The global ripper market, valued at $2.8 billion in 2025, is booming due to advancements in construction, mining, and agriculture. This article provides an in-depth analysis of the key factors to consider when selecting a ripper, offering valuable assistance to professional buyers. Transitioning now, let’s explore the essential aspects of ripper selection.
Table of Contents:
– Key Factors When Selecting a Ripper
– Latest Technology Features in Rippers
– Durability and Quality
– Budget and Price Range
– Final Thoughts
Global Ripper Market Overview
The global ripper market has experienced notable growth in recent years, driven by demand in construction, mining, and agriculture sectors. As of 2025, the market is valued at approximately $2.8 billion, with a compound annual growth rate (CAGR) of 6.5% projected through 2030. This growth is largely due to rising infrastructure development projects and the adoption of advanced machinery for improved efficiency and productivity.
Regionally, Asia-Pacific leads the ripper market, holding 38% of the total market share. North America and Europe follow with market shares of 28% and 24%, respectively. Rapid industrialization and urbanization in emerging economies like China and India significantly contribute to market expansion in the Asia-Pacific region. Government initiatives to boost infrastructure development further drive demand for rippers in these areas.
In terms of application, the construction sector holds the largest market share at 45%, followed by mining at 30% and agriculture at 25%. The versatility of rippers in handling various terrains and materials makes them essential in these sectors. The growing need for efficient land clearing and preparation in agriculture has also significantly increased the demand for rippers.
Detailed Analysis and Insights into the Ripper Market
Several key performance benchmarks influence purchasing decisions in the ripper market, including strength, durability, versatility, and ease of maintenance. Leading manufacturers continuously innovate to enhance these attributes. For example, advancements in material science have led to high-strength steel rippers that offer superior durability and performance.
Market share dynamics show that a few key players dominate the ripper market. Companies such as Caterpillar Inc., Komatsu Ltd., and John Deere collectively hold over 50% of the market share. These companies leverage extensive distribution networks and strong brand reputations to maintain their market positions. Strategic partnerships, mergers, and acquisitions also play crucial roles in expanding their market reach and product offerings.
Economic factors, such as fluctuating raw material prices and varying global economic conditions, significantly impact the ripper market. For instance, volatility in steel prices can affect the overall cost of ripper production, influencing market prices. Economic downturns can reduce infrastructure spending, subsequently affecting demand for rippers. Understanding these economic factors is crucial for market players to navigate challenges effectively.
Recent Innovations and Digitalization in the Ripper Market
Recent innovations in the ripper market focus on enhancing efficiency and reducing environmental impact. For example, integrating smart technologies like GPS and IoT in rippers has revolutionized the market. These technologies enable precise control and monitoring of ripper operations, leading to improved productivity and reduced fuel consumption. The adoption of such innovations is expected to further drive market growth in the coming years.
Digitalization is another significant trend shaping the ripper market. Manufacturers increasingly use digital platforms for sales and after-sales services. This shift enhances customer experience and streamlines operations, reducing costs. For instance, predictive maintenance powered by AI and machine learning can identify potential issues before they lead to equipment failure, minimizing downtime and maintenance costs.
Social trends, such as the growing emphasis on sustainability, also influence the ripper market. Consumers increasingly opt for eco-friendly machinery that minimizes environmental impact. In response, manufacturers are developing rippers with improved fuel efficiency and reduced emissions. This focus on sustainability meets regulatory requirements and aligns with evolving consumer preferences, enhancing brand positioning and market differentiation.
Addressing Customer Pain Points and Niche Markets
Customer pain points in the ripper market primarily revolve around maintenance costs and equipment downtime. To address these issues, manufacturers invest in research and development to enhance the durability and reliability of rippers. The use of wear-resistant materials and advanced lubrication systems can significantly reduce maintenance requirements and extend the lifespan of rippers.
Niche markets within the ripper industry, such as specialized rippers for forestry and marine applications, are gaining traction. These markets require rippers with features tailored to their unique operational needs. For example, forestry rippers are designed to handle dense vegetation and tough soil conditions, while marine rippers are built to operate in underwater environments. By catering to these niche markets, manufacturers can diversify their product portfolios and tap into new revenue streams.
