The surge in demand for sustainable and customized printing solutions has propelled the silk screen printing market to new heights. This article delves into the key aspects of selecting the right equipment, from performance and functionality to the latest technological advancements. Professional buyers will find valuable insights to aid in making informed purchasing decisions, ensuring efficiency and long-term success.
Table of Contents:
– Silk Screen Printing Market Overview
– Detailed Introduction and Analysis of the Silk Screen Printing Market
– Key Factors When Selecting Silk Screen Printing Equipment
– Latest Technology Features in Silk Screen Printing
– Compatibility with Future Upgrades
– Regulatory Compliance and Safety Standards
– Packaging Quality and Initial Setup Complexity
– Wrapping Up
Silk Screen Printing Market Overview
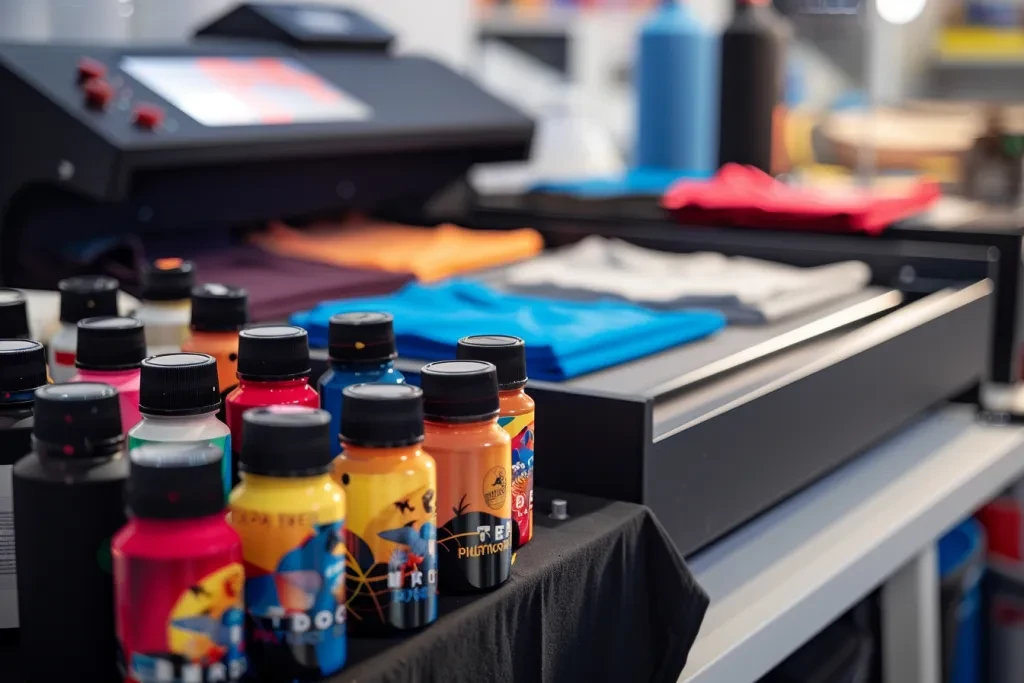
The global silk screen printing market has seen significant growth, reaching an estimated value of $3.9 billion recently, with projections to hit $11.2 billion by 2030. This growth represents a compound annual growth rate (CAGR) of 16.3%, driven by increasing demand in various industries such as textiles, electronics, and packaging. The U.S. market alone was valued at $993 million, highlighting its substantial contribution to the global market.
Key regions like China are expected to exhibit impressive growth rates, with a forecasted CAGR of 21.3%, potentially reaching $3.0 billion by 2030. The European market, including countries like Germany and the United Kingdom, also shows robust expansion, supported by technological advancements and a growing emphasis on sustainable printing practices. The textile printing segment is poised to grow significantly, with an estimated market size of 36.1 billion square meters by 2030.
Innovations in screen printing technology, such as automated and semi-automated machines, enhance production efficiency and output quality. The adoption of eco-friendly inks and substrates aligns with global sustainability trends, further driving market growth. The increasing popularity of personalized and custom-printed products also contributes to the rising demand for silk screen printing services.
