Recent advancements in mortising machine technology have revolutionized the woodworking industry, with the market projected to hit USD 2.5 billion by 2025. This article provides an in-depth analysis of the key factors in selecting a mortising machine, ensuring professional buyers make informed decisions. Discover valuable insights into market dynamics, performance benchmarks, and the latest innovations to enhance operational efficiency.
Table of Contents:
-Mortising Machine Market Overview
-In-Depth Analysis of the Mortising Machine Market
-Key Factors When Selecting a Mortising Machine
-Latest Technological Features in Mortising Machines
-Maintenance and Upgrade Potential
-Packaging Quality and Regulatory Compliance
-Summary
Mortising Machine Market Overview
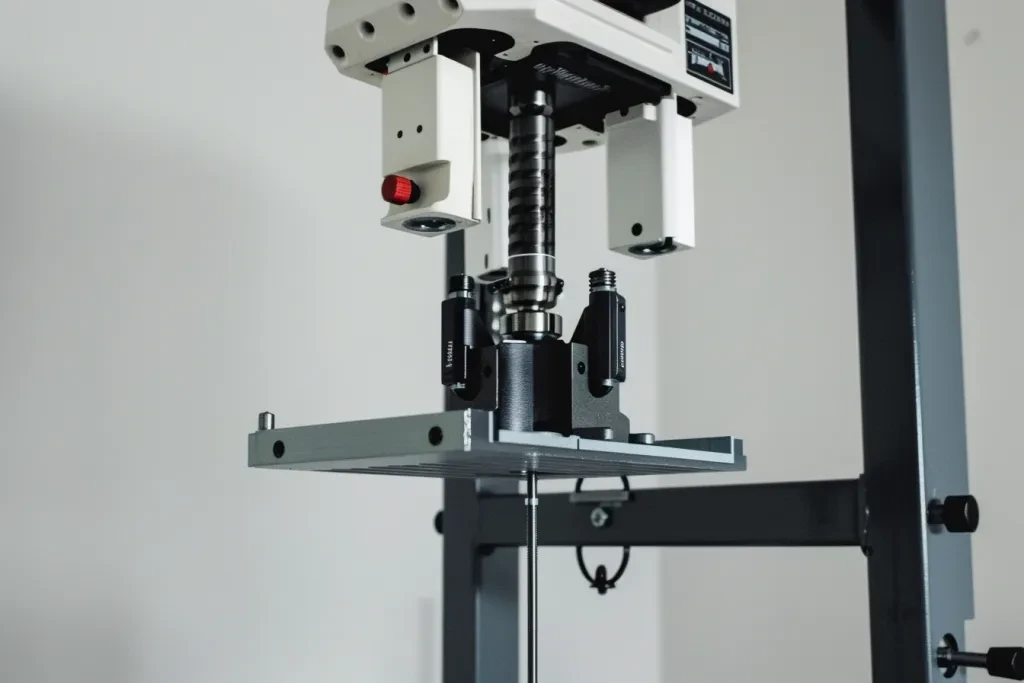
The global market for mortising machines has experienced significant growth, driven by the rising demand for precision woodworking equipment. By 2025, the market is valued at approximately USD 2.5 billion, with a projected compound annual growth rate (CAGR) of 4.5% over the next five years. This demand is primarily fueled by the increasing adoption of advanced woodworking technologies and the need for high efficiency and accuracy in wood joinery processes.
Regionally, the Asia-Pacific region holds the largest market share, accounting for 40% of the global mortising machine market. This dominance is due to the robust growth of the woodworking industry in countries like China, India, and Japan. North America and Europe follow with market shares of 25% and 20%, respectively. The remaining 15% is distributed across other regions, including Latin America, the Middle East, and Africa.
The market is segmented by product type, with horizontal mortising machines accounting for 60% of the market share, followed by vertical mortising machines at 30%, and chain mortisers at 10%. The end-user industries driving demand include furniture manufacturing, construction, and educational institutions.
