MIG welding, also known as Metal Inert Gas (MIG) welding, has been part of the American industrial scene since the 1940s. Over the years, innovative technological advancements have led to the development of a wide range of MIG welding products.
Navigating the market can be overwhelming due to the various options available, including CO2 welding and flux core welding. This guide discusses the pros and cons of different MIG welding products, so buyers can make an informed decision.
Table of Contents
MIG welding machinery: Market share and demand
5 factors to consider when buying MIG welding machines
Different types of MIG welders
Conclusion
MIG welding machinery: Market share and demand
The global welding market is expected to grow at a compound annual growth rate (CAGR) of over 4.6% by 2028. The global welding market surpassed US $20 billion in 2020, favoring the CAGR projection. However, while worldwide demand for quality welding machinery increases, certain industries are facing welder shortages.
According to the American Welding Society (AWS), the country anticipates a deficit of 375,000 skilled welders by 2023. The shortage does, however, increase the need for high-quality and technologically advanced welding machinery, such as MIG welding machines.
5 factors to consider when buying MIG welding machines
The type of material to be welded is the starting point when choosing a MIG welding machine. There are currently several types of MIG welding machines on the market, each designed for specific welding applications and materials. The material determines the power needed, portability, and machine capacity.
Below we discuss the most pertinent factors to consider when choosing a MIG welding machine.
1. Materials to weld
The thickness of the metal to be welded determines the type of MIG welding machine to be used. Welders are categorized by the current they produce during a given duty cycle. A duty cycle refers to the length of time a welding machine can operate a specific amperage without overheating within a 10 minute period. MIG welding machines with a high duty cycle are ideal for processing thick metals, while low duty cycles are appropriate for thinner metals.
2. Welding speed
Welding speed determines the quality of the weld and efficiency of the welding process. While welding at a faster speed reduces the overall welding time, it can result in a poor-quality weld due to incomplete fusion and excessive spatter.
110 Volt MIG welders are a good choice for amateur welders or DIY home projects. These MIG welders have a low duty cycle and are rated to a maximum of 80–100 amps. As a result, they’re only appropriate for welding thin metals for a short period of time.
220 Volt MIG welders, on the other hand, are ideal for professionals and bigger projects. 220V machines have outputs from 20–220 amps. They can weld up to ½ an inch plate and can be turned down to weld thin metals too.
The maximum welding speed can impact the productivity and efficiency of the welding process. Higher welding speeds are generally more appropriate where productivity is a priority. However, where appearance and strength are a priority, a lower maximum welding speed would be more appropriate.
3. Power supply
There are two main categories of MIG power supply, namely inverters and transformers. Transformers dominated the market for nearly 100 years, while inverters are considered to be a modern solution.
Inverters promote better welds, while transformers are generally more durable. Inverters surpass transformers in one key area — they reduce weld spatter. Inverters automatically adjust variables that welders cannot always immediately respond to. The automatic adjustments reduce the chances of weld spatter occurring.
Transformers, however, retain one advantage over inverters — longevity. Due to their simple design, they can withstand the challenges that come with daily use. Transformers have also been around for a lot longer than inverters, which have allowed manufacturers to analyze their lifespan and promote their durability.
The power supply required would depend on the material and product being welded. However, as a rule of thumb, the MIG welder’s wire feed should be set to a speed to the range of 240 to 290 inches per minute (ipm). The travel speed should be set to 14 and 19 ipm, depending on the thickness of the material and the type and size of the wire being used.
4. Types of controls
There are three types of MIG welding controls: manual, semi-automatic, and fully automatic. Manual controls offer the least precise welding outcome, but are simple to use and are inexpensive. This type of control is best suited for experienced welders as they are more knowledgeable about welding parameters, voltage, and welding materials.
Semi-automatic controls are known for their simplicity and precision as they provide consistent wire feed speeds. Welders can set the welding parameters manually too.
Fully automatic controls provide the most precise and consistent welds out of the three controls. They require more setup and programming and are more expensive. Fully automatic controls are most commonly used in industrial settings where high productivity and quality are crucial.
5. Strength of the weld
The strength of the weld influences the performance and safety of the finished product. There are multiple factors that influence the strength of the weld and the MIG welder chosen. The most important are the type of wire being used and the wire feed speed.
Lower wire feed speeds result in narrower weld beads and slower welding speeds, which produces higher weld strength and visually appealing welds. Conversely, higher wire feed speeds result in wider weld beads and faster welding speeds which can lead to potentially lower weld strength and less visually appealing welds.
