Circular knitting machines are experiencing a surge in demand in 2025, driven by advancements in technology and the growing apparel industry. This article delves into an in-depth analysis of the circular knitting machine market, including types, performance, design, technical specifications, and more. Professional buyers will find valuable insights and guidance to make informed purchasing decisions, ensuring high-quality and efficient production processes.
Table of Contents:
– Circular Knitting Machine Market Overview
– Detailed Analysis of the Circular Knitting Machine Market
– Key Factors When Selecting a Circular Knitting Machine
– Advanced Technology Features in Circular Knitting Machines
– Durability and Quality Assurance
– Conclusion
Circular Knitting Machine Market Overview
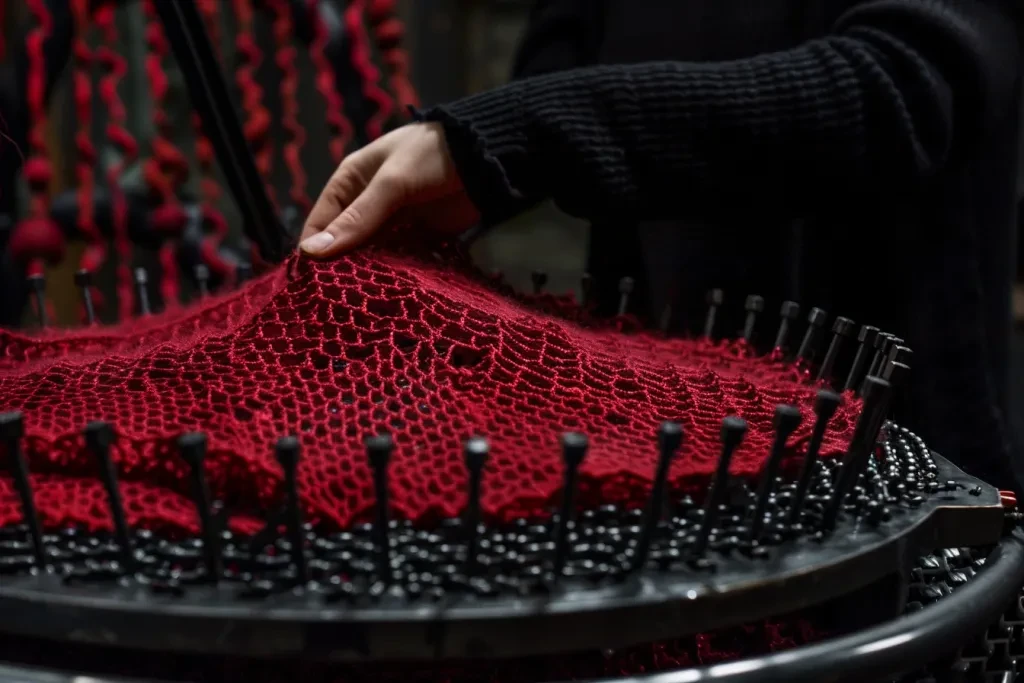
The global circular knitting machine market has shown robust growth in 2024. It is projected to reach USD 7.8 billion by 2030, expanding at a compound annual growth rate (CAGR) of 6.9% from 2024 to 2030. The demand for circular knitting machines is driven by the growing apparel industry, which needs efficient, high-speed knitting solutions to meet the increasing consumer demand for knitted garments.
Asia-Pacific is the largest market for circular knitting machines, accounting for over 45% of the global market share. This dominance is due to the significant textile manufacturing base in countries like China, India, and Bangladesh. The adoption of advanced circular knitting machines, featuring automated control systems and high-speed operation, is expected to enhance production efficiency and drive market growth.
In North America and Europe, there is a shift towards customized and high-quality knitwear, increasing the demand for technologically advanced circular knitting machines. The focus on sustainability and the use of eco-friendly materials in textile production also contribute to market expansion in these regions.
