In recent years, the powder coating business has been rising, with several entrepreneurs curious about it. This business is soaring because powder painting creates a sleek, durable, and beautiful finish on any metal.
This article gives insight to those who want to install their first successful coating line and the equipment needed in every step.
Table of Contents
What is powder coating?
The powder coating process and equipment involved
What to consider when buying a powder coating equipment
What is powder coating?
It is a finishing process that involves multiple steps in which dry, thermoset, or thermoplastic powder material is sprayed on a surface, melted, and cooled into an even coating.
The surface to be coated could be plastics, metals, medium-density fireboard, and glass. Powder coating is superior to traditional liquid coating because it can easily achieve decorative and functional purposes in various finishes, colors, and textures.
It takes three distinct steps—the first step involves the preparation and cleaning of the surface for coating, the second step includes coating the surface with fine powder, and the final step entails curing the painted surface in an oven where the powder melts and flows to form a uniform coating.
However, the steps may vary depending on the type of powder coating. Fluidized bed application and electrostatic spray deposition (ESD) differ in their curing stage.
The powder coating process and equipment involved
Powder coating takes three stages: preparation, application, and heat curing.
Preparation stage
Preparation is the first step in any powder coating process, where the material’s surface is cleaned and treated to rid it of dust, rust, debris, oil, solvent, dirt, and old paints. If the material is not adequately cleaned, remaining deposits and residues could interfere with the powder’s adhesive properties and the quality of the final product.
The preparation process varies from material to material; however, the typical stages include cleaning, etching, rinsing, blasting, and drying.
Preparation equipment
This stage involves three main pieces of equipment, as discussed below.
Blast room
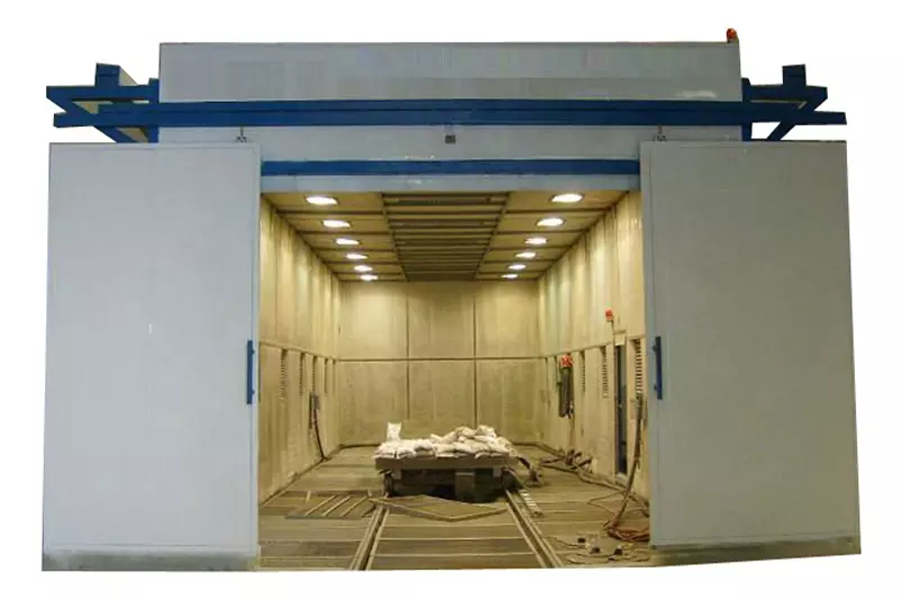
Since preparing surfaces sometimes involve high-pressured air to propel abrasive materials, this must be done in an enclosed blast room. Depending on the material, one may use different blasting media such as grit or steel shot to remove unwanted debris from the metal surface to be powder coated.
Blast rooms are vital for shops dealing with non-pristine raw materials, such as tubes with oxidated areas or welding residue. Blast rooms also ensure that dust, debris, or fine metal particles are contained to prevent workers and the surrounding community from breathing them.
Wash station
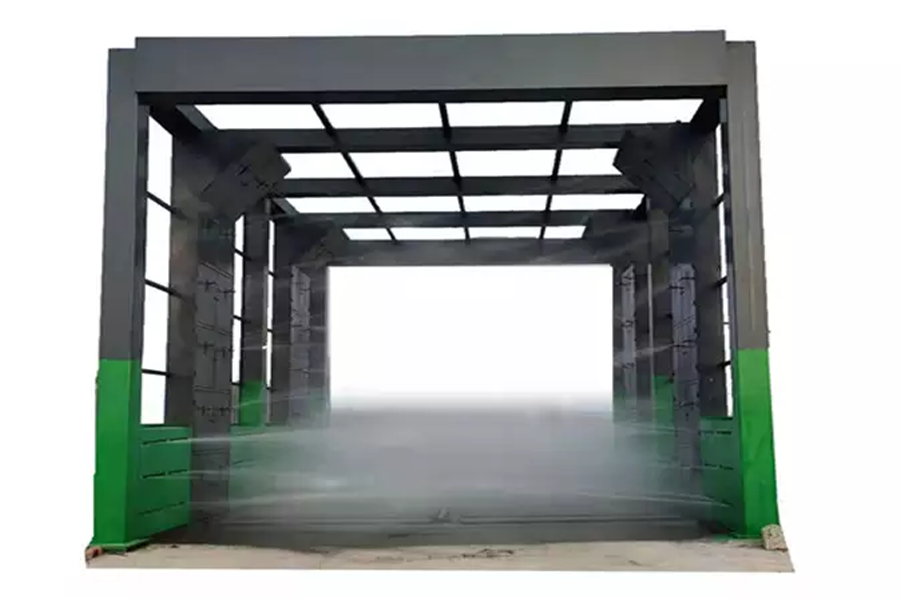
A wash station is required to remove oil, solvent, grease, or chemical residue from the material’s surface to be coated. At the wash station, the surface is sprayed using weak alkali, chemical pre-treatment agents, hot water, or neutral detergents.
