Industrial dryers are an important investment and one that should be considered carefully before a purchase is made. Technological advancements have also made drying equipment more complex and diverse. These changes make it challenging for non-experts to choose the right machine.
Given this, this article will help buyers to make the right purchasing decision by highlighting the key factors to consider before making a selection, as well as some of the most popular machines available on the market today.
Table of content
The global market for industrial dryers
Factors to consider when choosing an industrial dryer
Types of dryers
The global market for industrial dryers
The industrial dryers market was valued at $4 billion in 2015 and is estimated to grow at a compound annual growth rate (CAGR) of 4.3%, reaching $6.37 billion by 2026. Several factors are fuelling this growth, including increasing demand for these machines from several end-use industries like pharmaceutical, food, fertilizers, chemicals, minerals, cement, and paper & pulp. The industrial dryers’ ability to efficiently process large quantities of materials, thus helping industries to meet their drying goals, makes it an invaluable asset to various industries. And as a result the application of dryers in various sectors will continue to grow.
Factors to consider when choosing an industrial dryer
One of the most important steps in choosing the ideal dryer is to test wet materials on the drying equipment, ensuring that the final product is dry and is of the desired quality. However, before testing begins, here are six factors to consider when narrowing down on the drying system.
1. Size and density
The size and density of materials to be dried determine the size and capacity of the drying machine to be bought. For instance, smaller materials require different drying methods to larger ones. And as with size, the density of the material is also a key consideration. The density determines the movement of the material through the dryer, with denser material requiring different machines from the less dense ones.
2. Moisture content to be dried
It is also important to know the material’s moisture content at both the start and the end of the drying process. Testing the dryer in advance can help determine the dryer’s efficiency and whether it is the correct size. If the company detects variation from their end product moisture content goal, they should consider different dryer sizes.
It is also important to determine how the material to be dried is holding the moisture. For instance, a vaporizing machine will be sufficient if the moisture is only on the surface. However, if the material has absorbed the moisture content, a machine that thoroughly dries from the inside is needed. This factor also helps establish whether to add pre-dying requirements to the processing line.
3. Material handling
How the wet material is handled also plays a role when choosing a dryer. Sticky or sludgy materials are often forced into the dryer to prevent them from plugging the line. If the company handles sticky materials, the engineer could choose drying machines with non-stick surfaces or built-in paddles to keep the materials flowing.
The material’s abrasiveness and fragility are other factors to consider. If the company intends to dry fragile material, it should avoid drying equipment that roughly moves materials, and may opt for a machine that uses a gentler method. On the other hand, if the dried materials are abrasive, the company could choose abrasive resistant drying machines to prevent maintenance issues or damage.
4. Reaction to heat
Some materials are affected by heat and could react when they reach certain temperatures. If the machine is drying a chemical solution, it could result in a chemical reaction.
Also, certain heat sources could melt or burn some materials if they are exposed to certain temperatures for a long time. Therefore, the drying machine could be slower or larger to help lower the temperature. If the company deals in materials likely to melt, it could choose a dryer with a high temperature but short residence to prevent a possible product reaction.
5. Efficiency & cost
Cost consideration forms part of every major purchase. The company will consider the upfront capital cost when buying the machine and the operational costs during the machine’s lifetime. However, the upfront cost should not be the only determinant of the dryer’s cost-effectiveness because some machines may cost less upfront but operate inefficiently, thus costing more in the long run. And it is also essential to consider the type of fuel running the machine.
6. Production requirements
Finally, the dryer’s size should match the expected production levels. It’s worth considering whether the dryer will run continuously or operate in batches. If the company has large jobs that require a high output, using an undersized dryer will lead to clogging, and the operation could stop because it will overwhelm the machine. On top of this, the dryer could even burn out faster than expected. On the other hand, if an oversized dryer is selected, it will waste energy. It could also burn or over-dry the product.
Types of dryers
Drying equipment varies depending on the mechanism each uses to remove water content from the material being dried. The equipment also comes in various shapes, sizes, and capacities. Therefore, it is essential to know the targeted machine’s size, type, and specifications to make an informed decision. Here are a few types of drying machines to choose from:
Fluidized bed dryers
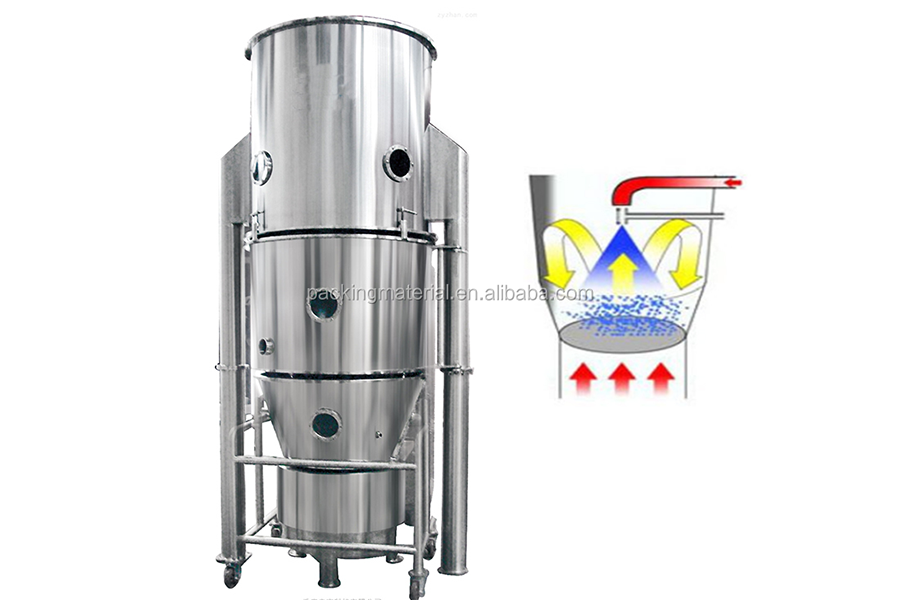
Fluidized Bed Dryers are often used in the pharmaceutical industries to dry pharmaceutical granules and powder. They use the fluidization principle to dry the materials — a process in which hot air is passed through a perforated bed of moist solid materials at high pressure to lift these materials from the bed. These moist granules or powder are then suspended in a stream of air, where they are heated. The resulting vaporized liquid is removed or partially recycled during the drying process, leaving the materials dried to the desired degree.