Detailed Analysis of the Circular Knitting Machine Market
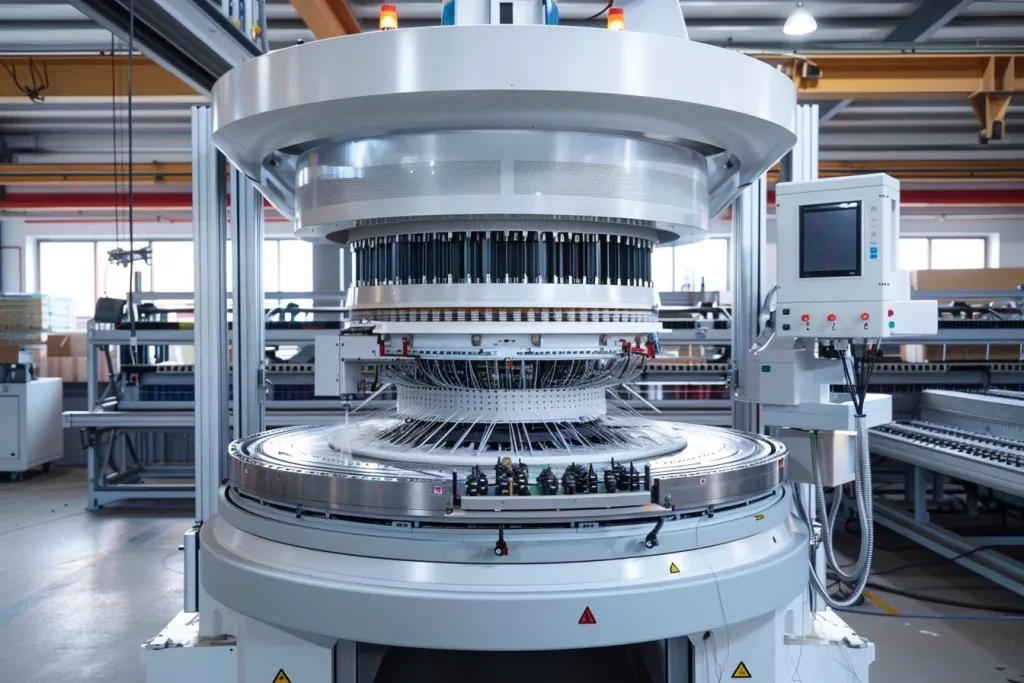
Circular knitting machines are crucial in the textile industry, offering high productivity and versatility in producing various knitted fabrics. These machines are classified by diameter, gauge, and the type of fabric they produce, such as single jersey, double jersey, and jacquard. The single jersey segment holds the largest market share due to its widespread use in manufacturing T-shirts, sportswear, and casual wear.
Market dynamics are influenced by factors like technological advancements, economic conditions, and shifts in consumer behavior. Recent innovations include digital control systems that enhance precision and reduce downtime. This trend towards digitalization is expected to continue, with manufacturers investing in IoT-enabled machines for real-time monitoring and predictive maintenance.
The economic landscape plays a crucial role, with fluctuations in raw material prices and labor costs impacting profitability. Manufacturers are seeking cost-effective solutions, such as high-speed circular knitting machines that optimize production efficiency. Additionally, the growing preference for sustainable and ethically produced textiles is pushing manufacturers to adopt eco-friendly practices and materials.
Distribution channels for circular knitting machines include direct sales, distributors, and online platforms. Direct sales dominate, accounting for approximately 60% of the market share, as they offer personalized service and support. However, online sales are gaining traction due to the increasing digitalization of the manufacturing sector and the convenience of online purchasing.
Circular knitting machines are in the growth stage of their product lifecycle, with continuous innovations and upgrades being introduced to meet the evolving demands of the textile industry. The market is characterized by intense competition, with key players focusing on brand positioning and differentiation strategies. Companies are investing in R&D to develop machines with advanced features, such as automatic yarn feeders and waste reduction systems, to gain a competitive edge.
Customer pain points mainly involve machine maintenance and operational efficiency. To address these issues, manufacturers are offering comprehensive after-sales services, including training programs and technical support. Additionally, niche markets, such as medical textiles and smart fabrics, are emerging, presenting new growth opportunities for circular knitting machine manufacturers.
Overall, the circular knitting machine market is set for significant growth, driven by technological advancements, economic influences, and evolving consumer preferences. With ongoing innovations and a focus on sustainability, the market is expected to continue its upward trajectory in the coming years.
