How much does it cost to manufacture the products you sell? You know your sales numbers, but sales don’t tell the whole story. Before you can figure out your actual profit, you need to calculate what it costs to produce those goods in the first place.
For this reason, many businesses use the cost of goods manufactured (COGM) formula. Gross profit will look good on paper, but you’ll only know how much your company made in profit by factoring in what it spent on raw materials, labor, and overheads to produce finished goods.
Want to assess your business’s financial health better? Keep reading for a detailed look at COGM and how to use it to improve profitability and optimize manufacturing.
Table of Contents
What is cost of goods manufactured (COGM)?
How to calculate COGM (step-by-step)
Step 1: Calculate direct materials used
Step 2: Add direct labor costs
Step 3: Add manufacturing overhead
Step 4: Adjust for work-in-progress (WIP) inventory
Real-world example of COGM
COGM vs. COGS: What’s the difference?
Relation to costs incurred
Inputs
Relation to sales revenue
Simple example
Rounding up
What is cost of goods manufactured (COGM)?
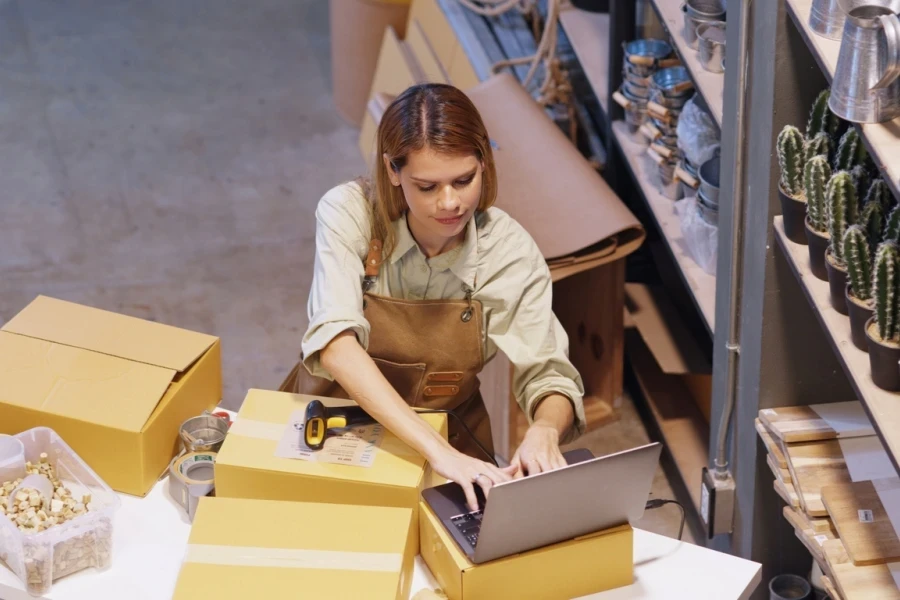
COGM is the total cost of turning raw materials into finished products within a specific period. It includes:
- Direct materials used (the cost of raw materials that go into the final product).
- Direct labor (wages paid to workers making the product).
- Manufacturing overhead (factory rent, utilities, machine maintenance, and indirect labor).
- Beginning and ending work-in-progress (WIP) inventory adjustments (the cost of unfinished products at the start and end of the period).
In essence, COGM tells you the true cost of production. If you don’t track it, you’re blind to how much you’re spending to make your products and how much profit your business makes..
