In 2025, the AC DC TIG welder market continues to thrive, driven by technological advancements and increased demand across various industries. This article will provide an in-depth analysis of the market, highlighting essential considerations for professional buyers. It will assist in making informed decisions to select high-performance welders that meet industry standards and specific business needs.
Table of Contents:
– Market Overview of AC DC TIG Welder
– Detailed Introduction and Analysis of the AC DC TIG Welder Market
– Key Factors When Selecting an AC DC TIG Welder
– Latest Technology Features in AC DC TIG Welders
– Durability and Build Quality
– Safety Standards and Certifications
– Final Thoughts
Market Overview of AC DC TIG Welder
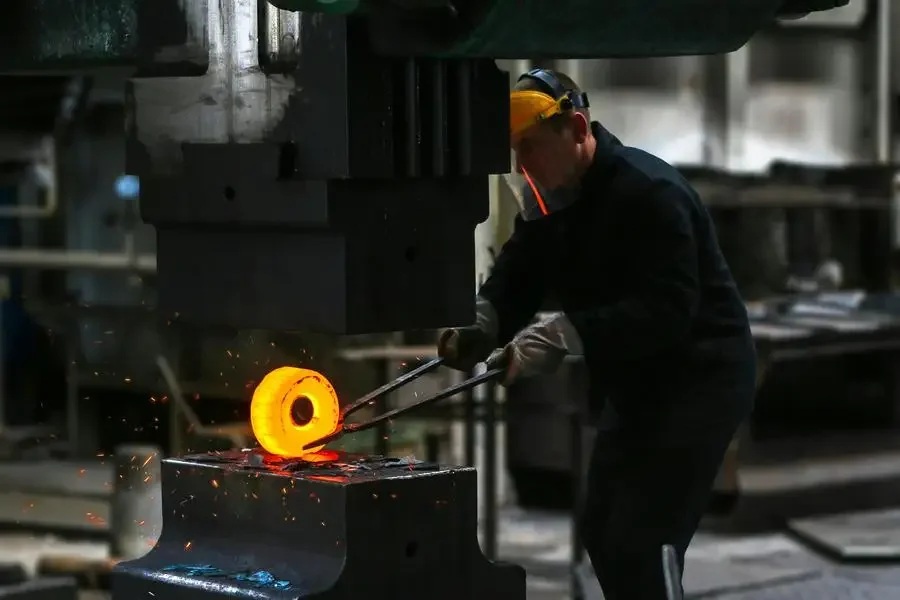
The AC DC TIG welder market is experiencing robust growth, driven by technological advancements and increasing demand across various industries. The global electric welding machine market, which includes AC DC TIG welders, grew from USD 5.52 billion in 2023 to USD 5.93 billion in 2024. It is expected to continue growing at a CAGR of 7.81%, reaching USD 9.35 billion by 2030. This growth is largely fueled by expanding infrastructure projects, the booming automotive sector, and the increasing need for precision in welding advanced materials.
Regionally, the Asia-Pacific market is a significant contributor, with countries like China, India, and Japan leading due to their extensive infrastructure projects and growing manufacturing sectors. In the Americas, the market is driven by robust industrial sectors such as automotive, construction, and manufacturing, with the United States being a key player. The EMEA region is also experiencing growth due to rising demand for manufacturing and construction activities, particularly in Europe, where there is a strong emphasis on innovation and environmental sustainability.
Market dynamics are influenced by factors such as the high initial investment and maintenance costs of welding machines, which can hinder growth. However, opportunities abound in the automation of welding processes and the construction of green energy infrastructure, such as solar panels and wind turbines. The growing reliance on welding machines in the shipping industry for repair and manufacturing also contributes significantly to market growth.