Key Factors When Selecting a Circular Knitting Machine
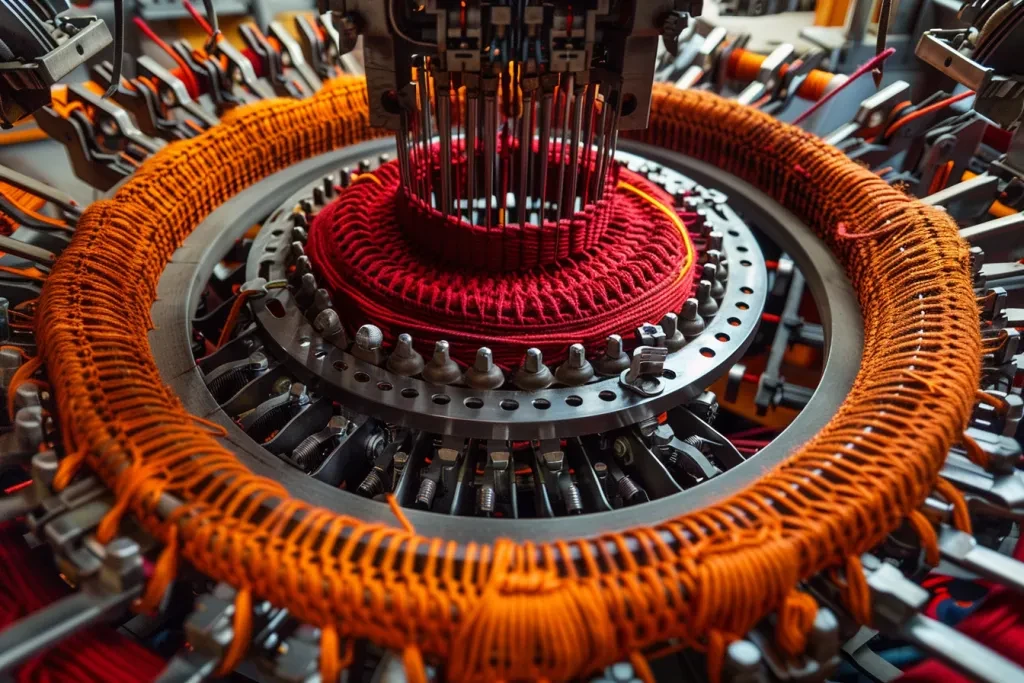
Choosing the right circular knitting machine can be a complex task, requiring an evaluation of several technical and operational aspects. These factors are crucial to ensure the machine meets the specific needs of your production process and delivers high-quality output. Below are the key factors to consider.
Types and Styles of Circular Knitting Machines
Circular knitting machines come in various types and styles, each designed for specific applications and fabric types. The three main types are single jersey, double jersey, and jacquard machines.
Single jersey machines are ideal for producing lightweight, stretchy fabrics. They use a single set of needles and are typically employed to create t-shirts, innerwear, and sportswear. Their simple design allows for high-speed production and ease of maintenance.
Double jersey machines have two sets of needles, enabling them to create thicker, more stable fabrics with less stretch. They are commonly used for producing outerwear, sweaters, and heavier garments. These machines offer more versatility in pattern creation but tend to be more complex and expensive.
Jacquard circular knitting machines are equipped with advanced needle selection mechanisms, allowing them to produce intricate patterns and designs. These machines are suitable for high-end fashion garments and home textiles. They are the most sophisticated and costly among the three types, requiring specialized knowledge for operation and maintenance.
Performance and Functionality
The performance and functionality of a circular knitting machine are critical to ensuring efficient and high-quality production. Key performance indicators include speed, precision, and versatility.
The speed of a circular knitting machine is measured in revolutions per minute (RPM). High-speed machines can operate at up to 40 RPM, significantly increasing production capacity. However, higher speeds may lead to increased wear and tear, necessitating more frequent maintenance.
Precision in needle movement and yarn feeding is essential for producing consistent fabric quality. Advanced electronic controls and servo motors enhance precision, reducing the likelihood of defects and improving overall product quality.
