This makes them ideal for applications that require portability, such as fieldwork and on-site repairs. Additionally, inverter-based welders offer precise control over welding parameters, allowing for high-quality welds on a variety of materials, including aluminum, stainless steel, and titanium.
The advanced technology used in inverter-based welders provides several benefits, including a higher duty cycle and improved arc stability. This allows for longer welding periods and consistent performance, making them suitable for industrial applications where productivity and reliability are critical. In sectors such as aerospace and automotive, where precision and quality are paramount, inverter-based TIG welders are preferred for their ability to produce clean and defect-free welds.
Moreover, inverter-based welders are energy-efficient, reducing power consumption and operating costs. This is particularly advantageous in large-scale manufacturing operations where energy savings can significantly impact the bottom line. The ability to operate on different power sources, including generators, further enhances their versatility and makes them suitable for use in remote locations. Overall, inverter-based TIG welders offer a combination of portability, precision, and efficiency, making them a valuable asset in various industries.
Transformer-Based TIG Welders
Transformer-based TIG welders are known for their durability and robustness. These welders use traditional transformer technology to convert power, resulting in a more substantial and heavier design compared to inverter-based welders. However, their simplicity and reliability make them ideal for heavy-duty applications and environments where ruggedness is essential. Industries such as shipbuilding, construction, and heavy manufacturing often prefer transformer-based welders for their ability to handle demanding tasks.
One of the key advantages of transformer-based welders is their ability to deliver consistent performance under challenging conditions. They are less sensitive to power fluctuations and can operate effectively in environments with unstable power supplies. This makes them suitable for use in remote locations and industrial settings where power quality may be an issue. Additionally, their robust construction ensures long-term reliability and reduces the need for frequent maintenance and repairs.
While transformer-based welders may lack some of the advanced features of inverter-based models, they offer excellent value for applications that require high power output and durability. Their ability to handle thick materials and provide deep penetration makes them ideal for welding structural components and heavy machinery. By choosing a transformer-based TIG welder, businesses can benefit from reliable performance and longevity, ensuring that their welding needs are met in even the most demanding environments.
Multi-Process Welders
Multi-process welders offer the versatility of performing various welding techniques, including TIG, MIG, and stick welding. This flexibility makes them an excellent choice for businesses that require different welding processes for various applications. Multi-process welders are particularly beneficial in industries such as automotive repair, fabrication, and maintenance, where different welding tasks may be needed on a single project. The ability to switch between processes quickly and easily enhances productivity and reduces the need for multiple machines.
The integration of multiple welding processes into a single machine also offers cost savings and space efficiency. Instead of investing in separate welders for each process, businesses can use a multi-process welder to handle a wide range of tasks. This reduces the initial investment and ongoing maintenance costs, making it a cost-effective solution for small to medium-sized enterprises. Additionally, the compact design of multi-process welders saves valuable workspace, which is particularly advantageous in workshops and manufacturing facilities with limited space.
Moreover, multi-process welders often come with advanced features and digital controls that enhance their usability and performance. Features such as automatic parameter adjustment, memory settings, and intuitive interfaces make it easier for operators to achieve consistent and high-quality welds. This is particularly important in production environments where efficiency and precision are critical. By investing in a multi-process welder, businesses can benefit from the versatility, cost savings, and advanced capabilities that these machines offer.
Emerging Trends in TIG Welding Technology
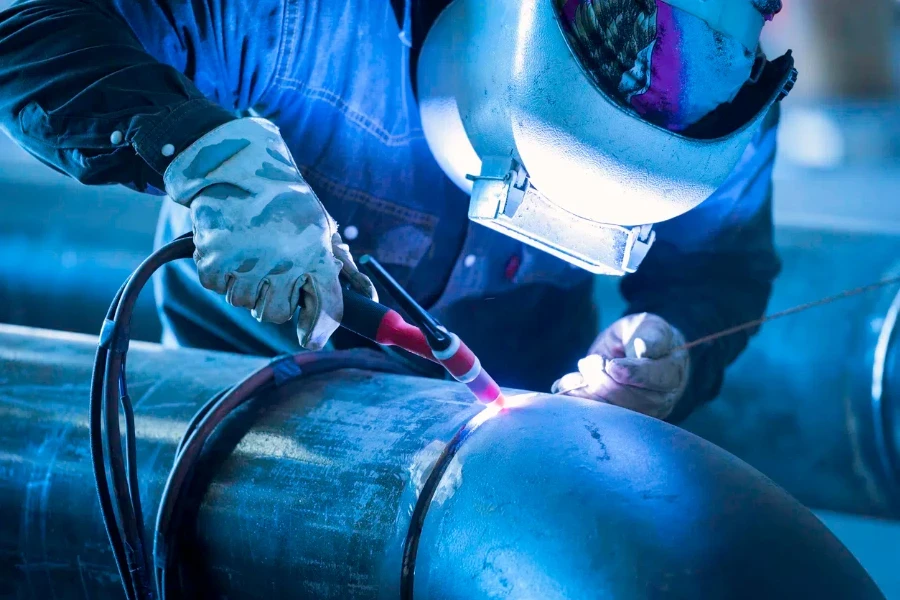
Automation and Robotics Integration
The integration of automation and robotics in TIG welding is a significant trend shaping the future of the industry. Automated welding systems and robotic welders offer increased precision, consistency, and efficiency, making them ideal for high-volume production environments. These systems can perform complex welding tasks with minimal human intervention, reducing the risk of errors and improving overall productivity. In industries such as automotive and aerospace, where precision and repeatability are crucial, the adoption of automated TIG welding systems is on the rise.
