In 2025, the industrial sewing machine market is projected to reach USD 10.3 billion, reflecting the growing demand for high-efficiency, precision sewing equipment. This article provides an in-depth analysis of key factors, from machine types to the latest technological advancements, assisting professional buyers in making informed purchasing decisions.
Table of Contents:
– Industrial Sewing Machine Market: A Comprehensive Overview
– Key Factors When Selecting an Industrial Sewing Machine
– Latest Technology Features in Industrial Sewing Machines
– Compatibility with Future Upgrades
– Ensuring Durability and Quality
– Final Thoughts on Industrial Sewing Machines
Industrial Sewing Machine Market: A Comprehensive Overview

Market Overview
The global industrial sewing machine market has shown significant growth. It is projected to expand at a compound annual growth rate (CAGR) of 4.7% from 2023 to 2032, aiming for a valuation of USD 10.3 billion by 2032. Key drivers include the growing fashion and textile industries, which demand high-efficiency and precision sewing equipment. Additionally, the DIY trend and the rise in home-based businesses have boosted demand for both basic and advanced sewing machines.
The industrial segment is particularly robust, driven by the need for mass production. Growth in this sector is supported by increasing adoption in the automotive industry for manufacturing items like car seats and airbags. The Asia-Pacific region, especially China, Japan, and India, are major producers and consumers of sewing machines. The Americas and Europe also show strong demand, particularly for high-quality and technologically advanced machines.
Detailed Market Analysis
Key performance benchmarks in the industrial sewing machine market include stitch quality, speed, and durability. Machines are evaluated based on their ability to maintain consistent stitch quality at high speeds, crucial for mass production. Machines capable of achieving 5,000 stitches per minute are highly sought after in industries requiring rapid production cycles.
Market share dynamics reveal that companies such as JUKI Corporation, Brother Industries, Ltd., and Bernina International AG hold significant portions of the market due to their innovative products and strong brand reputations. Increasing labor costs in manufacturing hubs like China have led to a shift towards more automated and efficient sewing solutions.
Consumer behavior has shifted towards advanced features such as computerized controls and automated thread cutting, enhancing productivity and ease of use. Distribution channels are evolving, with a growing trend towards online sales platforms. This shift is driven by the convenience and wider product selection available online, as well as the increased penetration of e-commerce in emerging markets.
Recent innovations include the integration of Internet of Things (IoT) technology, allowing for real-time monitoring and maintenance alerts, significantly reducing downtime and enhancing operational efficiency. Additionally, the development of energy-efficient machines is gaining traction, addressing environmental concerns and reducing operational costs.
Product lifecycle stages vary, with basic mechanical machines often having longer lifespans compared to electronic and computerized counterparts, which may require more frequent updates and maintenance. Digitalization is transforming the sewing machine industry, with smart machines offering features such as pattern storage, automatic tension adjustment, and remote diagnostics.
Social trends, such as the increasing popularity of sustainable fashion and upcycling, are influencing the market. Consumers are more inclined towards repairing and customizing their clothing, driving demand for versatile and user-friendly sewing machines. Customer pain points include the complexity of operating advanced machines and the high initial costs of high-end models.
Brand positioning strategies focus on technological advancements, superior customer service, and comprehensive training programs. Companies are also targeting niche markets such as custom embroidery and quilting, which require specialized machines. Differentiation strategies involve offering modular machines that can be upgraded with additional features, providing flexibility and scalability for businesses.
