We often underestimate the seemingly insignificant function of battery terminals while enjoying the convenience of electronic devices. But terminals are an essential component for electrical connection between batteries and circuits. Although they may appear simple, they play an indispensable role in powering of insatiable need for technology and industry. These unassuming battery terminals are therefore ubiquitous and found in everything from large aerospace equipment to small automobiles, cellular phones, and household appliances, etc., and will continue to exist as long as people need electrical energy.
Here, we’ll introduce the common types, applications, and R&D directions of modern-day battery terminals.
Table of Contents
Common types of battery terminals
Current major application areas and market economies for battery terminals
Considerations for choosing and using battery terminals
R&D directions for battery terminals
Common types of battery terminals
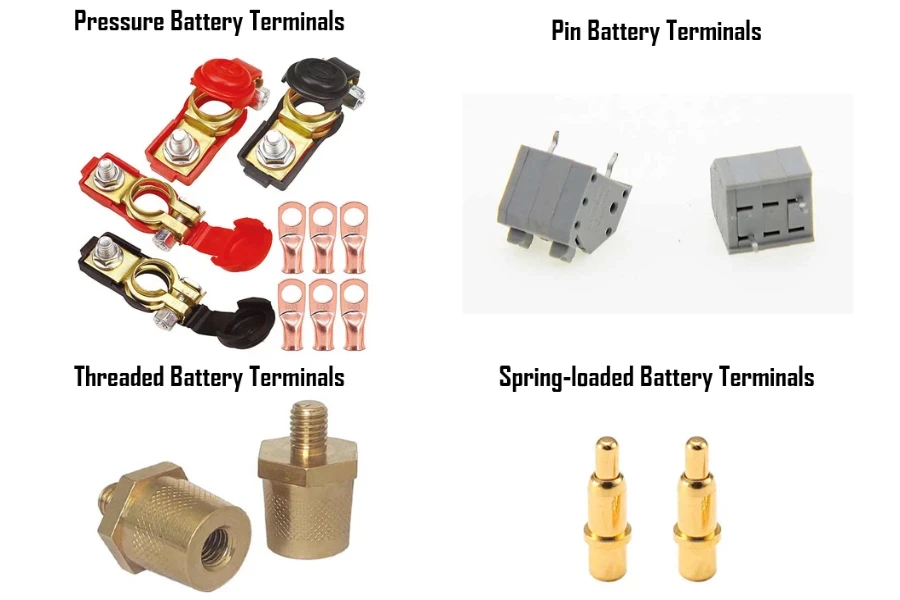
The primary distinctions among the four main battery terminals – pressure, pin, threaded, and spring-loaded – relate to their shape, connection method, current-carrying capacity, and environmental suitability. For example, pressure battery terminals rely on direct pressure to maintain contact with the battery, applied using a spring or other flexible material that pushes the terminal against the battery; threaded battery terminals connect via a screwing mechanism; pin battery terminals connect via a male (pin) and female (socket) connection; and spring-loaded battery terminals use a spring mechanism to apply constant pressure to the battery contact.
Regarding current capacity, pressure battery terminals and threaded battery terminals typically support currents in the range of 200-300A, while pin battery terminals and spring-loaded battery terminals generally handle currents of less than 50A.
At present, the majority of battery terminals are customized for specific applications, necessitating the selection of battery terminals based on the exact demands of a given application scenario.