In-Depth Analysis of the Mortising Machine Market
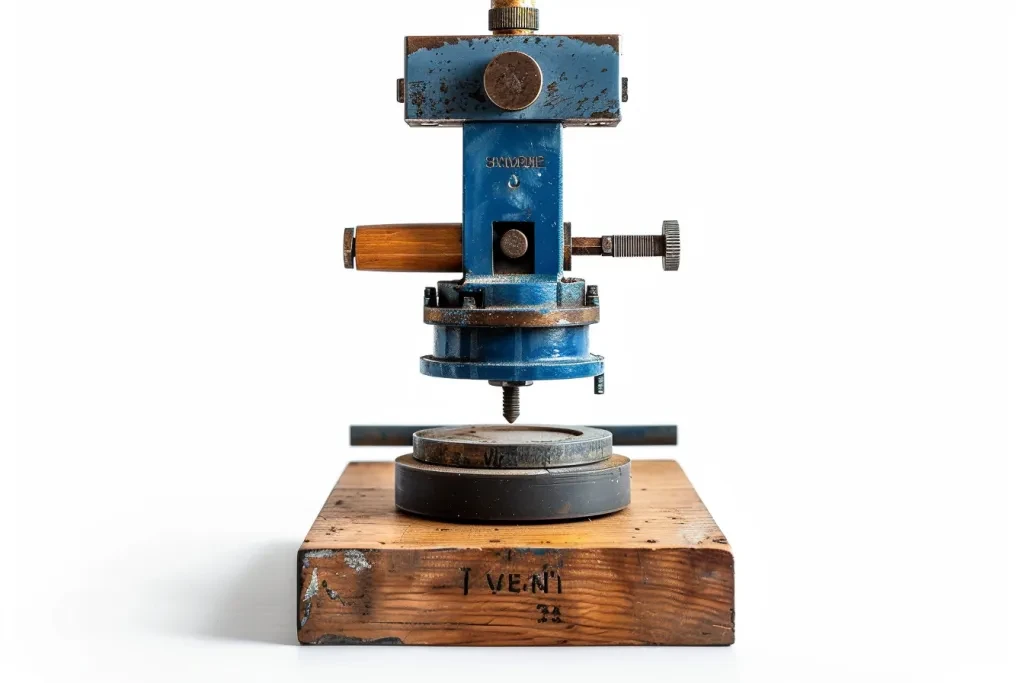
Key Performance Benchmarks
Mortising machines are evaluated based on precision, speed, and ease of use. Modern machines often incorporate computerized numerical control (CNC) systems, enhancing precision and repeatability. The integration of CNC technology has become a benchmark for high-performance mortising machines, allowing for intricate and precise wood joinery tasks.
Market Share Dynamics
The market is highly competitive, with leading manufacturers such as SCM Group, Felder Group, and Biesse Group holding substantial market shares. SCM Group leads with a 20% share, followed by Felder Group at 18%, and Biesse Group at 15%. These companies have established strong brand recognition and extensive distribution networks, contributing to their market dominance.
Economic Influences and Consumer Behavior Shifts
The economic landscape significantly impacts the mortising machine market. The growth of the woodworking industry, driven by increased consumer spending on home improvement and furniture, has positively influenced demand. Additionally, the trend towards DIY woodworking projects has increased the demand for user-friendly and affordable mortising machines.
Distribution Channel Preferences
Mortising machines are predominantly distributed through dealers and distributors, which account for 70% of sales. Direct sales to end-users and online marketplaces make up the remaining 30%. Dealers and distributors provide crucial after-sales services, including installation, training, and maintenance, vital for the optimal performance of mortising machines.
Recent Innovations
Recent innovations include the development of automated mortising systems that integrate IoT (Internet of Things) capabilities for predictive maintenance and real-time performance monitoring. These advancements reduce downtime and enhance operational efficiency, meeting the evolving needs of modern woodworking operations.