Key Factors When Selecting an Industrial Sewing Machine
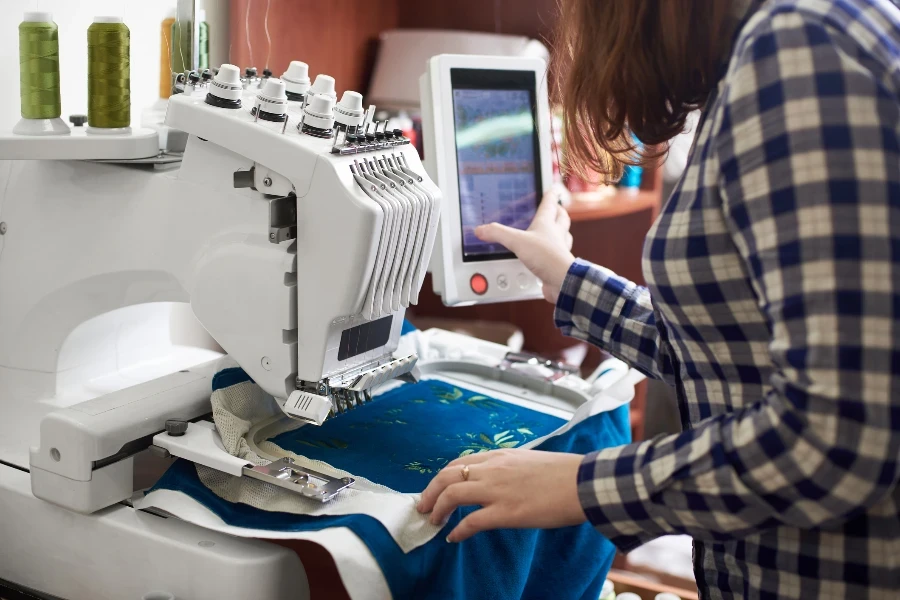
Types and Styles
Understanding the different types and styles of industrial sewing machines is crucial for making the right selection. The most common types include lockstitch, chainstitch, overlock, and coverstitch machines. Each type serves a specific purpose and is designed to handle particular fabrics and stitching techniques.
Lockstitch machines are versatile and produce a strong, straight stitch, making them ideal for general sewing tasks and garment manufacturing. Chainstitch machines create a looped stitch, offering more flexibility for stretchy fabrics and applications requiring elasticity.
Overlock machines, also known as sergers, specialize in finishing edges and preventing fraying. They can trim the fabric while stitching, speeding up the sewing process. Coverstitch machines are designed for hemming and are often used in activewear and other stretchable fabrics. Understanding these types and their applications helps buyers choose the right machine for their specific needs.
Performance and Functionality
Performance and functionality are critical factors in selecting an industrial sewing machine. The machine’s speed, measured in stitches per minute (SPM), is essential. High-speed machines can significantly increase productivity, with some models capable of 5,000 SPM or more. However, the appropriate speed depends on the fabric type and the complexity of the sewing tasks.
Stitch quality and consistency are also important. Advanced models feature automatic thread tension adjustment and stitch length control, ensuring uniform stitches and reducing the need for manual adjustments. Machines with programmable stitch patterns and automated functions, such as thread trimming and backstitching, enhance efficiency and reduce operator fatigue.
Functionality includes the machine’s ability to handle different materials, from lightweight fabrics like silk to heavy-duty materials such as denim and leather. Machines with adjustable presser foot pressure and variable needle positions offer greater flexibility for various sewing projects.
Technical Specifications
Technical specifications play a pivotal role in evaluating industrial sewing machines. Key specifications to consider include the machine’s motor power, which affects its ability to handle heavy fabrics and sustain high-speed operation without overheating. Typically, a motor power of at least 550 watts is recommended for demanding applications.
The needle system is another crucial specification. Industrial machines often use specific needle types designed for particular fabrics and stitching techniques. For example, ballpoint needles are suitable for knit fabrics, while sharp needles are better for woven materials. Ensuring compatibility with the required needle system is essential for achieving optimal stitch quality.
The machine’s dimensions and weight are also important, especially if space is limited or if the machine needs to be moved frequently. Compact models with a sturdy build offer the best balance between durability and portability. Additionally, the throat space, the distance between the needle and the machine’s body, should be sufficient to accommodate the size of the projects being handled.
Safety Standards and Certifications
Adherence to safety standards and certifications is paramount when selecting an industrial sewing machine. Machines should comply with relevant safety regulations, such as those set by the Occupational Safety and Health Administration (OSHA) in the United States or the European Union’s Machinery Directive. These standards ensure safe operation and reduce the risk of workplace accidents.
Certifications from recognized bodies, such as the International Organization for Standardization (ISO) or Underwriters Laboratories (UL), provide additional assurance of the machine’s quality and safety. Machines with these certifications have undergone rigorous testing to meet high safety and performance standards.
Consider features that enhance operator safety, such as needle guards, automatic shut-off mechanisms, and emergency stop buttons. These features prevent injuries and ensure a safer working environment. Regular maintenance and proper training for operators are also crucial for maintaining safety standards.
Price Range and Budget Considerations
The price range of industrial sewing machines can vary significantly, depending on the features and capabilities of the machine. Entry-level models may start at around $1,000, while high-end machines with advanced features can cost upwards of $10,000. Balancing the budget with the required features and performance is essential.
