Tower cranes are used throughout the world and are, by far, the most used type of crane for constructing tall buildings. If you are considering sourcing tower cranes, this article offers some guidance on the different types of tower cranes available, and looks at some of the top choices in the market.
Table of Contents
The projected growth of the tower crane market
An introduction to tower cranes
Types of tower cranes
Tower crane assembly, cranes that climb
How to select the right tower crane
Final thoughts
The projected growth of the tower crane market
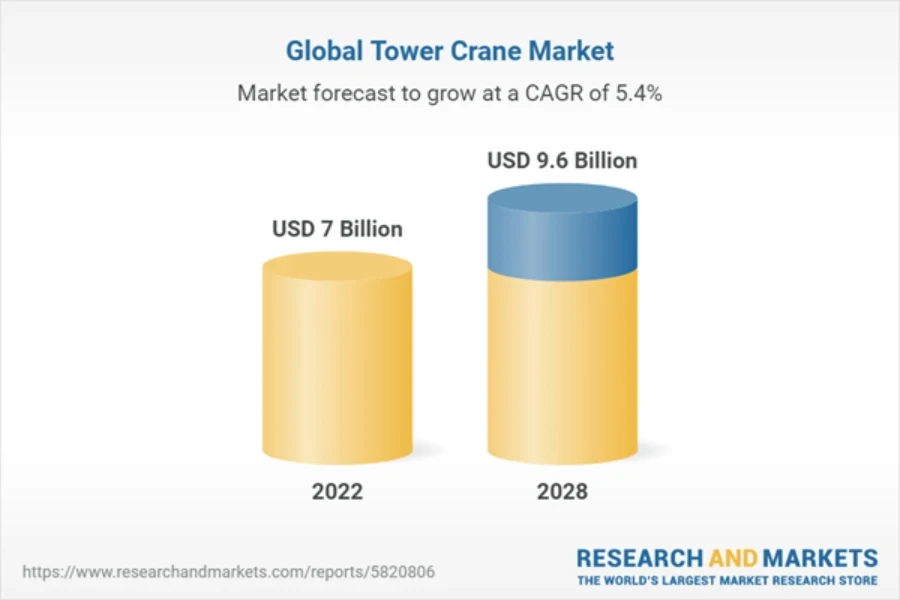
The global tower crane market is projected to show a compound annual growth rate (CAGR) of 5.1% through the period from 2022 to 2028, growing from a value of US$ 7.0 billion in 2022 to US$ 9.6 Billion by 2028. Much of this growth is fueled by a bounce-back in the construction industry, after the pandemic slowdown. Tower cranes are especially sought after for major high-rise residential and office buildings projects as they can work at greater heights than most crawler cranes.
An introduction to tower cranes
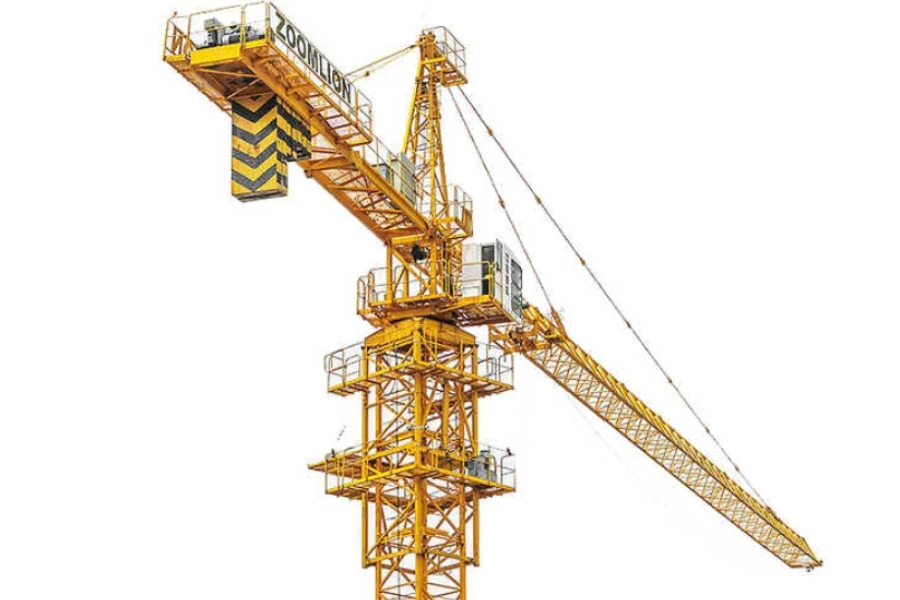
Tower cranes are balance cranes that are fixed to the ground, and also may be attached to the inside or outside of the structure being built. As tower cranes are fixed firmly, they take time to assemble and disassemble, time which is needed to ensure that the crane is safe, stable and properly balanced for the heights and weights that are to be hauled. Once assembled, their purpose is to lift for that specific construction project only, and they are not intended to be easily mobile.
