The global market for protective clothing is projected to reach $16.1 billion by 2030, growing at a CAGR of 5.8%. This growth is driven by stringent regulatory requirements and increasing awareness of workplace safety. The machinery industry, in particular, faces numerous risks and hazards, making protective apparel essential for worker safety. This article delves into the critical role of protective apparel in the machinery industry, examining key statistics, regulatory requirements, and common risks.
Table of Contents:
– Key Statistics and Market Growth of Protective Apparel
– Types of Protective Apparel and Their Applications
– Factors to Consider When Selecting Protective Apparel
– Trends in Protective Apparel Technology
– Best Practices for Implementing Protective Apparel in the Workplace
– Making Informed Decisions for Optimal Safety and Performance
Key Statistics and Market Growth of Protective Apparel
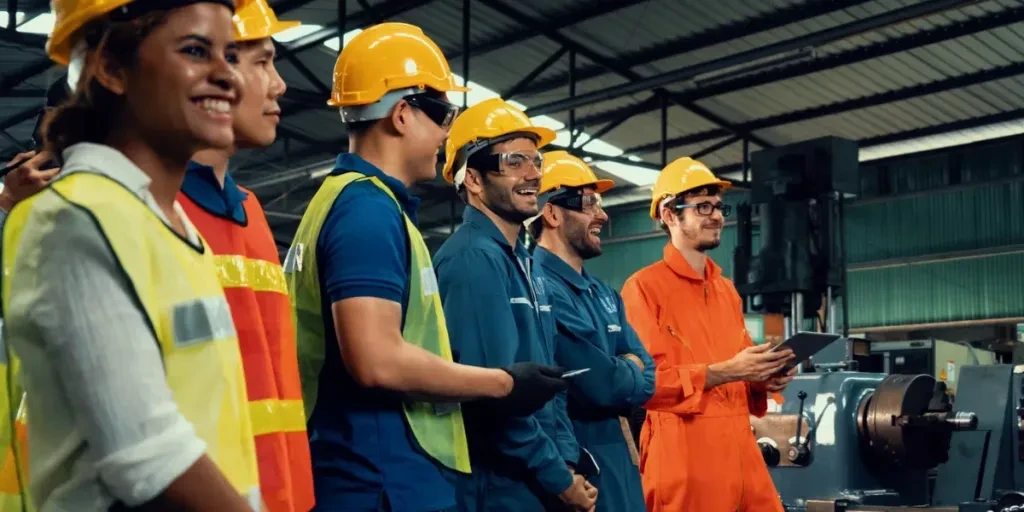
The global protective clothing market was worth $10.8 billion in 2023 and is expected to reach $16.1 billion by 2030. This represents a compound annual growth rate (CAGR) of 5.8%. The demand for protective clothing is driven by the need for safety in various industries, including machinery. The Aramid & Blends-based protective clothing segment is expected to grow at a CAGR of 6.0%, reaching $5.1 billion by 2030. Similarly, the Polyolefin & Blends-based segment is projected to grow at a CAGR of 5.5%.
In the U.S., the protective clothing market was estimated at $4.0 billion in 2023. China is forecasted to grow at an impressive 7.7% CAGR, reaching $2.2 billion by 2030. Other key regions, including Japan, Canada, Germany, and the Asia-Pacific, also show significant growth potential. The increasing adoption of protective clothing by small and medium enterprises (SMEs) is expanding the market reach.
Regulatory Requirements and Compliance
Stringent regulatory requirements are a major driver of the protective clothing market. In the machinery industry, compliance with safety standards is crucial to prevent workplace accidents. The Occupational Safety and Health Administration (OSHA) mandates the use of appropriate protective gear in various industrial settings. Similarly, the European Union enforces strict regulations to ensure worker safety across sectors.
Regulations are frequently updated to address new hazards and improve safety standards. For instance, the introduction of the ISO 45001 standard emphasizes the importance of occupational health and safety management systems. Compliance with these regulations not only ensures worker safety but also helps companies avoid legal liabilities and penalties.