Pros
- The constant gas-particle movement generates strong heat, resulting in efficient moisture removal
- It achieves high thermal efficiency when the internal heat exchanger supplies drying thermal energy
- The initial capital and maintenance costs are relatively low
- It is relatively stable and easy to control
- It has limited residency time
Cons
- It consumes lots of energy due to the high-pressure drop needed to suspend the wet materials in the gas
- Maintaining high thermal efficacy requires extensive gas handling because of gas recirculation
- If the feed is extremely wet, the process will result in poor fluidization
- It is not ideal when the drying process involves removing organic solvents
- They are unsuitable when drying highly toxic or flammable solids because they could cause a fire or explosion
Rotary dryer
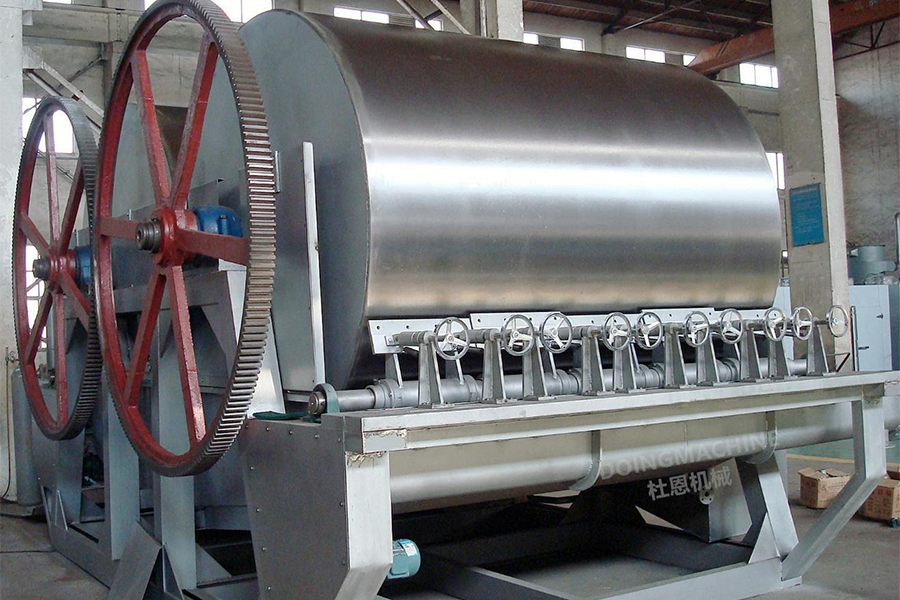
Rotary dryers are industrial drying equipment often used with bulk solids to reduce their moisture content by coming into contact with the heated gas.
This machine has a declined long drum fitted with internal lifters or flights. It rocks the materials when the drum slowly rotates as hot air passes through it.
The rotary dryer allows the feed material to directly interact with the hot air to flush out the moisture. However, the indirect rotary dryer has the hot air separated from the feed material by a tube or metal plate. It is therefore suitable for heat-sensitive materials. It can also perform both batch and continuous drying processes.