Therefore they differ from tracked crawler cranes and mobile truck cranes, that are designed to move easily from location to location, but in doing so, have more limited lifting capacity.
The main mast section of the tower crane is made of multiple sections of lattice frame, bolted together upon a concrete base. The main load jib and counter jib are also made of a lattice frame. Lattice frames provide great strength at a relatively low weight, with the strength and weight spread across the lattice framework.
The slewing unit, which is a rotating turntable, allows the crane to move its jib and load through 360 degrees, with either the load or the jib adjusting to compensate for balance, depending on crane type. The main jib that carries the load is balanced with a shorter counter jib, which holds the counter weights.
The operator’s cab sits on the slewing unit so that it can rotate as the crane rotates, and the operator can have full view of the block and hook. On a fixed jib, balance and load movement is achieved by ‘racking’ the hook, sliding it in or out along the length of the main jib with a trolley mechanism.
Depending on the type of crane, there may be a short mast above the slewing platform, called a cathead, with steel cable jib ties that run from the counter jib over the cathead to the main load jib.
For self-climbing cranes, a climbing frame is assembled around the mast, under the slewing platform.
Types of tower crane
There are three main types of tower crane, A-frame, flat-top, and luffing cranes. A-frame and flat-top cranes are also sometimes called hammerhead cranes due to their short counter jib and long main jib resembling a hammer shape.
A-frame cranes
A-frame cranes have a fixed jib and counter jib. A-frame cranes are so named for their strong ‘A-frame’ assembly above the mast, with a cathead frame that extends up from the mast, and strong supporting tie rods that run from the cathead to the front and rear jibs.
The stability that the A-frame provides allows these cranes to lift very large weights upwards of 200 tons, and these are the crane of choice for a static location with heavy lifting needs.
The disadvantage of the added A-frame assembly is that the cathead and jib tie rod supports do add to the overall height requirement for the crane. In some working environments with limited clearance this may not be workable, so a crane with a flat-top and no A-frame may be preferred.
