In 2025, the hat knitting machine market is set to evolve with cutting-edge technologies and increased automation. This article delves into the latest trends, key players, and essential features to consider when selecting a hat knitting machine. Professional buyers will find valuable insights to make informed decisions, ensuring their businesses stay competitive and efficient.
Table of Contents:
– Understanding the Hat Knitting Machine Market
– Types of Hat Knitting Machines
– Key Features to Look for in a Hat Knitting Machine
– Quality and Durability Considerations
– Budget and Cost Analysis
– Technological Advancements in Hat Knitting Machines
Understanding the Hat Knitting Machine Market
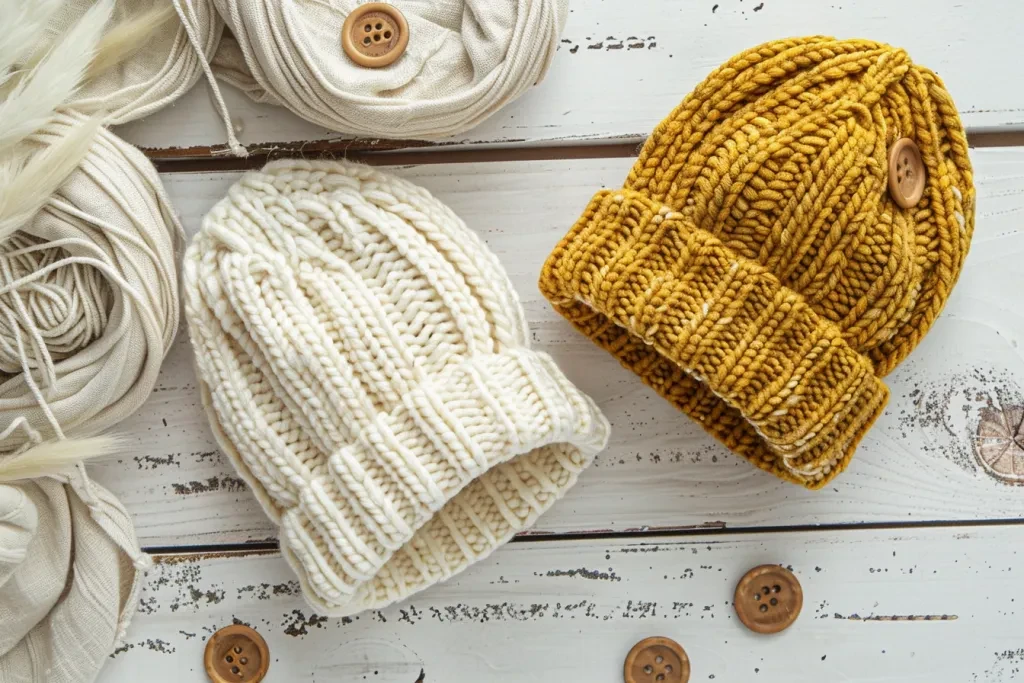
Key Market Players
The hat knitting machine market is dominated by several key players who have established themselves through innovation and quality. Companies such as Shima Seiki Mfg., Ltd., Stoll (a part of Karl Mayer Group), and Santoni S.p.A. are leading the market with their advanced knitting technologies. Shima Seiki, for instance, has been at the forefront with its WHOLEGARMENT technology, which allows for seamless knitting, significantly reducing production time and material waste. Stoll, known for its flat knitting machines, has integrated Industry 4.0 capabilities, enhancing machine efficiency and connectivity.
In 2024, the market saw a significant increase in the adoption of automated hat knitting machines, driven by the need for higher productivity and precision. Companies like Santoni have introduced circular knitting machines that cater specifically to the hat manufacturing sector, offering high-speed production and versatility in design. The competitive landscape is further intensified by the entry of new players from the Asia-Pacific region, particularly China and India, where the textile machinery industry is rapidly growing.
The market dynamics are also influenced by strategic partnerships and acquisitions. For example, in 2023, Shima Seiki acquired a smaller European knitting machine manufacturer to expand its product portfolio and market reach. This trend of consolidation is expected to continue, with major players seeking to enhance their technological capabilities and market presence through mergers and acquisitions.
Global Demand and Supply Trends
The global demand for hat knitting machines is projected to grow at a CAGR of 5.2% from 2024 to 2030, driven by the increasing popularity of knitted hats in fashion and sportswear. The Asia-Pacific region, particularly China and India, is expected to lead the market growth due to the booming textile industry and rising disposable incomes. In 2024, the Asia-Pacific region accounted for 45% of the global market share, with China being the largest producer and exporter of hat knitting machines.
