In 2025, the demand for efficient packaging solutions has surged, making stretch wrapper machines indispensable. This article delves into market trends, performance metrics, and essential considerations for professional buyers, providing valuable insights for informed decision-making.
Table of Contents:
– Stretch Wrap Machine Market Overview
– Key Factors When Selecting a Stretch Wrapper Machine
– Innovations and Technological Advancements
– Cost Considerations and Budget Planning
– Final Thoughts
Stretch Wrap Machine Market Overview
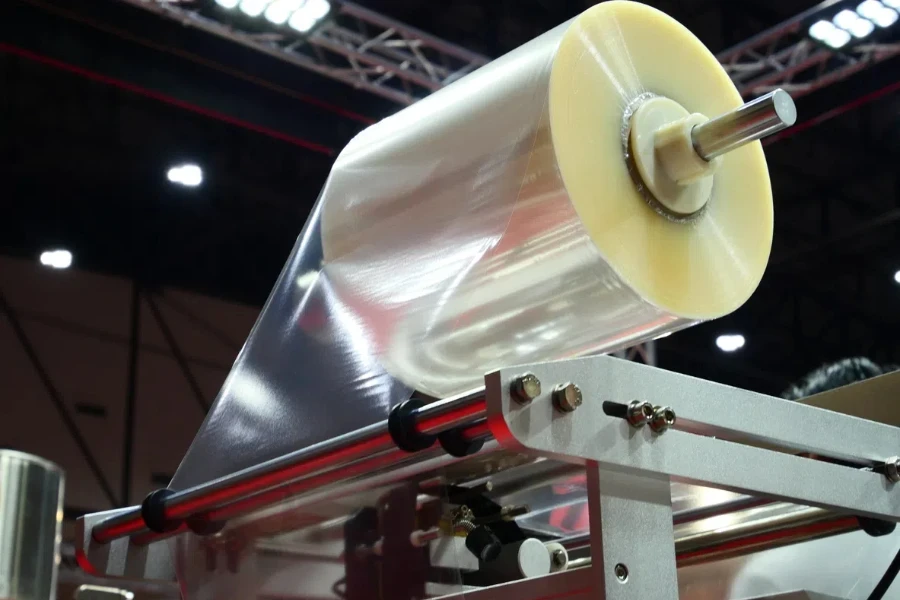
The global stretch wrap machines market has seen notable growth recently, driven by the rising demand for efficient packaging solutions across various industries. As of 2024, the market size was worth USD 843.47 million and is projected to reach USD 1,118.51 million by 2030, growing at a compound annual growth rate (CAGR) of 5.00%. This growth is due to the increasing need for secure and durable packaging in sectors such as automotive, chemical, and construction.
The market is divided into different types based on the machinery used: orbital stretch wrapper, ring straddle stretch wrapper, straddle stretch wrapper, and turntable stretch wrapper. Each type meets specific packaging needs, contributing to overall market growth. The Americas and Asia-Pacific regions have shown significant market penetration due to their growing industrial activities and investments in packaging automation.
Detailed Introduction and Analysis of the Stretch Wrap Machine Market
Stretch wrap machines are crucial in modern packaging, offering secure and efficient wrapping solutions. These machines wrap products tightly with stretch film, ensuring stability and protection during transport and storage. A key performance benchmark is the machine’s ability to handle various load sizes and shapes while maintaining high productivity and minimal film waste.
The market is competitive, with key players like Aetnagroup S.p.A, ATLANTA STRETCH, and Phoenix Wrappers, Inc. These companies focus on innovation, such as developing automated and semi-automated stretch wrap machines that enhance operational efficiency and reduce labor costs. Innovations include advanced control systems and real-time monitoring capabilities, significantly improving machine performance and reliability.
Consumer behavior has shifted towards sustainable packaging solutions, impacting the stretch wrap machine market. The focus on eco-friendly materials and energy-efficient machines has led manufacturers to invest in R&D for greener technologies. Distribution channels have evolved, with a preference for direct sales and online platforms, providing customers with easier access to a wide range of products and services.
Key Trends and Future Outlook
The stretch wrap machine market is set for continuous growth, driven by advancements in automation and digitalization. Integrating IoT and AI in stretch wrap machines will enhance operational efficiency and predictive maintenance, reducing downtime and operational costs. Additionally, the trend towards sustainable packaging solutions will further drive market growth, as manufacturers aim to meet regulatory requirements and consumer demands for eco-friendly products.
Technological innovations and improved machine designs are addressing customer needs for consistent wrapping quality and reduced film waste. Companies are also focusing on brand positioning strategies that emphasize their commitment to sustainability and operational excellence, differentiating themselves in a competitive market.