How to calculate COGM (step-by-step)
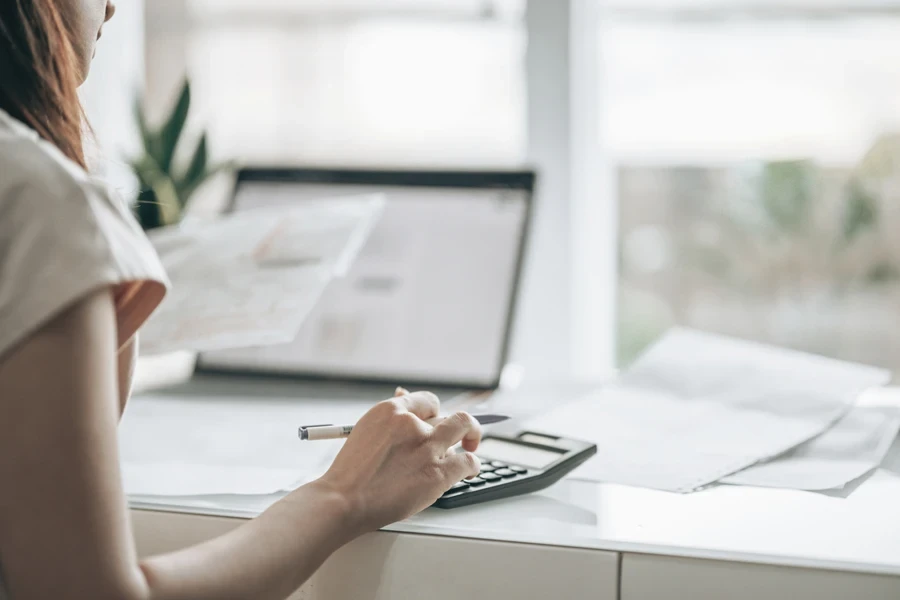
Getting your cost of goods manufactured requires adding all the elements discussed above into a simple formula. So, here’s what it will look like when calculating COGM:
COGM = (Direct Materials Used + Direct Labor + Manufacturing Overhead + Beginning WIP Inventory) − Ending WIP Inventory
However, remember that COGM only accounts for expenses directly related to the manufacturing process. It won’t include indirect costs like bulk raw material purchases used for multiple products. Your COGM calculations will also exclude HR, marketing, and administration (and other business expenses like them)
Now, let’s go through each step without the confusing accounting jargon.
Step 1: Calculate direct materials used
First, figure out how much raw material you used during production with the formula below:
Direct Materials Used = (Beginning Raw Materials Inventory + Raw Materials Purchased) − Ending Raw Materials Inventory
A great way to visualize this is a flour bakery measuring how much it used in a month—not what it bought, but what went into the bread.
Step 2: Add direct labor costs
This is the total wages paid to workers directly involved in manufacturing. The keyword here is “involved in the manufacturing,” meaning no office staff or marketing team should enter the final figure—just the people making the product.
Step 3: Add manufacturing overhead
These are the other costs that keep your factory running. It’s everything needed to make products, even if it’s not part of the product itself. These often include:
- Factory rent/mortgage
- Utilities (electricity, water, gas)
- Equipment depreciation
- Indirect labor (like supervisors or quality control staff)
Step 4: Adjust for work-in-progress (WIP) inventory
Finally, adjust for unfinished products still in production at the start and end of the period.
COGM = (Total Manufacturing Costs + Beginning WIP Inventory) − Ending WIP Inventory
You need this step because those unfinished products haven’t been sold yet. It’ll stop you from counting materials and labor twice.
Note: total manufacturing costs includes direct materials, direct labor, and manufacturing overhead costs.
Real-world example of COGM
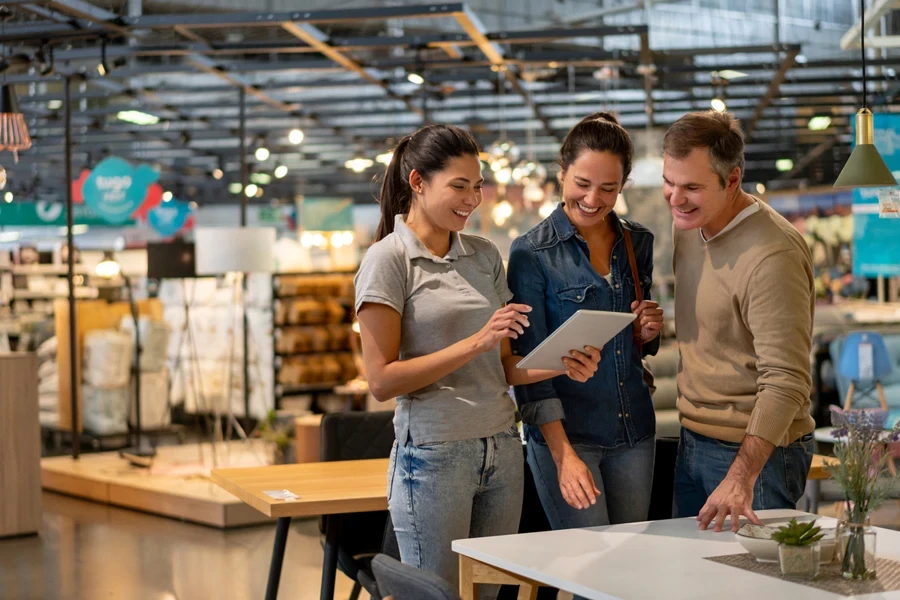
Let’s say you run a furniture manufacturing business and your costs for the quarter looks like this:
- Raw materials purchased: $80,000
- Direct labor costs: $60,000
- Manufacturing overhead: $50,000
- Beginning work-in-progress inventory: $40,000
- Ending work-in-progress inventory: $45,000
Now, plug them into the formula:
COGM = ($80,000 + $60,000 + $50,000 + $40,000) – $45,000
COGM = $185,000
So, you spent $185,000 this quarter to produce finished furniture. That’s your true production cost before considering sales or profits.