Detailed Introduction and Analysis of the Silk Screen Printing Market
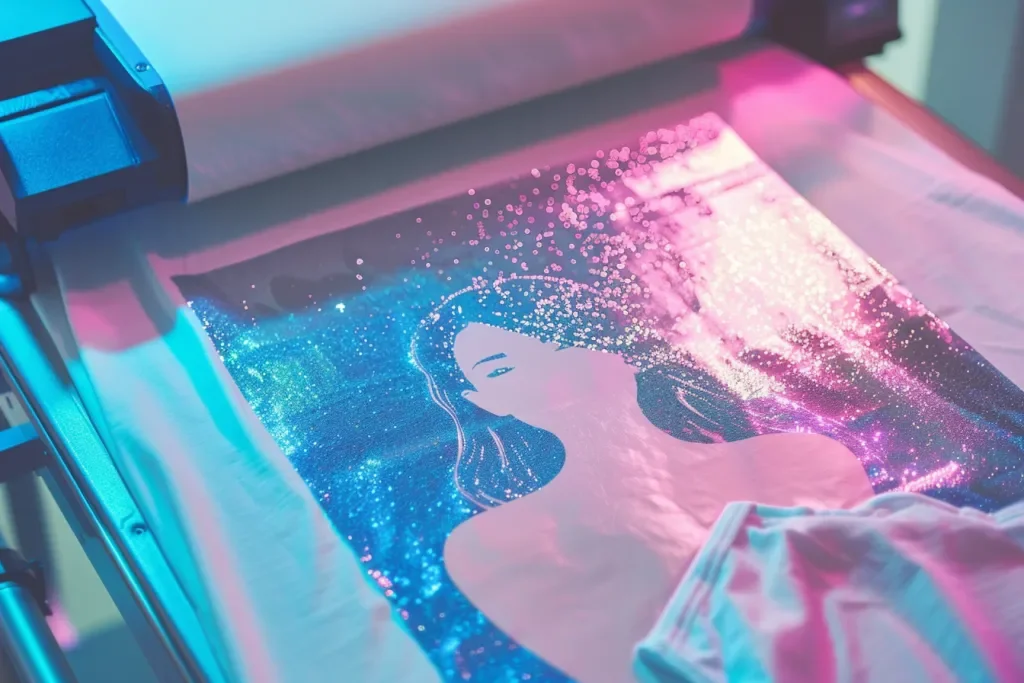
Silk screen printing, also known as serigraphy, is a versatile and durable printing method used for producing vibrant and long-lasting prints on materials like textiles, ceramics, glass, and metals. The process involves creating a stencil on a mesh screen and forcing ink through the open areas using a squeegee. This technique is highly valued for its ability to produce bold graphics and intricate designs, making it ideal for fashion, advertising, and electronics.
Key performance benchmarks in the silk screen printing market include precision, efficiency, and the ability to handle high-volume production. The introduction of automatic and semi-automatic screen printing machines has significantly improved these benchmarks, enabling faster production speeds and consistent quality. Major players like M&R Printing Equipment, Inc., and A.W.T. World Trade, Inc. dominate the industry, leveraging advanced technologies and extensive distribution networks.
Economic influences such as fluctuations in raw material costs and geopolitical tensions can impact market growth. However, the industry’s resilience is supported by continuous innovation and the adoption of sustainable practices. Consumer behavior shifts towards personalized and eco-friendly products also drive demand, with digital hybrid systems allowing for intricate designs and photorealistic details. The integration of digital and traditional screen printing techniques caters to niche markets, offering customization and short-run production capabilities.
Recent innovations include high-tension, low-elongation polyester and stainless-steel mesh materials, enhancing print accuracy and resolution. The use of water-based and UV-curable inks provides environmentally friendly alternatives to traditional solvent-based inks, aligning with global sustainability trends. The adoption of eco-friendly substrates, such as organic cotton and recycled plastics, further supports market growth.
Digitalization is another significant trend, with automated systems and IoT integration improving production efficiency and quality control. Social trends towards DIY culture and small-scale businesses have increased demand for entry-level screen printing equipment, allowing entrepreneurs to produce custom prints on demand. Customer pain points, such as the need for high initial investments and the complexity of automation implementation, are addressed through continuous training and support for workforce skills development.
Brand positioning strategies focus on differentiation through quality, innovation, and sustainability. Companies like Grafica Flextronica and H. G. Kippax & Sons Limited emphasize their commitment to eco-friendly practices and advanced technologies, appealing to environmentally conscious consumers. Differentiation strategies also include offering specialized services, such as the use of conductive inks for printed electronics and thermochromic inks for unique visual effects.
