As of 2024, the global demand for aluminum TIG welders is surging, driven by advancements in lightweight, corrosion-resistant materials. With the Basic Metals market projected to reach a staggering US$4.0 trillion, business buyers are keen to capitalize on this growth.
Understanding the latest trends and innovations in aluminum TIG welding is crucial for wholesalers, retailers, and purchasing professionals aiming to optimize their product selection and meet the evolving needs of industries like aerospace and automotive.
Table of Contents:
Aluminum TIG Welder Market Overview
Detailed Analysis of the Aluminum TIG Welder Market
Trends and Innovations in Aluminum TIG Welder Market
Key Factors When Selecting an Aluminum TIG Welder
Understanding the Role of Safety Standards and Certifications
Exploring the Latest Technological Innovations in TIG Welding
Wrapping Up
Aluminum TIG Welder Market Overview
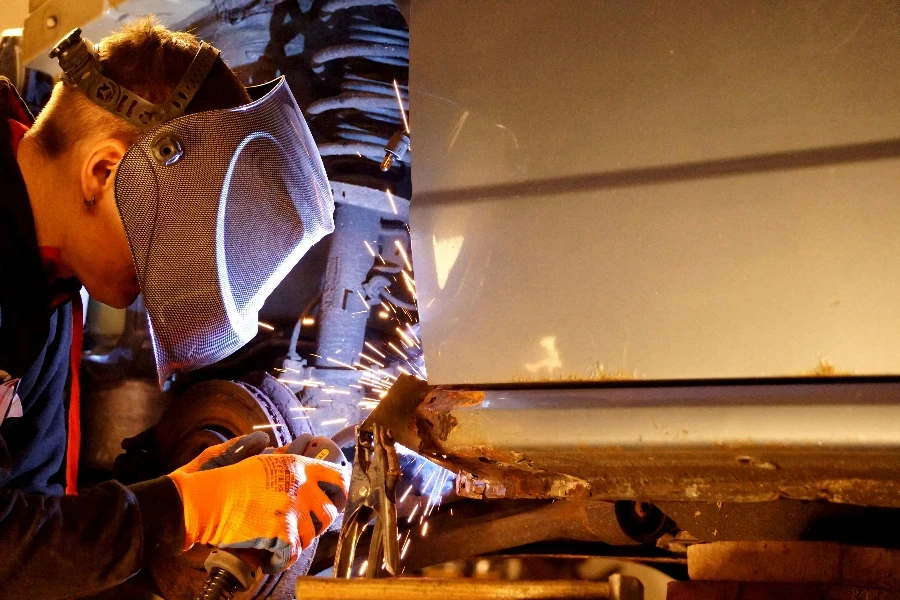
The Aluminum TIG Welder market, a key segment of the Basic Metals and Fabricated Metals industries, is experiencing notable growth. By 2024, the Basic Metals market is expected to achieve a global value added of US$0.5 trillion, with a compound annual growth rate (CAGR) of 1.30% from 2024 to 2029. The sector’s output is projected to reach US$4.0 trillion in 2024, reflecting a CAGR of 1.22% over the same period. In the United States, the Fabricated Metals market, which includes aluminum welding equipment, is anticipated to reach a value added of US$211.3 billion in 2024, growing at a CAGR of 1.26% from 2024 to 2029.
The employment scenario in these markets is also significant. The global Basic Metals market is expected to employ 8.84 million people in 2024, with a CAGR of 1.90% from 2024 to 2029. In the U.S., the Fabricated Metals market will employ about 1.40 million people in 2024, with a projected CAGR of 1.25% over the next five years. These figures highlight the substantial human resource investment and the critical role of skilled labor in the aluminum TIG welding sector.
The aluminum TIG welder market is noted for its high labor productivity and efficiency. Labor productivity in the Basic Metals market is projected to be US$50.4k per employee in 2024, while the U.S. boasts a higher figure of US$150.9k in the Fabricated Metals market. This difference underscores the advanced manufacturing technologies and practices in the U.S., which are essential for enhancing welding precision and efficiency.
