In 2025, the welding machinery market is thriving, with significant advancements in automation and digitalization. This article provides an in-depth analysis of welding positioners, covering key factors such as types, performance, design, and compliance. Professional buyers will gain valuable insights to make informed purchasing decisions and enhance their product offerings.
Table of Contents:
– Welding Positioner Market: A Comprehensive Overview
– Key Factors When Selecting a Welding Positioner
– Durability and Build Quality
– Latest Technology Features
– Cost and Budget Considerations
– Regulatory Compliance and Certifications
– Initial Setup Complexity
– Conclusion
Welding Positioner Market: A Comprehensive Overview
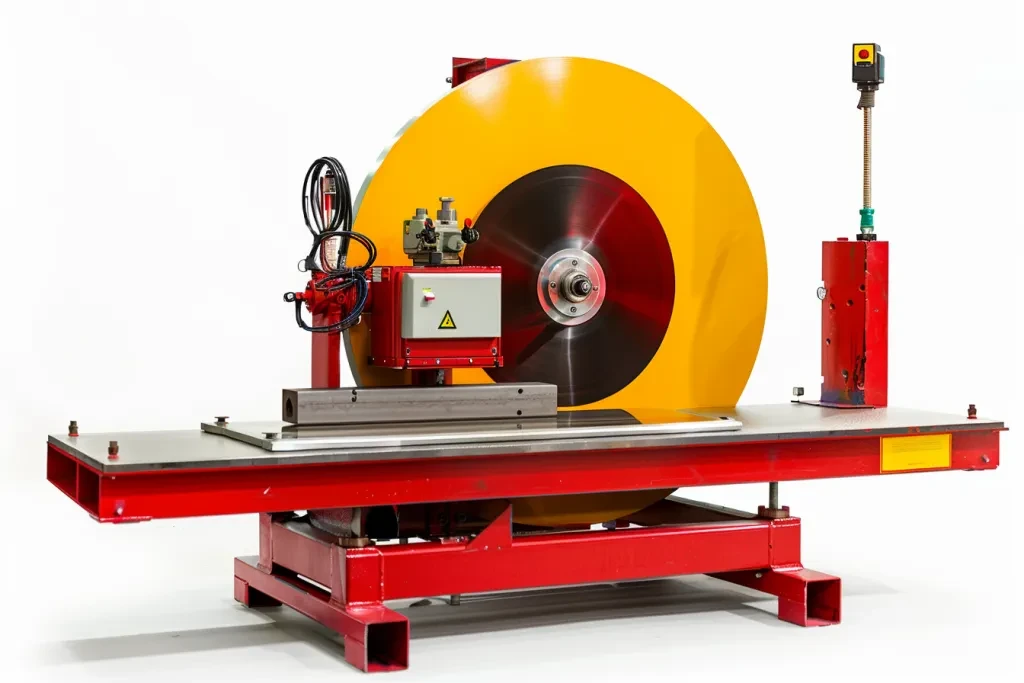
Market Dynamics and Growth Trends
The global welding machinery market has been experiencing notable growth, driven by advancements in automation technologies and increased demand across various industries. In 2023, the market size was estimated at USD 28.56 billion, growing to USD 30.58 billion in 2024. By 2030, it is expected to reach USD 47.52 billion, with a CAGR of 7.54%. This growth is largely due to the rising demand for efficient and precise welding processes in the automotive, aerospace, and construction industries.
Arc welding technology dominates the market due to its versatility and efficiency. Arc welding machines account for a substantial market share. Automation in welding processes is also crucial, with automatic and semi-automatic welding machines gaining traction for their ability to enhance productivity and reduce labor costs.
Regionally, the Asia-Pacific region leads the market, driven by rapid industrialization and infrastructure development in countries like China, India, and Japan. North America and Europe also hold significant market shares, focusing on technological innovations and stringent quality standards in manufacturing processes.
In-Depth Analysis of the Welding Positioner Market
Welding positioners are essential tools in the welding machinery market, facilitating the manipulation of workpieces to achieve optimal welding angles and positions. These devices enhance welding precision, reduce operator fatigue, and improve overall efficiency. The market for welding positioners is driven by factors such as the increasing adoption of automation, the need for high-quality welds, and the growing complexity of welding tasks.