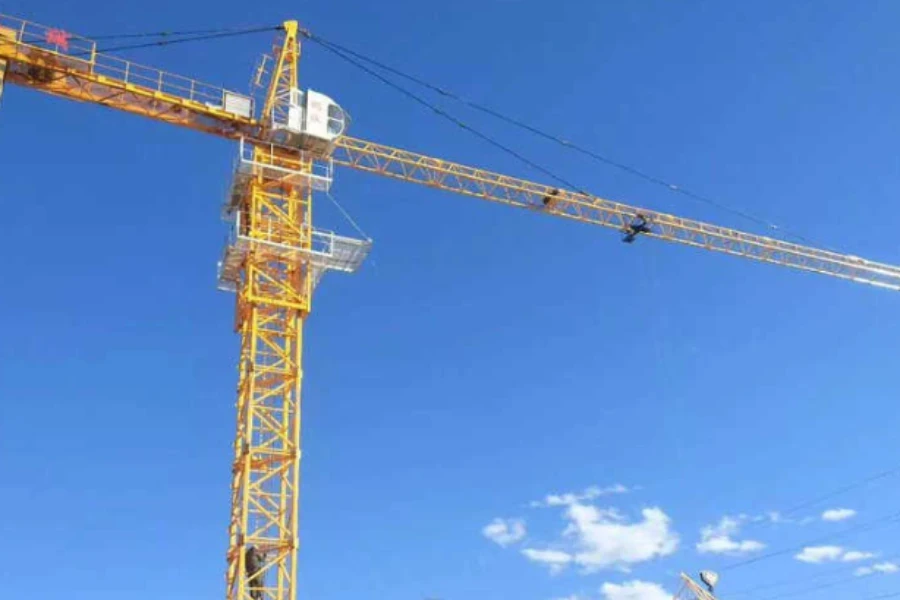
This 8 ton A-frame tower crane, model QTZ125 TC6015-8 is available for around US$ 19,000.
This Zoomlion A-frame tower crane, model D5200-240 has a 240 ton capacity and sells for US$ 820,000.
Flat-top cranes
Flat-top, or low-top, cranes are also fixed jib cranes and use the same racking mechanism as A-frame cranes to move the block and hook. They do not have the added A-frame assembly, or have a very short cathead, so the top of the crane takes up less height, allowing for operations where there is less clearance available above the jib. These are preferred when multiple cranes are operating above and below each other or when there is restricted clearance above the crane.
The advantage of a flat-top crane over an A-frame crane is its reduced clearance requirements. This used to come with the disadvantage of a lesser lifting capacity than A-frame cranes, and this remains true for very high weight loads, but flat-top cranes are now comfortable with lifting loads up to 50 tons.
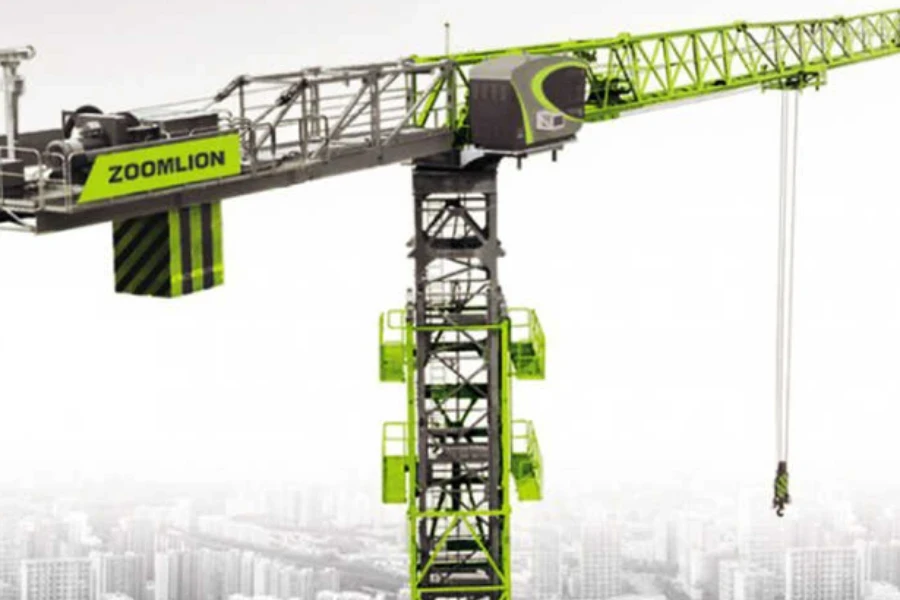
This Zoomlion flat top crane, model TC5013A-5, has a 5 ton capacity and is available for US$ 65,000.
