Chillers are critical components in modern industries, ensuring efficient cooling for processes, equipment, and spaces across sectors like manufacturing, healthcare, and data centers. As commercial and industrial needs evolve, innovative cooling systems are becoming indispensable for energy efficiency, environmental compliance, and operational reliability. Understanding the latest market trends and advancements in chiller technology empowers businesses to make informed purchasing decisions that align with their operational goals. This article provides a comprehensive overview of the chiller market, explores key types and features, and offers expert guidance to help professional buyers select the ideal solution. Staying ahead in the competitive landscape starts with making the right choice for cooling systems.
Table of Contents
● Market overview: understanding the global chiller industry
● Different types of chillers and their standout features
● Key factors to consider when choosing a chiller
● Conclusion
Market overview: understanding the global chiller industry
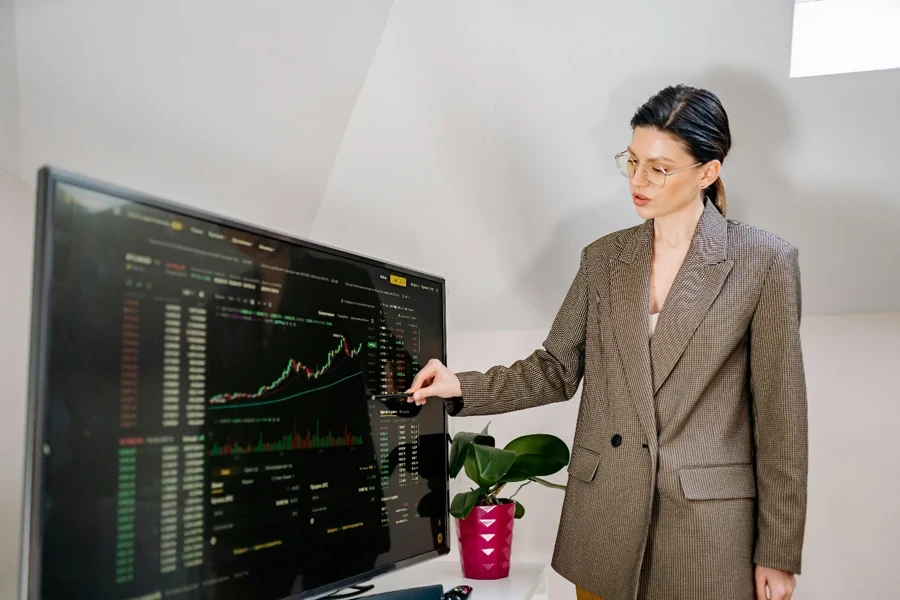
Market size and growth trends
The global chillers market was valued at USD 11.59 billion in 2023 and is projected to reach USD 18.35 billion by 2033, growing at a CAGR of 4.7% during this period, according to Precedence Research. This growth is driven by increasing demand across commercial, industrial, and residential sectors for energy-efficient cooling solutions. The market expansion is further influenced by the rise of advanced technologies, such as IoT-integrated systems and smart cooling solutions, which enhance operational efficiency and sustainability.
Regional highlights
Asia-Pacific leads the market with a 38% share as of 2023, fueled by rapid industrialization, urbanization, and the expansion of data centers, food processing units, and pharmaceuticals. North America also showcases substantial growth due to a strong emphasis on energy-efficient cooling technologies, particularly in smart buildings and large commercial setups. Meanwhile, Europe is driven by strict environmental regulations, promoting sustainable chiller systems in sectors like healthcare and manufacturing.
Segment analysis
Among product types, water-cooled chillers dominate the market, favored for their high energy efficiency and reliability in large-scale industrial applications. On the other hand, air-cooled chillers are gaining traction due to their compact size, lower maintenance needs, and suitability for areas with water scarcity. Additionally, advancements in screw and scroll chillers are boosting their adoption in various commercial and industrial settings, providing tailored cooling solutions for specific operational demands.
Technological advancements
The integration of IoT and smart technologies is reshaping the chiller market, enabling real-time monitoring, predictive maintenance, and energy optimization. Companies like Johnson Controls are developing cloud-connected chillers that utilize data analytics to minimize downtime and enhance efficiency. These innovations are not only improving operational reliability but also aligning with growing environmental concerns by reducing energy consumption and emissions.