Below we take a closer look at the common types of battery terminals and their application scenarios:
Type | Brief introduction | Application scenarios |
Pressure battery terminals | Establish connections between circuits by applying pressure to metals. Some rely on the inherent hardness of a larger conductive metal (such as copper) to deform and establish a firm and enduring connection, which generally remains unchanged. Others use screws to control the pressure on the metal, making them easy to remove and replace. | Primarily employed in applications demanding high currents, such as power tools and electric vehicles. They are designed to meet the requirements of high-power circuits and ensure efficient transmission of electrical energy. |
Threaded battery terminals | Equipped with a threaded structure designed to securely connect the battery and the circuit. This design not only ensures the safety of the connection but also allows for convenient disassembly when needed. | Predominantly used in automotive batteries and industrial equipment. The threaded design enables these terminals to endure demanding elements, including high vibration and high voltage, assuring dependable circuit connections in specific environments. |
Pin battery terminals | Typically encapsulated by protruding metal pins, commonly used for connecting circuits to printed circuit boards (PCBs), often by soldering. | Primarily employed in electronic devices, including computer motherboards, embedded systems, and electronic instruments. They offer reliable connections and are frequently utilized to facilitate intricate circuitry between chips or between chips and sensors or responsive devices. |
Spring-loadedbattery terminals | Features a compressible spring structure, allowing for easy insertion and removal to establish or disconnect the circuit connection. | Available in various shapes designed to match the configuration of the relevant circuit or battery. They are commonly used in portable devices such as mobile power supplies, portable audio equipment, and test and measurement devices. These terminals enable easy alterations in circuit connections and disconnections, ensuring dependable electrical contact. |
Current major application areas and market economies for battery terminals
Battery terminals are closely intertwined with the evolution of the consumer electronics industry. With the integration of artificial intelligence and other emerging technologies into consumer electronics, the pace of product updates is poised to accelerate. This, in turn, is expected to lead to an expansion of the market size within the consumer electronics industry, consequently driving growth in the battery terminals market.
The global market size for battery terminals was approximately US $24.68 billion by 2022, according to an analysis of historical data from 2016 to 2022, indicating a compound annual growth rate (CAGR) of approximately 5.42%. It is forecast that this market will exceed US $30 billion by 2028. Furthermore, the rapid pace of iterative development in electronic products is poised to generate opportunities and heightened performance requirements for battery end products.
The battery terminal industry chain encompasses upstream sectors for metal, plastic, and plating raw materials, as well as the midstream manufacturing industry, which includes stamping, plating, injection molding, and assembly, among others. Furthermore, it extends to the downstream application industry.
Battery terminals are now mainly used in the following sectors:
Electric vehicles
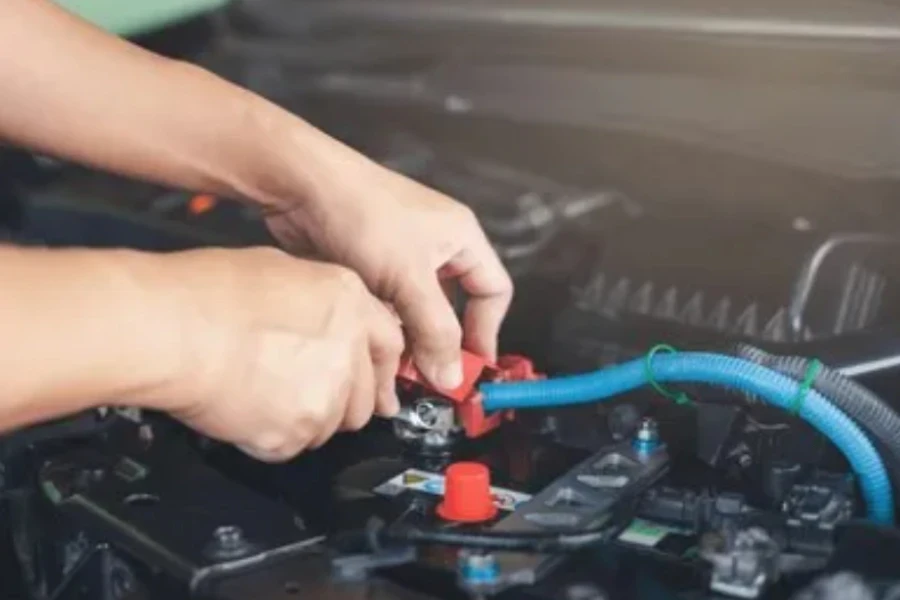
Specialized automotive battery terminals serve as power sources for internal combustion engines and information security systems, typically operating within the current range of 40 to 100 amps. These terminals are purpose-built to withstand the high voltages, electrical demands, and severe vibrations associated with vehicle operation.
The electric vehicle (EV) industry has seen a remarkable 30% increase in market share over the past few years. This surge is a consequence of the automotive industry’s shift from conventional fossil fuel-powered vehicles to electric and hybrid alternatives. In turn, the substantial expansion of the electric vehicle sector has catalyzed significant growth in the battery end assembly market. It is anticipated that this market will reach US $8 billion in the next five years, with a projected CAGR of 5% during the forecast period.