Versatility refers to the machine’s ability to handle different yarn types, diameters, and fabric structures. Machines with interchangeable cylinders and cams offer greater flexibility, enabling manufacturers to switch between different production requirements with minimal downtime.
An ergonomically designed machine reduces operator fatigue and increases productivity. Features such as adjustable control panels, easy-to-reach maintenance points, and clear visibility of the knitting area contribute to better ergonomics.
Modern circular knitting machines are equipped with touch-screen interfaces that provide intuitive control over machine settings. These interfaces often include diagnostic tools, production monitoring, and pattern programming capabilities, simplifying the operation process.
Space is often a constraint in manufacturing facilities. Compact machines that maximize production capacity while minimizing floor space usage are highly desirable. Additionally, machines with modular designs allow for easier expansion and reconfiguration of production lines.
Technical Specifications
Technical specifications provide a detailed understanding of a circular knitting machine’s capabilities and limitations. Important specifications include gauge, diameter, and needle count.
The gauge of a circular knitting machine refers to the number of needles per inch. Higher gauge machines produce finer fabrics, while lower gauge machines are suitable for thicker, coarser fabrics. Common gauges range from 14 to 28, with some specialized machines offering gauges as high as 32.
The diameter of the knitting cylinder determines the width of the fabric that can be produced. Machines with larger diameters (up to 60 inches) are used for wide-width fabrics, while smaller diameters (down to 20 inches) are suitable for narrow fabrics and tubular knits.
The total number of needles on the machine affects production capacity and fabric quality. Machines with higher needle counts can produce larger quantities of fabric more quickly, but they may also require more frequent maintenance and adjustments.
Price Range and Budget
The cost of a circular knitting machine is a significant factor for any business. Prices can vary widely based on the machine’s type, features, and brand.
Basic single jersey machines can start from $10,000 to $20,000. These machines are suitable for small-scale production and limited fabric types.
Double jersey and basic jacquard machines typically range from $30,000 to $60,000. These machines offer a good balance of performance, versatility, and cost.
Advanced jacquard machines with sophisticated electronic controls and high-speed capabilities can cost upwards of $100,000. These machines are ideal for large-scale production and high-quality fabric requirements.
Materials and Build Quality
The materials and build quality of a circular knitting machine directly impact its durability, maintenance needs, and overall performance.
High-quality machines are built with robust frames made from cast iron or high-grade steel, ensuring stability and longevity. Critical components such as cams, needles, and sinkers should be made from wear-resistant materials to minimize downtime and maintenance costs.
Reliable yarn feeding and tension systems are essential for consistent fabric quality. Machines equipped with advanced yarn tension controllers and feeders that can handle a wide range of yarn types and thicknesses offer greater flexibility and better performance.
Proper lubrication and cooling systems are crucial for maintaining the machine’s performance and preventing overheating. Automated lubrication systems and efficient cooling mechanisms help extend the machine’s lifespan and reduce maintenance requirements.