Key performance benchmarks for welding positioners include load capacity, rotational speed, and control systems. Advanced positioners now feature digital controls and automated functions, allowing for precise adjustments and consistent performance. The integration of IoT and smart technologies further enhances their capabilities, enabling real-time monitoring and remote control.
Economic influences such as fluctuating raw material prices and trade policies also impact the market dynamics. However, the increasing investment in infrastructure projects and the rising demand for renewable energy solutions, like wind turbines and solar panels, present significant growth opportunities for welding positioners. Innovations in product design, such as modular and customizable positioners, cater to diverse industry needs, further driving market growth.
Consumer behavior is shifting towards automation and digitalization, with industries aiming to minimize manual intervention and improve welding accuracy. Distribution channels are evolving, with a growing emphasis on online platforms and direct sales to reach a broader customer base. Customer pain points, such as the need for operator training and maintenance support, are addressed through comprehensive service packages offered by leading manufacturers.
In terms of brand positioning strategies, companies like Lincoln Electric Holdings, Inc., Miller Electric Mfg. LLC, and ESAB Corporation focus on innovation, quality, and customer support to differentiate themselves in the competitive landscape. These brands leverage their industry experience and technological expertise to offer advanced welding positioners that meet the market’s evolving demands.
Recent Innovations and Future Outlook
Recent innovations in welding positioners include automated and robotic positioners that integrate seamlessly with welding robots and other automated systems. These innovations enhance welding precision and reduce cycle times, making them ideal for high-volume production environments. Additionally, advanced materials and engineering techniques have led to the creation of lightweight yet robust positioners, improving their portability and ease of use.
The product lifecycle stages of welding positioners typically include research and development, introduction, growth, maturity, and decline. However, continuous technological advancements and increasing automation adoption are likely to prolong the growth and maturity stages, ensuring sustained demand for these devices.
Digitalization and Industry 4.0 are expected to play pivotal roles in the future of the welding positioner market. The integration of smart sensors, data analytics, and machine learning algorithms will enable predictive maintenance, optimize performance, and reduce downtime. Social trends towards sustainability and energy efficiency also drive the demand for eco-friendly welding solutions, prompting manufacturers to develop energy-efficient positioners.
Key Factors When Selecting a Welding Positioner
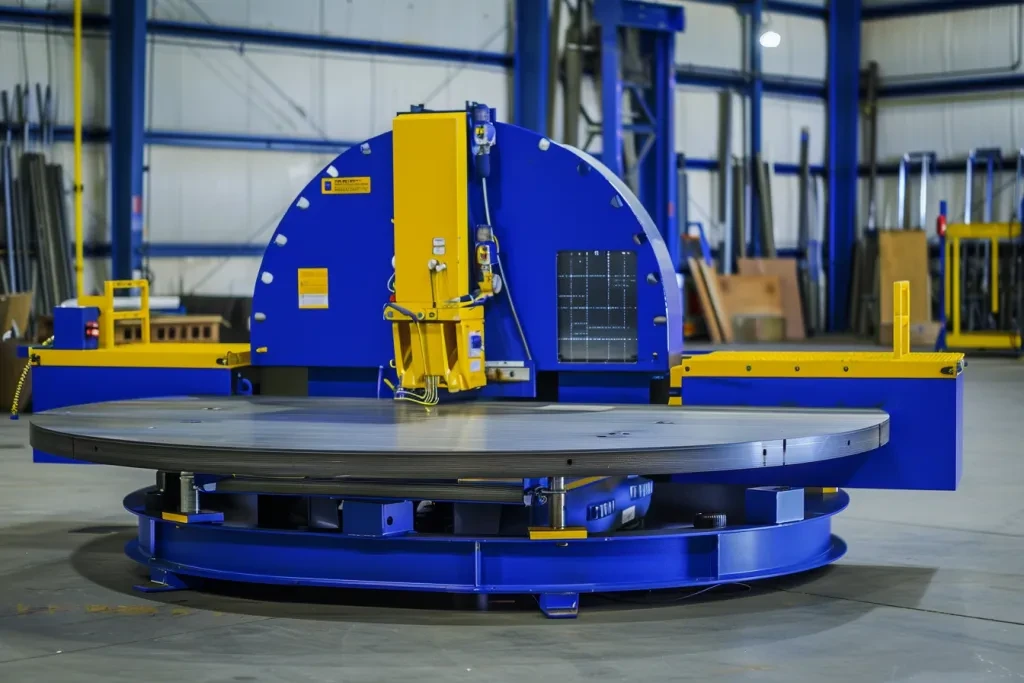
Types and Styles of Welding Positioners
When selecting a welding positioner, understanding the different types and styles is crucial. These include turntables, head and tailstock positioners, pipe welding positioners, and benchtop positioners.