When setting a budget, consider the total cost of ownership, including the initial purchase price, maintenance, spare parts, and potential upgrades. Machines offering greater durability and lower maintenance costs may provide better long-term value, even if their initial price is higher.
Financing options and leasing programs can also be beneficial for managing the budget. Many manufacturers and distributors offer flexible payment plans that allow buyers to spread the cost over time. Additionally, investing in machines with energy-efficient motors and components can reduce operating costs and contribute to overall savings.
Latest Technology Features in Industrial Sewing Machines
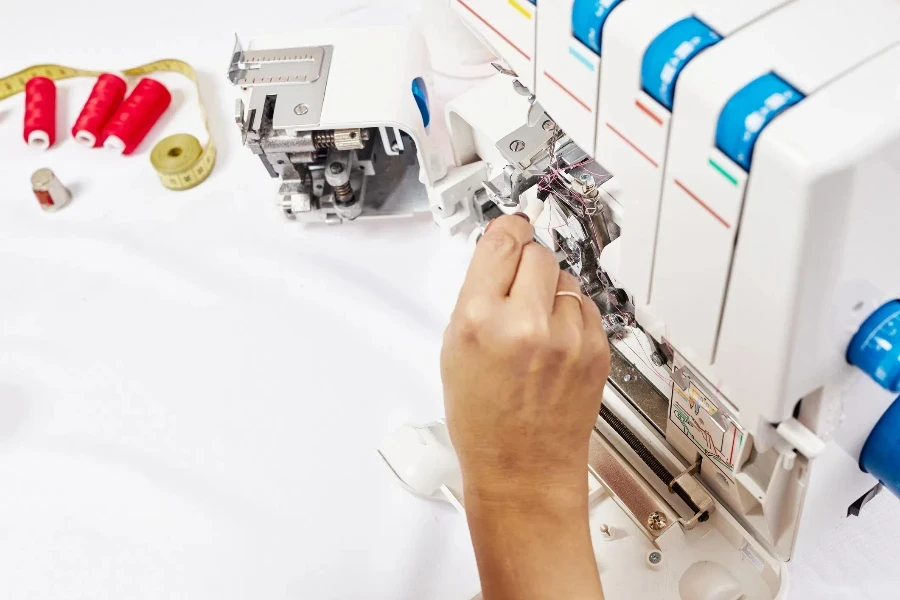
Technological advancements have significantly enhanced the capabilities of industrial sewing machines. One notable advancement is the integration of computer-aided design (CAD) and computer-aided manufacturing (CAM) systems. These systems enable precise control over stitch patterns and allow for the customization of designs with minimal manual intervention.
Another cutting-edge feature is the use of direct drive motors, which offer greater energy efficiency and lower noise levels compared to traditional clutch motors. Direct drive motors provide better control over the sewing speed and reduce the wear and tear on machine components, extending the machine’s lifespan.
Automation is becoming increasingly prevalent in industrial sewing machines. Features such as automatic thread trimming, needle positioning, and fabric feeding systems streamline the sewing process and reduce the need for manual adjustments. Some advanced models are equipped with sensors and cameras that detect fabric inconsistencies and adjust the stitching parameters in real-time, ensuring consistent quality.
Compatibility with Future Upgrades
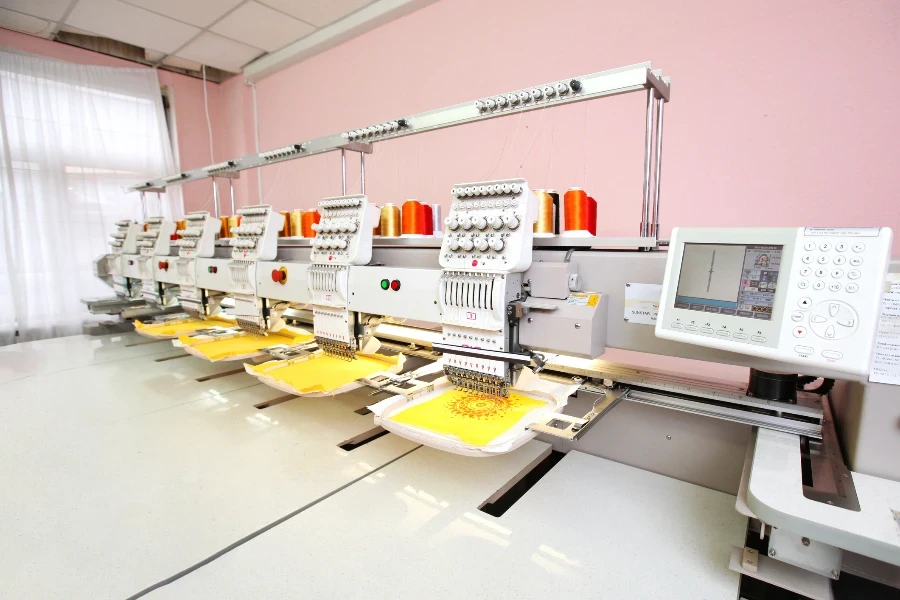
When selecting an industrial sewing machine, consider its compatibility with future upgrades. Machines designed with modular components and open architecture can be easily upgraded with new features and technologies as they become available. This flexibility allows businesses to keep up with evolving industry standards and maintain a competitive edge.