Advanced Technology Features in Circular Knitting Machines
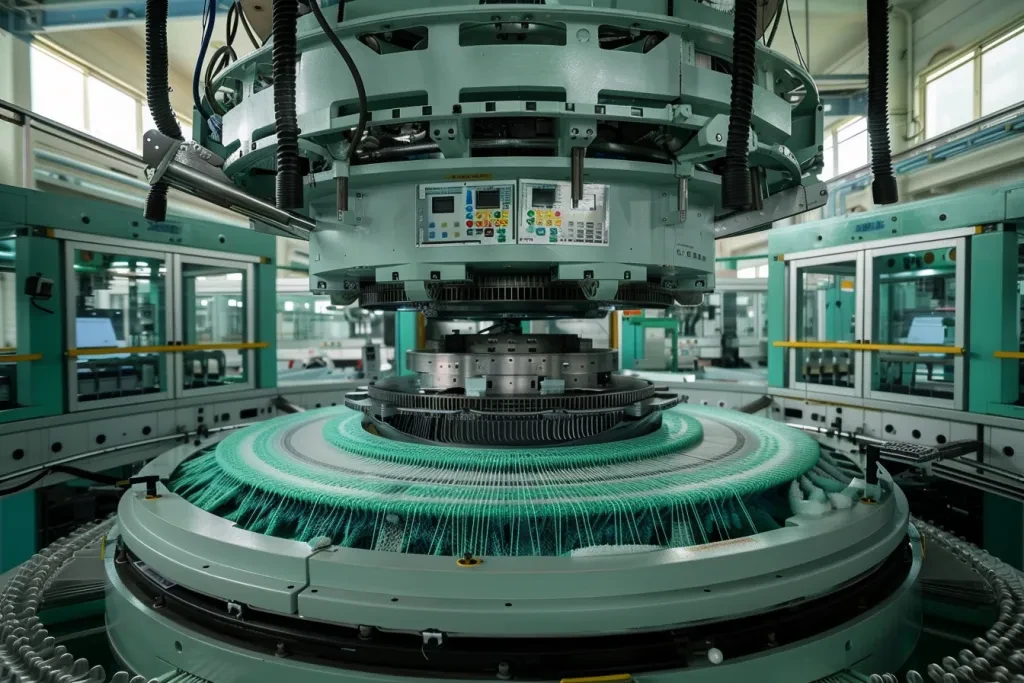
Circular knitting machines have seen significant technological advancements, making them more efficient, versatile, and user-friendly. These features enhance production capabilities and open up new possibilities for fabric design and manufacturing.
Computerized Control Systems
Modern circular knitting machines are equipped with computerized control systems that offer precise control over various machine functions. These systems use advanced algorithms to optimize knitting patterns, tension, and speed.
Computerized control systems allow operators to program complex patterns directly into the machine. This feature is particularly beneficial for jacquard machines, enabling the production of intricate designs with high precision.
These systems provide real-time monitoring of machine performance, including production speed, fabric quality, and error detection. Operators can quickly identify and address issues, minimizing downtime and ensuring consistent quality.
Some advanced machines offer remote access capabilities, allowing operators to monitor and control the machine from a distance. This feature enhances flexibility and enables quick responses to any production issues, even when operators are not physically present at the machine.
Energy Efficiency
Energy efficiency is a critical consideration for modern circular knitting machines, given the increasing focus on sustainability and cost reduction.
The use of servo motors in circular knitting machines enhances energy efficiency by providing precise control over needle movement and yarn feeding. Servo motors consume less energy compared to traditional motors, reducing overall energy consumption.
Variable speed drives (VSDs) allow machines to operate at optimal speeds for different fabric types and production requirements. By adjusting the speed based on the specific needs of each production run, VSDs help minimize energy usage and improve machine efficiency.
Some machines are equipped with energy-saving modes that automatically reduce power consumption during idle periods. These modes help lower energy costs and contribute to a more sustainable production process.
Integration with Industry 4.0
The integration of circular knitting machines with Industry 4.0 technologies has revolutionized the textile industry, enabling smarter and more connected manufacturing processes.
Internet of Things (IoT) connectivity allows circular knitting machines to communicate with other equipment and systems within the production facility. This connectivity enables seamless data exchange, improving coordination and efficiency across the production line.
IoT-enabled machines can collect and analyze data on machine performance and wear patterns. This data is used to predict maintenance needs, allowing operators to perform maintenance proactively and prevent unexpected breakdowns.
Advanced data analytics tools provide valuable insights into production trends, machine efficiency, and fabric quality. By leveraging these insights, manufacturers can optimize their processes, reduce waste, and enhance overall productivity.