Turntables are common and ideal for welding round objects. They can rotate 360 degrees, allowing continuous welding without repositioning the workpiece. These positioners range from small benchtop models to large industrial turntables handling several tons.
Head and tailstock positioners support long, heavy workpieces at both ends. Common in aerospace and shipbuilding, they handle large components needing precise positioning. They can be manually or automatically controlled.
Pipe welding positioners are designed for welding pipes and tubular structures. They provide rotational movement around the pipe’s axis, ensuring a consistent weld seam. These positioners are essential in industries like oil and gas.
Benchtop positioners are smaller and more compact, suitable for precision welding tasks. Commonly used in electronics and medical device industries, they offer various degrees of freedom, including tilt and rotation, to accommodate complex welding geometries.
Performance and Functionality
Performance and functionality are critical when choosing a welding positioner. Key performance metrics include load capacity, rotational speed, and tilt angle.
Load capacity indicates the maximum weight the positioner can handle. Industrial positioners can support several tons, suitable for heavy-duty applications. Select a positioner with a load capacity that matches or exceeds the workpieces’ weight for safe operation.
Rotational speed determines how quickly the workpiece can be rotated during welding. Some positioners offer variable speed control, allowing operators to adjust rotation speed based on welding requirements, ensuring consistent weld quality on different materials and thicknesses.
Tilt angle is crucial for positioning the workpiece at the optimal angle for welding. Positioners with adjustable tilt angles provide flexibility, enabling operators to access hard-to-reach areas and achieve better weld penetration. Advanced positioners may offer programmable tilt functions for precise and repeatable positioning.
Design
User-friendly controls are essential for efficient operation. Positioners with intuitive control panels and easy-to-read displays simplify setup and adjustment, reducing errors. Some advanced models offer touch-screen interfaces and remote control options for greater convenience.
Adjustable workpiece supports accommodate different sizes and shapes of workpieces. Positioners with modular support systems allow quick reconfiguration, minimizing downtime between welding tasks. This feature is valuable in high-mix, low-volume production environments.
High-quality materials like stainless steel and aluminum offer better resistance to corrosion and wear, ensuring a longer service life. A well-finished positioner with smooth surfaces and protected components is easier to clean and maintain, reducing contamination and damage risk.
Technical Specifications
Technical specifications provide detailed information about a welding positioner’s capabilities and limitations. Key specifications to consider include power supply requirements, control interface options, and compatibility with welding equipment.
Power supply requirements ensure the positioner can operate within the available electrical infrastructure. Positioners may require single-phase or three-phase power, depending on their size and capacity. Verify the power specifications and ensure necessary electrical connections are available.
Control interface options determine how the positioner integrates with other welding equipment. Some positioners offer analog or digital interfaces for seamless communication with welding machines, robots, and automation systems. This integration is crucial for synchronized operation and precise control.
Compatibility with welding equipment is another critical consideration. Positioners should be compatible with specific welding machines and torches used in the production process. Compatibility ensures easy integration and control, minimizing the need for additional adapters or modifications.
Safety Standards and Certifications
Safety standards and certifications ensure the safe and reliable operation of welding positioners. Compliance with industry standards, such as those set by the American Welding Society (AWS) and the International Organization for Standardization (ISO), is crucial for maintaining high safety and quality standards.
Welding positioners should meet specific safety requirements, such as load capacity limits, electrical safety, and mechanical stability. Certifications from organizations like Underwriters Laboratories (UL) and the Canadian Standards Association (CSA) assure that the positioner meets stringent safety standards.
Additionally, positioners should include safety features like overload protection, emergency stop buttons, and interlocks to prevent accidents and injuries. These features enhance operator safety and ensure compliance with regulatory requirements.
Durability and Build Quality

Durability and build quality are critical factors determining the longevity and reliability of welding positioners. High-quality materials and robust construction ensure the positioner can withstand industrial use and maintain consistent performance over time.
