Stocking up top-notch blow molding machines is possible. However, the decision-making process could be brutal most times—considering the number of brands available.
This article will reveal seven things every seller should look out for before purchasing these machines. But before jumping on the seven buying guide tips, here’s some information about the blow molding machine market.
Table of Contents
The blow molding machine market is experiencing a huge growth
Blow molding machines: seven amazing tips to selecting the perfect option
Different types of molding machines
Who are the targeted consumers for blow molding machines?
Bottom line
The blow molding machine market is experiencing a huge growth
According to reports, the blow molding market was valued at US$ 4.8 billion in 2018, and it’s forecasted to hit US$ 6.6 billion in 2026. In other words, the market has been growing at a CAGR of 3 percent since 2018.
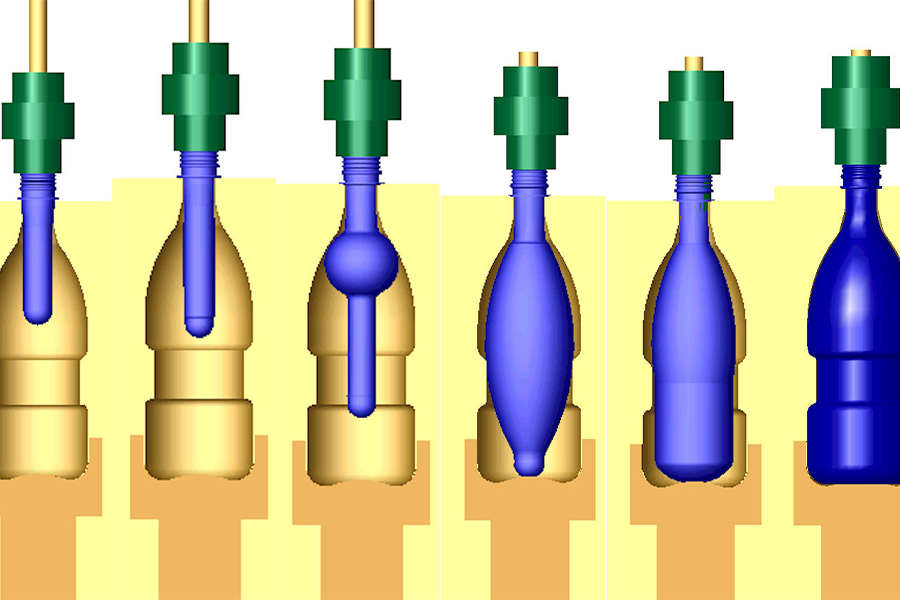
There are three major drivers of the blow molding market:
- Low waste creation
- Increased demand for molded plastic products
- Material flexibility
Moreover, the surge in technological developments is another key factor that impacts the industry’s growth. The above reports mean there’s a high potential of this market growing big and further in the next few years. Hence, now is the ideal time to jump into the market as a seller.
Blow molding machines: seven amazing tips to selecting the perfect option
Mold size
The mold size of a blow molding machine is dependent on the consumer’s requirements. For a user who produces certain plastics, it’s ideal to buy machines with specifications that match the end products.
Automation
The whole idea behind automation is to save consumers money and time. Hence, the right automation yields smooth end-products. But before buying a blow molding machine, sellers must check if it has a relay logic or PLC control.
The PLC control automation system handles input devices with custom programs.
In contrast, wired relay logic uses different electrical relays based on specific configurations.
Consumers can use either of these automations—based on their specific requirements.
Machine capacity
Before choosing a blow molding machine, businesses must identify their production capacity. That way, they can figure out the machine capacity to stock up. A general rule of thumb is to consider a machine with at least 25 percent more capacity. Such a machine can support business growth over time.
Auxiliary machinery
Auxiliary machinery is more like the accessories that accompany the machine. These accessories are like backup parts that users need if the primary equipment fails. A few examples of auxiliary machinery include cooling systems, air compressors, grinders, etc.
Before making a choice, it’s ideal to choose machines that come with this feature.
Quality
The quality of a blow molding machine solely depends on the manufacturer. It’s important to confirm if the supplier produces quality machines before making your buying decision.