Different types of MIG welders
MIG welders are a common form of stick welding that produces high-quality welds with minimal effort. It uses electrical impulses from a power source to fuse metal pieces together and a solid wire electrode that metals and forms the weld joint.
Over the years, the principles of MIG welding have remained largely unchanged, but new power source options have been introduced to the market that allow for more efficient welding.
The advancement in power sources has introduced new types of MIG welders that each offer unique features, advantages, and disadvantages.
Flux cored arc welders (FCAW)
FCAW machines are most commonly used in the construction, shipbuilding, and automotive industries, and where strong, durable welds are required. They can weld a variety of metals, including steel, stainless steel, and aluminum.
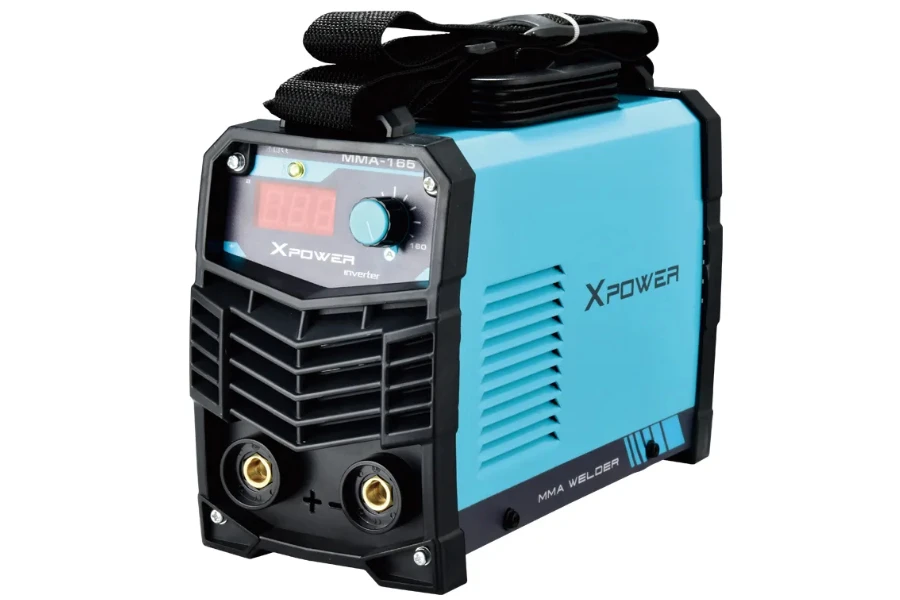
FCAW welders generally consist of a power supply, welding gun, and wire feed system. The power supply provides the electrical energy needed to create the arc, while the welding gun guides the wire electrode and delivers the shielded gas to the weld area. The wire feed system controls the speed at which the wire electrode is fed into the weld area, allowing the welder to adjust the rate of deposition to suit the unique needs of the welding job.
Advantages:
- High welding speed
- Good welding penetration
- Ability to weld in all positions
- Easy to use
- Suitable for filler metals
Disadvantages:
- Produces more smoke and fumes
- May require frequent cleaning
- Not suitable for welding thin materials
- Uses shielded gas which can be expensive
Gas metal arc welders (GMAW)
GMAW machines, like FCAW welders, are used to weld a variety of metals including steel, stainless steel, and aluminum. They are most commonly used in the construction, manufacturing, and automotive industries due the durability and strength of their welds.