Positioners made from durable materials like stainless steel and high-strength alloys offer better resistance to wear, corrosion, and mechanical stress. These materials provide a strong, stable platform for welding operations, reducing the risk of component failure and downtime.
Robust construction techniques, such as precision machining and reinforced joints, enhance the positioner’s structural integrity. Welded frames and heavy-duty bearings contribute to strength and stability, ensuring smooth and accurate movement during welding.
Attention to detail in design and assembly is crucial for high build quality. Positioners with well-fitted components, smooth surfaces, and protected electrical connections are less prone to damage and require less maintenance.
Latest Technology Features
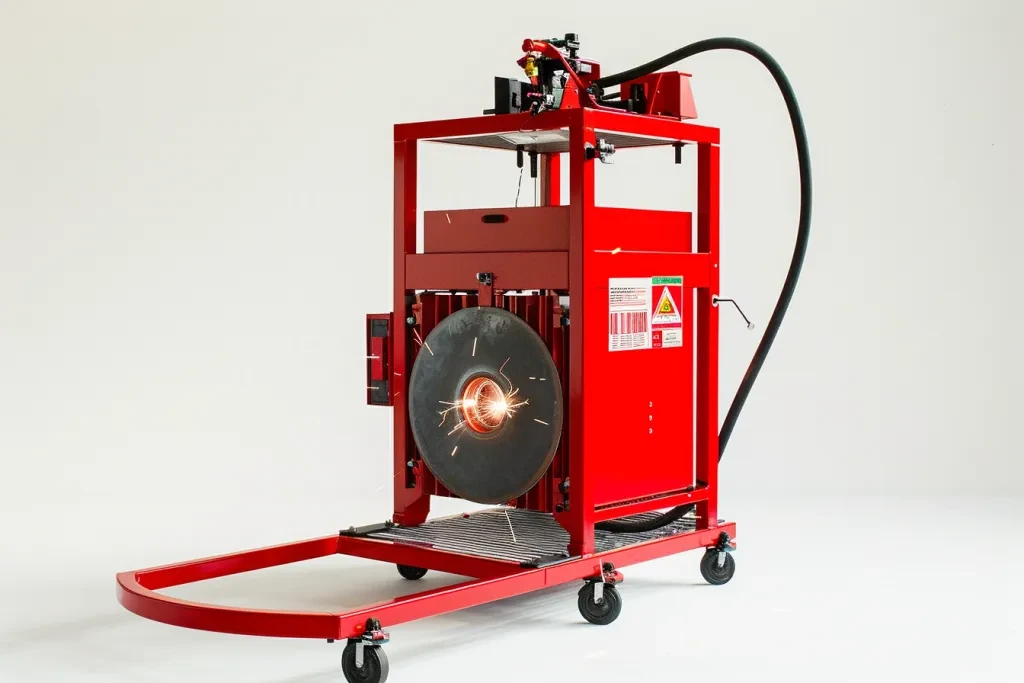
Advancements in technology have led to innovative features enhancing welding positioners’ performance and functionality. These features improve precision, efficiency, and ease of use, making modern positioners more versatile and capable.
One such feature is the integration of programmable logic controllers (PLCs) and automation systems. PLCs enable precise control over the positioner’s movements, allowing for complex welding sequences and automated operations. This reduces manual intervention and increases productivity.
Another advanced feature is the use of servo motors and drives for precise and responsive movement control. Servo-driven positioners offer greater accuracy and repeatability, ensuring consistent weld quality. These motors also provide higher torque and speed capabilities, suitable for demanding welding applications.
Remote monitoring and diagnostics are becoming increasingly common in modern welding positioners. These features allow operators to monitor the positioner’s performance and status in real-time, enabling proactive maintenance and troubleshooting. Remote access capabilities facilitate quick issue responses, minimizing downtime and improving efficiency.