Key Factors When Selecting a Ripper
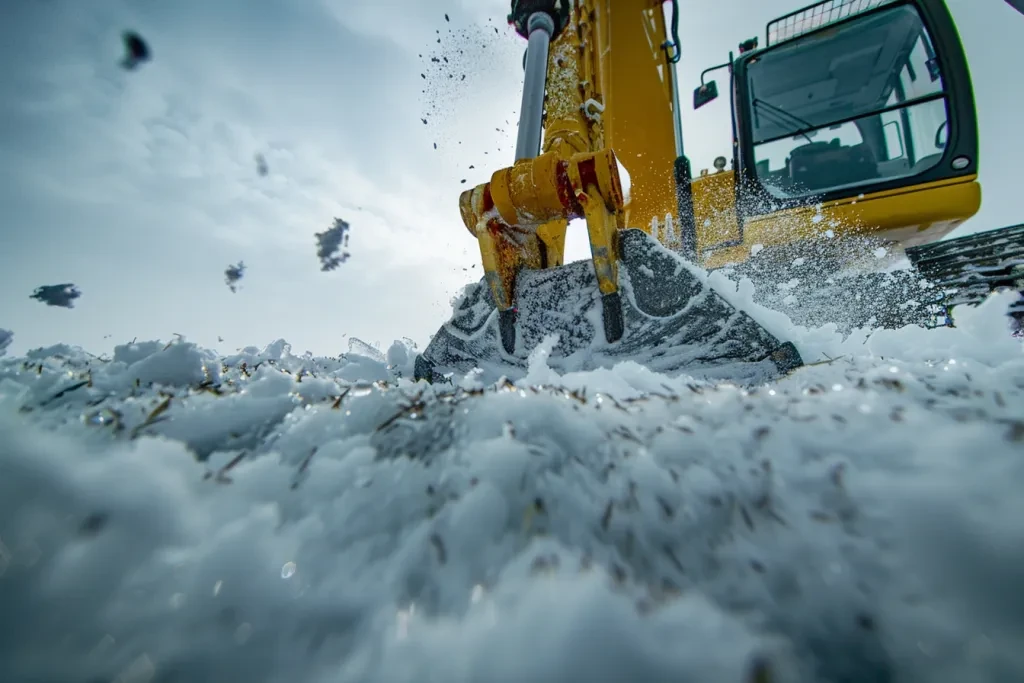
Types of Rippers
When choosing a ripper, it’s crucial to understand the different types available. The primary categories include single shank, multi-shank, and vibratory rippers, each suited for specific applications.
Single shank rippers are designed for heavy-duty tasks, breaking through hard, compacted soils and rocks. Their deep penetration makes them ideal for initial soil penetration and breaking large rocks. Multi-shank rippers are more versatile with multiple shanks covering a wider area, suitable for medium to light ripping tasks, often used in agricultural settings to prepare soil for planting. Vibratory rippers use vibration to enhance penetration, particularly effective for breaking through frozen ground or asphalt, making them ideal for construction and road maintenance.
Performance and Functionality
The performance of a ripper is determined by its power, speed, and efficiency. Higher horsepower rippers handle tougher materials and work faster but may consume more fuel, so efficiency is also important.
Functionality is critical. Look for adjustable shank depth for precise control and interchangeable shanks for flexibility. Ease of operation is key, with advanced models offering automated controls and GPS integration for enhanced precision and reduced manual adjustments.
Design
The design of a ripper impacts usability and maintenance. Ergonomic design features like comfortable seating and intuitive controls reduce operator fatigue and increase productivity. The layout should allow easy access to critical components for maintenance and repairs.
Build quality is crucial. High-quality materials like hardened steel for shanks and reinforced frames extend the ripper’s lifespan and reduce repair frequency. Proper weight distribution improves stability and reduces wear on tracks or tires.
Technical Specifications
Understanding the technical specifications of a ripper is essential. Key specifications include ripping depth, force, and shank size. The ripping depth indicates how deep the ripper can penetrate soil or rock, important for deep soil preparation or rock breaking.
Ripping force measures the power exerted by the ripper. Higher ripping force allows for more efficient breaking of tougher materials. Shank size and spacing affect coverage area and ripping efficiency, with larger shanks handling more substantial materials.
Safety Standards and Certifications
Safety is paramount when operating heavy machinery like rippers. Ensure the ripper complies with relevant safety standards and certifications, such as rollover protection structures (ROPS) and falling object protective structures (FOPS), to protect the operator in case of accidents.