Key Factors When Selecting a Stretch Wrapper Machine
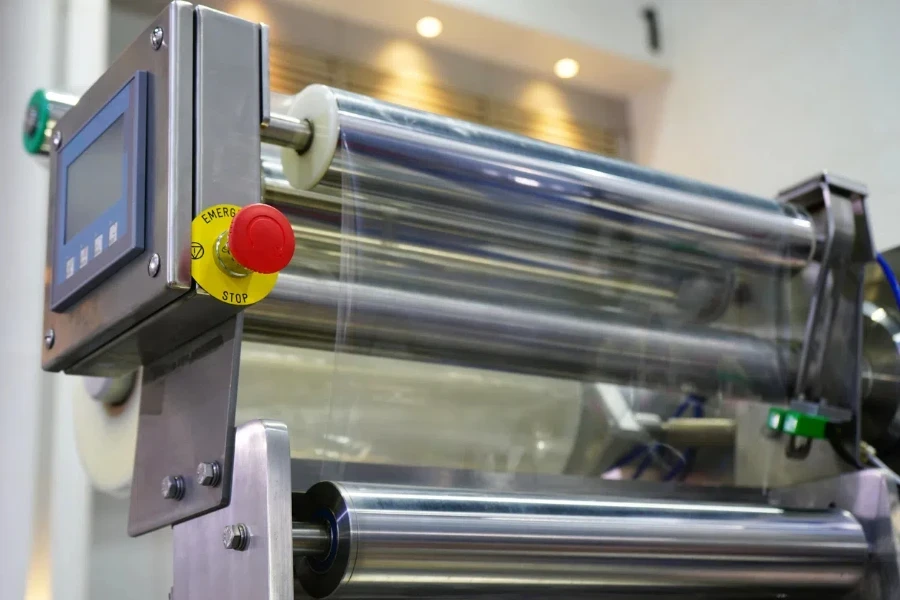
Performance and Efficiency
When evaluating a stretch wrapper machine, consider its speed and throughput. High-speed models can wrap up to 45 loads per hour, boosting productivity for larger operations. Machines with variable-speed controls allow operators to adjust the wrapping speed based on load size and type, optimizing material usage and reducing waste.
The efficiency of a stretch wrapper is influenced by its film delivery system. Machines with pre-stretch technology can extend the film up to 300%, maximizing usage and cutting costs. Automated film cutting and sealing systems minimize downtime by eliminating manual intervention, ensuring a consistent wrapping process and enhancing overall operational efficiency.
Energy consumption is another critical aspect. Modern stretch wrappers feature energy-efficient motors and components, reducing electricity usage and operational costs. Some advanced models also have energy-saving modes that automatically power down the machine when not in use, conserving energy and lowering utility expenses.
Durability and Build Quality
The durability and build quality of a stretch wrapper machine are crucial for long-term reliability and performance. Machines made with high-grade steel frames and corrosion-resistant components offer enhanced longevity, even in demanding industrial environments. Robust construction ensures that the machine can withstand heavy usage without frequent breakdowns or maintenance issues.
Attention to detail in manufacturing, such as precision welding and high-quality bearings, contributes to the machine’s overall durability. Protective coatings and finishes can prevent wear and tear, extending the machine’s lifespan. Ensuring that the machine meets industry standards, such as ISO 9001 for quality management systems, attests to its build quality and reliability.
Regular maintenance is essential to maintain the machine’s durability. Many modern stretch wrappers come with built-in diagnostic systems that alert operators to potential issues before they become major problems. This proactive approach to maintenance can prevent costly downtime and extend the machine’s operational life.
Safety Standards and Certifications
Compliance with safety standards and certifications is crucial when selecting a stretch wrapper machine. Machines that adhere to international safety standards, such as CE marking for European markets or UL certification for North America, ensure they meet stringent safety requirements. These certifications indicate that the machine has undergone rigorous testing and meets the necessary safety criteria.
Safety features, such as emergency stop buttons, safety interlocks, and light curtains, are essential to protect operators from potential hazards. Machines equipped with these safety mechanisms can prevent accidents and injuries, creating a safer working environment. User-friendly control panels with clear instructions and warnings enhance operational safety by reducing the risk of operator error.
Regularly updated safety protocols and training programs for operators are also vital. Manufacturers that provide comprehensive training and support can help ensure that operators are well-versed in the safe use of the machine, further minimizing the risk of accidents and enhancing overall workplace safety.
Compatibility and Integration
The compatibility and integration of a stretch wrapper machine with existing systems and processes are essential for seamless operation. Machines that can easily integrate with warehouse management systems (WMS) or enterprise resource planning (ERP) systems offer enhanced efficiency and data accuracy. This integration allows for real-time monitoring and control of the wrapping process, optimizing inventory management and reducing errors.