Detailed Introduction and Analysis of the AC DC TIG Welder Market
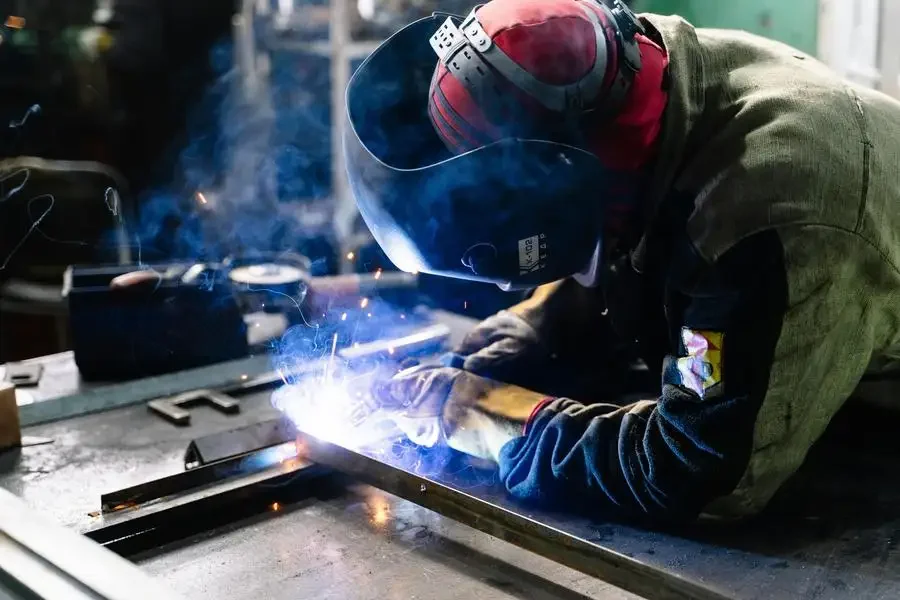
AC DC TIG welders are known for their versatility and precision, making them essential in industries requiring high-quality welds. These machines are valued for their ability to weld both ferrous and non-ferrous metals, including aluminum. Key performance benchmarks include stable arcs, precise heat control, and high-frequency start capabilities, which are crucial for achieving clean and strong welds.
Manufacturers are focusing on developing advanced features, such as digital controls and automation capabilities, to differentiate their products. Economic influences, such as fluctuations in raw material costs and the economic health of key industrial sectors, play a significant role in shaping market trends. Consumer behavior is shifting towards high-efficiency, low-maintenance machines, driving demand for innovative and cost-effective solutions.
Distribution channels for AC DC TIG welders have evolved, with online sales gaining traction due to convenience and a wide range of options. However, traditional offline channels, such as specialized equipment retailers and direct sales, remain crucial for hands-on demonstrations and personalized customer support. Recent innovations include lightweight, portable models that do not compromise performance, making them ideal for fieldwork and small-scale operations.
The product lifecycle of AC DC TIG welders involves several stages, from development and market introduction to growth, maturity, and eventual decline. Digitalization has significantly impacted this lifecycle, with smart welders incorporating Internet of Things (IoT) capabilities for remote monitoring and diagnostics becoming more common. Social trends, such as the push towards sustainability and energy efficiency, have also influenced product development, leading to more eco-friendly welding solutions.
Customer pain points often revolve around high upfront costs and the complexity of operating advanced machines. To address these issues, manufacturers are investing in user-friendly interfaces and comprehensive training programs. Brand positioning strategies highlight the reliability, durability, and advanced features of their products, while differentiation strategies emphasize innovation, customization options, and superior customer support.
In niche markets, there is a growing demand for specialized AC DC TIG welders designed for specific applications, such as aerospace, medical device manufacturing, and fine art restoration. These niche markets require welders that offer exceptional precision and control, often necessitating custom solutions tailored to the unique needs of the industry.
Overall, the AC DC TIG welder market is poised for continued growth, driven by technological advancements, expanding industrial applications, and a focus on sustainability and efficiency.