Consumer electronics
Consumer electronics comprise a vast, trillion-dollar market, encompassing hundreds of millions of portable devices, including smartphones, tablets, cameras, headphones, and more. These devices are heavily dependent on battery terminals for their power supply, necessitating the miniaturization and swift charging capabilities of these battery terminals. Owing to swift technological advancements and rising demands for battery terminals, the market size of battery terminals in the realm of consumer electronics applications is poised to grow by 6% or more in the foreseeable future.
Military and aerospace
The specific criteria for battery terminals revolve primarily around the need to ensure high reliability and optimal performance under challenging environmental conditions. Given the changing military landscape, advances in space exploration technology, and increasing mission frequency, it is estimated that the market demand for battery terminals with exceptional reliability will continue to grow. Based on historical data, the end-use size of the defense and aerospace sector is about 25% of the automotive industry and is expected to reach US $4 billion by 2028.
Furthermore, battery terminals are crucial across diverse industries, including Internet of Things (IoT) devices, maritime applications, and smart healthcare. In light of the significance and diversity of these battery terminals, what key considerations should be considered?
Considerations for choosing and using battery terminals
Model selection
Selecting the right battery terminal is crucial to ensure a secure, reliable, and safe connection. Here’s what you should consider:
- Material: Battery terminals are typically constructed from metals such as copper, aluminum, or stainless steel. The choice of material primarily governs the terminal’s conductivity, resistance to corrosion, and capacity to withstand varying temperature ranges.
- Voltage rating: This parameter defines the maximum system voltage that the designed terminals must not surpass during installation. It is typically contingent on factors such as the pitch and the dielectric strength of the housing.
- Current rating: The current rating signifies the maximum nominal current per pole for which the terminal block is designed. This electrical specification is generally influenced by several factors, including the cross-sectional area, terminal conductivity, heat generation at the rated current (following UL1059 standards), or power dissipation at the rated current (as per IEC 60947-7 standards).
- Termination type: The termination type delineates the methodology employed to connect wires to the terminals. Common connection methods encompass crimping, soldering, and threaded connections.
- Wiring range: The wiring range represents the minimum and maximum wire sizes that the terminal is designed to accommodate.
- Environmental conditions: Terminals deployed in diverse environmental conditions necessitate careful consideration of relevant characteristics, encompassing temperature, humidity, vibration, shock, and resistance to corrosion.
Installation and tests
Upon due consideration of the aforementioned factors and the selection of a prospective product, it is essential to exercise vigilance during the installation and testing phases. Particular attention must be devoted to detecting issues such as poor contact, inadequate insulation, and resistance mismatches. The occurrence of such conditions may be attributable to various factors, including improper storage methods, inadequate pressure, the exceeding of screw torque limits during installation, defects in metal molds employed during processing, rough surface finishes, and the imprudent selection of plating processes. Furthermore, issues may also arise due to factors such as moisture ingress or the aging of organic materials.
We recommend subjecting the terminals to testing under the same environmental conditions that the complete assembly will encounter. These tests should encompass assessments of on-off functionality, instantaneous interruption detection, insulation integrity, interchangeability, evaluation of environmental adaptability, assessment of maximum nominal current, determination of maximum torque tolerance, temporary overvoltage or inrush current capabilities, evaluation of potential wire tension, and other relevant aspects. Additionally, for battery terminal assessment, the utilization of a specialized terminal cross-section analyzer is advisable. This apparatus facilitates automatic analysis by dissecting, grinding, and assessing corrosion at the terminal’s crimping section, ultimately generating a comprehensive quality report.