Detailed Analysis of the Aluminum TIG Welder Market
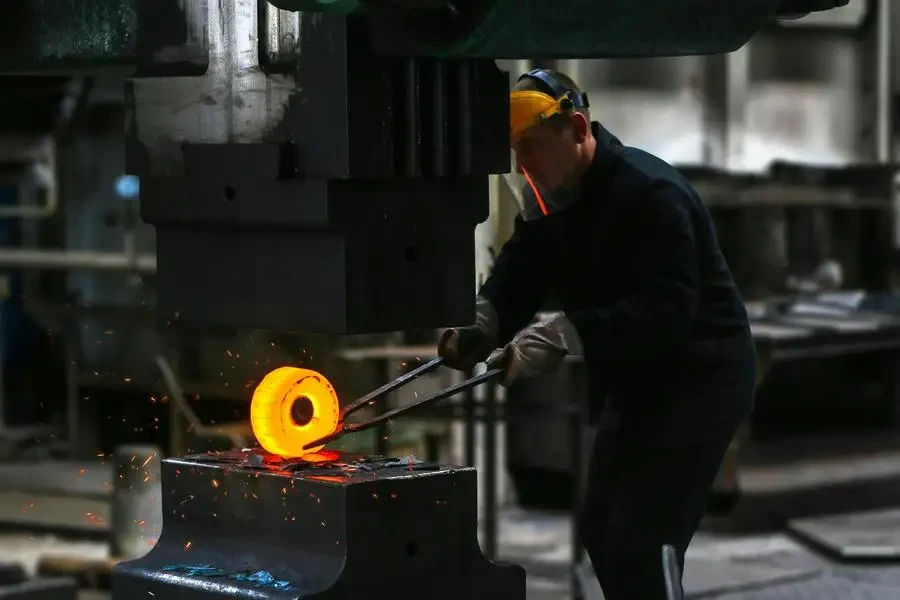
Aluminum TIG welders are vital in industries requiring precise, high-quality welds, such as aerospace, automotive, and construction. Key performance benchmarks include amperage control, duty cycle, and arc stability. Advanced models feature inverter technology, which enhances energy efficiency and weld quality. The market is driven by the rising demand for lightweight, corrosion-resistant aluminum structures, particularly in the automotive and aerospace sectors.
Market share dynamics reveal a concentration of key players in North America and Europe, with companies like Lincoln Electric, Miller Electric, and ESAB leading. These companies are innovating by integrating digital controls and IoT capabilities into their welders to boost performance and user experience. Economic factors, such as fluctuating aluminum prices and tariffs, significantly impact the market. However, technological advancements and automation investments are helping to mitigate these challenges.
Consumer behavior trends show a growing preference for eco-friendly, energy-efficient welding solutions. Seasonal demand patterns align with construction and manufacturing cycles, peaking in spring and summer. Distribution channels are evolving, with a notable increase in online sales platforms. This shift is driven by the convenience and expanded reach of e-commerce, enabling manufacturers to access global markets more effectively.
Trends and Innovations in Aluminum TIG Welder Market
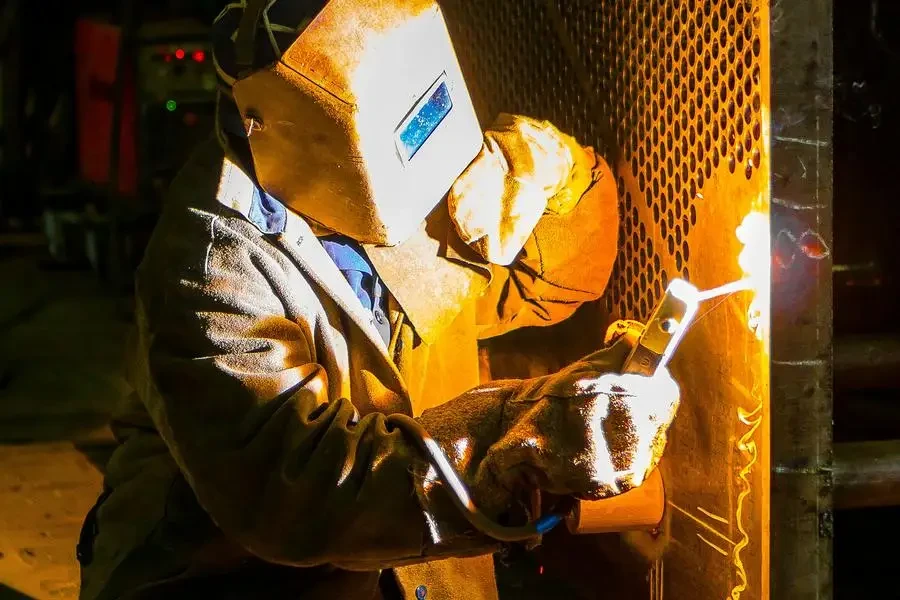
Recent innovations in aluminum TIG welders include the use of artificial intelligence and machine learning to optimize welding parameters and improve precision. Digitalization is transforming the market, with smart welders offering real-time monitoring and data analytics to enhance productivity and quality control. Environmental regulations are encouraging manufacturers to develop more sustainable welding solutions, focusing on reducing emissions and energy consumption.