Key Factors When Selecting an AC DC TIG Welder
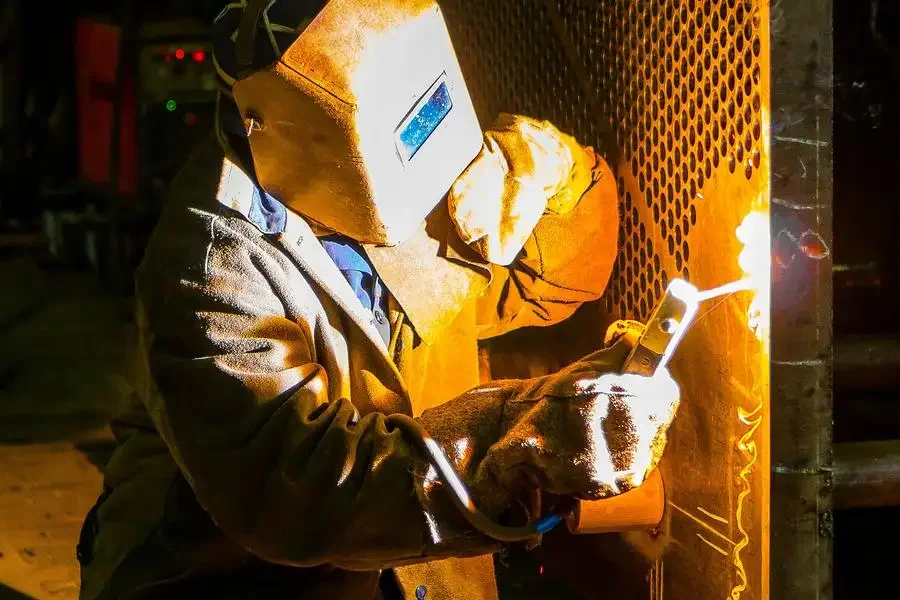
Type and Style of the Welder
The type and style of an AC DC TIG welder significantly influence its usability and application scope. TIG welders can be either inverter-based or transformer-based. Inverter-based models are generally lighter and more portable, ideal for fieldwork and smaller shops. They offer better arc control and energy efficiency, crucial for precision tasks. Transformer-based welders are known for their robustness and durability, suitable for heavy-duty applications and long-term use.
The style of the welder also matters. Handheld TIG welders are suitable for intricate work requiring high maneuverability, such as in aerospace or automotive industries. Bench-top models provide a stable platform for more extensive projects, ensuring consistency and reducing operator fatigue. The choice between these types depends on the specific needs of the application and the working environment.
Performance and Functionality
Performance metrics such as duty cycle, output power, and arc stability are vital when selecting an AC DC TIG welder. The duty cycle, expressed as a percentage, indicates how long the welder can operate continuously within a 10-minute period without overheating. For industrial applications, a higher duty cycle is preferred to ensure consistent performance during prolonged welding sessions.
Output power, measured in amperes, determines the welder’s capability to handle different material thicknesses. A welder with a broad amperage range is versatile, allowing for both thin-gauge and heavy-gauge welding. Arc stability is another critical factor, as a stable arc ensures clean, precise welds with minimal spatter. Advanced models feature arc control technologies that maintain a steady arc under varying conditions, enhancing weld quality and reducing rework.
The design of the welder can impact its ease of use and ergonomic comfort. Modern AC DC TIG welders are designed with user-friendly interfaces, including intuitive control panels and digital displays that provide real-time feedback on welding parameters. These features simplify adjustments and enhance precision, especially for complex welding tasks.
Ergonomic design elements, such as comfortable grips and strategically placed controls, reduce operator fatigue and improve handling during extended use. The overall build quality, including the durability of the housing and components, ensures the welder can withstand harsh working conditions.
Technical Specifications
Technical specifications such as input voltage, frequency, and phase compatibility are crucial for ensuring the welder can be integrated into existing electrical systems. AC DC TIG welders typically operate on single-phase or three-phase power, with the former being common in residential and light commercial settings, and the latter used in industrial applications. Ensuring compatibility with the available power supply is essential to avoid electrical issues and ensure optimal performance.