Robotic welding systems also enhance safety by reducing the need for operators to work in hazardous environments. By automating repetitive and dangerous tasks, businesses can protect their workforce and comply with stringent safety regulations. Additionally, the use of robotics in welding allows for greater flexibility in production processes, enabling manufacturers to adapt quickly to changing demands and market conditions. This trend is expected to continue as advancements in robotics and automation technology drive further improvements in welding efficiency and quality.
Advancements in Welding Materials and Consumables
Advancements in welding materials and consumables are driving improvements in TIG welding performance and efficiency. The development of new filler materials and electrodes with enhanced properties, such as increased strength and corrosion resistance, allows for better weld quality and durability. These advancements are particularly important in industries such as oil and gas, where welds are exposed to harsh environments and must withstand extreme conditions. The use of advanced materials ensures that welds maintain their integrity and performance over time.
Innovations in consumables, such as improved shielding gases and fluxes, also contribute to better weld quality and efficiency. These consumables help protect the weld area from contamination and improve arc stability, resulting in cleaner and stronger welds. Additionally, the development of eco-friendly and sustainable welding consumables aligns with the growing emphasis on environmental responsibility in manufacturing. By adopting advanced materials and consumables, businesses can achieve higher quality welds, reduce waste, and enhance their sustainability efforts.
Enhanced Precision and Control Systems
Enhanced precision and control systems are revolutionizing TIG welding technology, enabling operators to achieve higher levels of accuracy and consistency. Advanced control systems, such as digital interfaces and programmable settings, allow for precise adjustment of welding parameters, ensuring optimal performance for different materials and applications. These systems provide real-time feedback and monitoring, helping operators maintain consistent weld quality and reduce the risk of defects. In industries such as medical device manufacturing, where precision is critical, these advancements are particularly valuable.
The integration of smart technologies, such as artificial intelligence and machine learning, is further enhancing the capabilities of TIG welding systems. These technologies enable welders to learn from previous welds and optimize parameters automatically, improving efficiency and reducing the need for manual adjustments. Additionally, the use of sensors and data analytics allows for predictive maintenance and real-time monitoring of welding equipment, ensuring that potential issues are identified and addressed before they impact production. By leveraging enhanced precision and control systems, businesses can achieve higher quality welds, increase productivity, and reduce operational costs.
Assessing the Total Cost of Ownership for TIG Welders
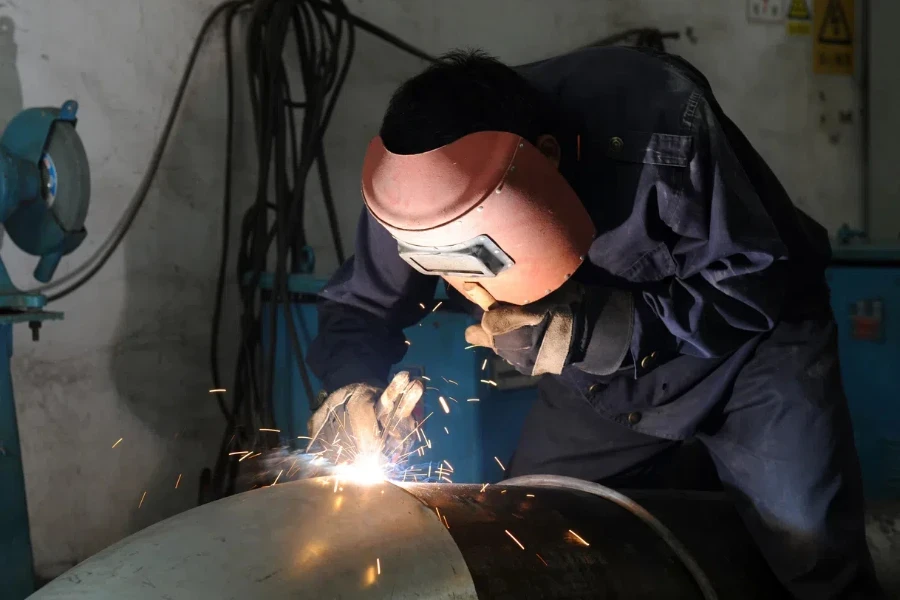
Initial Purchase Cost
The initial purchase cost of a TIG welder is a significant factor to consider when assessing the total cost of ownership. This cost includes the price of the welder itself, as well as any additional accessories and equipment required for operation. High-quality TIG welders with advanced features and capabilities may have a higher upfront cost, but they often provide better performance and durability. Investing in a reliable and efficient welder can result in long-term savings by reducing the need for frequent repairs and replacements.