Product Lifecycle Stages
Mortising machines typically have a product lifecycle spanning several years, with key stages including introduction, growth, maturity, and decline. Currently, the market is in the growth stage, characterized by increasing adoption of advanced technologies and rising demand across various end-user industries.
Digitalization and Social Trends
Digitalization is transforming the mortising machine market, with manufacturers increasingly adopting digital platforms for sales, marketing, and customer support. Social trends, such as the growing interest in sustainable and eco-friendly woodworking practices, are also influencing the market. Manufacturers are responding by developing energy-efficient and environmentally friendly mortising machines.
Customer Pain Points
Key customer pain points in the mortising machine market include high initial investment costs, maintenance challenges, and the need for skilled operators. Addressing these pain points through innovative product designs, comprehensive training programs, and robust after-sales support is crucial for manufacturers to enhance customer satisfaction.
Brand Positioning Strategies
Leading brands position themselves based on reliability, precision, and technological innovation. SCM Group, for example, emphasizes its commitment to quality and customer-centric solutions, while Felder Group focuses on providing versatile and high-performance woodworking machines.
Differentiation Strategies
Manufacturers differentiate their products through unique features such as advanced CNC capabilities, user-friendly interfaces, and enhanced safety mechanisms. Offering customizable solutions to meet specific customer requirements is another effective differentiation strategy.
Niche Markets
Niche markets within the mortising machine industry include specialized woodworking applications such as musical instrument manufacturing and high-end custom furniture production. These markets demand exceptionally high precision and quality, presenting opportunities for manufacturers to cater to specific needs with tailored solutions.
Key Factors When Selecting a Mortising Machine
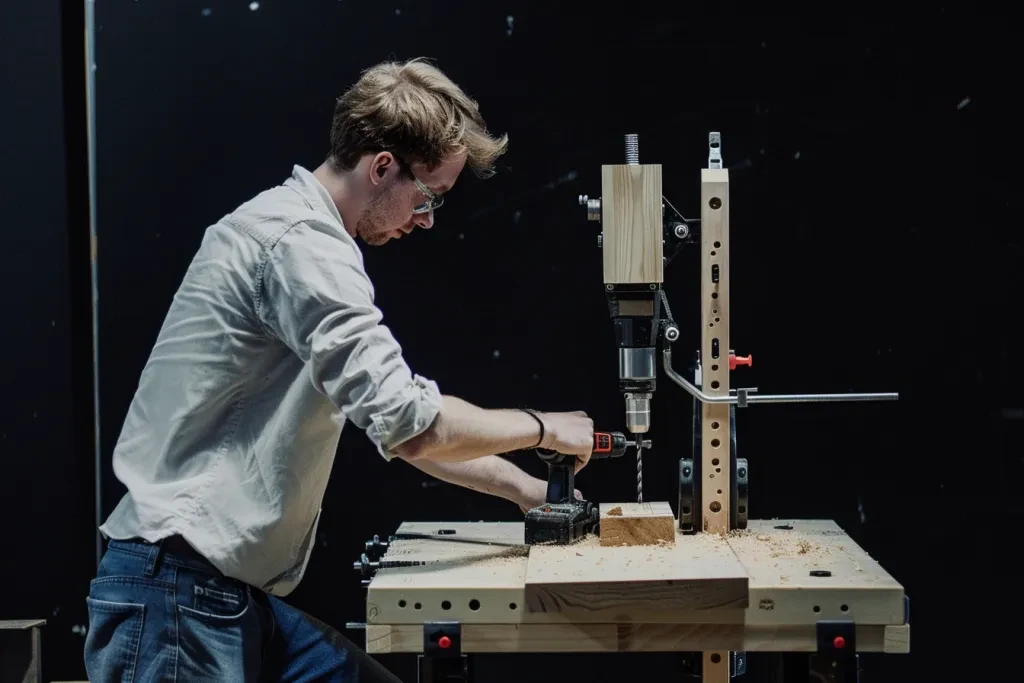
Types and Styles of Mortising Machines
Mortising machines are specialized woodworking tools designed to cut square or rectangular holes, or mortises, into a piece of wood. There are three main types: benchtop, floor-standing, and chain mortisers. Each type has its own advantages and is suitable for different applications.