Cost and Budget Considerations
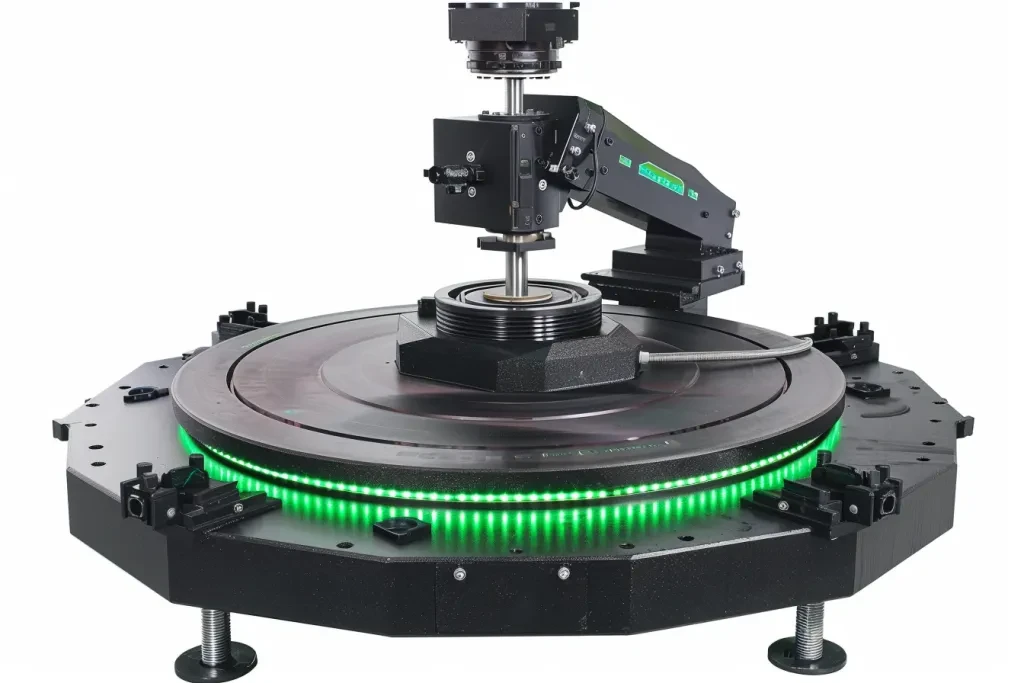
Cost and budget considerations play a significant role in selecting welding positioners. The price can vary widely based on type, size, features, and build quality. Balance the initial investment with long-term benefits and return on investment (ROI).
Entry-level positioners, such as small benchtop models, are typically more affordable and suitable for light-duty applications. They offer basic functionality and are ideal for small workshops and hobbyists. However, they may lack advanced features and have limited load capacity.
Mid-range positioners provide a good balance between cost and performance. They offer higher load capacities, better build quality, and additional features like variable speed control and adjustable tilt angles. These positioners are suitable for medium-sized enterprises and more demanding welding tasks.
High-end positioners are designed for heavy-duty industrial applications and come with advanced features like automation, servo drives, and remote monitoring. These positioners offer superior performance, durability, and precision but come at a higher cost. They are ideal for large-scale manufacturing operations and industries with high production requirements.
When evaluating the cost of a welding positioner, consider the total cost of ownership (TCO), including maintenance, repair, and operational costs. Investing in a high-quality positioner with advanced features may result in lower long-term costs and higher productivity, providing better value for money.
Regulatory Compliance and Certifications
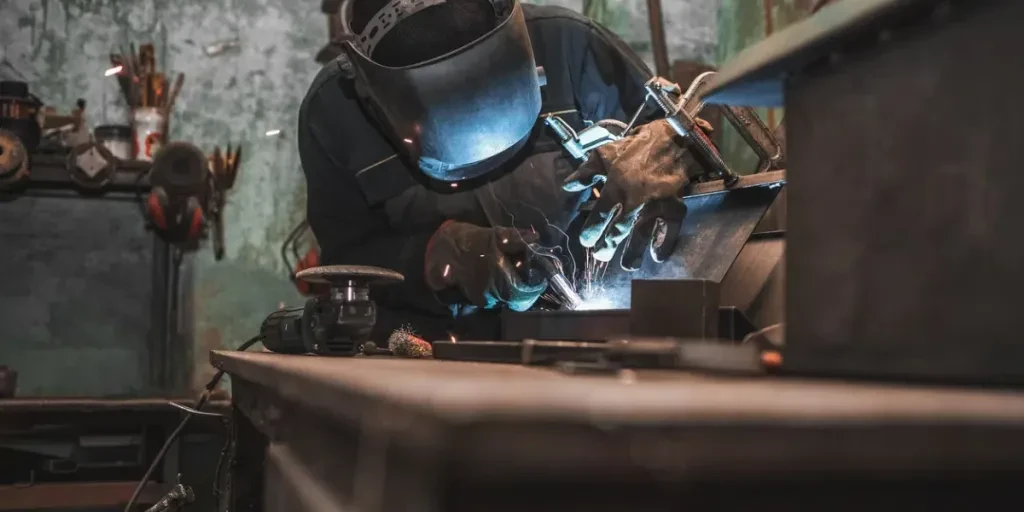
Regulatory compliance and certifications ensure welding positioners meet industry standards and legal requirements. Compliance with regulations such as those set by the Occupational Safety and Health Administration (OSHA) and the European Union’s Machinery Directive is crucial for maintaining workplace safety and avoiding legal liabilities.