When evaluating the initial purchase cost, it is important to consider the specific needs and requirements of the intended applications. For example, a welder with a higher duty cycle and power output may be necessary for industrial applications, while a more basic model may suffice for lighter tasks. Additionally, the cost of consumables, such as electrodes and shielding gases, should be factored into the overall budget. By carefully assessing the initial purchase cost and selecting a welder that meets the required specifications, businesses can ensure a cost-effective investment.
Operating and Maintenance Costs
Operating and maintenance costs are ongoing expenses that contribute to the total cost of ownership for a TIG welder. These costs include electricity consumption, consumables, and routine maintenance and repairs. Energy-efficient welders with advanced power management features can help reduce electricity costs, making them a more economical choice for long-term use. Additionally, the availability and cost of consumables, such as filler materials and shielding gases, should be considered when evaluating operating expenses.
Regular maintenance is essential for ensuring the longevity and performance of a TIG welder. This includes routine inspections, cleaning, and replacement of worn parts. The cost of maintenance can vary depending on the complexity and durability of the welder. Welders with robust construction and high-quality components may require less frequent maintenance, resulting in lower overall costs. Additionally, the availability of spare parts and technical support from the manufacturer can impact maintenance expenses. By choosing a welder with low operating and maintenance costs, businesses can minimize downtime and maximize productivity.
Energy Efficiency and Long-Term Savings
Energy efficiency is a critical factor in assessing the total cost of ownership for a TIG welder. Energy-efficient welders consume less power, resulting in lower electricity bills and reduced environmental impact. Inverter-based welders, for example, are known for their high energy efficiency and can provide significant long-term savings compared to traditional transformer-based models. Additionally, energy-efficient welders often have a higher duty cycle, allowing for longer welding periods and increased productivity.
Long-term savings can also be achieved through the use of advanced features and technologies that enhance performance and reduce waste. For example, welders with programmable settings and digital controls can optimize welding parameters for different applications, resulting in higher quality welds and reduced rework. The use of eco-friendly consumables and materials can further contribute to cost savings.
Rounding up
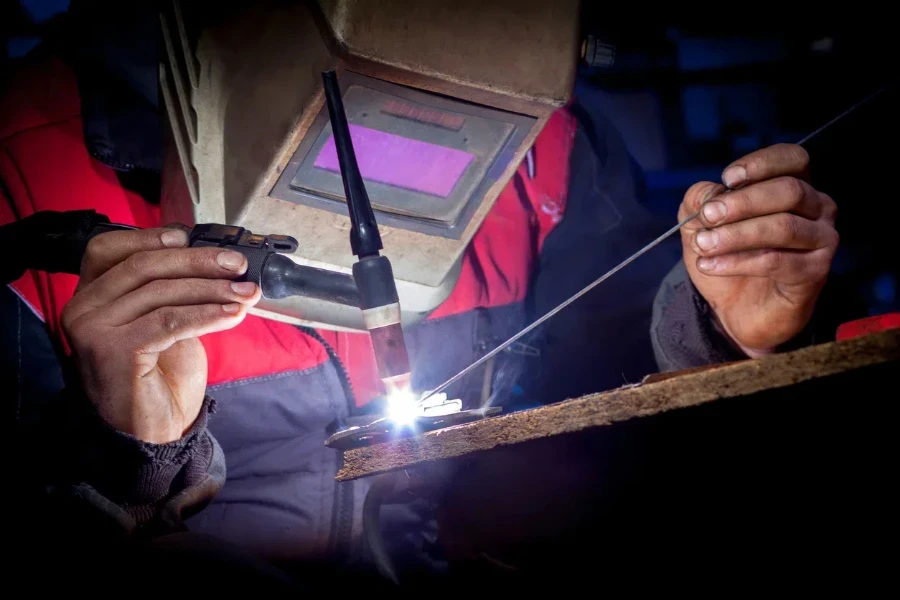
TIG welders are vital across industries requiring precision and quality. With rising global demand, factors like power output, AC/DC capability, and safety features are key in selecting the right welder. Innovations in automation and materials are enhancing performance, efficiency, and cost savings, making TIG welders a smart investment for businesses aiming for high-quality, productive welding.