Benchtop mortising machines are compact and portable, ideal for small workshops or hobbyists. They typically have a smaller capacity and are less powerful than floor-standing models. Despite their smaller size, benchtop mortisers can offer precise and clean cuts, often equipped with adjustable fences and hold-downs to secure the workpiece.
Floor-standing mortising machines are larger and more powerful, designed for heavy-duty use in professional woodworking shops. These machines can handle larger workpieces and more demanding tasks. They often come with advanced features such as multiple chisels, adjustable tables, and powerful motors, allowing for greater versatility and efficiency.
Chain mortisers are specialized machines used for cutting large mortises, especially in timber framing and log construction. They use a chain, similar to a chainsaw, to cut the mortise. Chain mortisers are highly efficient for cutting deep and wide mortises quickly, but they are generally more expensive and less versatile than other types of mortising machines.
Performance and Functionality
When selecting a mortising machine, performance and functionality are crucial factors to consider. The power of the motor, the machine’s capacity, and the precision of the cuts all affect overall performance.
The motor power determines the machine’s ability to handle different types of wood and the size of the mortises it can cut. Machines with more powerful motors can cut larger and deeper mortises more efficiently. For example, a floor-standing mortising machine with a 1.5 HP motor can handle heavy-duty tasks and dense hardwoods, while a benchtop model with a 0.5 HP motor might struggle with such materials.
The capacity of the machine, including the maximum size of the chisel and the maximum depth of cut, is another critical factor. A machine with a larger chisel capacity can cut wider mortises, essential for certain joinery techniques. The maximum depth of cut determines how deep the mortise can be, crucial for ensuring strong joints.
Precision is also vital, especially for fine woodworking. Features such as adjustable fences, hold-downs, and precision-ground cast-iron tables enhance the accuracy of the cuts. Some advanced models also include digital readouts or laser guides to further improve precision.
Technical Specifications
Understanding the technical specifications of a mortising machine is essential for making an informed decision. Key specifications to consider include spindle speed, chisel capacity, and table size.
Spindle speed, measured in revolutions per minute (RPM), affects cutting efficiency and the quality of the mortises. Higher spindle speeds typically result in cleaner cuts and faster operation. For example, a machine with a spindle speed of 3,500 RPM will generally produce smoother mortises than one with a speed of 2,500 RPM.
Chisel capacity indicates the maximum size of the chisel that the machine can accommodate. Larger chisels can cut wider mortises, necessary for larger joinery. A machine with a chisel capacity of 1 inch can handle most standard woodworking tasks, while a capacity of 1.5 inches or more is suitable for heavy-duty applications.
The size of the table determines the maximum size of the workpiece that the machine can handle. A larger table provides more support and stability for the workpiece, important for maintaining precision and safety. Some machines also feature adjustable tables that can tilt or rotate, allowing for more versatile cutting angles.
Safety Standards and Certifications
Safety is a paramount concern when working with mortising machines, as they involve high-speed cutting tools and powerful motors. Ensuring that the machine meets relevant safety standards and certifications is essential to protect operators and maintain a safe working environment.
Mortising machines should comply with international safety standards such as the International Organization for Standardization (ISO) and the American National Standards Institute (ANSI). These standards ensure that the machines are designed and manufactured to minimize risks and prevent accidents. For example, ISO 23125 sets safety requirements for machine tools, including mortising machines, covering aspects such as guarding, emergency stop functions, and electrical safety.
In addition to ISO and ANSI standards, some machines may also carry the CE mark, indicating compliance with European safety directives. The CE mark ensures that the machine meets essential health and safety requirements, including mechanical safety, electrical safety, and noise levels.
It is also important to consider the availability of safety features such as emergency stop buttons, blade guards, and dust extraction systems. These features can significantly reduce the risk of accidents and improve the overall safety of the working environment.