Supply chain dynamics have also evolved, with manufacturers focusing on reducing lead times and enhancing machine efficiency. The integration of IoT and AI in knitting machines has enabled real-time monitoring and predictive maintenance, significantly reducing downtime and operational costs. For instance, Stoll’s CMS 530 HP+ machine features advanced sensors and connectivity options, allowing for seamless integration into smart factory environments.
The demand for sustainable and eco-friendly knitting solutions is another key trend shaping the market. Consumers are increasingly seeking products made from organic and recycled materials, prompting manufacturers to develop machines capable of handling such materials efficiently. In response, companies like Shima Seiki have introduced machines with enhanced capabilities for knitting with sustainable fibers, aligning with the global push towards sustainability in the textile industry.
Types of Hat Knitting Machines
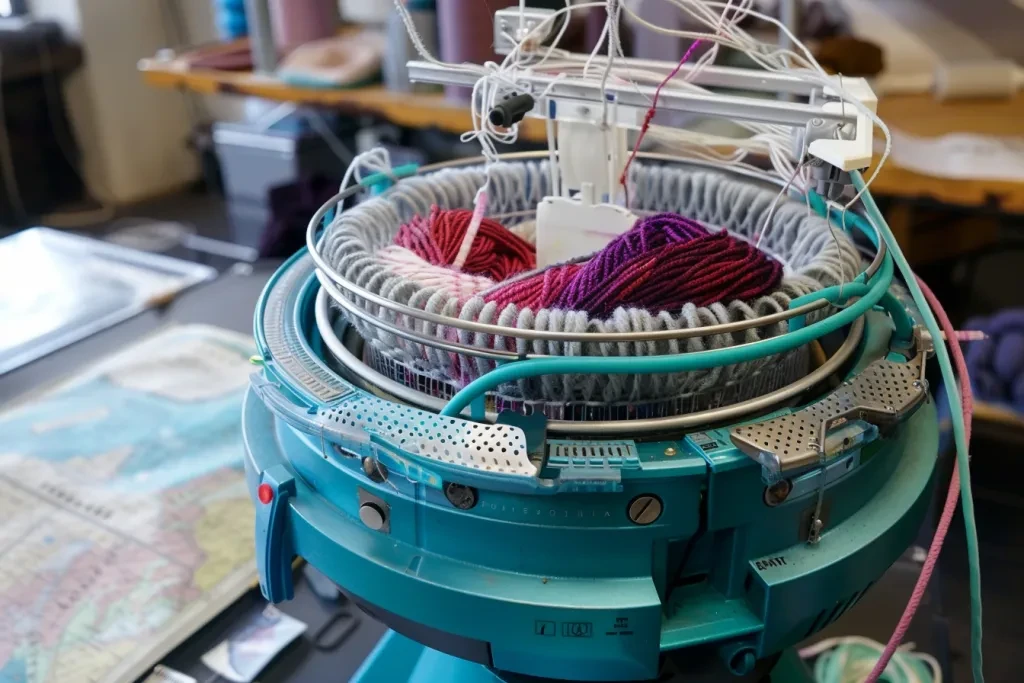
Circular Knitting Machines
Circular knitting machines are widely used in the production of hats due to their high-speed capabilities and ability to produce seamless garments. These machines operate by knitting in a continuous circular motion, which is ideal for creating tubular structures like hats. The market for circular knitting machines is expected to grow at a CAGR of 4.8% from 2024 to 2030, driven by advancements in machine technology and increasing demand for high-quality knitted hats.
One of the leading manufacturers, Santoni, has developed the SM8-TOP2V machine, which is specifically designed for hat production. This machine offers high productivity, with the ability to knit up to 1,200 hats per day, and features advanced electronic controls for precise patterning and stitch formation. The integration of automated yarn feeders and tension controls further enhances the machine’s efficiency and output quality.
The adoption of circular knitting machines is particularly high in the Asia-Pacific region, where manufacturers are investing in advanced machinery to meet the growing demand for knitted hats. In 2024, the region accounted for 55% of the global market share for circular knitting machines, with China and India being the largest consumers. The trend towards automation and digitalization in the textile industry is expected to further drive the adoption of circular knitting machines in the coming years.
