In the rapidly evolving landscape of industrial automation, selecting the right programmable logic controller (PLC) is more critical than ever for optimizing operations.
In this article, we provide an in-depth exploration of PLC options, key factors to consider when choosing a system, and essential regulatory requirements to ensure compliance. Read on to find a suitable programmable logic control system whose technical specifications meet your industrial automation targets.
Table of Contents
– Programmable logic control options on the market
– What to consider when choosing a PLC system
– Regulatory and compliance requirements
– Summary
Programmable logic control options on the market
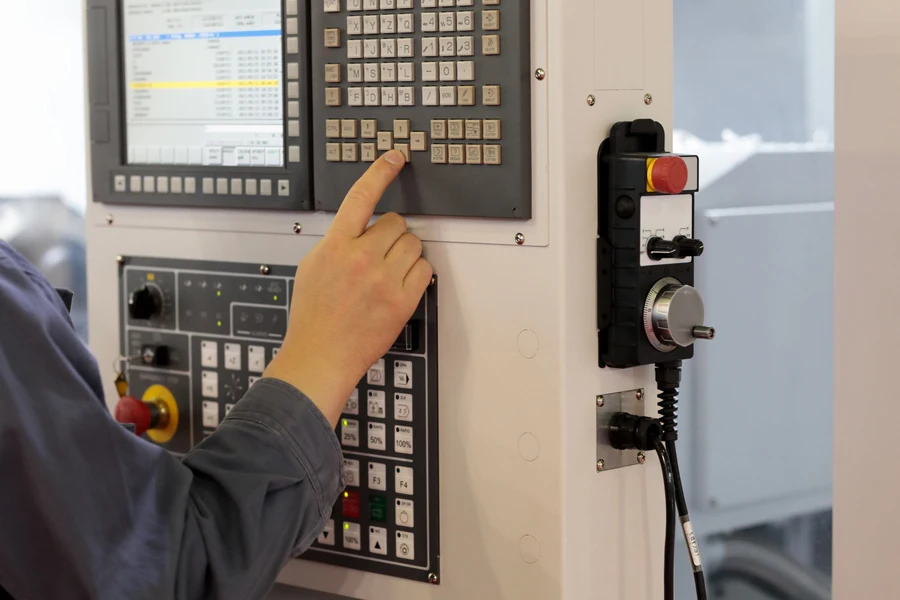
The typical programmable logic control systems you’ll come across include:
PLCs in compact form
Fixed I/O PLCs – also known as compact PLCs – integrate the CPU, power supply, and I/O points in one device. Their space-saving design and economy make them perfect for smaller applications with low I/O needs.
Usually used in small manufacturing cells, packing tools, and standalone machines across a range of sectors, these PLCs are simple to install and maintain. However, compared to modular systems, they lack expansion flexibility.
PLCs with modular construction
The greater flexibility and scalability offered by modular PLCs make them appropriate for larger-scale and challenging industrial uses. Unlike small PLCs, modular systems divide the CPU, power supply, and I/O units so that modules can be added or replaced as needed.
Because malfunctioning modules may be rapidly switched without compromising the whole system, this modularity helps to reduce downtime and improve troubleshooting. As such, large manufacturing facilities, automotive assembly lines, and process sectors where flexibility and high I/O capacity are critical use them extensively.
Rack-mounted PLCs
Designed for large-scale uses, rack-mounted PLCs hold several modules – including CPU, power supply, and I/O modules – using a chassis or rack. These systems are built to survive demanding industrial conditions and provide several I/O ports.
Their modular character facilitates great performance and comprehensive customization, which qualifies them for centralized control in water treatment, power generation, and broad process control activities.