Price Range and Budget Considerations
The price of a mortising machine can vary significantly depending on its type, features, and brand. Understanding the price range and budget considerations can help you choose a machine that meets your needs without overspending.
Benchtop mortising machines are generally the most affordable, with prices ranging from $300 to $800. These machines are suitable for hobbyists and small workshops with limited budgets. Despite their lower price, many benchtop models offer good performance and precision for most woodworking tasks.
Floor-standing mortising machines are more expensive, with prices typically ranging from $1,000 to $3,000. These machines are designed for professional use and offer greater power, capacity, and durability. Investing in a floor-standing model can be worthwhile for commercial woodworking shops that require a reliable and efficient machine for heavy-duty tasks.
Chain mortisers are the most expensive, with prices starting at around $2,500 and going up to $5,000 or more. These machines are specialized for cutting large mortises in timber framing and log construction. While they represent a significant investment, their efficiency and speed can save time and labor costs in large-scale projects.
When setting a budget, it is important to consider not only the initial purchase cost but also the long-term costs of maintenance, accessories, and potential upgrades. Investing in a high-quality machine with a good warranty and reliable customer support can provide better value in the long run.
Latest Technological Features in Mortising Machines
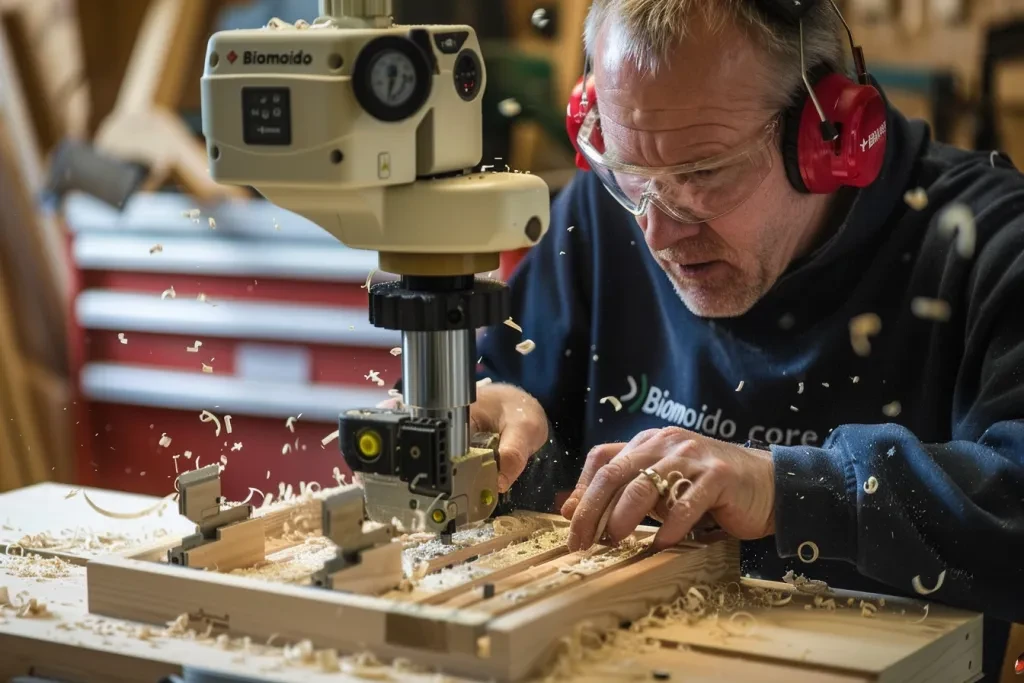
CNC and Automation
The integration of computer numerical control (CNC) and automation in mortising machines has revolutionized woodworking, offering unprecedented precision, efficiency, and versatility. CNC mortising machines use computer-controlled movements to cut mortises with high accuracy, making them ideal for complex and repetitive tasks.