Flat Bed Knitting Machines
Flat bed knitting machines are another popular choice for hat production, offering versatility in design and the ability to produce complex patterns. These machines operate by knitting in a back-and-forth motion, allowing for greater control over stitch formation and patterning. The market for flat bed knitting machines is projected to grow at a CAGR of 5.5% from 2024 to 2030, driven by the increasing demand for customized and intricate hat designs.
Stoll’s ADF 530-24 machine is a prime example of advanced flat bed knitting technology, featuring 24 yarn carriers and a multi-gauge capability, allowing for the production of a wide range of hat styles. The machine’s advanced software enables precise control over stitch density and patterning, making it ideal for high-end fashion and sportswear applications. The integration of Industry 4.0 capabilities further enhances the machine’s efficiency and connectivity.
The demand for flat bed knitting machines is particularly strong in Europe and North America, where consumers prefer high-quality, customized hats. In 2024, these regions accounted for 40% of the global market share for flat bed knitting machines. The trend towards personalization and customization in fashion is expected to drive further growth in this segment, with manufacturers focusing on developing machines that offer greater design flexibility and efficiency.
Single and Double Jersey Machines
Single and double jersey machines are essential in the production of various types of knitted hats, offering different fabric structures and properties. Single jersey machines produce lightweight, stretchy fabrics, making them ideal for casual and sports hats. Double jersey machines, on the other hand, produce thicker, more stable fabrics, suitable for winter hats and beanies. The market for single and double jersey machines is expected to grow at a CAGR of 4.9% from 2024 to 2030, driven by the diverse applications of these machines in hat production.
Shima Seiki’s MACH2XS machine is a leading example of double jersey knitting technology, featuring a unique slide needle design that allows for the production of complex patterns and textures. The machine’s advanced electronic controls enable precise stitch formation and patterning, making it ideal for high-quality hat production. The integration of automated yarn feeders and tension controls further enhances the machine’s efficiency and output quality.
The demand for single and double jersey machines is particularly high in the Asia-Pacific region, where manufacturers are investing in advanced machinery to meet the growing demand for knitted hats. In 2024, the region accounted for 50% of the global market share for single and double jersey machines, with China and India being the largest consumers. The trend towards automation and digitalization in the textile industry is expected to further drive the adoption of single and double jersey machines in the coming years.
Key Features to Look for in a Hat Knitting Machine
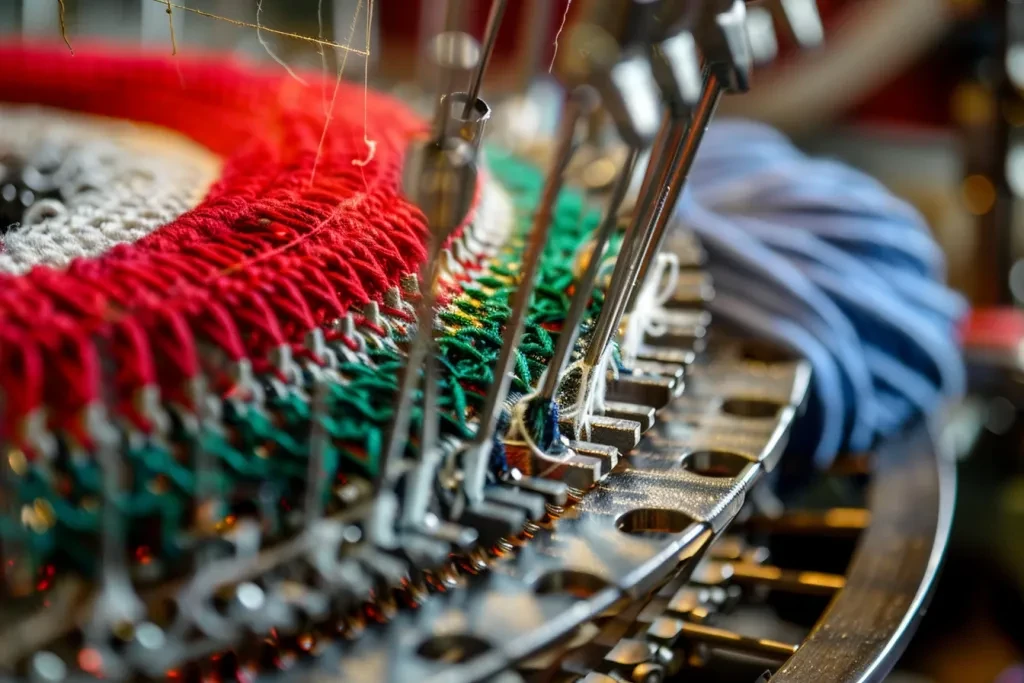
Production Speed
Production speed is a critical factor when selecting a hat knitting machine. High-speed machines can produce up to 1,200 hats per hour, significantly increasing output and efficiency. For instance, the Shima Seiki MACH2XS series offers a maximum knitting speed of 1.6 meters per second, making it ideal for large-scale production. Additionally, machines with adjustable speed settings allow operators to optimize production based on the complexity of the design and the type of yarn used.