Demo
The demo is another factor that can help you make better decisions on the machines to buy. An online review of “how it works” (probably on YouTube) is a good step to see the production and operation of the machine before buying it.
Budget
Price is a crucial factor to consider when looking for the perfect mold-blowing machine to buy.
Businesses that want to get premium-quality blow molding machines should be willing to spend at least US$ 10,000 up to US$ 89,999.
Different types of molding machines
Injection blow molding
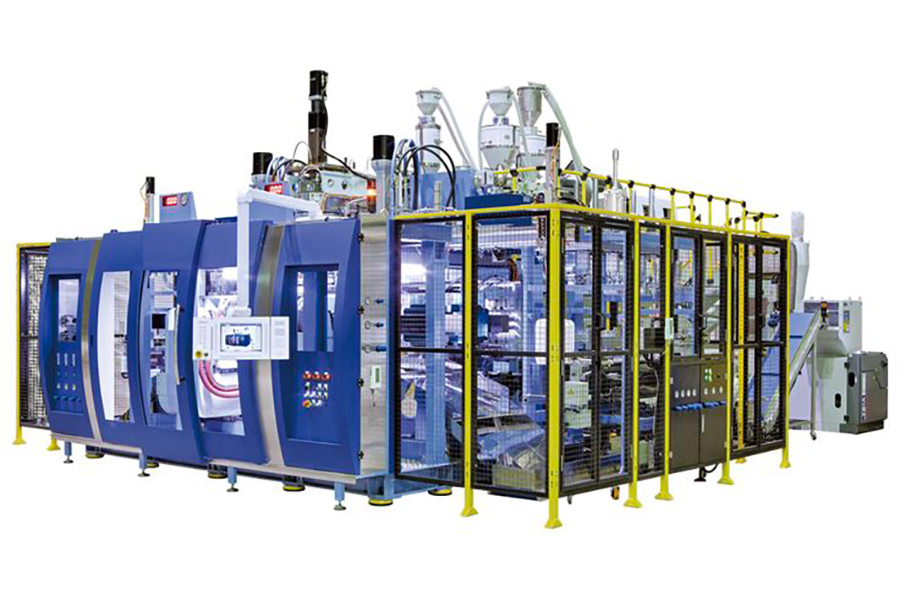
Injection blow molding machines use an extruder barrel and screw assembly to inject resin into the mold. Afterward, the injected plastic casts into a preform, and the machine blows air on it. In the last production stage, the plastic casts cool off and form the bottle–which moves the mold to a conveyor belt.
This machine is perfect for consumers with small to medium blowup ratios—producing PP (polypropylene), HDPE (high-density polyethylene), and LDPE (low-density polyethylene) bottles. Also, this machine produces bottles with tight neck tolerances.
Extrusion blow molding
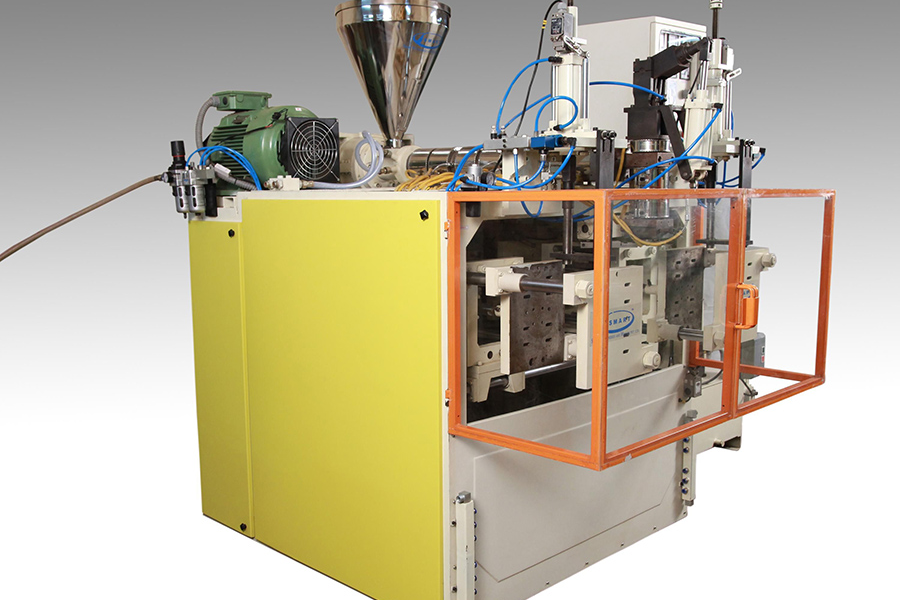
This machine extrudes heated resin to create a parison (a vertical shaped plastic that allows compressed air). The extrusion blow molding machine usually features a two-part mold that closes on both sides of the parison.