Customer challenges in the aluminum TIG welder market often involve high initial costs and operational complexity. Manufacturers are addressing these issues by offering financing options and developing user-friendly interfaces. Brand positioning strategies emphasize reliability, performance, and after-sales support. Differentiation strategies include extended warranties, training programs, and comprehensive maintenance services.
Niche markets for aluminum TIG welders are emerging in sectors like renewable energy and electric vehicle manufacturing. These industries require specialized welding solutions to handle the unique properties of aluminum used in solar panels and EV battery packs. As the market evolves, manufacturers are likely to focus on these high-growth areas to drive future expansion.
Key Factors When Selecting an Aluminum TIG Welder
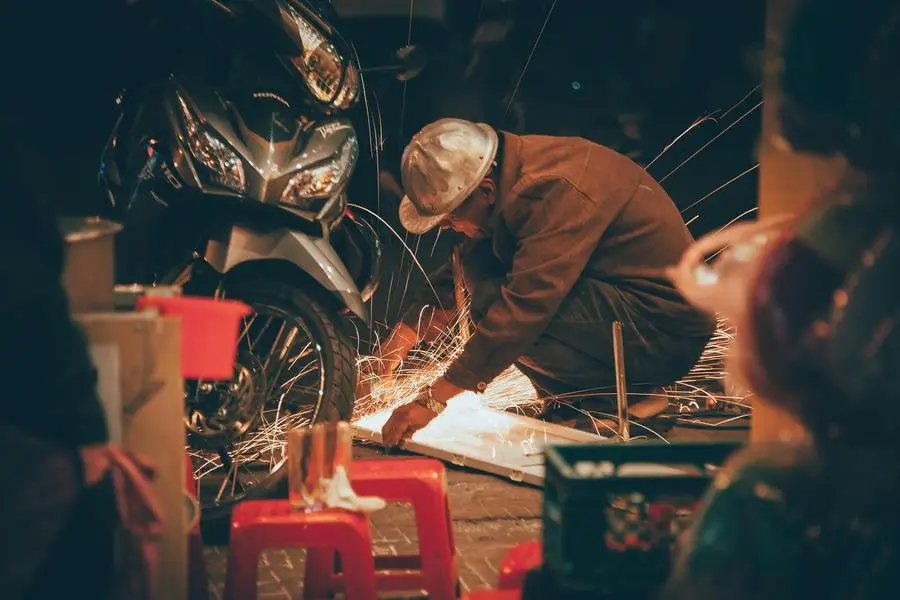
When choosing an aluminum TIG welder, several critical factors must be considered to ensure optimal performance and compatibility with your specific welding needs. These factors include the welder’s power output, duty cycle, compatibility with different materials, ease of use, and additional features that enhance functionality. Below, we delve into these considerations in detail.
1. Power Output and Duty Cycle
The power output of a TIG welder determines its capability to handle various thicknesses of aluminum. Typically, a welder with a higher amperage range is more versatile, allowing for welding both thin and thick materials. For instance, a welder with a range of 5 to 250 amps can efficiently handle tasks from delicate sheet metal work to robust structural applications.
The duty cycle indicates the percentage of time a welder can operate at a given output without overheating. For professional applications, a duty cycle of 60% or higher at maximum amperage is desirable, ensuring prolonged operation without interruptions. This is particularly important in industrial settings where continuous welding is required.
2. Material Compatibility and Versatility
Aluminum TIG welders must be compatible with various materials, including different aluminum alloys and other non-ferrous metals. The ability to switch between AC and DC modes is essential, as AC is typically used for aluminum due to its oxide cleaning action, while DC is preferred for steel and stainless steel. This versatility allows for a broader range of applications, making the welder a more valuable investment.
Additionally, the welder should support different electrode types and sizes, such as thoriated or ceriated tungsten, which are commonly used in TIG welding. This flexibility ensures that the welder can be tailored to specific tasks, enhancing its utility across different projects.
3. Ease of Use and User Interface
The ease of use of a TIG welder is significantly influenced by its user interface and control features. Modern welders often come equipped with digital displays and intuitive controls that simplify the setup process and allow for precise adjustments. Features such as pre-set welding programs, memory settings, and automatic adjustments for arc stability can greatly enhance the user experience, especially for less experienced operators.