Common Risks and Hazards in the Machinery Industry
The machinery industry is fraught with risks and hazards that necessitate the use of protective apparel. Common risks include exposure to chemicals, mechanical injuries, and thermal hazards. Workers are often at risk of cuts, abrasions, and punctures from sharp tools and machinery parts. Chemical spills and splashes pose significant health risks, necessitating the use of chemical-resistant clothing.
Thermal hazards, such as arc flashes and fires, require specialized protective gear to prevent burns and other injuries. The use of high-visibility clothing is essential in environments with heavy machinery to prevent accidents caused by poor visibility. Respiratory protection is also crucial in settings with airborne contaminants, such as dust and fumes.
Types of Protective Apparel and Their Applications
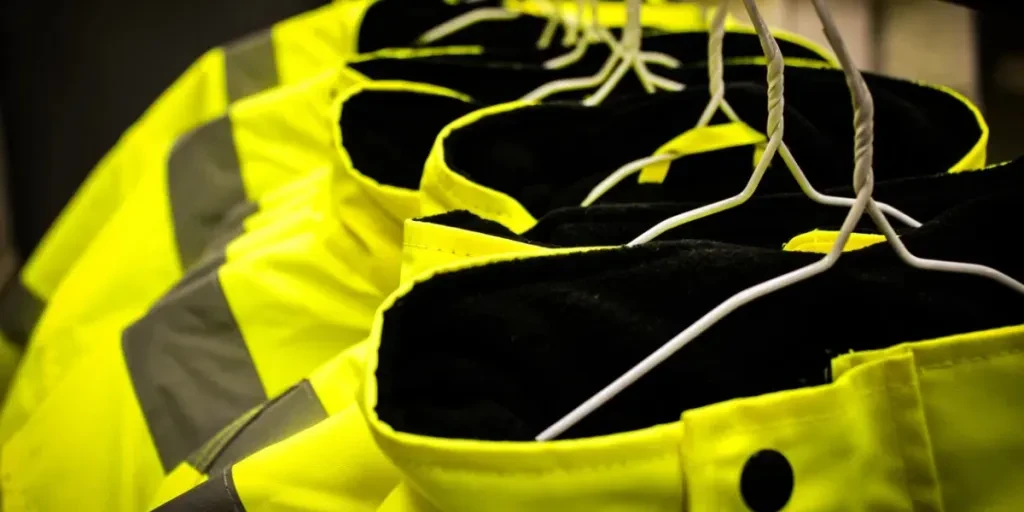
Protective Gloves
Protective gloves are essential in the machinery industry to prevent hand injuries. They are designed to protect against cuts, abrasions, and chemical exposure. The market for protective gloves is expected to grow significantly, driven by the increasing awareness of workplace safety. Gloves made from materials like nitrile, latex, and neoprene offer varying levels of protection based on the specific hazards present.
In 2022, Kimberly Clark Corporation introduced Kimtech Opal Nitrile Gloves, designed for use in research and manufacturing facilities. These gloves provide excellent chemical resistance and are suitable for handling hazardous materials. The demand for such specialized gloves is expected to rise as industries prioritize worker safety.
Safety Helmets
Safety helmets are crucial for protecting workers from head injuries caused by falling objects and collisions. The global market for safety helmets is driven by the construction, manufacturing, and machinery industries. Helmets are designed to absorb impact and provide a barrier against electrical hazards. Innovations in helmet design focus on improving comfort and durability while ensuring maximum protection.
In the machinery industry, safety helmets are often equipped with additional features such as face shields and ear protection. These enhancements provide comprehensive protection in hazardous environments. The adoption of smart helmets with integrated sensors for monitoring worker health and safety is an emerging trend in the market.
High-Visibility Clothing
High-visibility clothing is essential in environments with heavy machinery and low visibility. These garments are designed with reflective materials to ensure workers are easily seen, reducing the risk of accidents. The market for high-visibility clothing is expected to grow as industries prioritize worker safety and compliance with safety regulations.
In the construction and manufacturing sectors, high-visibility clothing is mandatory for workers operating near moving vehicles and machinery. The use of fluorescent colors and reflective strips enhances visibility in low-light conditions. The demand for high-visibility clothing is driven by the need to prevent accidents and improve overall workplace safety.