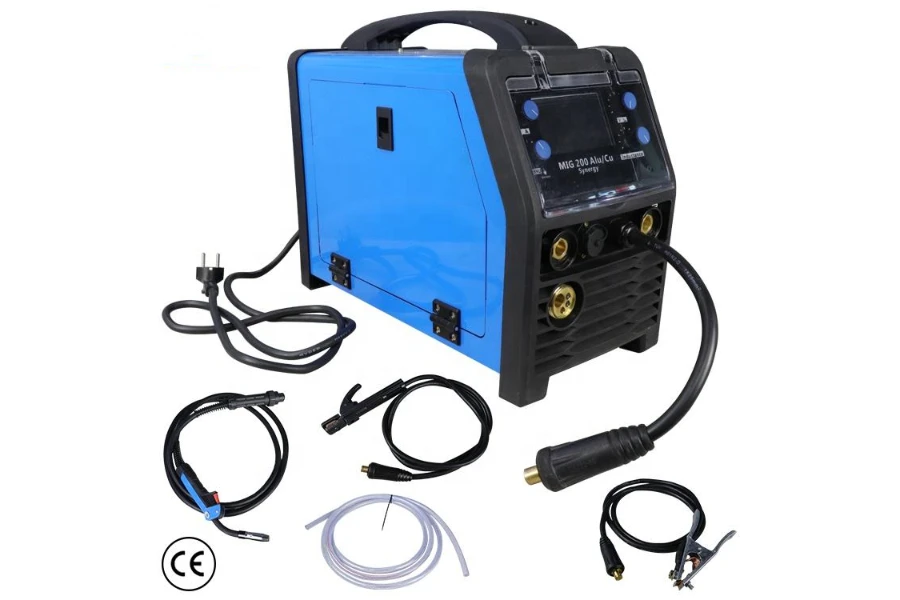
This electric welder uses a continuously fed wire electrode and an inert or semi-inert gas to produce a weld. The wire electrode is made of metal alloy and is fed through a welding gun, which also delivers a shield gas to the weld area. It functions similarly to FCAW machines.
Advantages:
- High welding speeds
- Good weld quality
- Ability to produce weld with minimal spatter
- Ease of use
- Appropropriate for use with filler metals
Disadvantages:
- Inappropriate for outdoor welding
- Not suitable for welding thin materials
- Uses shield gas which can be expensive
Pulse MIG welders
Pulse MIG welding machines produce welds using a modified version of the GMAW process. Like GMAW welders, pulse MIG welders use a continuously fed wire electrode and an inert or semi-inert gas to produce welds. However, they differ in the way that they deliver the electrical current to the weld area.
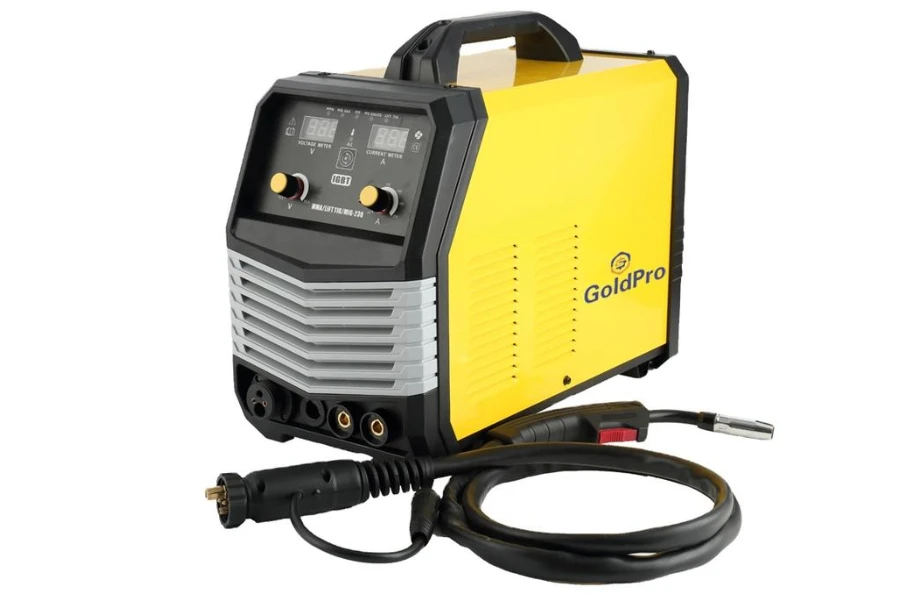
Pulse MIG welding machines allow the welder to control the amount of heat being applied to the weld area and reduces the risk of overheating the metal. The machine also allows for more accurate and consistent welds as the welder has better control over the amount of filler metal being deposited.
Advantages:
- Allows for durable welds
- High welding speeds
- Good welding quality
- Produces welds with minimal spatter
- Can be used with a variety of filler metals
Disadvantages:
- Inappropriate for outdoor welding
- Not suitable for welding thin materials
- Uses shield gas which can be expensive
Conclusion
The welding market is consistently growing, creating an even greater demand for quality welding products, such as MIG welding machinery. This article discussed the key factors to consider when selecting an MIG welding machine.
It further compared three types of MIG welding machines and considered their advantages and disadvantages to allow buyers to make an informed purchasing decision. Visit the Alibaba.com showroom to find the best MIG welding machinery on the market.