Machine Versatility
Versatility in a hat knitting machine is essential for meeting diverse market demands. Machines that can handle various knitting techniques, such as ribbing, jacquard, and intarsia, provide greater flexibility. For example, the Stoll CMS 530 HP can switch between different knitting styles seamlessly, enabling the production of a wide range of hat designs. Furthermore, machines with interchangeable knitting heads can adapt to different yarn types and thicknesses, enhancing their versatility.
Ease of Maintenance
Ease of maintenance is a crucial consideration to minimize downtime and extend the machine’s lifespan. Machines with modular components and easy access panels simplify routine maintenance tasks. The Lonati GL616, for instance, features a user-friendly design that allows quick replacement of parts without specialized tools. Additionally, automated lubrication systems and self-cleaning mechanisms reduce the need for frequent manual interventions, ensuring consistent performance.
Yarn Compatibility
Yarn compatibility is vital for producing high-quality hats with various textures and finishes. Machines that support a wide range of yarn types, including wool, cotton, and synthetic fibers, offer greater production flexibility. The Mayer & Cie. OVJA 1.6 EE 3WT/2WT, for example, can handle multiple yarn types and gauges, making it suitable for diverse knitting projects. Moreover, adjustable tension settings ensure uniform stitch quality across different yarns, enhancing the final product’s appearance.
Digital Controls and Automation
Digital controls and automation significantly enhance the efficiency and precision of hat knitting machines. Advanced machines equipped with computerized control systems, such as the Santoni SM8-TOP2V, allow for precise pattern programming and real-time monitoring. Automation features, including automatic yarn feeders and tension adjusters, reduce manual intervention and improve consistency. Additionally, integration with IoT platforms enables remote diagnostics and predictive maintenance, further optimizing production processes.
Quality and Durability Considerations
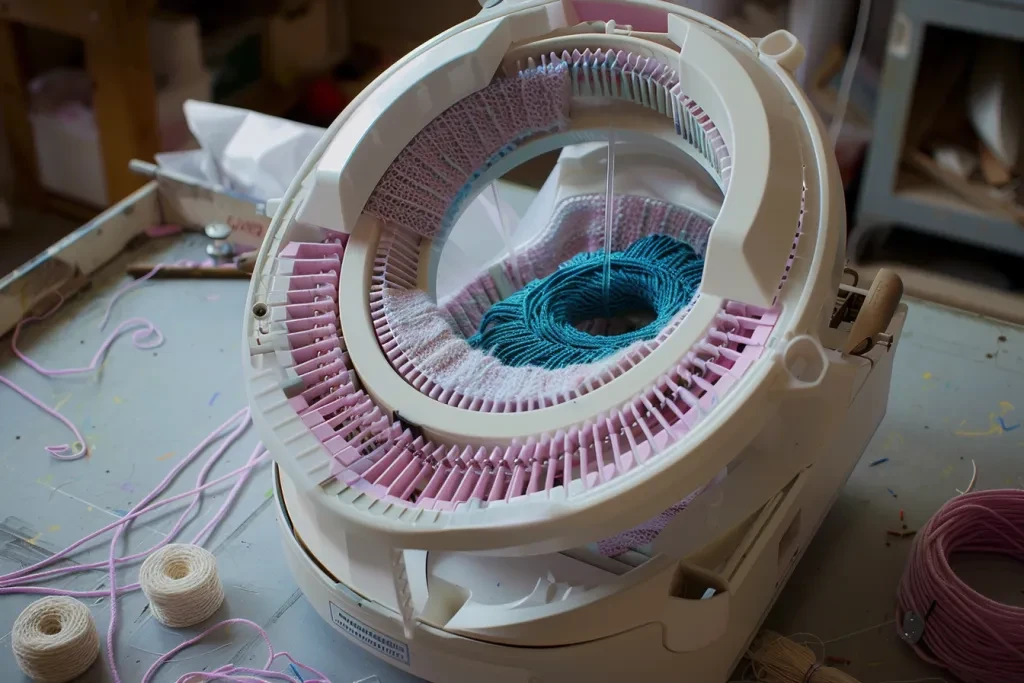
Material Construction
The material construction of a hat knitting machine directly impacts its durability and performance. Machines built with high-grade steel and aluminum components offer superior strength and resistance to wear and tear. For instance, the Terrot UCC572-T features a robust frame made from reinforced steel, ensuring long-term stability and reliability. Additionally, corrosion-resistant coatings and heat-treated parts enhance the machine’s lifespan, even under continuous operation.
