In 2025, the foam wire cutter market continues to innovate, driven by the demand for precision and efficiency in various industries. This article provides an in-depth analysis of foam wire cutter types, performance metrics, technical specifications, safety standards, and the latest technological advancements. It aims to assist professional buyers in making informed decisions to enhance their business operations.
Table of Contents:
– Foam Wire Cutter Market Overview
– Detailed Analysis of the Foam Wire Cutter Market
– Key Factors When Selecting a Foam Wire Cutter
– Latest Technology Features in Foam Wire Cutters
– Considerations for Foam Wire Cutter Accessories
– Conclusion
Foam Wire Cutter Market Overview
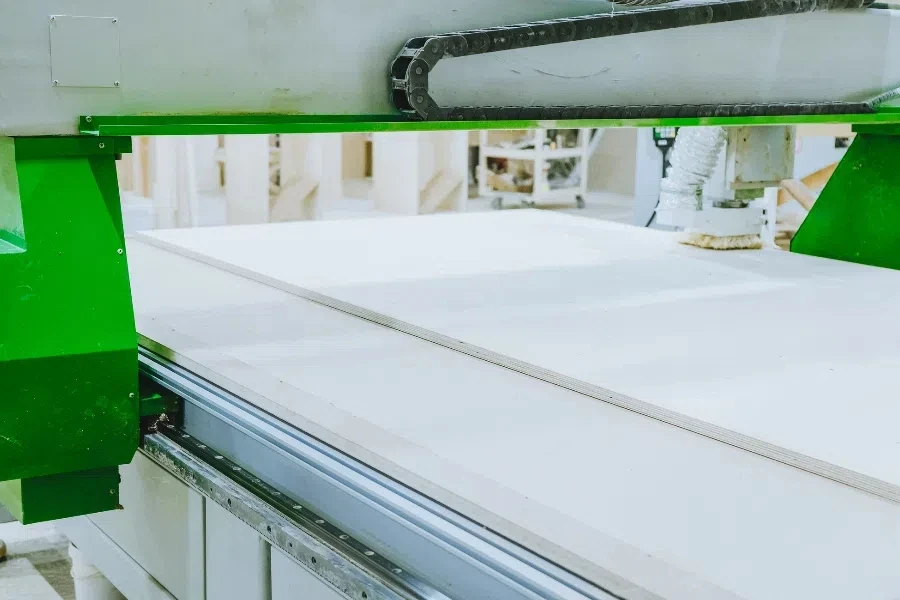
The foam wire cutter market has seen substantial growth, driven by advancements in technology and increasing demand from various industries. In 2024, the market size was estimated at USD 1.45 billion and is projected to grow at a CAGR of 4.7%, reaching USD 1.93 billion by 2030. The market is segmented by material type, application, and region, with significant contributions from the Americas, Asia-Pacific, and EMEA regions.
In terms of material type, aluminum and stainless steel dominate, accounting for over 60% of the market share. The increasing use of foam wire cutters in the automotive, aerospace, and construction industries is a major growth driver. Additionally, the demand for precision cutting tools in the electronics and packaging industries has further fueled market expansion.
The Asia-Pacific region is expected to witness the highest growth rate, with China, Japan, and India being the primary contributors. Rapid industrialization, infrastructure development, and the expansion of the automotive and construction sectors are key factors driving the market in this region. In the Americas, the United States holds the largest market share, driven by technological advancements and high demand from the manufacturing sector.
Detailed Analysis of the Foam Wire Cutter Market
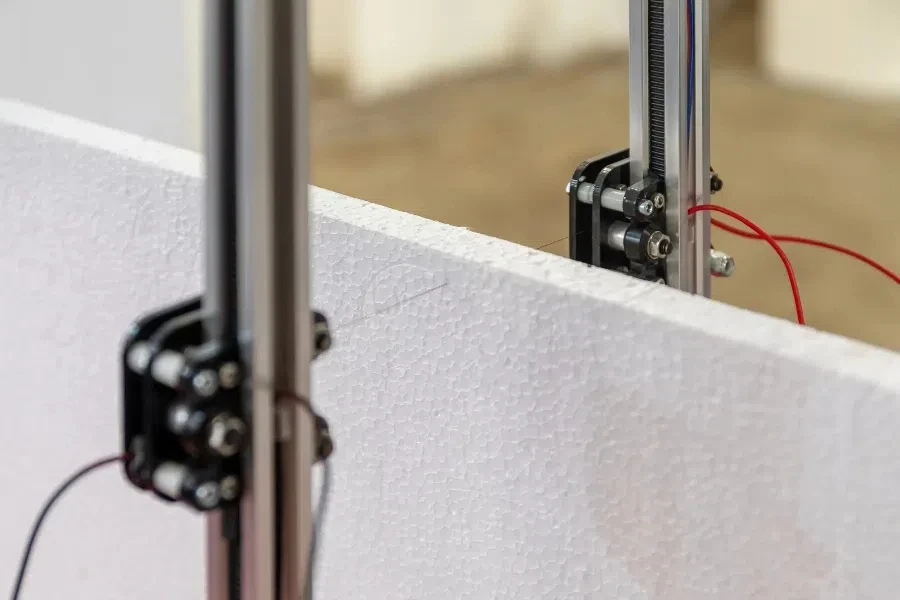
The foam wire cutter market is characterized by diverse applications and numerous market players. Key performance benchmarks include cutting precision, operational efficiency, and durability. The market is highly competitive, with major players like Loffler GmbH & Co. KG, Metaltec Castings LLC, and Sinto Group holding significant market shares.