What to consider when choosing a PLC system
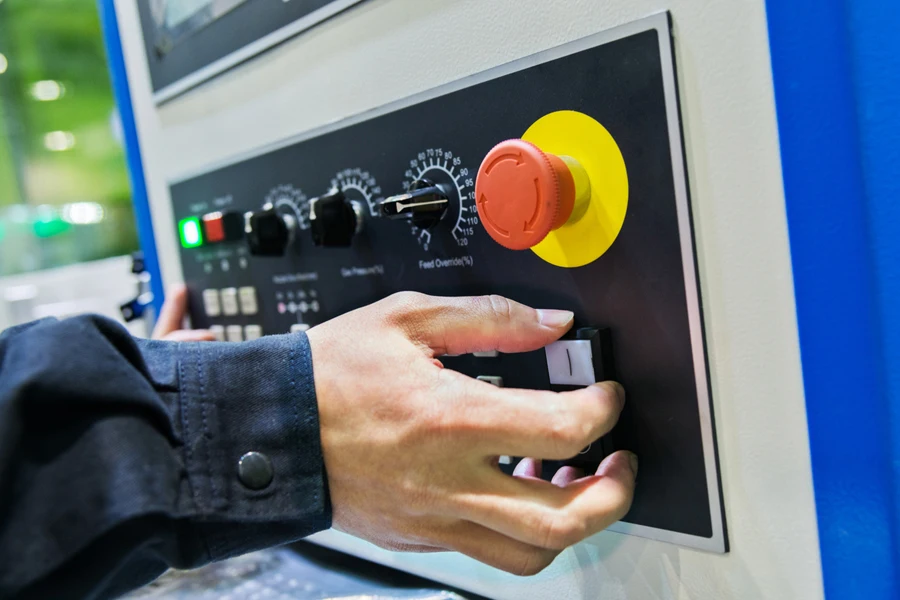
This is what you need to know when looking for a reliable programmable logic control system:
1. Application requirements
To determine application requirements, consider the machine’s intended purpose. Different industries have distinct requirements. For example, the food and beverage industry may require PLCs that can operate in washdown situations. Oil and gas? You’ll most likely need explosion-proof systems.
Also, think about how complex your procedures are. A modest machine may do well with a compact PLC, but if you are running a complex assembly line, you will require something more durable.
Environment also plays a big part on which PLC system will be suitable. Temperature fluctuations, humidity levels, and vibration can all significantly impact performance. Ideally, you’ll want a system that can withstand anything you throw at it.
2. Technical specifications
Specifications will also play a big part in determining which PLC system is right. How many inputs and outputs are needed? How about processing speed and memory? These specifications define how successfully the PLC will be able to manage various tasks.
Communication is also important. Make sure that the PLC you choose communicates in the same language as the other equipment it will be hooked up to – you don’t want a system that doesn’t work well with the rest of the setup.
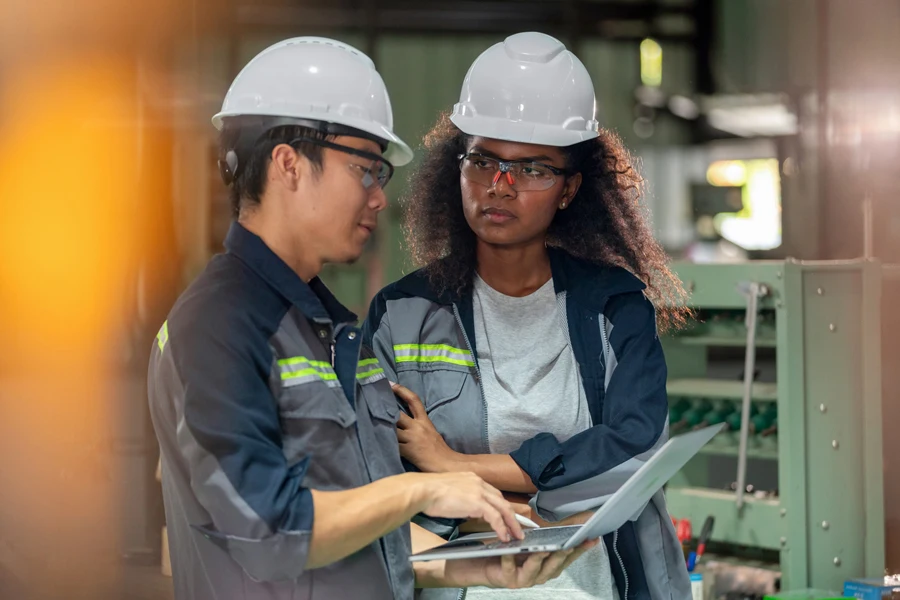
3. Scalability and flexibility
Plan for future scalability and flexibility. Your industry is likely to grow over time, and the PLC should be able to keep up. Look for systems with scaling options. Industry-standard software is also a solid bonus, making future upgrades less strenuous.