Key Factors When Selecting Silk Screen Printing Equipment
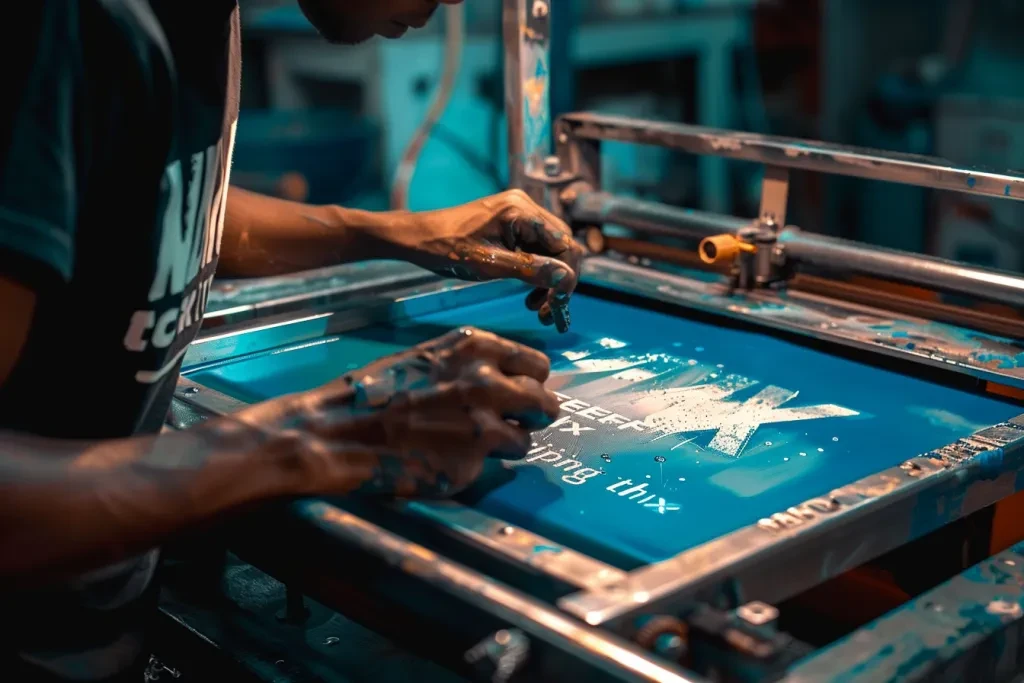
Choosing the right silk screen printing equipment is crucial for high-quality prints and efficient production. Consider these key factors:
Types of Silk Screen Printing Equipment
Understanding the different types of silk screen printing equipment is essential. Manual machines are suitable for small-scale operations, offering flexibility but requiring significant labor. Semi-automatic machines balance manual and automatic features, providing higher production rates with less manual intervention. Fully automatic machines are ideal for large-scale production, offering high-speed and consistent prints with minimal human input. The choice depends on production volume, budget, and specific printing needs.
Performance and Functionality
Performance and functionality are critical. The machine’s speed, precision, and ease of use impact overall efficiency. High-performance machines produce detailed and consistent prints faster. Advanced features like pre-registration systems and automatic squeegee adjustments reduce setup time and increase productivity. Ease of operation and maintenance are also important, as complex machines may need skilled operators and frequent servicing.
Technical Specifications
Technical specifications such as screen size, printing area, and ink compatibility are vital. The screen size should match the substrate dimensions. The printing area determines the maximum design size. Ink compatibility is crucial, as different machines may require specific inks like plastisol, water-based, or discharge inks. Ensuring compatibility prevents issues like clogging and poor print quality.
Materials and Build Quality
The materials and build quality affect durability and longevity. Machines made from high-quality materials like stainless steel and aluminum are more resistant to wear and corrosion, ensuring a longer lifespan. Robust build quality contributes to consistent performance, reducing breakdowns and repair needs. Investing in well-built equipment can lead to long-term cost savings and uninterrupted production.
Price Range and Budget
Pricing is a significant factor. The cost varies based on type, features, and brand. Manual machines are generally more affordable, while fully automatic machines can be expensive. Balance the budget with required features and production capacity. Consider the total cost of ownership, including maintenance and operating costs, for a more accurate investment assessment.
Latest Technology Features in Silk Screen Printing

Digital Integration
Modern silk screen printing machines increasingly integrate digital technologies to enhance precision and efficiency. Digital interfaces allow for easier control and monitoring, enabling on-the-fly adjustments. Advanced machines may include digital prepress systems that automate screen alignment and registration, reducing setup time and minimizing errors.