Compatibility with various types of loads and pallets is also crucial. Adjustable film tension settings and customizable wrapping patterns enable the machine to handle different load sizes and shapes, ensuring secure and stable wrapping. Machines that can accommodate a wide range of pallet sizes and configurations provide greater flexibility and versatility in the wrapping process.
Future-proofing the machine by ensuring compatibility with potential upgrades and advancements is another important consideration. Machines designed with modular components and open architecture can be easily upgraded or modified to incorporate new technologies, extending their useful life and providing a better return on investment.
Initial Setup and Ease of Use
The initial setup and ease of use of a stretch wrapper machine can significantly impact its overall efficiency and user satisfaction. Machines with straightforward installation processes, clear instructions, and minimal assembly requirements can be up and running quickly, reducing downtime and disruption to operations.
User-friendly interfaces and intuitive control panels make it easier for operators to learn and use the machine effectively. Touchscreen controls with graphical displays and step-by-step instructions can simplify the setup and operation, reducing the learning curve and minimizing the risk of errors. Machines with programmable settings and memory functions allow operators to save and recall frequently used wrapping patterns, further enhancing ease of use.
Ongoing support and training from the manufacturer or supplier are also important. Access to comprehensive user manuals, online resources, and responsive customer service can help operators troubleshoot issues and optimize the machine’s performance. Regular training sessions and updates on new features or best practices can ensure that operators remain proficient and confident in using the machine.
Innovations and Technological Advancements
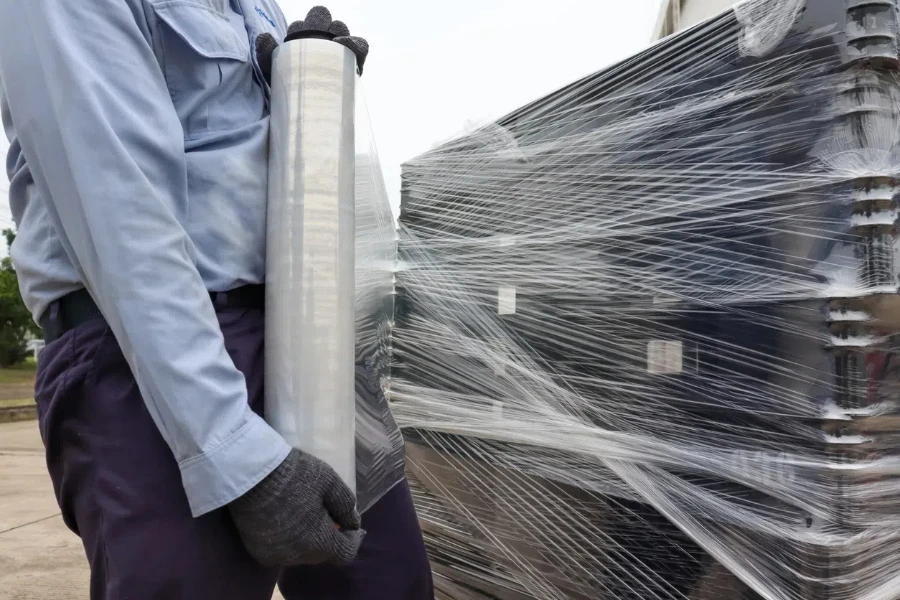
The stretch wrapper machine industry has seen significant technological advancements in recent years, aimed at improving efficiency, safety, and versatility. One notable development is the integration of Internet of Things (IoT) technology, allowing for real-time monitoring and remote control of the machine. IoT-enabled stretch wrappers provide valuable data on machine performance, film usage, and maintenance needs, enabling predictive maintenance and reducing downtime.
Another important innovation is the use of advanced sensors and automation. Modern stretch wrappers equipped with load sensors and automatic height detection can accurately measure and adjust wrapping parameters to suit the load, ensuring optimal film usage and load stability. Automated film threading and cutting systems further enhance efficiency by reducing the need for manual intervention.
Sustainability is also a key focus, with manufacturers developing eco-friendly stretch wrappers that use biodegradable films and energy-efficient components. These machines not only reduce the environmental impact but also offer cost savings through reduced energy consumption and lower film waste. As sustainability becomes increasingly important in global markets, these innovations are likely to become standard features in stretch wrapper machines.