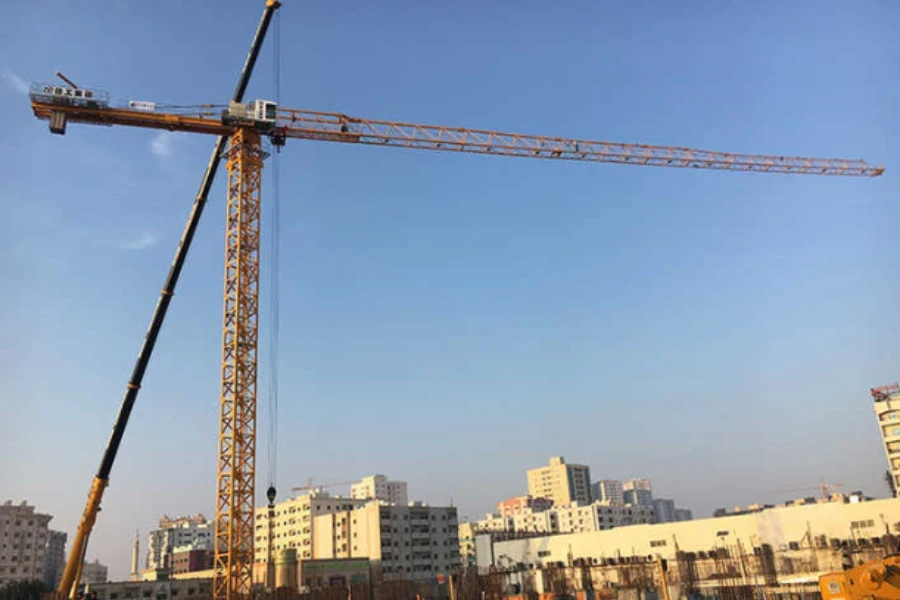
This XCMG flat-top crane, model XGTT100CII, has an 8 ton lifting capacity and sells for around US$ 500,000.
Luffing cranes
Luffing cranes have a main jib that can be raised and lowered (luffed). The raised jib is rotated on the slewing platform. These cranes can lift heavier loads than fixed jib cranes and can work in narrower spaces as the jib doesn’t extend as far out when raised. They don’t have a racking mechanism to move the block and hook in and and out, and instead use the raising and lowering of the jib to adjust balance and distance from the mast.
One of the big advantages of a luffing jib is that it does not extend out far from the mask, and therefore does not require as much space in which to operate. By contrast, a fixed jib may extend out beyond the construction site and add risk to those areas, requiring additional operating permissions and insurance. Also the luffing jib has less risk associated with high wind environments, whereas the extended fixed jib increased the impact of high winds.
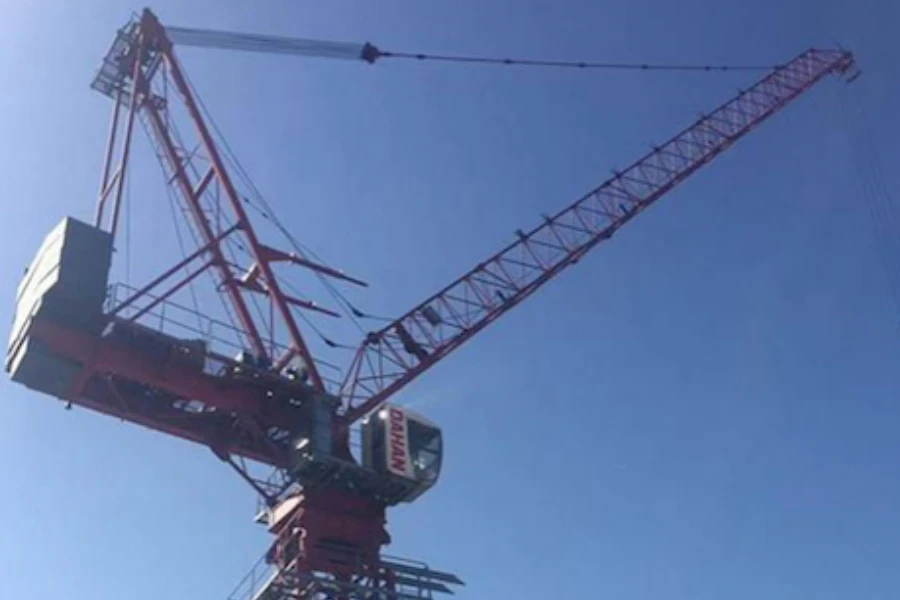
This Dahan luffing crane is a relatively smaller crane, with a 6 ton lifting capacity, selling for US$ 60,000.