COGM vs. COGS: What’s the difference?
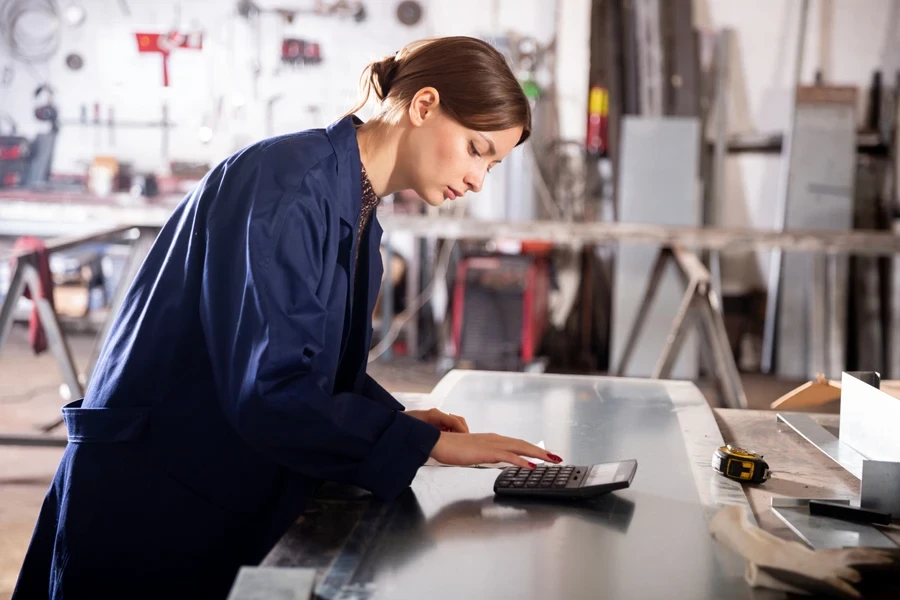
COGM and Cost of Goods Sold (COGS) are both key financial figures for production and sales. But that’s where their similarities end as they represent different stages in production and sales. While you could say they are connect, their purposes vary on a company’s financial statements. Here’s a quick look at their differences:
Relation to costs incurred
- How they’re similar: COGS and COGM give a good picture of a products total manufacturing costs.
- How they differ: While COGM represents the total cost a company spends to make finished goods within a period, COGS reflects the costs of only the ones the business sold during that time.
Inputs
- How they’re similar: Both formalas uses direct cost of labor.
- How they differ: COGM accounts for direct materials, manufacturing overhead, direct labor, and adjustments for work-in-process inventory at the start and end of the period. While COGS includes all these costs, it also factors in finished goods inventory (i.e. adding the beginning inventory and subtracting the ending inventory).
Relation to sales revenue
- How they’re similar: COGM and COGS help calculate costs for finished products ready for purchase.
- How they’re different: COGM represents the total cost of finished goods that are ready for sale, while COGS only covers the cost of goods that customers have already purchased.
Simple example
Using the example of a furniture business, if they made 1,000 chairs this quarter but only sold 700, COGM includes all 1,000 chairs. In contrast, COGS only counts the 700 that left the warehouse. That’s why COGM is a production cost metric, while COGS is a sales cost metric.
Rounding up
If you’re not tracking COGM, you may be making business decisions blind. COGM is so important because the formula helps businesses sets the right prices (If you don’t know how much a product costs to make, how can you price it correctly?), identifies cost problems (A rising COGM shows you may be overpaying for materials or running inefficient production), helps with budgeting (you need to know what you’re spending before expanding operations), and boosts profitability (cutting unnecessary manufacturing costs means bigger profit margins). In short, understanding COGM means understanding your business.