Respiratory Protection
Respiratory protection is critical in environments with airborne contaminants such as dust, fumes, and chemicals. Respirators and masks are designed to filter out harmful particles and provide clean air for breathing. The market for respiratory protection is driven by the increasing awareness of occupational health and safety.
In the machinery industry, workers are often exposed to hazardous substances that can cause respiratory issues. The use of advanced respirators with features like adjustable straps and replaceable filters ensures maximum protection and comfort. The demand for respiratory protection is expected to rise as industries adopt stricter safety standards.
Protective Footwear
Protective footwear is essential for preventing foot injuries caused by falling objects, sharp materials, and chemical spills. The market for protective footwear is driven by the need for safety in various industries, including machinery. Footwear designed with steel toes, puncture-resistant soles, and chemical-resistant materials offers comprehensive protection.
In the machinery industry, workers are at risk of injuries from heavy equipment and hazardous materials. The use of protective footwear ensures safety and compliance with safety regulations. Innovations in footwear design focus on improving comfort and durability while providing maximum protection. The demand for protective footwear is expected to grow as industries prioritize worker safety.
Factors to Consider When Selecting Protective Apparel
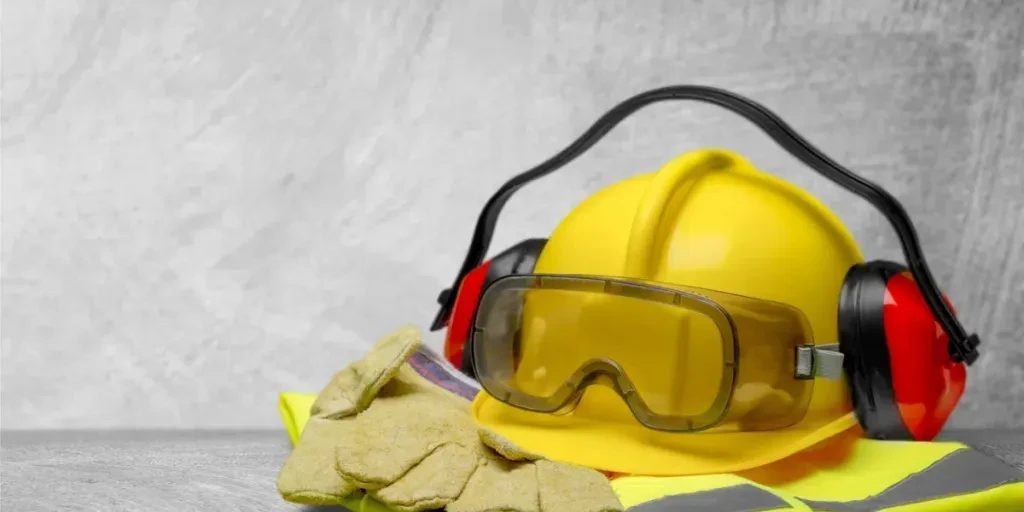
Material and Durability
When selecting protective apparel, the material is a critical factor. Materials such as Kevlar, Nomex, and high-density polyethylene (HDPE) are known for their durability and resistance to various hazards. Kevlar, for instance, is widely used in ballistic and puncture-resistant clothing due to its high tensile strength. Nomex, on the other hand, is preferred for its flame-resistant properties, making it ideal for firefighters and industrial workers exposed to high temperatures.
Durability is equally important as it determines the lifespan of the protective apparel. For example, leather, often used in welding jackets, offers excellent abrasion resistance and durability. However, it may dry out and become less effective over time. Similarly, materials like carbon fiber and aramid fibers are used in high-temperature environments due to their ability to withstand extreme conditions without degrading.
The choice of material also impacts the maintenance and replacement protocols. For instance, garments made from treated cotton may lose their flame-resistant properties after repeated washing. Therefore, understanding the material’s durability and maintenance requirements is essential for ensuring long-term protection and cost-effectiveness.
Comfort and Fit
Comfort and fit are crucial for the effectiveness of protective apparel. Ill-fitting garments can restrict movement, reduce productivity, and even pose additional safety risks. For instance, tight-fitting gloves may limit dexterity, while loose-fitting clothing can get caught in machinery. Therefore, selecting the right size and ensuring a proper fit is essential for both safety and comfort.