Moreover, ergonomic design considerations, such as lightweight construction and comfortable torch grips, contribute to reduced operator fatigue during extended welding sessions. These aspects are particularly important in professional environments where efficiency and productivity are paramount.
4. Advanced Features and Technology
Advanced features in aluminum TIG welders can significantly enhance their performance and adaptability. Pulse welding capabilities, for example, allow for better control over heat input, reducing the risk of warping and improving weld quality on thin materials. Similarly, high-frequency start and arc stabilization technologies ensure smooth arc initiation and consistent performance.
Some welders also incorporate advanced cooling systems to manage heat dissipation, extending the lifespan of the equipment and reducing maintenance requirements. These technological advancements not only improve the quality of the welds but also contribute to the overall reliability and durability of the welder.
5. Price Range and Budget Considerations
The price range of aluminum TIG welders can vary significantly based on their features, power output, and brand reputation. around $500, while professional-grade welders with advanced features can exceed $3,000. It’s important to balance your budget with the specific requirements of your welding tasks, ensuring that you invest in a welder that meets your needs without unnecessary expenditure.
When evaluating cost, consider the long-term benefits of investing in a high-quality welder, such as reduced downtime, lower maintenance costs, and improved weld quality. Additionally, factor in the availability of customer support, warranty options, and the potential for future upgrades, which can enhance the value of your investment over time.
Understanding the Role of Safety Standards and Certifications
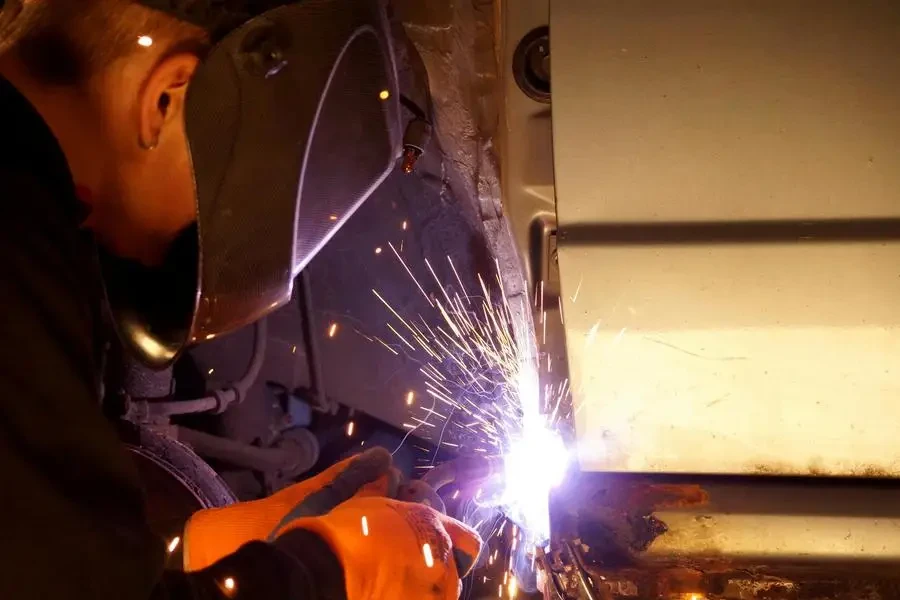
Safety standards and certifications play a pivotal role in the selection and operation of aluminum TIG welders. Compliance with recognized standards ensures that the equipment meets essential safety and performance criteria, providing peace of mind to operators and reducing the risk of accidents.
Importance of Compliance with Safety Standards
Compliance with safety standards, such as those set by the American Welding Society (AWS) or the International Organization for Standardization (ISO), is crucial for ensuring the safe operation of welding equipment. These standards cover various aspects, including electrical safety, thermal protection, and mechanical integrity, ensuring that the welder can withstand the demands of industrial use.
For instance, AWS D1.1 is a widely recognized structural welding code that outlines the requirements for welding steel structures, while ISO 9692 provides guidelines for welding and allied processes. Adherence to these standards not only enhances safety but also ensures that the welder delivers consistent and reliable performance.
Certifications and Their Impact on Quality Assurance
Certifications from reputable organizations serve as a mark of quality assurance, indicating that the welder has undergone rigorous testing and evaluation. These certifications often cover aspects such as energy efficiency, environmental impact, and overall performance, providing an additional layer of confidence in the product’s capabilities.
For example, a welder certified by the Underwriters Laboratories (UL) or the Canadian Standards Association (CSA) has been tested for safety and compliance with North American standards. Such certifications are particularly important for businesses that prioritize safety and quality in their operations, as they help mitigate risks and ensure compliance with regulatory requirements.