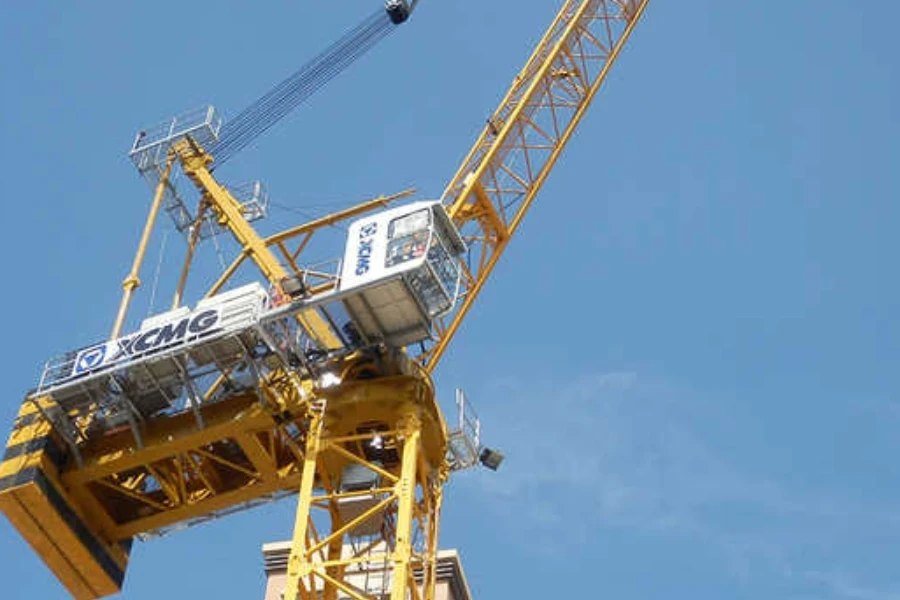
This XCMG luffing crane, model XL6025-20, has a lift of 20 tons and is available for US$ 50,000.
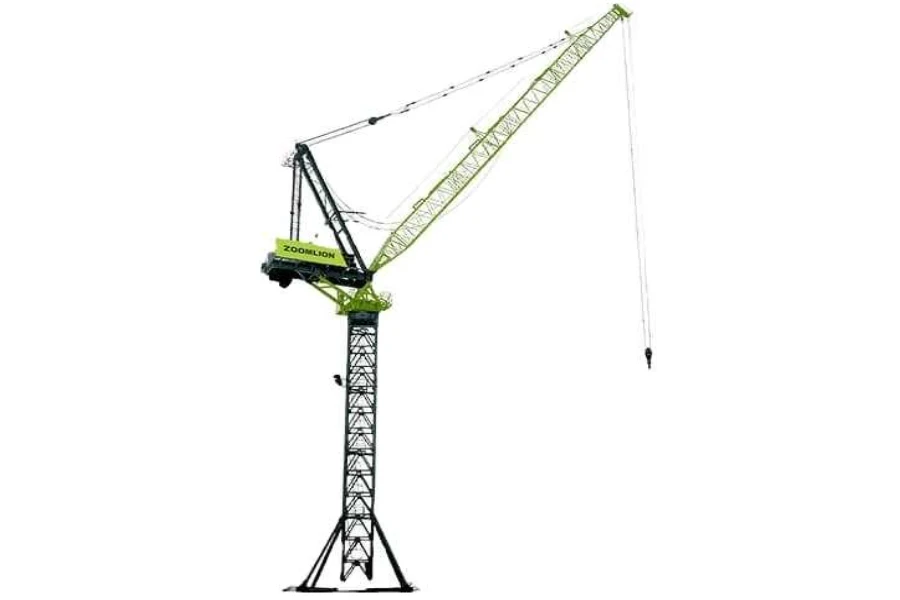
This heavy duty Zoomlion luffing crane, model LH3350-120, has an 180 ton lift and is available for around US$ 3,200,000.