CNC technology allows for the programming of intricate patterns and designs, which can be executed with minimal manual intervention. This not only improves the precision of the cuts but also reduces the risk of human error. For example, a CNC mortising machine can be programmed to cut multiple mortises with exact dimensions and spacing, ensuring consistent results across multiple workpieces.
Automation features, such as automatic tool changers and feed systems, further enhance the efficiency of CNC mortising machines. These features allow the machine to switch between different chisels and adjust the feed rate automatically, reducing downtime and increasing productivity. In a professional woodworking shop, the use of CNC and automation can significantly improve workflow and output.
Digital Readouts and Laser Guides
Digital readouts (DROs) and laser guides are advanced features that enhance the precision and ease of use of mortising machines. DROs provide real-time feedback on the position of the workpiece and the cutting tool, allowing for precise adjustments and accurate cuts.
Laser guides project a visible line or dot onto the workpiece, indicating the exact position and alignment of the chisel. This helps the operator to position the workpiece correctly and ensures that the cuts are made in the desired location. Laser guides are particularly useful for cutting multiple mortises with consistent spacing and alignment.
Both digital readouts and laser guides can significantly improve the accuracy and efficiency of mortising operations, making them valuable features for professional woodworkers and hobbyists alike.
Enhanced Dust Collection Systems
Dust collection is a critical aspect of woodworking, as it helps to maintain a clean and safe working environment. Mortising machines generate a significant amount of wood chips and dust, which can pose health risks and affect the performance of the machine.
Modern mortising machines are equipped with enhanced dust collection systems that effectively capture and remove dust and debris. These systems typically consist of a dust port connected to a vacuum or dust extractor, which draws the dust away from the cutting area. Some machines also feature built-in dust collection trays or hoods that contain the dust and prevent it from spreading.
Effective dust collection not only improves the safety and cleanliness of the workshop but also extends the lifespan of the machine by preventing dust buildup and clogging.
Maintenance and Upgrade Potential
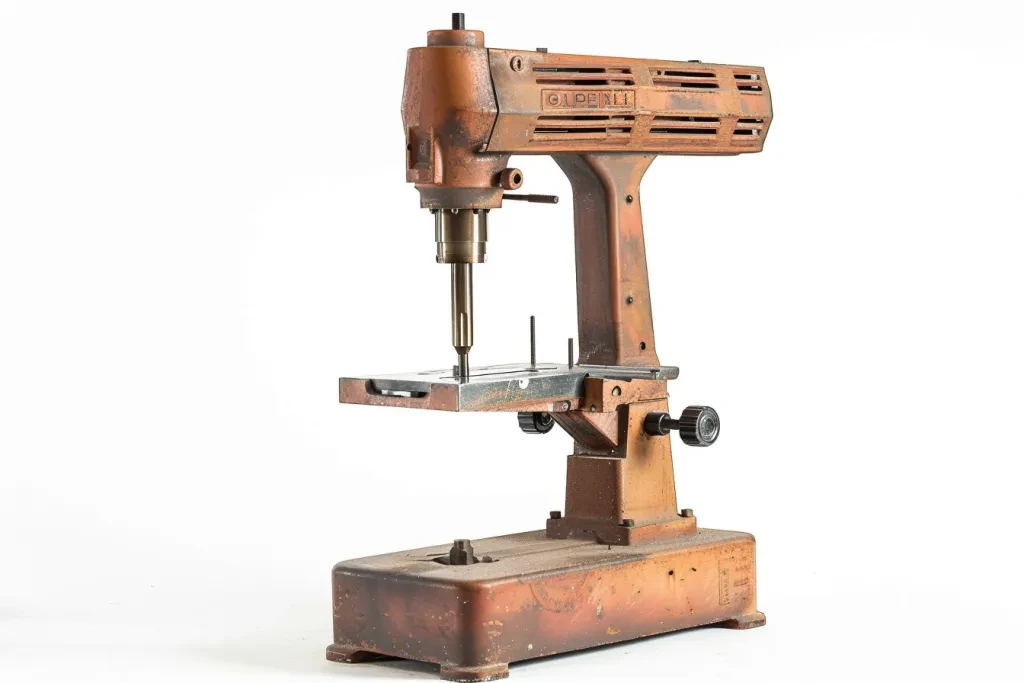
Regular Maintenance Practices
Regular maintenance is essential to keep a mortising machine in optimal condition and ensure its longevity. Key maintenance practices include cleaning, lubrication, and inspection.