Breathability is another important aspect of comfort. Materials like cotton and certain synthetic blends offer better ventilation, making them suitable for hot and humid environments. Moisture-wicking fabrics are also beneficial as they help keep the wearer dry and comfortable during extended periods of use. For example, cooling PPE incorporates breathable fabrics to maintain comfort in warm environments.
Adjustability features such as Velcro straps, elastic bands, and adjustable neck straps can enhance the fit and comfort of protective apparel. These features allow for a customized fit, accommodating different body shapes and sizes. For instance, welding aprons with adjustable neck straps provide sufficient protection while ensuring comfort and ease of movement.
Certification and Standards
Compliance with certification and standards is a non-negotiable factor when selecting protective apparel. Various regulatory bodies, such as OSHA, ISO, and ASTM, set standards to ensure the safety and effectiveness of protective clothing. For example, ISO 11611 outlines specifications for welding apparel, ensuring it provides adequate protection against molten splatter and heat.
Standards also cover specific performance criteria such as puncture resistance, flame retardation, and chemical resistance. For instance, ASTM F1891 specifies requirements for arc and flame-resistant rainwear, ensuring it meets the necessary safety standards for electrical workers. Similarly, BS EN 1149-1 covers ESD protective clothing, essential for environments with sensitive electronic components.
Certification from recognized bodies not only ensures compliance with safety regulations but also provides assurance of the product’s quality and performance. Employers must verify that the protective apparel meets the relevant standards for their specific industry and application. This verification process often involves reviewing test reports and certification documents provided by the manufacturer.
Cost-Effectiveness
Cost-effectiveness is a significant consideration, especially for large-scale operations requiring bulk purchases of protective apparel. While high-quality materials and advanced features may come at a higher initial cost, they often offer better durability and longer service life, reducing the need for frequent replacements. For example, investing in high-quality Kevlar gloves may be more cost-effective in the long run compared to cheaper alternatives that wear out quickly.
Bulk purchasing and supplier negotiations can also impact cost-effectiveness. Establishing long-term relationships with reputable suppliers can lead to discounts and better pricing. Additionally, some suppliers offer maintenance and replacement services, further enhancing the cost-effectiveness of the protective apparel. For instance, suppliers may provide laundering services for flame-resistant clothing, ensuring it maintains its protective properties over time.
Employers should also consider the total cost of ownership, which includes not only the purchase price but also maintenance, replacement, and potential downtime costs. Conducting a cost-benefit analysis can help determine the most cost-effective options that do not compromise on safety and performance. For example, while disposable gloves may seem cheaper initially, reusable gloves with proper maintenance may offer better value over time.
Trends in Protective Apparel Technology
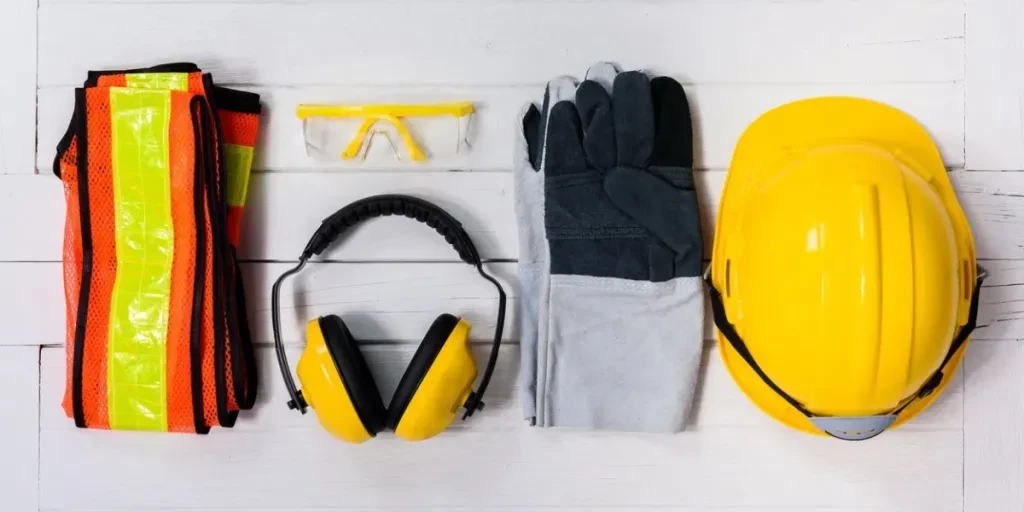
Innovations in Fabric Technology
Innovations in fabric technology are revolutionizing the protective apparel industry. Advanced materials such as graphene and nanofibers are being integrated into protective clothing to enhance their performance. Graphene, known for its exceptional strength and conductivity, is being used to create lightweight yet highly durable fabrics. These materials offer superior protection against cuts, abrasions, and even ballistic threats.