Look for certifications from recognized bodies like the Occupational Safety and Health Administration (OSHA) or the International Organization for Standardization (ISO), indicating the ripper meets stringent safety and quality standards. Availability of safety training and support from the manufacturer is also important for reducing accident risks and improving safety.
Latest Technology Features in Rippers
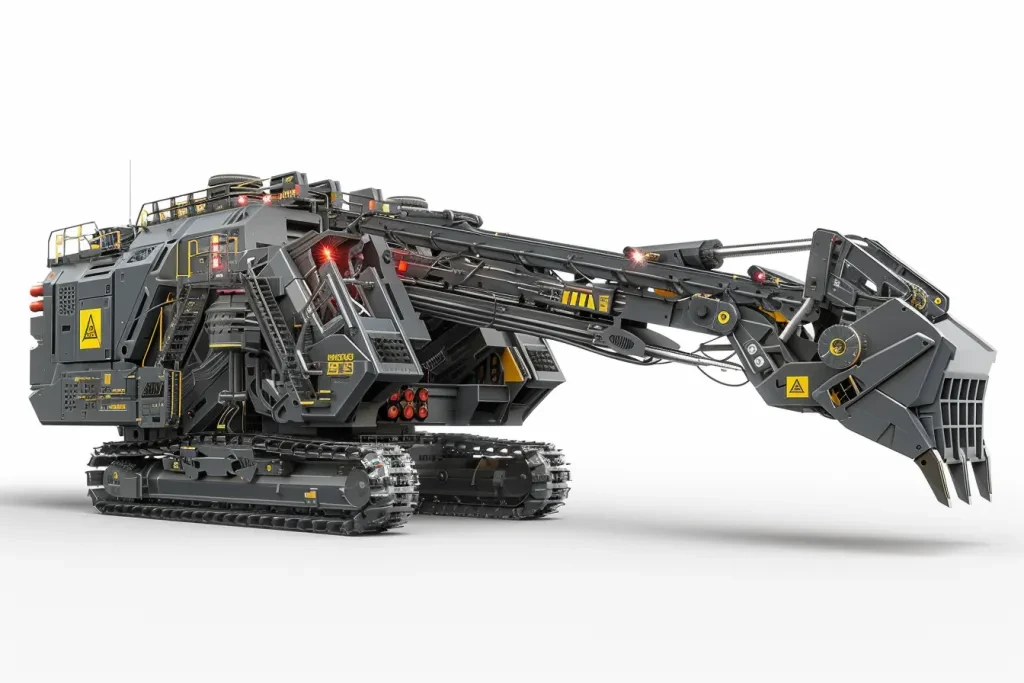
The ripper industry has seen significant technological advancements. Modern rippers are equipped with features enhancing performance, efficiency, and safety. One notable advancement is GPS integration, providing precise location data for accurate ripping patterns and reduced overlap.
Telematics systems offer real-time data on the machine’s performance, location, and maintenance needs, accessible remotely for better fleet management and timely maintenance. Automation and remote control capabilities are also becoming prevalent, reducing the risk of accidents and increasing efficiency by allowing operators to control the ripper from a safe distance, particularly useful in hazardous environments.
Durability and Quality

Durability and quality determine a ripper’s long-term value. High-quality materials and robust construction extend the machine’s lifespan. Look for rippers made from high-strength steel and other durable materials, and inspect welding quality and overall construction for weak points.
Regular maintenance is essential for durability and performance. Choose a ripper with easily accessible components and a comprehensive maintenance manual. Some manufacturers offer maintenance packages, including regular inspections and servicing, preventing costly repairs and downtime.