Additional specifications include the type of cooling system (air-cooled or water-cooled), which affects the welder’s ability to manage heat during operation. Water-cooled systems are more efficient for high-amperage welding, while air-cooled systems are sufficient for lighter tasks. Features such as pulse welding capabilities and high-frequency start are also important, as they enhance control over the welding process and improve arc initiation.
Price Range and Budget
The price range of AC DC TIG welders varies significantly based on factors such as brand, features, and performance capabilities. Entry-level models, suitable for hobbyists and small-scale operations, are generally more affordable and offer basic functionalities. Mid-range welders provide a balance between cost and advanced features, making them ideal for professional welders and small to medium-sized businesses.
High-end models, designed for industrial applications, come with a premium price tag but offer superior performance, durability, and advanced features such as programmable settings and automated controls. When setting a budget, it is important to consider the long-term benefits and potential return on investment. Investing in a high-quality welder can lead to improved productivity, reduced downtime, and lower maintenance costs.
Latest Technology Features in AC DC TIG Welders
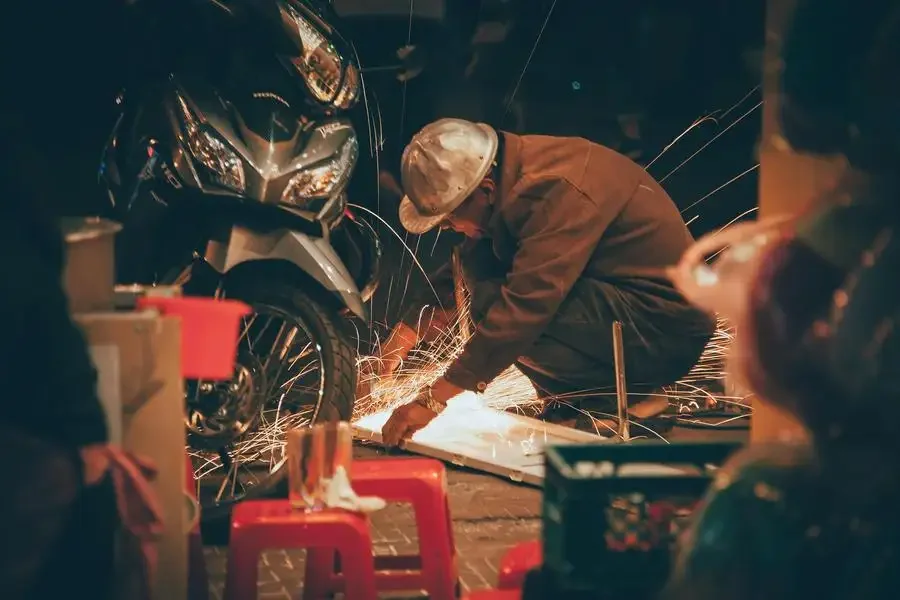
The latest technology features in AC DC TIG welders significantly enhance their performance, usability, and versatility. One notable advancement is the integration of digital control systems, which allow for precise adjustment of welding parameters. These systems often include touch screen interfaces and programmable memory settings, enabling welders to save and recall specific configurations for different materials and applications.
Another cutting-edge feature is advanced pulse welding technology. Pulse welding allows for better heat control and minimizes distortion, making it ideal for thin materials and intricate welds. This technology also reduces spatter and improves overall weld quality, leading to less post-weld cleanup and finishing work.
High-frequency start technology is another significant advancement. This feature ensures a smooth and consistent arc initiation without the need for direct contact with the workpiece. It enhances precision and reduces the risk of contamination, which is particularly important when welding reactive materials like aluminum and magnesium.