Brand Reputation
Brand reputation is a key indicator of a machine’s quality and reliability. Established brands like Shima Seiki, Stoll, and Mayer & Cie. are known for their innovative designs and high-performance machines. These manufacturers often provide extensive customer support and training programs, ensuring optimal machine operation. Furthermore, industry reviews and user testimonials can offer valuable insights into the machine’s performance and after-sales service, aiding in the decision-making process.
Warranty and Support Services
Warranty and support services are critical factors to consider when investing in a hat knitting machine. Comprehensive warranties that cover parts and labor for an extended period provide peace of mind and protect against unexpected repair costs. For example, the Lonati GL616 comes with a two-year warranty and access to a global network of service centers. Additionally, manufacturers that offer 24/7 technical support and on-site maintenance services ensure minimal downtime and prompt resolution of issues.
Budget and Cost Analysis
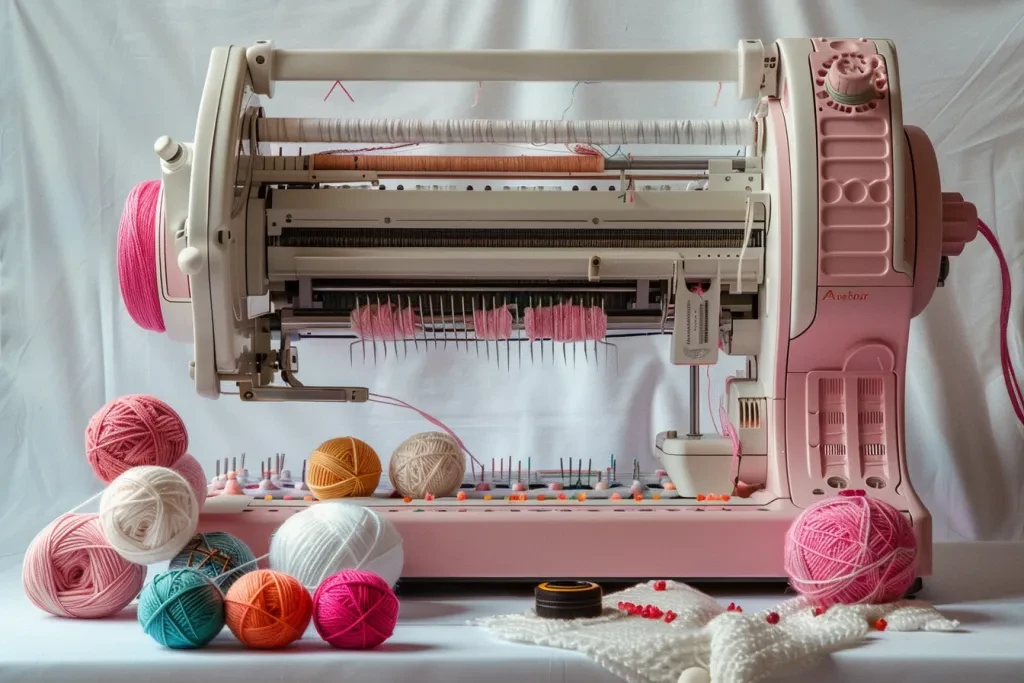
Initial Investment
The initial investment in a hat knitting machine can vary significantly based on its features and capabilities. High-end machines with advanced automation and digital controls can cost upwards of $100,000. However, entry-level models suitable for small-scale production may be available for around $20,000. It’s essential to balance the machine’s cost with its expected productivity and the specific needs of the business. Financing options and leasing programs can also help manage the initial investment.