Budget and Price Range
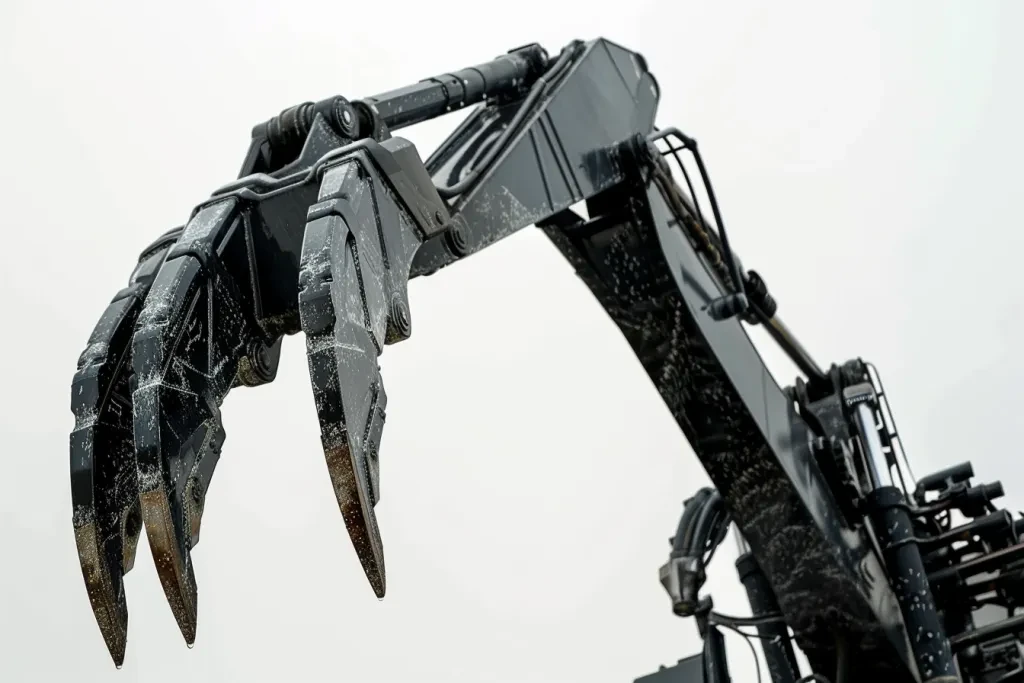
Ripper prices vary significantly based on type, features, and brand. Single shank rippers are generally more affordable than multi-shank and vibratory rippers. Consider the total cost of ownership, including maintenance, fuel consumption, and potential repairs, not just the initial cost.
Financing options from manufacturers and dealers can help manage upfront costs. Also, consider the resale value. High-quality, well-maintained rippers retain their value better, providing a higher return on investment when upgrading or replacing the machine.
Final Thoughts
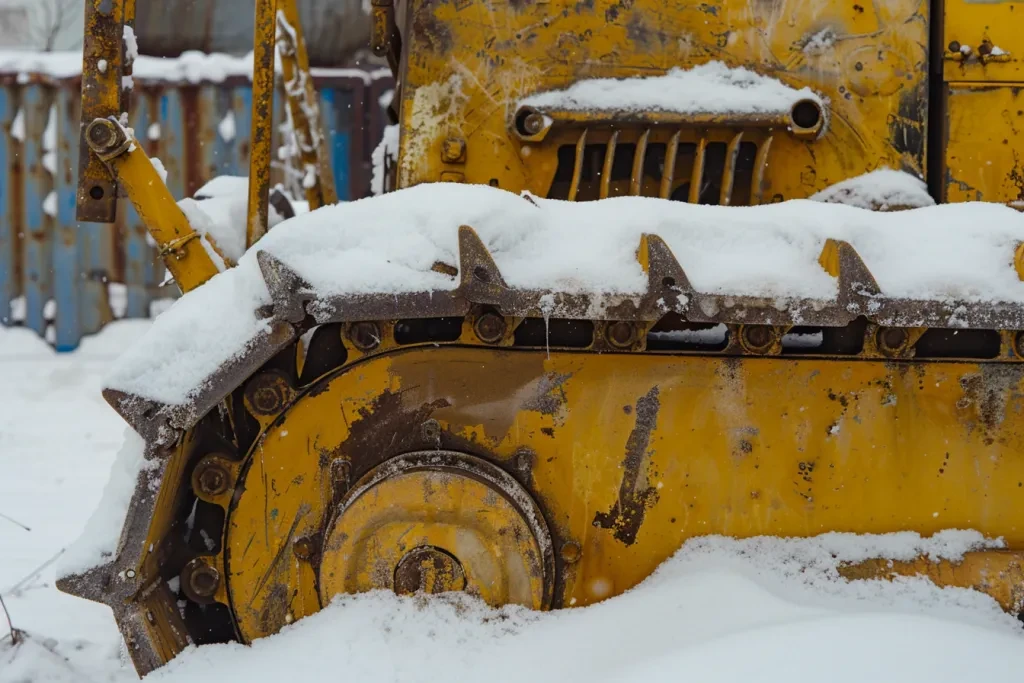
Selecting the right ripper involves careful consideration of various factors, including type, performance, design, technical specifications, safety standards, and budget. Understanding these key aspects helps make an informed decision that meets your needs and ensures long-term value and performance.