Eco-Friendly Inks and Processes
The industry is moving towards sustainable practices with eco-friendly inks and processes. Water-based and soy-based inks are gaining popularity due to their lower environmental impact compared to traditional plastisol inks. New curing technologies like LED UV curing are more energy-efficient and produce less heat, reducing energy consumption and improving workplace safety.
Automation and Robotics
Automation is revolutionizing silk screen printing, with robotic systems handling repetitive tasks like screen loading, ink application, and product unloading. This increases production speed and ensures consistent quality by eliminating human error. Fully automated lines can operate continuously with minimal supervision, ideal for large-scale production.
Compatibility with Future Upgrades
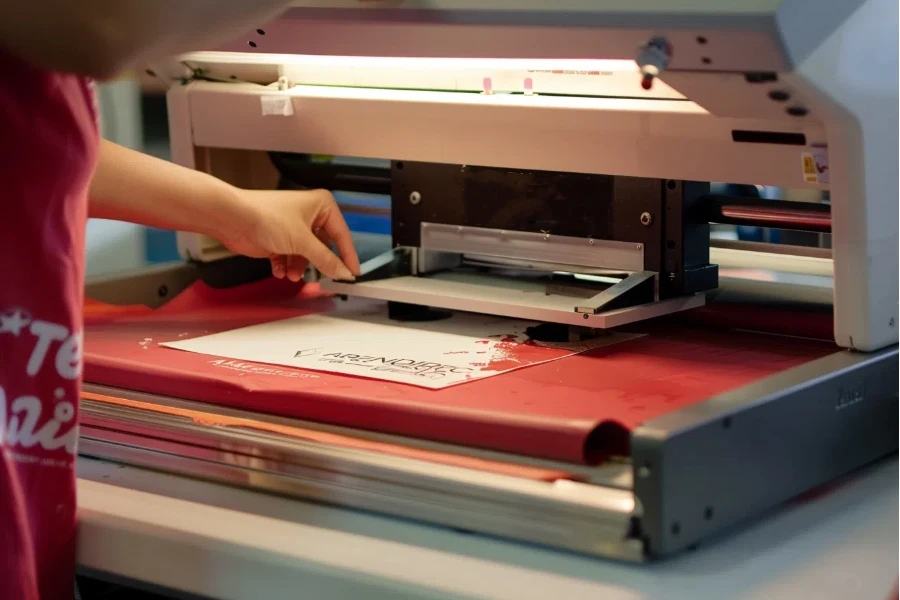
Modular Designs
Many modern silk screen printing machines feature modular components, allowing for easy upgrades and customization. This modularity lets businesses adapt equipment to changing production needs without investing in new machines. Adding additional printing heads or automated systems can increase capacity and functionality.
Software Updates
Software plays a crucial role in digital silk screen printing equipment. Regular updates can enhance performance, introduce new features, and improve compatibility with other devices. Manufacturers often provide updates to keep equipment up-to-date with technological advancements and industry standards.
Integration with Other Systems
Compatibility with other production systems is essential for a seamless workflow. Modern silk screen printing machines can integrate with ERP (Enterprise Resource Planning) and MIS (Management Information Systems) to streamline production management, inventory control, and order processing. This integration facilitates better coordination and efficiency across the production line.
Regulatory Compliance and Safety Standards
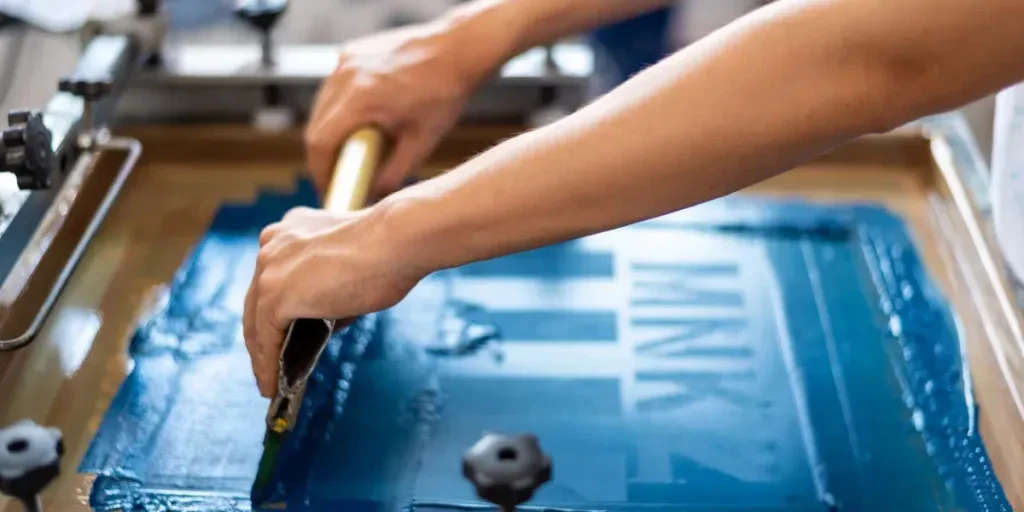
Industry Standards
Compliance with industry standards and regulations is crucial for safety and reliability. Machines should meet standards set by organizations like OSHA (Occupational Safety and Health Administration) and CE (Conformité Européenne). These standards ensure the equipment is safe to operate and meets quality benchmarks.