Economic influences such as fluctuating raw material prices and strict environmental regulations have impacted market dynamics. However, the increasing focus on automation and digitalization in manufacturing has led to innovations in foam wire cutter technology. For instance, the development of CNC foam cutters has enhanced precision and efficiency, reducing operational costs and increasing productivity.
Consumer behavior has shifted towards eco-friendly and recyclable materials, driving demand for sustainable foam wire cutters. The distribution channel preferences have evolved, with a growing inclination towards online platforms for procurement, supported by the convenience and wide range of options available through e-commerce.
Recent innovations in the market include high-speed wire cutters and advanced software integration for better control and accuracy. The product lifecycle stages indicate a mature market with continuous innovations to meet evolving customer needs. Digitalization has played a crucial role in enhancing product features and customer experience.
Social trends such as the rise in DIY projects and the increasing popularity of custom foam designs have also contributed to market growth. However, customer pain points such as high initial costs and maintenance requirements remain challenges for market players. To address these issues, companies are focusing on brand positioning strategies that emphasize durability, ease of use, and cost-effectiveness.
Differentiation strategies include offering customizable solutions and providing value-added services such as training and technical support. Niche markets such as the medical and aerospace sectors present significant opportunities for growth, given their specific requirements for precision and reliability.
Key Factors When Selecting a Foam Wire Cutter
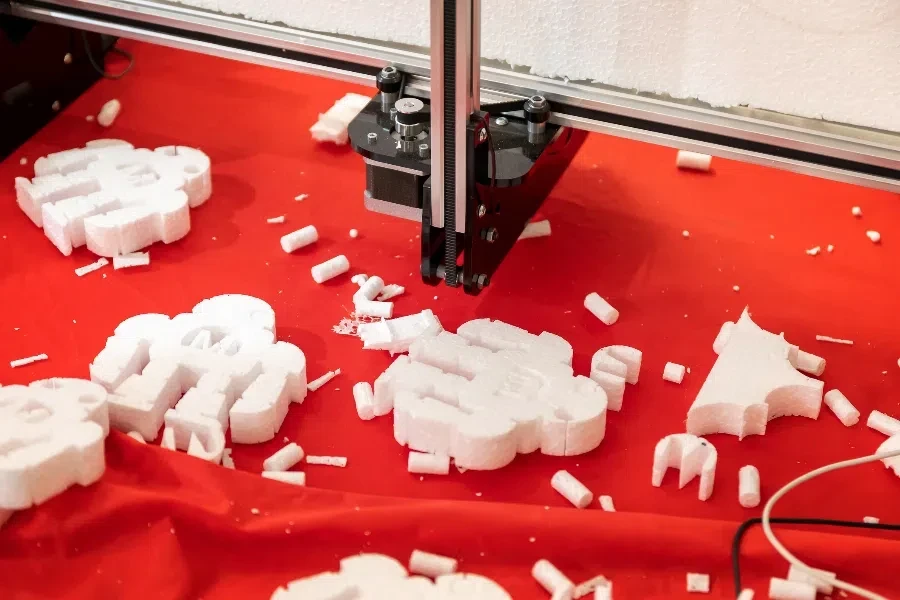
Types of Foam Wire Cutters
Foam wire cutters come in various types, each designed for specific applications. The most common types include handheld, benchtop, and CNC (Computer Numerical Control) foam cutters. Handheld foam cutters are portable and ideal for small projects or on-the-go tasks. Benchtop models provide a stable cutting platform and are suitable for medium-scale operations. CNC foam cutters offer high precision and are used for large-scale industrial applications, where intricate designs and high-volume production are required.
Handheld foam cutters often feature adjustable temperature settings, allowing the user to control the cutting speed and precision. They are lightweight and easy to maneuver but may lack the stability needed for larger projects. Benchtop foam cutters provide a fixed cutting surface, enhancing accuracy and consistency. These models are equipped with powerful motors and can handle thicker foam materials.