Different types of chillers and their standout features
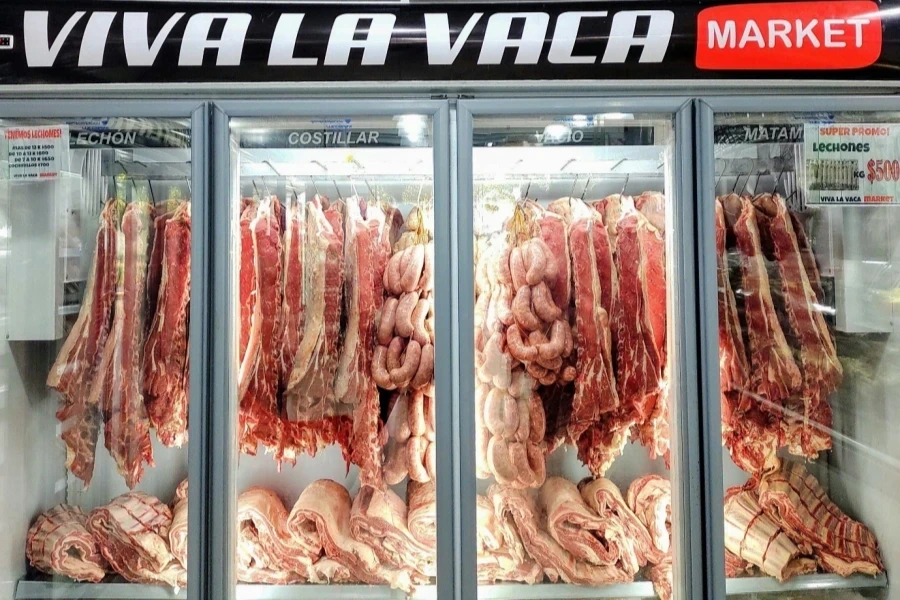
Water-cooled chillers: Efficient giants
Water-cooled chillers leverage cooling towers to dissipate heat through water evaporation, resulting in higher energy efficiency compared to air-cooled counterparts. These systems operate using a shell-and-tube heat exchanger, where the refrigerant transfers heat to water, which is subsequently cooled in a tower and recirculated. Typical capacities for these chillers range from 15 kW to over 6,000 kW, making them suitable for large-scale industrial processes and centralized cooling systems. Their ability to maintain consistent evaporator outlet temperatures of 4-10°C makes them ideal for applications requiring precise climate control, such as petrochemical plants and industrial HVAC setups. Regular water treatment is necessary to prevent scaling and corrosion, ensuring long-term operational efficiency.
Air-cooled chillers: Space-saving performers
Air-cooled chillers use ambient air and axial fans to cool the refrigerant, eliminating the need for cooling towers and associated water infrastructure. These systems feature finned-tube condensers, where air flows over the refrigerant coils to remove heat. Capacities typically range from 15 kW to 1,500 kW, and their ability to operate efficiently in outdoor settings with temperatures as low as -20°C makes them versatile for colder climates. These chillers also have a modular design, allowing for scalability in commercial applications such as data centers and smaller industrial facilities. Although their efficiency may decrease in extremely hot climates, they are favored for environments where water is scarce or costly to manage.
Scroll chillers: Quiet and energy-efficient options
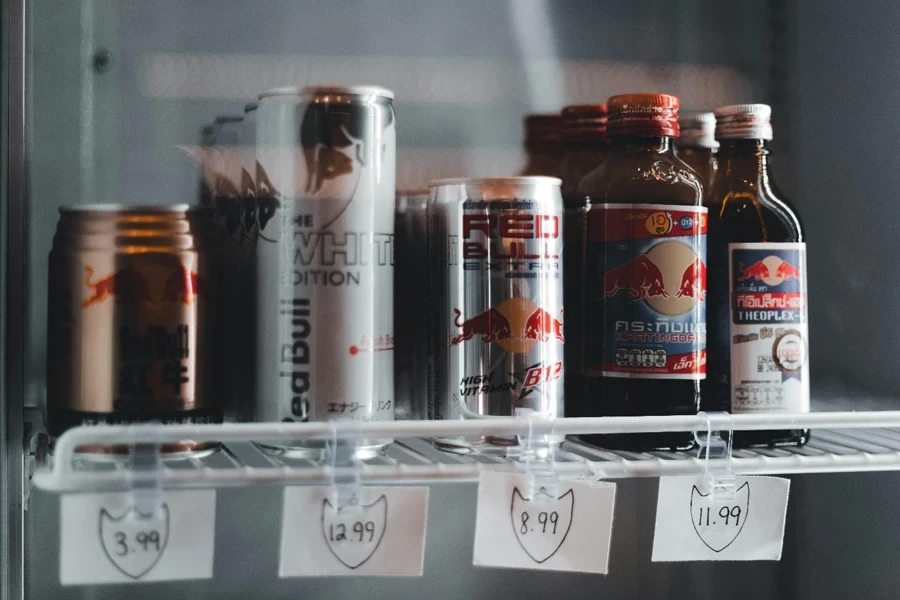
Scroll chillers are equipped with scroll compressors that use an orbiting scroll to compress refrigerant without pistons, resulting in minimal vibration and noise. These systems are designed for moderate cooling loads, typically ranging from 10 kW to 140 kW, making them suitable for office buildings, retail spaces, and light industrial operations. Modern scroll chillers often include variable frequency drives (VFDs) to adjust compressor speed based on load demand, enhancing energy efficiency. With fewer moving parts, they boast a longer operational life and reduced maintenance requirements. The sealed compressor design also minimizes refrigerant leakage, aligning with environmental standards.