Evaluating the Manufacturer’s Reputation and Support
The reputation of the manufacturer and the availability of customer support are critical factors to consider when selecting an aluminum TIG welder. Established manufacturers with a track record of producing reliable and high-quality equipment are more likely to offer robust support services, including technical assistance, warranty coverage, and access to replacement parts.
Customer support options, such as online resources, helplines, and service centers, can significantly impact the user experience, especially in the event of equipment malfunctions or technical issues. A manufacturer that provides comprehensive support and stands behind its products can enhance the overall value of the welder, ensuring that it remains a reliable tool in your arsenal.
Exploring the Latest Technological Innovations in TIG Welding
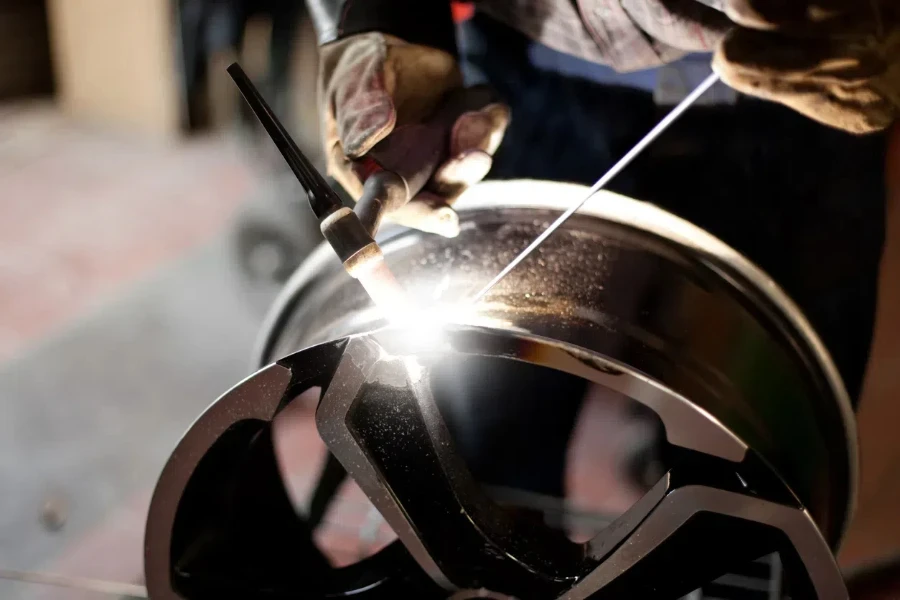
The field of TIG welding is continually evolving, with new technological innovations enhancing the capabilities and efficiency of aluminum TIG welders. These advancements not only improve the quality of welds but also expand the range of applications and simplify the welding process.
Integration of Smart Technologies
The integration of smart technologies in TIG welders is transforming the way welding is performed, offering features such as real-time monitoring, automated adjustments, and connectivity options. Smart welders can analyze welding parameters and make automatic adjustments to optimize performance, reducing the need for manual intervention and improving consistency.
Connectivity features, such as Bluetooth or Wi-Fi, enable remote monitoring and control, allowing operators to access welding data and make adjustments from a distance. This level of connectivity is particularly beneficial in large-scale industrial settings, where multiple welders may be in operation simultaneously.
Advancements in Arc Control and Stability
Recent advancements in arc control and stability have significantly improved the precision and quality of TIG welding. Technologies such as adaptive arc control and dynamic arc force adjustment allow for better management of the welding arc, ensuring consistent penetration and reducing the risk of defects.
These innovations are particularly valuable when working with challenging materials or complex joint configurations, where precise control over the welding process is essential. By enhancing arc stability, these technologies contribute to higher-quality welds and reduced rework, ultimately improving productivity and efficiency.
Energy Efficiency and Environmental Considerations
Energy efficiency is becoming an increasingly important consideration in the design and operation of TIG welders. Modern welders are equipped with energy-saving features, such as inverter technology, which reduces power consumption and minimizes heat loss. This not only lowers operating costs but also reduces the environmental impact of welding operations.
In addition to energy efficiency, manufacturers are also focusing on reducing the environmental footprint of their products by using sustainable materials and implementing eco-friendly manufacturing processes. These efforts align with the growing demand for environmentally responsible solutions in the welding industry, contributing to a more sustainable future.
Wrapping Up
Selecting the right aluminum TIG welder involves careful consideration of various factors, including power output, material compatibility, safety standards, and technological innovations. By understanding these aspects, you can make an informed decision that meets your specific welding needs and enhances your operational efficiency.