Operating Costs
Operating costs include expenses related to energy consumption, maintenance, and labor. Machines with energy-efficient motors and automated features can reduce electricity usage and labor costs. For instance, the Stoll CMS 530 HP is designed to minimize power consumption while maintaining high production speeds. Regular maintenance and the availability of affordable spare parts also play a crucial role in managing operating costs. Predictive maintenance technologies can further optimize maintenance schedules and reduce unexpected expenses.
Return on Investment (ROI)
Calculating the return on investment (ROI) involves assessing the machine’s productivity, operating costs, and the potential revenue generated from the hats produced. A high-speed, versatile machine like the Shima Seiki MACH2XS can significantly boost production capacity, leading to higher sales and faster ROI. Additionally, machines that offer customization options and high-quality output can command premium prices in the market, further enhancing profitability. It’s essential to conduct a thorough cost-benefit analysis to determine the machine’s financial viability.
Technological Advancements in Hat Knitting Machines
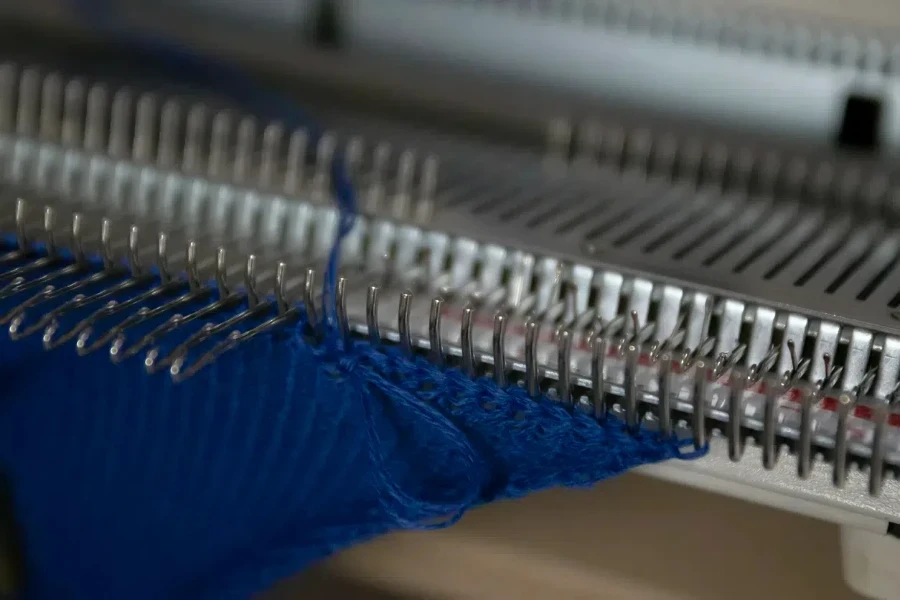
Integration of IoT
The integration of IoT in hat knitting machines is revolutionizing the industry by enabling real-time monitoring and data analytics. IoT-enabled machines, such as the Santoni SM8-TOP2V, can transmit performance data to cloud-based platforms, allowing for remote diagnostics and predictive maintenance. This connectivity helps identify potential issues before they cause downtime, optimizing machine efficiency. Additionally, IoT integration facilitates seamless communication between machines and production management systems, enhancing overall workflow.
AI and Machine Learning Enhancements
AI and machine learning are enhancing the capabilities of hat knitting machines by improving pattern recognition and production efficiency. Advanced algorithms can analyze production data to optimize knitting patterns and adjust machine settings in real-time. For example, the Mayer & Cie. OVJA 1.6 EE 3WT/2WT utilizes machine learning to predict yarn behavior and adjust tension settings automatically. These enhancements lead to higher quality output and reduced waste, making production more cost-effective.
Sustainability and Energy Efficiency Trends
Sustainability and energy efficiency are becoming increasingly important in the hat knitting industry. Modern machines are designed to minimize energy consumption and reduce environmental impact. The Terrot UCC572-T, for instance, features energy-efficient motors and eco-friendly materials. Additionally, manufacturers are focusing on developing machines that can utilize recycled and biodegradable yarns, aligning with global sustainability goals. These trends not only benefit the environment but also appeal to eco-conscious consumers, enhancing brand reputation.
Making the Final Decision
When making the final decision on a hat knitting machine, it’s essential to consider production needs, budget constraints, and technological advancements. Evaluating these factors will ensure the selection of a machine that meets both current and future production requirements.