4. Manufacturer and vendor reputation
A trusted brand can be worth its weight in gold, and good technical help can help reduce issues in the long run. Research a brand’s track record and what others have said about customer service, etc.
5. Budget constraints
Budget isn’t just about the upfront cost; consider long-term expenses like maintenance and upgrades. Sometimes, investing a little extra initially can help over time.
Remember that the cheapest model may not always be the most cost-effective in the long run.
Regulatory and compliance requirements
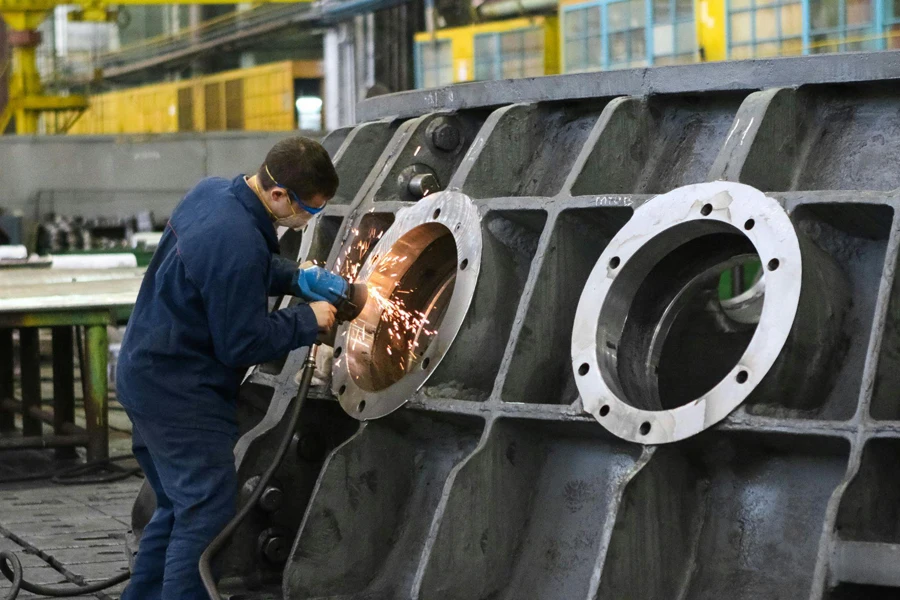
Your automation system must adhere to all applicable laws and industry standards to guarantee safe and effective operations. As such, pay close attention to:
Industry standards
Groups like NEMA or the International Electrotechnical Commission (IEC) are responsible for creating these standards. The IEC 61131 standard offers specifications for PLC programming languages, contributing to various systems’ uniformity and compatibility.
If you follow these guidelines, you’re likely to encounter fewer issues when integrating PLCs with other equipment, as well as when conducting employee training.
Various sectors adhere to distinct sets of regulations. Part 11, which addresses electronic records and signatures, is one example of an FDA regulation that pharmaceutical industry professionals may be required to follow.
Considerations such as ISO/TS 16949 and requirements for quality management systems in the automotive industry may impact PLC selection. Before deciding on a PLC system, ensure familiarity with the standards in a specific industry.