Cost Considerations and Budget Planning
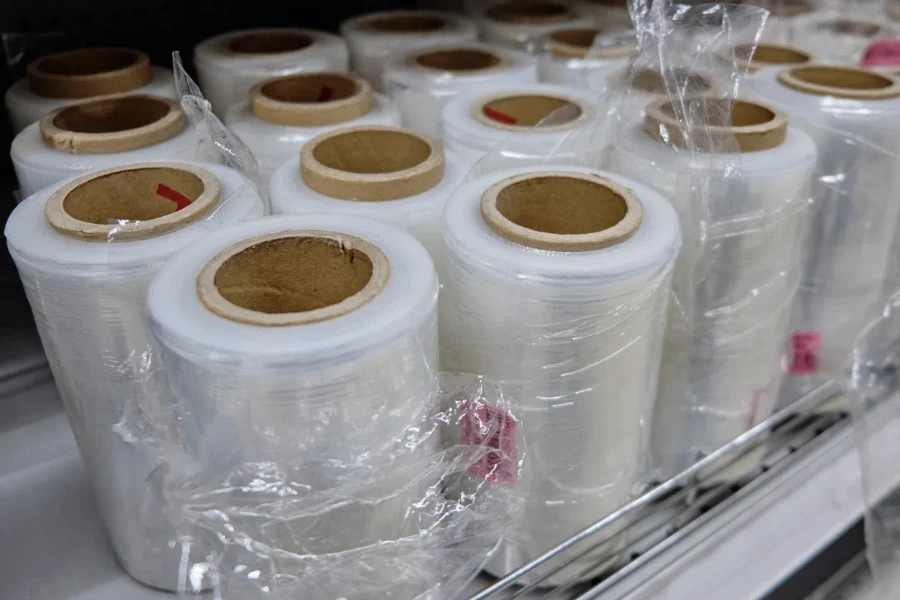
The cost of a stretch wrapper machine can vary widely depending on its features, capabilities, and brand. Entry-level models suitable for small to medium-sized operations may cost between $5,000 and $10,000, while high-end, fully automated machines for large-scale industrial use can exceed $50,000. It is important to consider the total cost of ownership, including initial purchase price, installation, maintenance, and operating costs, when planning a budget.
Financing options and leasing programs offered by manufacturers or suppliers can help manage the upfront costs. These programs allow businesses to spread the cost over time, making it more manageable and preserving capital for other investments. Additionally, some manufacturers offer trade-in programs for older machines, providing a cost-effective way to upgrade to newer models.
Investing in a high-quality stretch wrapper can yield significant long-term savings through improved efficiency, reduced film waste, and lower maintenance costs. Conducting a thorough cost-benefit analysis and considering the machine’s expected lifespan and potential return on investment can help make an informed purchasing decision.
Final Thoughts
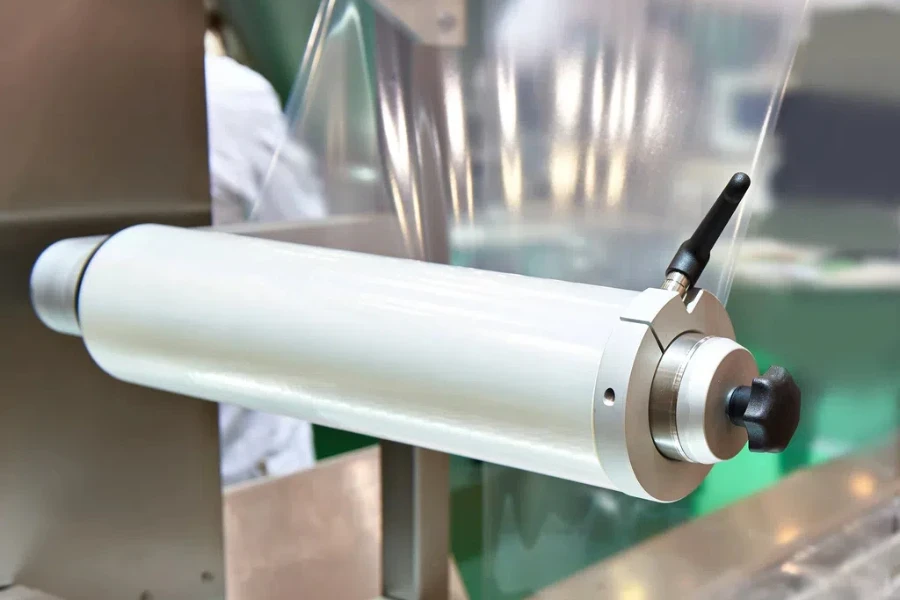
Selecting the right stretch wrapper machine involves careful consideration of various factors, including performance, durability, safety, compatibility, and cost. By evaluating these aspects and staying informed about the latest technological advancements, businesses can choose a machine that meets their specific needs and enhances their operational efficiency. Investing in a high-quality stretch wrapper not only improves productivity but also contributes to long-term cost savings and sustainability.