Cleaning the machine after each use is crucial to prevent dust and debris buildup, which can affect the performance and accuracy of the cuts. The chisel and drill bit should be cleaned and sharpened regularly to maintain their cutting efficiency. Lubricating the moving parts, such as the spindle and table, helps to reduce friction and wear, ensuring smooth operation.
Periodic inspection of the machine is also important to identify and address any potential issues before they become major problems. Checking for loose bolts, worn-out parts, and alignment issues can help to maintain the machine’s performance and prevent breakdowns.
Compatibility with Future Upgrades
When selecting a mortising machine, it is important to consider its compatibility with future upgrades. Investing in a machine that can be easily upgraded or modified can provide greater flexibility and extend its useful life.
Compatibility with different types of chisels and drill bits is an important consideration. Some machines are designed to accommodate a wide range of chisel sizes and shapes, allowing for greater versatility in cutting different types of mortises. Additionally, machines with adjustable tables and fences can be easily modified to handle larger or more complex workpieces.
The ability to integrate advanced features, such as CNC controls or laser guides, is another valuable consideration. Machines that are designed with modular components and open architecture can be more easily upgraded with new technologies and features as they become available.
Product Lifespan and Resale Value
The lifespan of a mortising machine depends on its build quality, maintenance, and usage. High-quality machines made from durable materials, such as cast iron and steel, tend to have a longer lifespan and can withstand heavy use. Regular maintenance and proper care can further extend the machine’s life.
The resale value of a mortising machine is an important consideration for businesses that may need to upgrade or replace their equipment in the future. Machines from reputable brands with a proven track record of reliability and performance tend to have higher resale value. Additionally, machines that are well-maintained and equipped with advanced features can command higher prices in the used equipment market.
Investing in a high-quality mortising machine with good resale value can provide better return on investment and reduce the overall cost of ownership.
Packaging Quality and Regulatory Compliance
Packaging Quality
The packaging quality of a mortising machine is an important consideration, especially for businesses that need to transport or ship their equipment. High-quality packaging ensures that the machine is protected from damage during transit and arrives in good condition.
Packaging should include adequate cushioning, such as foam or padding, to absorb shocks and prevent movement. The machine should be securely fastened within the packaging to prevent it from shifting or tipping over. Additionally, the packaging should be clearly labeled with handling instructions and safety warnings to ensure proper handling.
Regulatory Compliance
Compliance with regulatory standards is essential to ensure that the mortising machine meets safety, performance, and environmental requirements. Machines should comply with relevant international and national standards, such as ISO, ANSI, and CE.
ISO standards, such as ISO 23125, set safety requirements for machine tools, including mortising machines. These standards cover aspects such as guarding, emergency stop functions, and electrical safety. ANSI standards provide guidelines for the design and operation of woodworking machines, ensuring that they are safe and reliable.
The CE mark indicates compliance with European safety directives, covering aspects such as mechanical safety, electrical safety, and noise levels. Machines with the CE mark meet essential health and safety requirements, providing assurance of their quality and safety.
Ensuring that the mortising machine complies with relevant regulatory standards not only enhances safety but also facilitates international trade and market access.
Summary
In summary, selecting the right mortising machine involves careful consideration of various factors, including the type and style of the machine, its performance and functionality, technical specifications, safety standards, and price range. Advanced features such as CNC controls, digital readouts, and enhanced dust collection systems can significantly improve the efficiency and precision of mortising operations. Regular maintenance and compatibility with future upgrades can extend the machine’s lifespan and provide better return on investment. Ensuring high packaging quality and regulatory compliance is essential for safe and reliable operation.