Durability and Quality Assurance
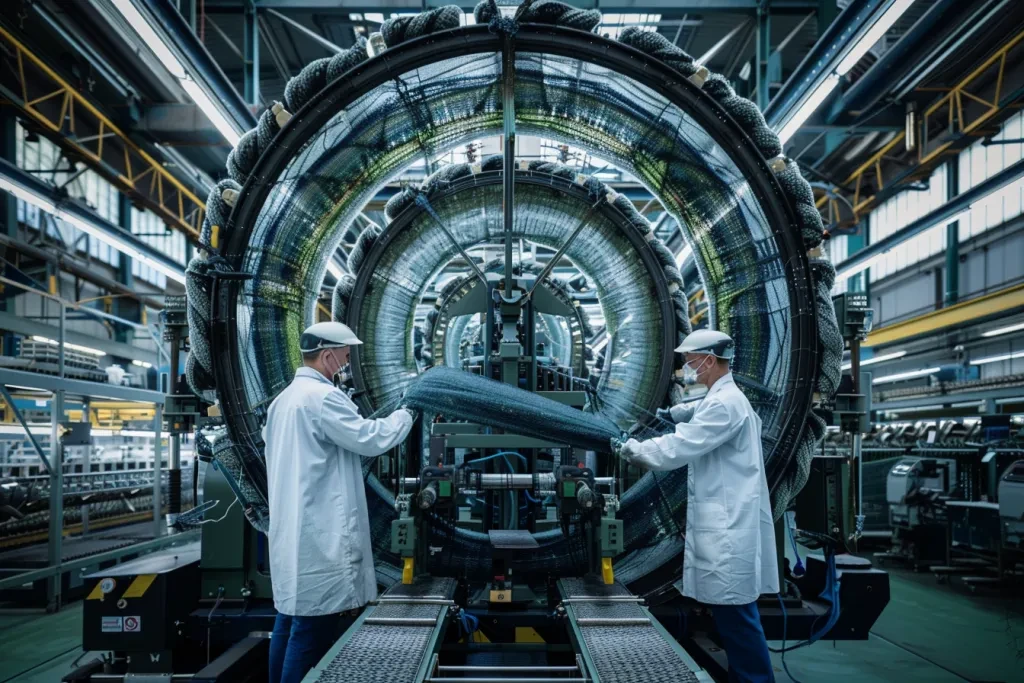
Durability and quality assurance are essential factors in the selection of circular knitting machines. High-quality machines offer longer lifespans, reduced maintenance costs, and consistent fabric quality.
Build Quality and Materials
The build quality and materials used in the construction of circular knitting machines play a crucial role in their durability and performance.
Machines with robust construction, using high-grade materials such as cast iron or stainless steel, offer greater stability and longevity. These materials provide resistance to wear and tear, ensuring that the machine can withstand the demands of continuous production.
High-quality components, such as cams, needles, and sinkers, are essential for maintaining consistent fabric quality. These components should be made from wear-resistant materials and manufactured to precise tolerances to ensure reliable performance.
Some machines come with protective coatings on critical components to prevent corrosion and reduce friction. These coatings help extend the lifespan of the machine and maintain its performance over time.
Certification and Compliance
Certification and compliance with industry standards are important indicators of a machine’s quality and reliability.
ISO certification ensures that the machine meets international standards for quality management and production processes. Machines with ISO certification are manufactured to high standards, providing assurance of their quality and performance.
CE marking indicates that the machine complies with European safety, health, and environmental protection standards. This certification is essential for machines used in the European market and provides assurance of their safety and reliability.
UL certification ensures that the machine meets safety standards set by Underwriters Laboratories. This certification is important for machines used in the North American market and provides assurance of their safety and compliance with regulatory requirements.
Maintenance and Support
Regular maintenance and access to support services are crucial for ensuring the long-term performance and reliability of circular knitting machines.
Manufacturers often provide recommended maintenance schedules for their machines, outlining routine tasks such as lubrication, cleaning, and inspection. Adhering to these schedules helps prevent unexpected breakdowns and extends the machine’s lifespan.
Access to spare parts is essential for maintaining the machine’s performance and minimizing downtime. Manufacturers that offer a comprehensive range of spare parts and quick delivery times provide valuable support for ongoing machine maintenance.
Technical support services, including remote assistance and on-site visits, are crucial for addressing any issues that arise during machine operation. Manufacturers that offer responsive and knowledgeable support teams help ensure that any problems are resolved quickly and effectively.
Conclusion
In summary, selecting the right circular knitting machine involves careful consideration of various factors, including types and styles, performance and functionality, technical specifications, price range and budget, materials and build quality, advanced technology features, and durability and quality assurance. By evaluating these factors and understanding the specific needs of your production process, you can make an informed decision that ensures efficient and high-quality fabric production.