Screw chillers: Industrial-grade cooling power
Screw chillers feature rotary screw compressors that use two meshing helical rotors to compress refrigerant, offering consistent performance under heavy loads. These systems are designed to handle capacities from 30 kW to over 2,000 kW, making them ideal for large industrial facilities like chemical plants and manufacturing units. Screw compressors provide precise temperature control, maintaining outlet temperatures within ±0.5°C, critical for processes like plastic extrusion and pharmaceutical production. Their ability to handle wide temperature ranges and high pressure differentials makes them more reliable than other chiller types in high-stress environments.
Specialized chillers for unique needs
Explosion-proof chillers are specifically engineered for hazardous environments, using reinforced casings and non-sparking components to prevent ignition in flammable atmospheres. These units meet stringent certifications like ATEX or IECEx, ensuring safety in petrochemical or chemical industries. Low-temperature chillers are equipped with enhanced evaporators and advanced refrigerants capable of achieving leaving fluid temperatures as low as -40°C, essential for cryogenic applications and ice rink maintenance. Glycol chillers incorporate robust heat exchangers compatible with propylene or ethylene glycol solutions, providing precise temperature regulation for food and beverage applications. These systems often include digital controllers for maintaining optimal conditions in processes like fermentation or wine storage, ensuring high product quality.
Key factors to consider when choosing a chiller
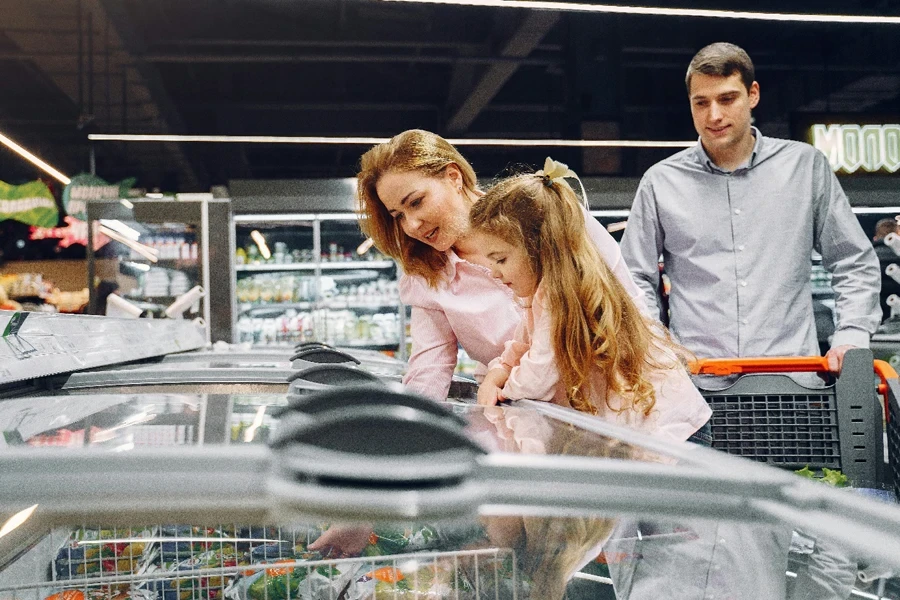
Assess your application’s requirements
Choosing the right chiller begins with a clear understanding of the intended application, as different industries require tailored cooling solutions. Industrial operations, such as chemical processing or metal fabrication, often demand chillers capable of managing high heat loads with consistent performance. Conversely, medical facilities prioritize chillers designed for precision cooling of sensitive equipment, such as MRI machines, where temperature fluctuations can lead to operational inefficiencies. Commercial spaces, including office buildings and retail outlets, may require smaller systems with moderate capacities to maintain comfortable indoor environments. Matching the chiller type to the application ensures optimal performance and longevity, reducing downtime and operational disruptions.
Understand heat load and sizing
Accurate calculation of heat load is essential for selecting a chiller that meets operational demands without unnecessary energy expenditure. Heat load depends on variables such as process type, ambient conditions, and equipment specifications. For example, processes requiring a temperature differential of 5°C between input and output fluid may need larger chillers compared to applications with lower deltas. Oversized chillers waste energy, while undersized units can lead to overheating and system failures. Calculations often include flow rate requirements, typically expressed in liters per minute (LPM), and cooling capacities in kilowatts (kW). Correct sizing, combined with the use of performance charts, ensures that the selected chiller can handle peak demand efficiently.