Safety Features
Modern silk screen printing machines include various safety features to protect operators and prevent accidents. Safety guards, emergency stop buttons, and interlock systems are common safety mechanisms. Machines with lower noise levels and reduced emissions contribute to a safer and more comfortable working environment.
Certifications
Certifications from recognized bodies assure the equipment’s quality and compliance with safety standards. For example, ISO (International Organization for Standardization) certification demonstrates adherence to international quality management and safety practices. Investing in certified equipment reduces the risk of non-compliance and enhances production credibility.
Packaging Quality and Initial Setup Complexity
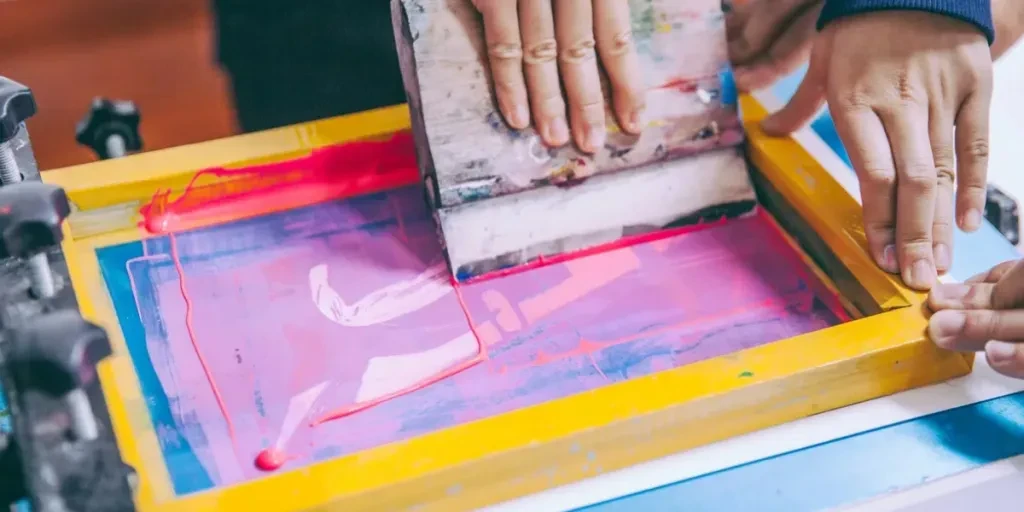
Protective Packaging
The quality of packaging significantly impacts the condition of the equipment upon delivery. High-quality packaging protects the machine from damage during transit, ensuring it arrives in perfect working condition. Protective materials like foam inserts, sturdy boxes, and shrink wrap safeguard delicate components.
Setup and Installation
The complexity of initial setup and installation affects the time to get the equipment operational. Machines with detailed manuals, video tutorials, and manufacturer support simplify the setup process. Some manufacturers offer on-site installation and training services, ensuring correct setup and operator training.
User-Friendly Interfaces
User-friendly interfaces and intuitive controls make it easier for operators to learn and operate the equipment. Touchscreen panels, clear display screens, and straightforward navigation menus reduce the learning curve and minimize operational errors. Investing in machines with user-friendly interfaces can enhance productivity and reduce downtime.
Wrapping Up
Selecting the right silk screen printing equipment involves careful consideration of various factors such as types, performance, technical specifications, materials, budget, latest technology features, future upgrade potential, regulatory compliance, and packaging quality. By thoroughly evaluating these aspects, businesses can make informed decisions that align with their production needs and long-term goals.