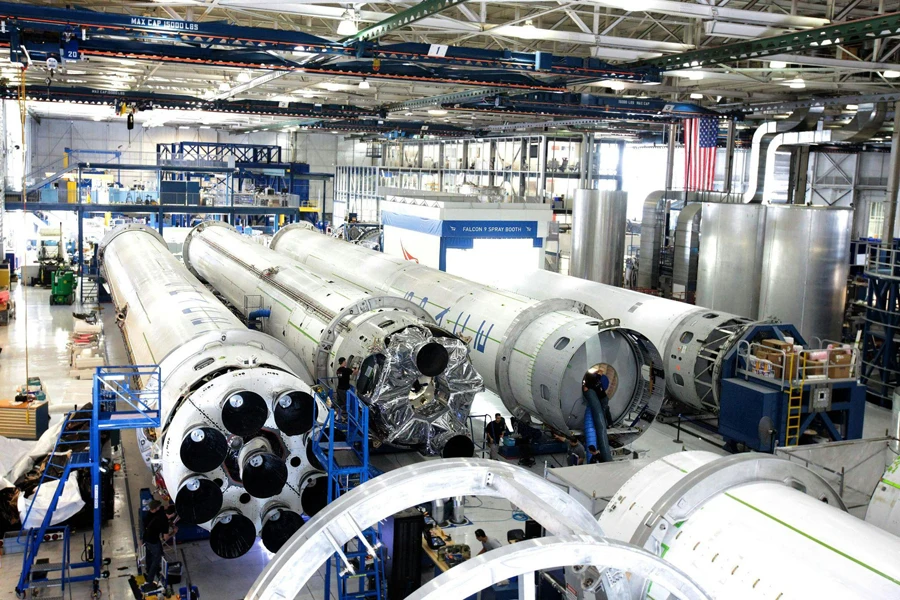
Safety certifications
For functional safety, PLCs should meet IEC 61508; for machinery safety, source PLCs that meet ISO 13849. These certifications guarantee the safe operation of the PLC, lowering the potential for accidents.
Environmentally rated PLCs may be necessary in various situations. PLCs that fulfill ATEX or IECEx requirements are necessary, for instance, in areas with a high risk of explosion.
If you’re doing business worldwide or selling your items abroad, make sure the systems satisfy the requirements of all applicable markets. For instance, products aimed at the European Union market may require CE labeling, while those destined for the North American market may necessitate UL certification.
When assessing PLCs, it is essential to communicate with suppliers regarding their adherence to applicable certifications and requirements. Respected producers will have certifications demonstrating adherence to specific guidelines.
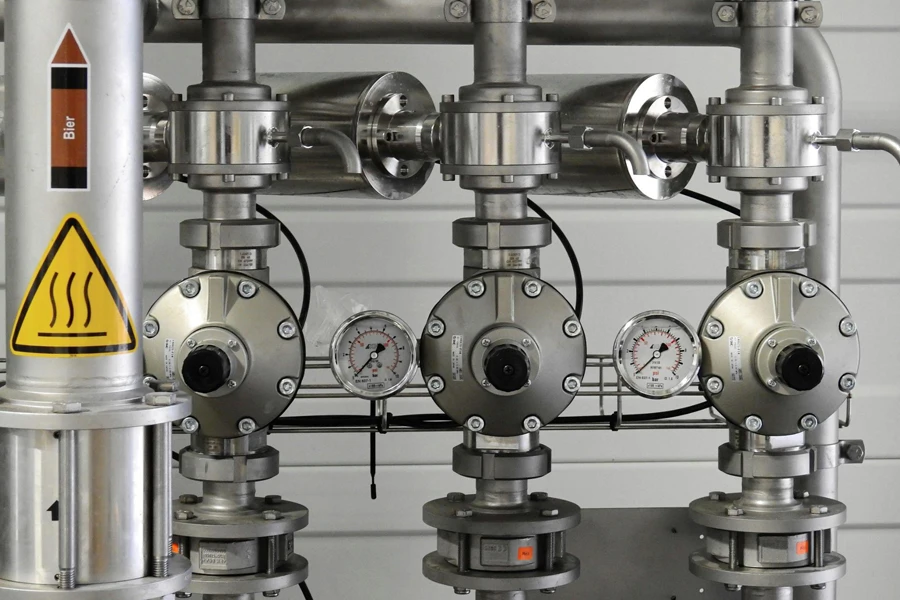
Summary
Maximizing industrial operations requires the correct programmable logic control (PLC) system. Begin by pinpointing your clients’ specific applications in terms of technical specs and scalability.
In general, compact PLCs are suited to small-scale projects with few I/O points. On larger, more complicated processes, modular and rack-mounted PLCs offer improved flexibility and scalability.
Finally, consider your budget and ensure the system satisfies all industry requirements and safety certifications, never underestimating the importance of selecting a reliable manufacturer or vendor.
Browse a huge range of PLCs from trusted suppliers on Alibaba.com.