Factor in installation location
Environmental factors play a significant role in chiller selection. Outdoor installations must account for temperature fluctuations, exposure to debris, and potential weather-related challenges. For example, outdoor chillers may require sump heaters to prevent freezing in colder climates and enhanced air filters to protect internal components from dirt and dust. Indoor units, on the other hand, need adequate ventilation to dissipate heat without affecting surrounding equipment. Placement also affects noise considerations, with quieter units like scroll chillers preferred for settings where sound levels must be minimized. Accessories such as vibration dampeners and acoustic enclosures further enhance compatibility with specific locations.
Safety and compliance
Safety features are critical, particularly for operations involving hazardous materials. Explosion-proof chillers, designed to prevent ignition in environments containing flammable gases or chemicals, meet stringent certifications like ATEX or IECEx. These units often include sealed components, non-sparking motors, and reinforced casings to enhance safety. Compliance with international standards, such as the EU’s Ecodesign Directive or local energy regulations, ensures adherence to environmental and safety requirements. Companies must evaluate both legal mandates and industry-specific standards to select chillers that align with their operational and regulatory needs.
Energy efficiency and coolant compatibility
Energy-efficient chillers reduce operational costs by optimizing power usage while maintaining consistent performance. Models equipped with variable speed drives (VSDs) adjust compressor speeds based on cooling demands, significantly lowering energy consumption during off-peak hours. Coolant compatibility is another key factor, as improper fluids can lead to corrosion, blockages, or reduced efficiency. Glycol-water mixtures, commonly used in industrial and food processing applications, ensure stability across a range of operating temperatures. Coolants like R-134a or R-410A are chosen for their low global warming potential (GWP) to meet environmental regulations while ensuring efficient heat transfer.
Evaluate cost and longevity
Balancing initial costs with long-term benefits is crucial for sound investment. While advanced models with features like smart diagnostics may have higher upfront costs, their extended lifespan and reduced maintenance needs provide better return on investment. Factors such as ease of serviceability, availability of spare parts, and warranty terms should also be considered. For example, water-cooled chillers typically have lower operational costs but require additional infrastructure, such as cooling towers, which can increase installation expenses. Regular maintenance schedules and monitoring systems further enhance the lifespan and efficiency of the chosen unit, ensuring consistent performance over time.
Conclusion
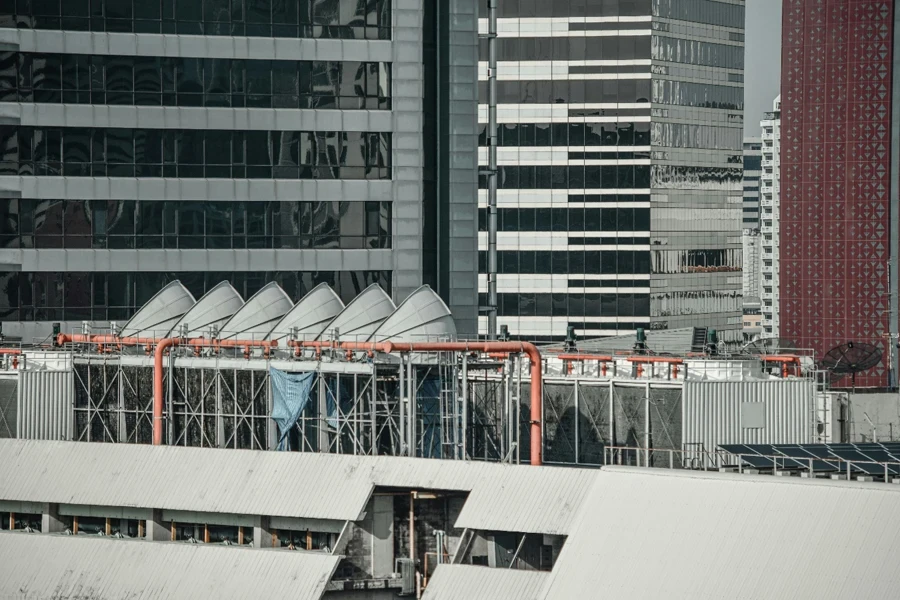
Selecting the right chiller requires a deep understanding of market trends, technical specifications, and the unique demands of various applications. By analyzing the available types, evaluating energy efficiency, and prioritizing safety and compliance, businesses can ensure their cooling systems deliver optimal performance and sustainability. Thoughtful investment in the appropriate chiller not only meets immediate operational needs but also supports long-term reliability and cost efficiency, helping organizations maintain a competitive edge in their industries.