A blow pin goes into the bottle’s neck area when the mold seals and blows air. Then, the air pressure helps the parison take the mold’s shape while including details like threads in the neck. When the mold cools, the machine trims the parison’s bottom. Finally, the mold releases the bottle with a trimmed top.
This machine is perfect for consumers that produce large-sized PP, HDPE, and LDPE bottles with large necks. Also, this blow molding machine is ideal for adjusting bottle weight, multiple plastic layers, and window stripes.
Injection-stretch blow molding
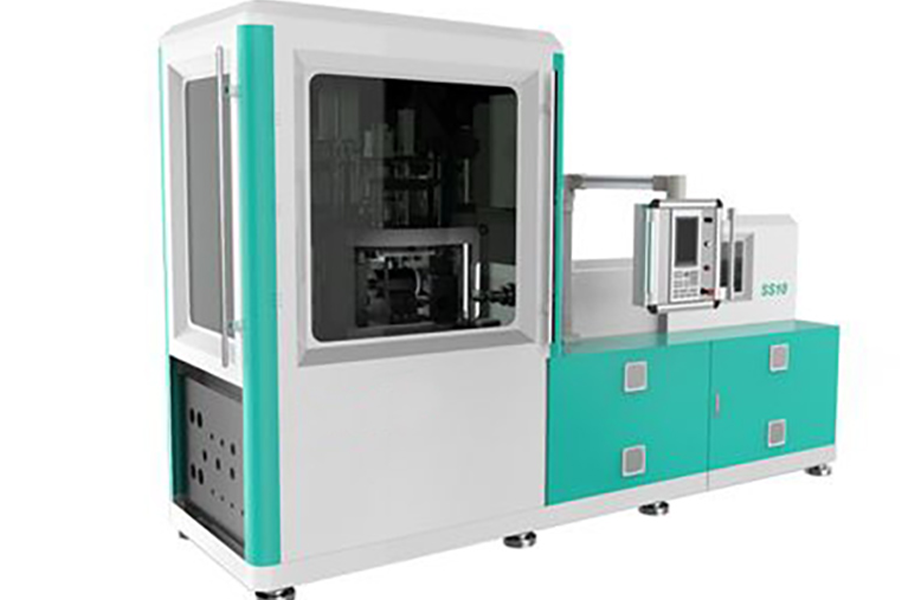
The injection-stretch blow molding machine is similar to the injection blow molding machine. This machine uses an extruder barrel and screw assembly to inject heated resin into the mold. Afterward, the injected plastic in the mold becomes a preform. As a result, the preform undergoes a stretching process as air moves into the mold. This process also boosts the barrier properties of the bottle in the mold. Afterward, the mold cools, and the bottle moves from the mold to the conveyor belt.
This machine is for consumers that produce PET (polyethylene terephthalate) bottles with small to medium blow-up ratios.
Who are the targeted consumers for blow molding machines?
According to the earlier reports, LAMEA (Latin America, Middle East, and Africa) regions are second to the biggest target market for blow molding machines—the Asia Pacific region. Thus, capitalizing on these regions as a seller opens up tremendous opportunities to boost business.
The US blow molding market is another highly lucrative market—thanks to the launch of new blow molding brands every year. Plus, there’s a huge consumption of bottled water in the US.
Bottom line
Considering the market’s huge growth, now is the right time to stock your inventory with blow molding machines. As earlier mentioned, it’s pretty hectic to make a perfect choice when selecting a blow molding machine.
But there’s a way out—by considering all the seven buying guide tips listed in this article.