For instance, machines with USB ports or wireless connectivity can receive software updates and new stitch patterns directly from the manufacturer. This capability ensures the machine remains up-to-date with the latest advancements and can adapt to changing production requirements.
Additionally, compatibility with a wide range of accessories and attachments can enhance the machine’s versatility. Common accessories include different types of presser feet, hemming guides, and quilting attachments. Investing in a machine that supports a variety of add-ons can expand its functionality and make it suitable for a broader range of applications.
Ensuring Durability and Quality
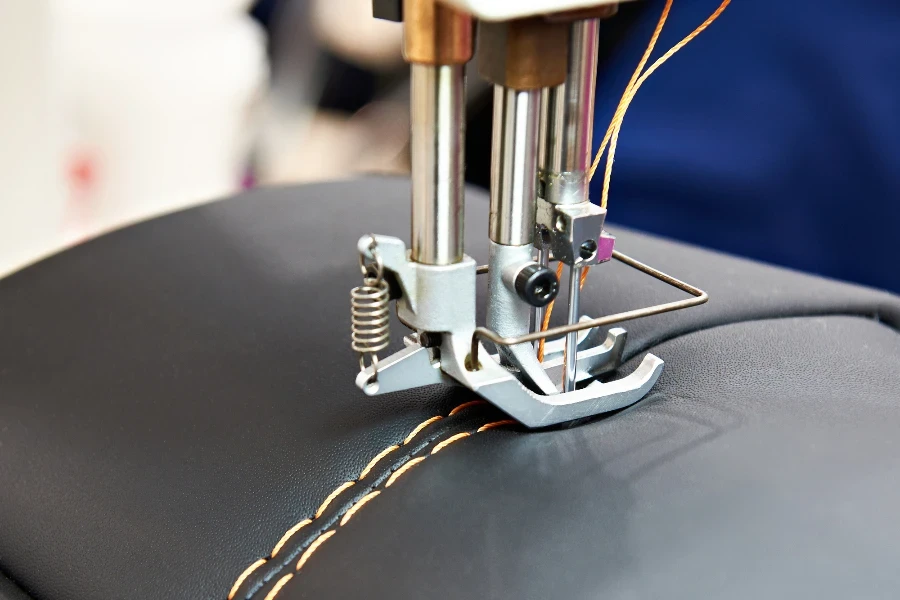
Durability and quality are critical considerations for industrial sewing machines, as they are subjected to intensive use in demanding environments. Machines constructed with high-quality materials, such as cast iron frames and stainless steel components, offer greater longevity and resistance to wear and tear.
Reputable manufacturers often provide warranties and after-sales support, which can be a good indicator of the machine’s quality. A comprehensive warranty that covers parts and labor for an extended period provides peace of mind and protects the investment.
Regular maintenance is essential for ensuring the machine’s durability. Following the manufacturer’s recommended maintenance schedule, such as lubricating moving parts, replacing worn components, and cleaning the machine regularly, can prevent breakdowns and prolong the machine’s lifespan. Some advanced models come with built-in diagnostic tools that alert operators to maintenance needs, ensuring timely servicing and reducing downtime.
Final Thoughts on Industrial Sewing Machines
Selecting the right industrial sewing machine requires careful consideration of various factors, including types and styles, performance and functionality, technical specifications, safety standards, price range, latest technology features, compatibility with future upgrades, and ensuring durability and quality. By thoroughly evaluating these aspects, businesses can make informed decisions that meet their specific needs and contribute to efficient and high-quality production.