Tower crane assembly, cranes that climb
The process of assembling a tower crane begins with establishing a secure base, then using a mobile crane to lift lower sections of the mast up to their working height, and then adding the rotating platform, cab and jibs.
First the large concrete slab base is built, using reinforced concrete, which is required to harden for about a month. Once that base is fully set, the first steel truss section of the mast is lifted into place by mobile crane, and secured with anchor bolts that are embedded into the concrete foundation. This makes the first stable platform for the rest of the crane to come.
Next, further mast sections are added on top of the base truss, and the sections secured together with steel bolts. When sufficient mast sections have been added, a slewing (rotating) unit is added on top of the mast, then the operating cab and the lifting components.
On top of the slewing unit, the cathead is added for an A-frame crane, then the counter jib and main jib, with tie rods to support the jibs. Concrete counterweights are then added to the counter jib. This makes up the working assembly of the tower crane.
Tower cranes that climb
Fixed tower cranes have the ability to lift themselves higher, section by section, in a unique and intriguing fashion. When the crane is required to operate at heights beyond the reach of the cranes that are required to assemble them, then they must extend their own height. This is quite a simple process in theory, but in practice can be one of the most dangerous tasks that a tower crane can perform.
The approach differs depending on whether the crane is climbing within a building, where the building grows around the crane, or the crane is free standing outside the building that is being constructed.
Climbing externally to a building or as a free-standing tower
Free-standing tower cranes use a self-climbing hydraulic mechanism, to build themselves higher from the initially constructed height. When the crane is ready to climb, a steel climbing frame is assembled around the base of the mast, with three closed sides and one open side. The frame is lifted up to the underside of the slewing platform and attached with steel bolts, and a hydraulic push mechanism is fitted to the new frame.
A new mast section is raised up by the crane hook, and is moved to the open section of the climbing frame by the jib and racking mechanism. The crane then needs to add load to the main hook to provide additional balance for the next task. The climbing frame is not designed to handle torsion of the main mast so the jib and mast must be carefully balanced with no slewing at all during the climbing process.
Once the crane is perfectly balanced, the climbing frame is unbolted from the slewing unit, and the hydraulics raise the climbing frame up sufficiently to allow a new mast section to be inserted. The new section is maneuvered into place, the hydraulics depressurised, and the new mast section firmly bolted into place. The cycle repeats for new sections of the mast until the desired height is reached, after which the climbing frame is either removed or left in place for later mast dismantling.
When the tower crane is alongside a stable building, mast sections can be anchored to the building to provide more stability as the crane climbs.
Climbing within a building as the building grows
Tower cranes that climb within a building make use of the existing support of that building for stability, and as a platform for climbing. In this way they can grow higher without the need for additional mast sections for the full height from the ground.
When a tower crane climbs within a building, the completed floors of the building are used to support the frame as it climbs. As each new floor is completed, the crane can be raised up to the next level. The crane base is first built as usual, fixed to the main floor, but with a climbing section included within the base of the mast. Then two supporting collars are fitted, typically using a gap of around three floors, connecting the crane firmly to the building structure. Climbing rails extend down the length of the mast to provide stability as the crane is raised.