Routine maintenance
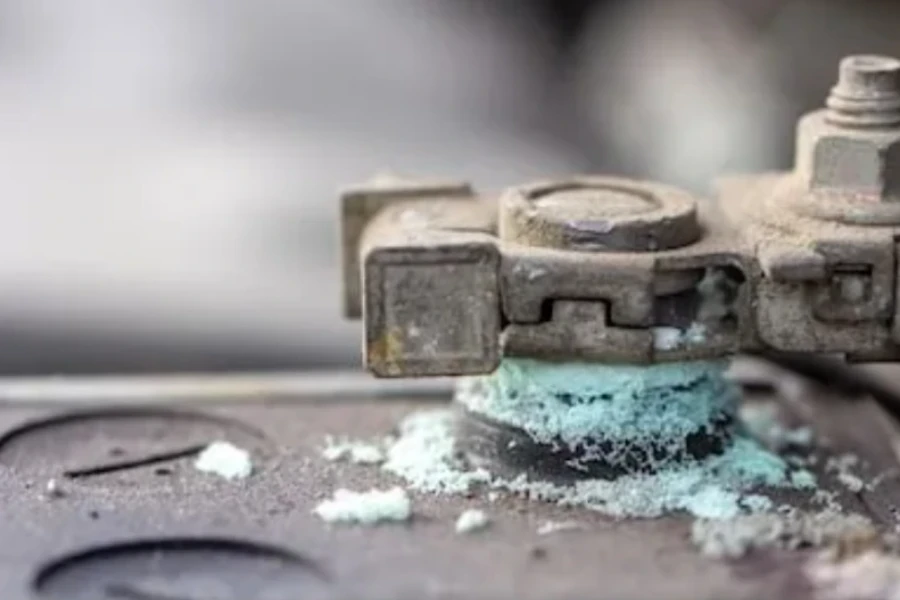
During usage, it is imperative to routinely inspect the terminal connections and their cleanliness. In cases where corrosion is observed during maintenance, it can be effectively remedied through cleaning with a mixture of baking soda and water. Rust, if encountered, can be addressed by utilizing rust remover or penetrating oil. Furthermore, lubricants can be employed to alleviate terminals that have been excessively tightened.
R&D directions for battery terminals
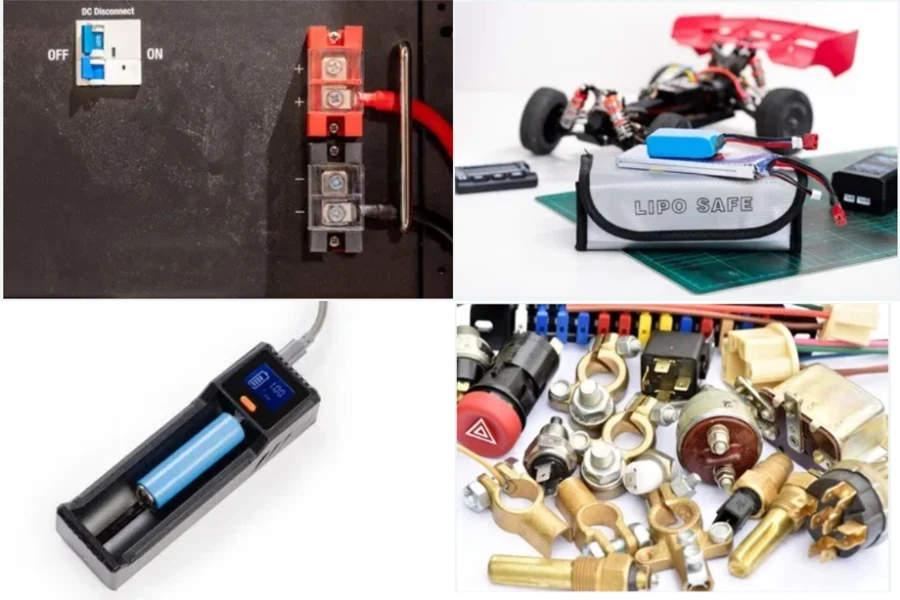
The latest research in the field of battery terminals primarily centers around the utilization, intelligence, and miniaturization of new materials. In the future, battery terminals are expected to feature enhanced performance and stability, be more environmentally friendly, have real-time battery status monitoring, and facilitate the development of small electronic products. For instance, the surging need for rapid charging in new energy vehicles places substantial requirements on the current handling capacity of battery terminals. Presently, high-power charging stations can deliver up to 500kW with a peak current of 650A. Consequently, the pursuit of swifter and more efficient charging solutions, weight reduction in terminal design, and enhanced electrical connection performance represent highly promising avenues for future battery terminal development.