Certifications from recognized organizations, such as CE marking, indicate that the positioner has been tested and meets specific safety and performance standards. These certifications assure buyers that the positioner is safe to use and complies with relevant regulations.
In addition to safety standards, welding positioners may need to comply with environmental regulations, such as those related to energy efficiency and emissions. Positioners with energy-efficient designs and low environmental impact are more sustainable and may qualify for incentives or certifications like Energy Star.
When selecting a welding positioner, verify that it meets all applicable regulatory requirements and has the necessary certifications. This ensures the positioner can be legally and safely operated in the intended environment.
Initial Setup Complexity
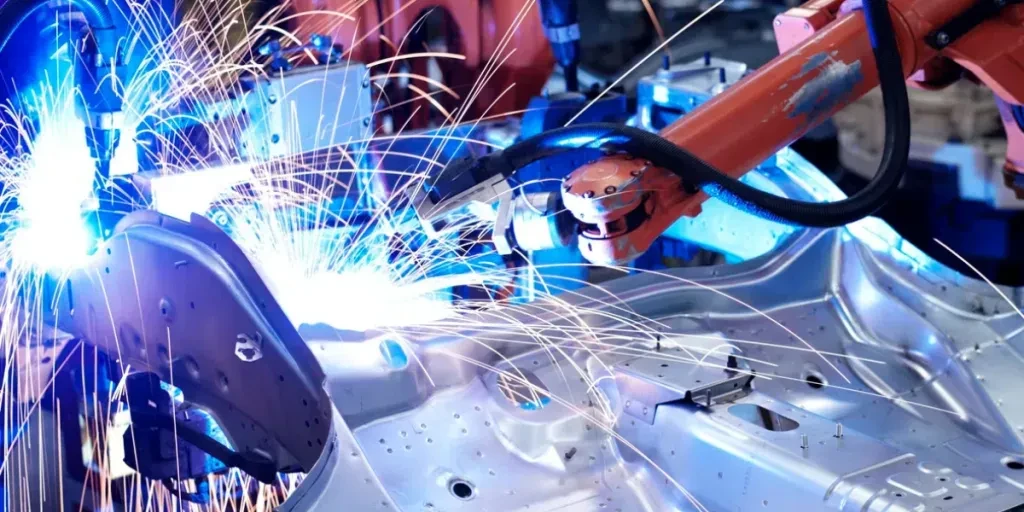
The initial setup complexity is an important consideration when choosing a welding positioner. An easy-to-set-up and configure positioner can save time and reduce installation errors.
Some positioners come with pre-configured settings and plug-and-play functionality, allowing for quick and straightforward setup. These models are ideal for users with limited technical expertise or those needing quick operation.
More advanced positioners may require detailed calibration and configuration for optimal performance. While more time-consuming, this allows for greater customization and fine-tuning to meet specific welding requirements. Manufacturers often provide comprehensive setup guides and technical support to assist with installation.
Consider the availability of training and support services. Some manufacturers offer on-site training and installation services, ensuring the positioner is set up correctly and operators are familiar with its features and operation. This can be particularly valuable for complex or high-end positioners with advanced functionalities.
Conclusion
In summary, selecting the right welding positioner involves careful consideration of various factors, including types and styles, performance and functionality, design, technical specifications, safety standards and certifications, durability and build quality, latest technology features, cost and budget considerations, regulatory compliance, and initial setup complexity. By evaluating these factors, buyers can make informed decisions and choose a welding positioner that meets their specific needs and requirements.