Durability and Build Quality
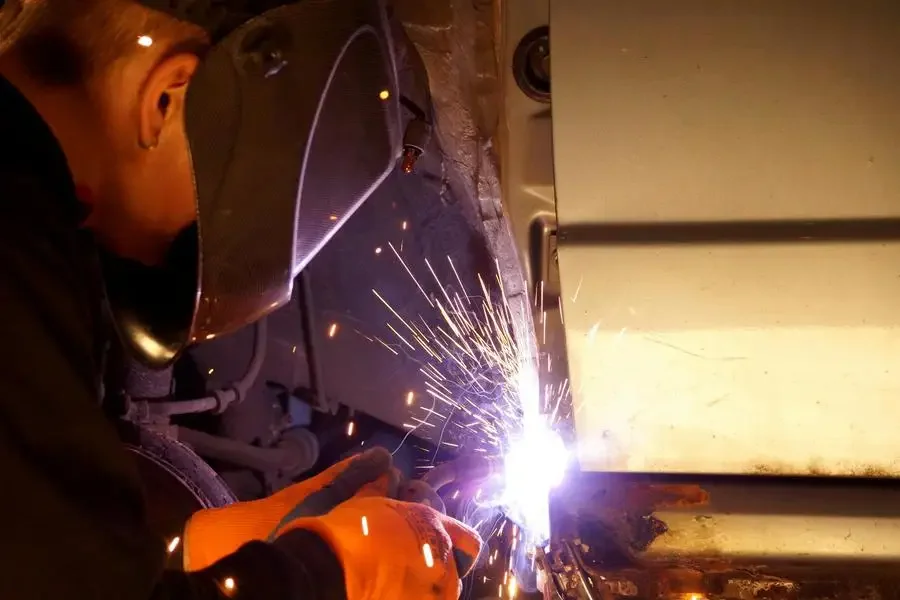
Durability and build quality are paramount when selecting an AC DC TIG welder. These machines are often subjected to harsh working conditions, including high temperatures, dust, and occasional impacts. A welder with a robust build and high-quality materials can withstand these conditions and provide reliable performance over time.
Key components such as the torch, cables, and connectors should be made from durable materials that resist wear and tear. The housing should be constructed from high-grade metal or reinforced plastic to protect the internal components from damage. Additionally, features like rugged handles and protective covers for control panels enhance the welder’s resilience and longevity.
Regular maintenance and proper storage also play a role in extending the lifespan of the welder. Models with easy-to-access components and simplified maintenance procedures reduce downtime and ensure the machine remains in optimal working condition. Investing in a durable welder not only ensures consistent performance but also reduces the total cost of ownership by minimizing the need for frequent repairs or replacements.
Safety Standards and Certifications

Compliance with safety standards and certifications is a critical consideration when selecting an AC DC TIG welder. These standards ensure that the welder meets specific safety and performance criteria, reducing the risk of accidents and ensuring reliable operation. Common certifications include those from the International Electrotechnical Commission (IEC), Underwriters Laboratories (UL), and the European Conformity (CE) mark.
Safety features such as thermal overload protection, voltage fluctuation protection, and automatic shut-off mechanisms are essential for preventing accidents and protecting both the operator and the equipment. Welders with built-in safety sensors can detect potential issues and take corrective actions, such as shutting down the machine in case of overheating or excessive current.
Proper training and adherence to safety protocols are also crucial for safe operation. Manufacturers often provide detailed user manuals and safety guidelines to help operators understand the correct usage and maintenance procedures. Ensuring that the welder complies with relevant safety standards and certifications provides peace of mind and helps maintain a safe working environment.
Final Thoughts
Selecting the right AC DC TIG welder involves careful consideration of various factors, including type and style, performance and functionality, technical specifications, and price range. Incorporating the latest technology features, ensuring durability and build quality, and adhering to safety standards and certifications are also essential for making an informed decision. By evaluating these aspects, buyers can choose a welder that meets their specific needs and delivers reliable performance for years to come.