Smart textiles are another significant innovation, incorporating sensors and conductive fibers to monitor the wearer’s physiological conditions. These textiles can detect changes in temperature, heart rate, and even exposure to hazardous substances. For example, smart fabrics embedded with temperature sensors can alert workers to potential heat stress, allowing for timely intervention and prevention of heat-related illnesses.
The development of multi-functional fabrics is also gaining traction. These fabrics combine various protective properties, such as flame resistance, chemical resistance, and anti-static features, into a single garment. For instance, fabrics that integrate aramid fibers with chemical-resistant coatings provide comprehensive protection for workers in hazardous environments. This multi-functionality reduces the need for multiple layers of clothing, enhancing comfort and ease of movement.
Smart Protective Apparel
Smart protective apparel is an emerging trend that leverages technology to enhance safety and performance. Wearable technology, such as smart helmets and vests, is being integrated into protective clothing to provide real-time data and alerts. For example, smart helmets equipped with sensors can detect impacts and alert supervisors to potential head injuries, enabling prompt medical attention.
Augmented reality (AR) is also being incorporated into protective eyewear, providing workers with real-time information and guidance. AR-enabled glasses can display critical data, such as equipment status and safety protocols, directly in the wearer’s field of vision. This technology enhances situational awareness and reduces the risk of accidents by providing immediate access to essential information.
The use of IoT (Internet of Things) in protective apparel is another significant advancement. IoT-enabled garments can communicate with other devices and systems, creating a connected safety ecosystem. For instance, smart vests with GPS tracking can monitor the location of workers in hazardous areas, ensuring their safety and enabling efficient emergency response. These innovations are transforming protective apparel from passive safety gear to active safety solutions.
Sustainable and Eco-Friendly Options
Sustainability is becoming a key focus in the protective apparel industry. Manufacturers are increasingly adopting eco-friendly materials and production processes to reduce their environmental impact. Recycled and biodegradable materials are being used to create protective clothing, minimizing waste and promoting sustainability. For example, recycled polyester and organic cotton are being used to produce high-visibility vests and other protective garments.
Waterless dyeing and other sustainable manufacturing techniques are also being implemented to reduce water and chemical usage. These processes not only lower the environmental footprint but also improve the safety and quality of the protective apparel. For instance, waterless dyeing eliminates the need for harmful chemicals, resulting in safer and more durable fabrics.
The concept of a circular economy is gaining traction, with manufacturers designing protective apparel for recyclability and reuse. End-of-life recycling programs are being established to collect and recycle used protective clothing, reducing waste and conserving resources. For example, companies are developing take-back programs for used gloves and garments, ensuring they are recycled into new products rather than ending up in landfills.