Pros
- It is not sensitive to particle size
- It is economical because of the low maintenance cost
- It has a bigger capacity than most dryers
Cons
- It can potentially cause excessive entrainment losses, especially if the feed material has extremely fine materials
Rolling bed dryer
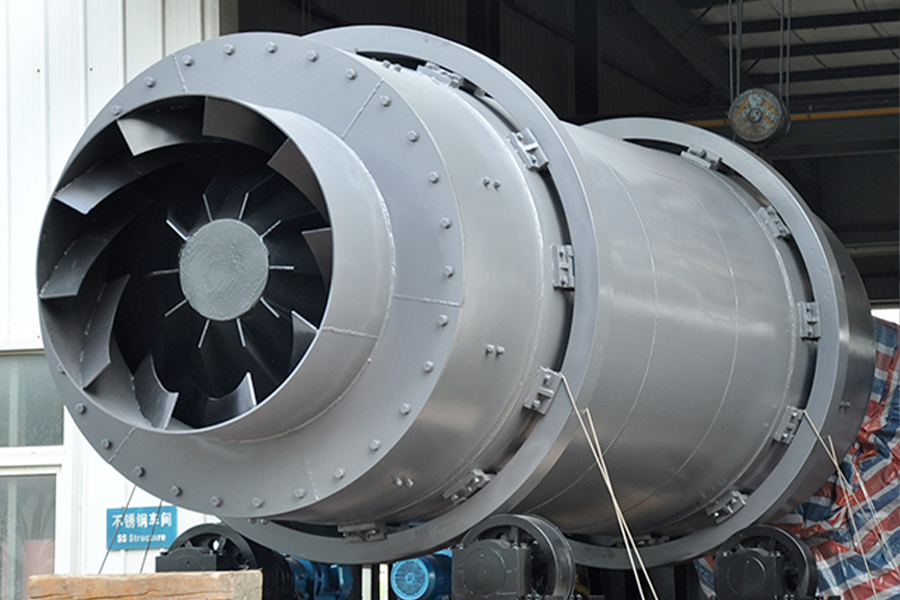
With the world’s growing interest in using biomass as a fuel source, the rolling bed dryer has become more popular. It combines the features of a fluidized bed dryer and drum dryer to dry any form of biomass.
Its design ensures a gentle and even drying process at low temperatures. It has a long residence time vital for biofuel and recycling/waste industries. It effectively dries large quantities of green waste, wood chips, and bio residues with residual energy.
The rolling bed dryer is fitted with a perforated plate where the product lies and is supplied with hot air from below. The product agitator continuously circulates the air as it effectively mixes the bulk material.
The machine has a high filling ratio, ensuring that hot air passes through several deflections before leaving the bulk. This heat exchange guarantees zero moist zones, thus creating an optimum drying result.
Pros
- The low-temperature capability ensures maximum efficiency since waste heat is easily recovered
- It performs highly even with large or entangling particles
- It has minimal processing costs since it uses residual energies
- It is universally used for numerous products
- It is explosion-proof and safe to operate
Cons
- The low temperature could result in insufficient product residence time
- Poor solid mixing
- Partial solid overheating
Convection dryers
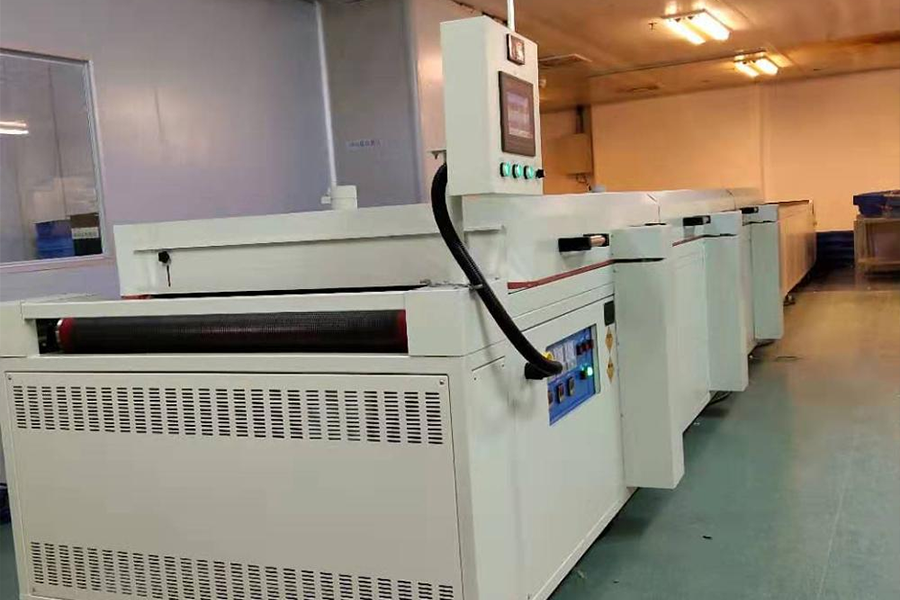
These dryers are often used in the food industry to dry solids. Convection dryers are equipped with four corrosion-free removable plates where feed materials are placed for drying.
Once the food is placed in the drying channel, the plates are exposed to the hot air blown through the channel. The hot air will heat the solid material, removing any moisture. Furthermore, the air can be pre-heated and its velocity regulated to meet the drying needs.
Pros
- It has heat and mass transfer
- It ensures uniform heating regardless of the product’s color, size, or shape
- It allows for accurate temperature control
Cons
- It achieves lower heat transfer than most heating methods
- Airflow can contaminate the product
- It needs increased product residence time
- It relies on the product’s thermal conductivity to heat its thick interior
Conclusion
Industrial dryers can be an invaluable asset to many businesses and have many useful applications that will see a growing demand over the coming years. However, considering their hefty price tag, purchasing an industrial dryer is a decision that should be approached carefully. This guide has therefore outlined some key points to consider when choosing an industrial dryer so that businesses can be sure to find the suitable model for their budget and needs.