When a higher floor has been installed a new support collar is fitted at the higher floor, and the crane is ready to climb. The base of the crane is unbolted, hydraulics raise the crane up to the new collar, and the base is bolted to the middle collar. The bottom collar can now be removed and can be fitted at the next higher level, so the process can be repeated.
How to select the right tower crane
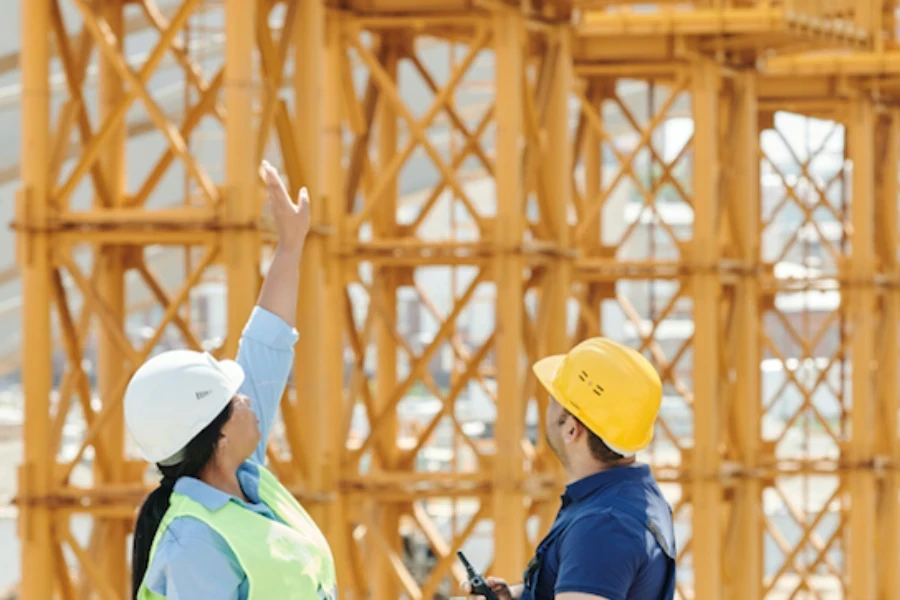
There are a number of key factors to consider in deciding which would be the right tower crane to choose, aside from the basic considerations of the required height and load that will be moved.
The available working radius of the job in hand is a key factor. Most cranes will have 360 degree rotation, but the construction site may not provide sufficient clearance to allow a wide turn. This will determine not only where a crane needs to be sited, but whether multiple cranes are required.
Working clearance above the crane will be a factor in determining whether A-frame or flat-top cranes are most suitable. The required clearance under the hook will determine how high the working crane needs to be, with a rough guide being approximately 10 meters clearance above the highest points of any surrounding buildings.
The siting and construction methods to be applied for the crane will determine whether the crane is free standing outside the building, anchored to the building, self-climbing externally, or internally within the building. Internal climbing cranes take up much less space on the construction site, and can climb as high as the building requires, but require more expensive dismantling on project completion.
A-frame and flat-top cranes are suitable for most projects where there is free rotation, and where there are no structural, safety or legal issues with a boom swinging across other areas and buildings. Luffing cranes are more suitable for restricted and crowded spaces, as they don’t need wide swing clearance.
Final thoughts
Tower cranes are perhaps one of the most familiar sights on high building construction sites for offices and condominiums. Their ability to lift very heavy weights to great heights makes them unique amongst cranes and the crane of choice for any high-rise projects. When properly assembled and balanced, they have amazing stability and this can be enhanced by anchoring the crane to surrounding structures.
As they are fixed, they do take time to assemble and disassemble, so are not the choice for more mobile projects, where crawler or truck cranes may be more suitable.
The potential buyer will have a clear idea of the type of crane that is most appropriate for the construction site, choosing between A-frame, flat-top or luffing, or may use different types for selected roles across the site.
For more information on the wide selection of tower cranes available in the market, check out the online showroom at Alibaba.com.