CNC foam cutters represent the pinnacle of precision and automation in foam cutting technology. They are equipped with advanced software for complex design inputs and automated cutting processes. These machines produce highly detailed and intricate cuts, making them ideal for industries such as packaging, automotive, and aerospace.
Performance and Functionality
The performance of a foam wire cutter depends on several factors, including cutting speed, precision, and versatility. Cutting speed refers to how quickly the cutter can move through the foam material. High-performance cutters achieve faster speeds without compromising accuracy, crucial for high-volume production environments.
Precision is critical for applications requiring intricate designs or tight tolerances. The precision of a foam wire cutter is influenced by the quality of the cutting wire, the stability of the cutting platform, and the control system. High-quality cutting wires made from materials such as nichrome or tungsten provide clean and precise cuts, reducing the need for additional finishing.
Versatility refers to the cutter’s ability to handle different foam materials and varying thicknesses. A versatile foam wire cutter should cut through materials such as polystyrene, polyurethane, and polyethylene foam. Adjustable cutting parameters accommodate different material densities and thicknesses.
Technical Specifications
When selecting a foam wire cutter, consider the technical specifications that determine its capabilities. Key specifications include cutting area, wire temperature range, power consumption, and control system. The cutting area refers to the maximum dimensions of the foam material that the cutter can handle. Larger cutting areas are beneficial for industrial applications, allowing for the cutting of large foam blocks or sheets.
The wire temperature range is crucial for achieving the desired cutting performance. Adjustable temperature settings optimize cutting speed and precision for different foam materials. Power consumption affects the operational cost and efficiency of the cutter. Energy-efficient models reduce electricity costs and minimize environmental impact.
The control system of a foam wire cutter determines its ease of use and precision. Advanced models feature digital control systems with programmable settings, allowing for automated and repeatable cutting processes. Some models also offer remote control capabilities, enabling the user to operate the cutter from a distance or integrate it into an automated production line.
Safety Standards and Certifications
Safety is paramount when selecting a foam wire cutter. Choose a cutter that complies with relevant safety standards and certifications. These standards ensure the cutter is designed and manufactured to minimize the risk of accidents and injuries. Common safety features include emergency stop buttons, thermal protection, and insulated handles.
Certifications from organizations such as UL (Underwriters Laboratories), CE (Conformité Européenne), and ISO (International Organization for Standardization) indicate that the cutter has undergone rigorous testing and meets industry-specific safety and quality standards. Additionally, look for cutters that offer comprehensive user manuals and safety guidelines to ensure proper operation and maintenance.
Durability and Build Quality
The durability and build quality of a foam wire cutter influence its lifespan and reliability. A well-built cutter made from high-quality materials can withstand frequent use and harsh operating conditions. Key components such as the cutting wire, frame, and motor should be constructed from durable materials to ensure long-term performance.
Stainless steel and aluminum are commonly used for the frame and cutting wire, offering excellent strength and corrosion resistance. The motor should be powerful enough to handle the cutting tasks without overheating or wearing out prematurely. Additionally, the cutter should feature robust construction with reinforced joints and connections to prevent damage and ensure stability during operation.
Latest Technology Features in Foam Wire Cutters

Automated Cutting Systems
The integration of automated cutting systems in foam wire cutters has revolutionized the industry, providing unmatched precision and efficiency. Automated systems utilize advanced software and CNC technology to control the cutting process, allowing for the creation of complex shapes and designs with minimal human intervention. These systems feature automatic wire tensioning, real-time monitoring, and error detection, ensuring consistent and high-quality cuts.
Automated cutting systems also offer programmability, enabling users to save and recall cutting profiles for repetitive tasks. This feature is particularly beneficial for mass production environments, where consistency and speed are critical. Additionally, automated systems can be integrated with other production equipment, such as conveyor belts and robotic arms, to create a fully automated production line.
Advanced Control Interfaces
Modern foam wire cutters are equipped with advanced control interfaces that enhance usability and precision. Touchscreen interfaces provide an intuitive and user-friendly platform for controlling the cutter. These interfaces allow users to easily adjust cutting parameters, monitor the cutting process, and troubleshoot issues. Some models also offer remote control capabilities, enabling operators to manage the cutter from a distance using a smartphone or tablet.
Other advanced control features include programmable logic controllers (PLCs) and human-machine interfaces (HMIs). PLCs provide precise control over the cutting process, allowing for the execution of complex cutting sequences and the integration of additional sensors and actuators. HMIs offer a visual representation of the cutting process, providing real-time feedback and allowing for quick adjustments to improve cutting accuracy and efficiency.
Energy-Efficient Technologies
Energy efficiency is a growing concern in the machinery industry, and foam wire cutters are no exception. Manufacturers are increasingly incorporating energy-efficient technologies to reduce power consumption and minimize environmental impact. One such technology is the use of variable frequency drives (VFDs) to control the motor speed. VFDs adjust the motor speed based on the cutting load, reducing energy consumption during low-load operations and extending the motor’s lifespan.