Best Practices for Implementing Protective Apparel in the Workplace
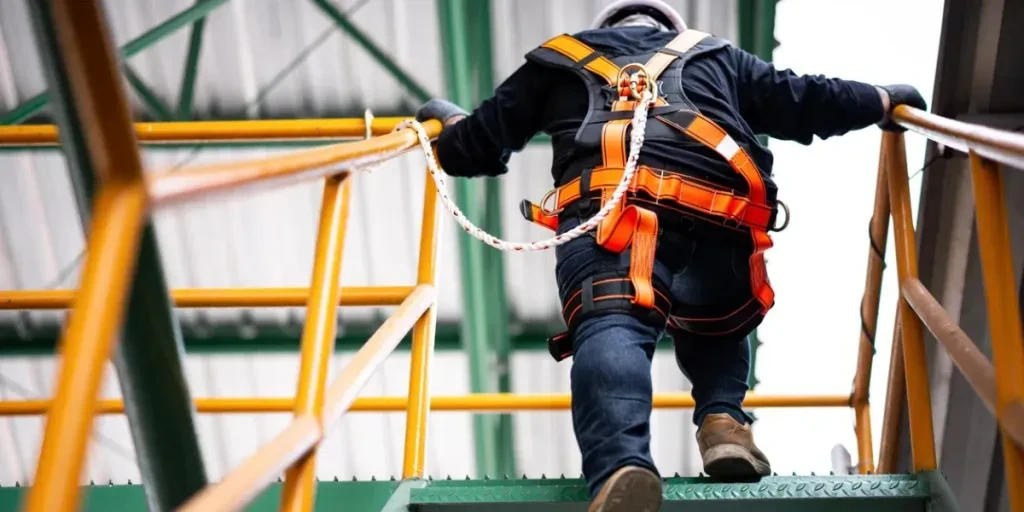
Conducting Risk Assessments
Conducting thorough risk assessments is the first step in implementing protective apparel in the workplace. Risk assessments help identify potential hazards and determine the appropriate level of protection required. For example, a chemical plant may require different protective clothing compared to a construction site. By understanding the specific risks, employers can select the most suitable protective apparel for their workers.
Risk assessments should be conducted regularly and updated to reflect any changes in the work environment or processes. This ensures that the protective apparel remains effective and relevant. For instance, introducing new machinery or chemicals may necessitate a reassessment of the existing protective clothing. Regular assessments also help identify any gaps in protection and allow for timely interventions.
Involving employees in the risk assessment process can provide valuable insights and enhance the effectiveness of the protective measures. Workers are often the best source of information regarding the hazards they face and the practicality of the protective apparel. For example, feedback from welders can help identify specific areas where additional protection or comfort features are needed in welding jackets.
Training and Education for Employees
Training and education are essential for the effective use of protective apparel. Employees must be trained on the proper use, maintenance, and limitations of the protective clothing. For example, workers should know how to correctly don and doff protective suits to avoid contamination. Training should also cover the importance of regular inspections and the signs of wear and tear that indicate the need for replacement.
Ongoing education programs can help reinforce the importance of using protective apparel and keeping up with any changes in safety protocols. For instance, regular safety meetings and refresher courses can ensure that employees remain aware of the latest safety standards and best practices. These programs can also address any misconceptions or resistance to wearing protective clothing.
Employers should also provide clear and accessible information on the protective apparel, including user manuals and safety data sheets. This information should be readily available to all employees and include details on the proper care and maintenance of the protective clothing. For example, providing guidelines on the correct laundering procedures for flame-resistant garments can help maintain their protective properties.
Maintenance and Replacement Protocols
Establishing maintenance and replacement protocols is crucial for ensuring the ongoing effectiveness of protective apparel. Regular inspections should be conducted to identify any signs of damage or wear. For example, checking for tears, abrasions, or chemical degradation in gloves can prevent potential exposure to hazards. Inspections should be documented, and any damaged items should be replaced immediately.
Proper maintenance procedures should be followed to extend the lifespan of the protective apparel. This includes adhering to the manufacturer’s guidelines for cleaning and storage. For instance, flame-resistant clothing should be laundered using specific detergents to maintain its protective properties. Proper storage, such as keeping garments in a cool, dry place, can also prevent damage and degradation.
Replacement protocols should be based on the specific usage and wear patterns of the protective apparel. For example, high-use items like gloves may need to be replaced more frequently than less-used items like aprons. Employers should establish a schedule for regular replacement and ensure that adequate stock is available to avoid any gaps in protection. By implementing these protocols, employers can ensure that their workers are always equipped with effective and reliable protective apparel.
Making Informed Decisions for Optimal Safety and Performance
Making informed decisions about protective apparel is essential for ensuring optimal safety and performance in the workplace. By considering factors such as material durability, comfort, certification, and cost-effectiveness, employers can select the most suitable protective clothing for their specific needs. Staying updated on the latest trends and innovations in protective apparel technology can further enhance safety and efficiency.