Another energy-efficient feature is the use of high-efficiency heating elements for the cutting wire. These elements provide rapid heating and precise temperature control, reducing the time required to reach the optimal cutting temperature and minimizing energy waste. Additionally, some models incorporate regenerative braking systems that recover and store energy during deceleration, further improving energy efficiency.
Considerations for Foam Wire Cutter Accessories
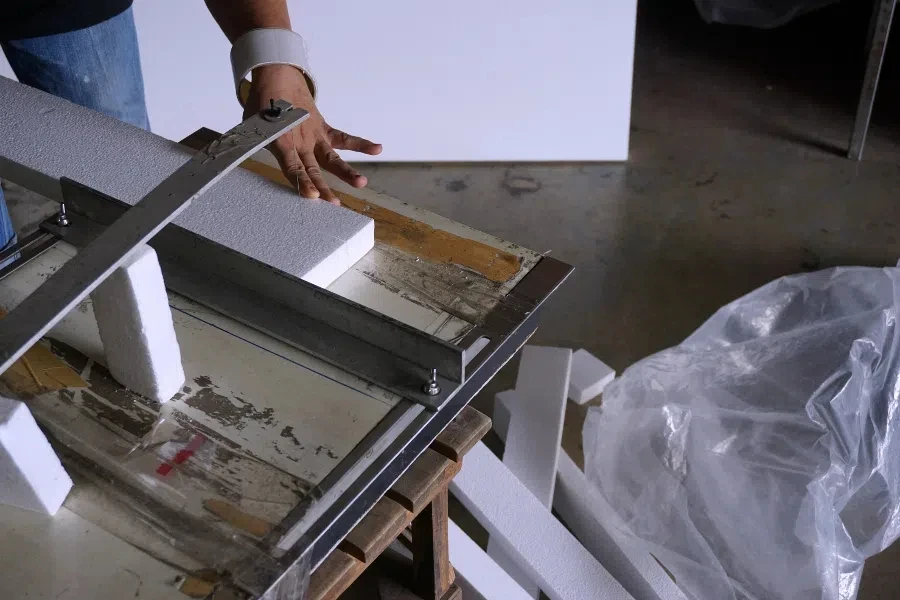
Replacement Cutting Wires
Replacement cutting wires are essential accessories for foam wire cutters, as the cutting wire is subject to wear and tear over time. Select high-quality cutting wires made from durable materials such as nichrome or tungsten. These materials offer excellent heat resistance and maintain their cutting performance over extended periods. Additionally, some manufacturers offer pre-tensioned cutting wires that simplify the replacement process and ensure consistent tension.
When selecting replacement cutting wires, consider the wire’s diameter and length. Thicker wires provide greater durability and are suitable for cutting thicker foam materials, while thinner wires offer higher precision for intricate cuts. The length of the cutting wire should match the specifications of the foam wire cutter to ensure proper installation and operation.
Guide Rails and Templates
Guide rails and templates are valuable accessories that enhance the precision and versatility of foam wire cutters. Guide rails provide a stable and straight cutting path, ensuring consistent and accurate cuts. They are particularly useful for cutting large foam sheets or blocks, where maintaining a straight line can be challenging. Guide rails are available in various lengths and can be easily attached to the cutting platform.
Templates allow for the creation of complex shapes and designs. They are typically made from durable materials such as acrylic or metal and can be custom-made to match specific design requirements. Templates can be used in conjunction with guide rails to achieve precise and repeatable cuts, making them ideal for applications such as model making, signage, and packaging.
Dust and Fume Extraction Systems
Cutting foam materials often generates dust and fumes, which can pose health and safety risks to operators. Dust and fume extraction systems are essential accessories that help maintain a clean and safe working environment. These systems use powerful fans and filters to capture and remove airborne particles and fumes, preventing them from being inhaled by operators or settling on the cutting platform.
Dust and fume extraction systems are available in various configurations, including portable units and integrated systems. Portable units are versatile and can be easily moved between different workstations, while integrated systems are built into the foam wire cutter, providing continuous extraction during the cutting process. Select a system with adequate airflow and filtration capacity to effectively capture and remove dust and fumes.
Conclusion
In summary, selecting the right foam wire cutter involves considering various factors such as types, performance, technical specifications, safety standards, and durability. The latest technology features, including automated cutting systems, advanced control interfaces, and energy-efficient technologies, have significantly enhanced the capabilities of foam wire cutters. Additionally, accessories such as replacement cutting wires, guide rails, templates, and dust and fume extraction systems play a crucial role in optimizing the cutter’s performance and ensuring a safe working environment. By carefully evaluating these factors, business buyers can make informed decisions and invest in foam wire cutters that meet their specific needs and requirements.