A wash station can also help remove any lingering dust after surface blasting, thus increasing powder adhesion and finish quality. While some wash stations are built for manual chemical application, others are automated, where the conveyor belt passes the parts to the cleaning, rinsing, and prep stages.
Dry-off oven
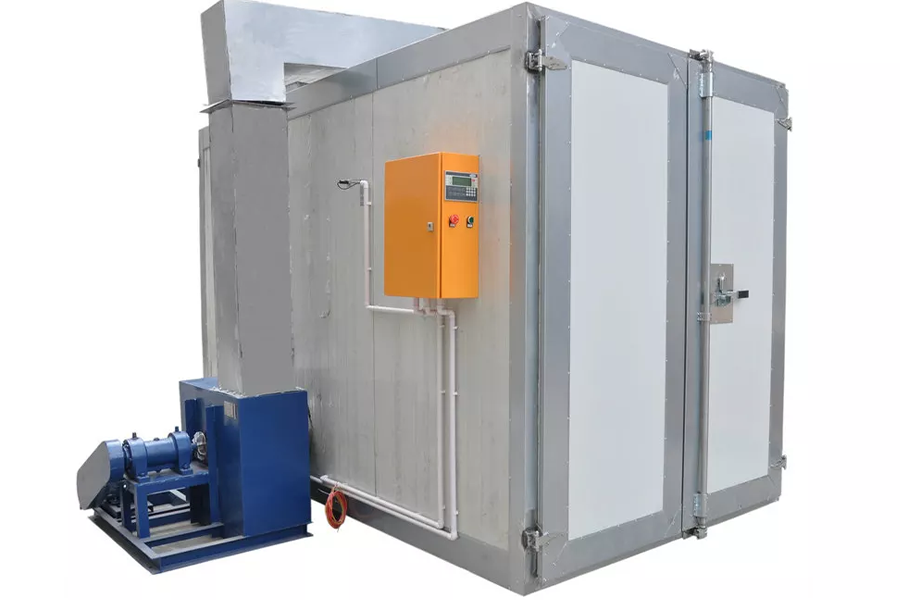
Although this equipment is used in the curing stage for electrostatic spray deposition (ESD) powder coating, it is also helpful in the fluidized bed preparation stage. The washed parts are passed into an oven to evaporate any lingering water or chemicals.
Additionally, the dry-off oven ensures the metal parts are at an ideal temperature before powder application.
Pre-treatment equipment can make a difference in the quality of the final product. One does not need to buy the most expensive cleaning equipment, but this stage is essential for the success of the powder coating process.
Application stage
Once the materials are clean, they move to the application stage. There are two powder application methods: fluidized bed application and electrostatic spray deposition (ESD).
For electrostatic spray deposition (ESD), the powder is applied using electrostatic spray deposition before it is taken for curation.
On the other hand, fluidized bed powder coating involves dipping preheated parts into powder materials in a fluidized bed. One can also use electrostatic fluidized bed powder coating, where powder particles are electrically charged to form a cloud over the fluidized bed. The preheated parts are then passed through it for coating.
Equipment for the application stage
Here is the possible equipment needed during the application stage.
Electrostatic powder spray gun
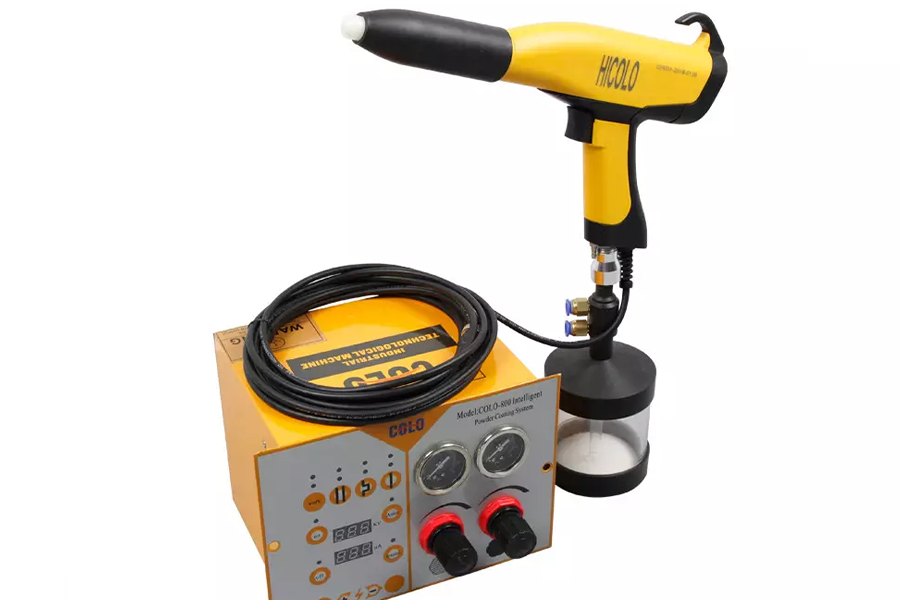
Powder coating is often done using a unique powder spray gun designed exclusively for this job. Compressed air is blown into the powder to move it through the gun and form a cloud. As the cloud-like powder leaves the gun, it is electrostatically charged.
The charged powder cloud covers and sticks to the material part. So, a powder coating gun is an essential piece of equipment for the process. Fortunately, the market has many types of professional-grade guns an entrepreneur can invest in.
Powder spray booth
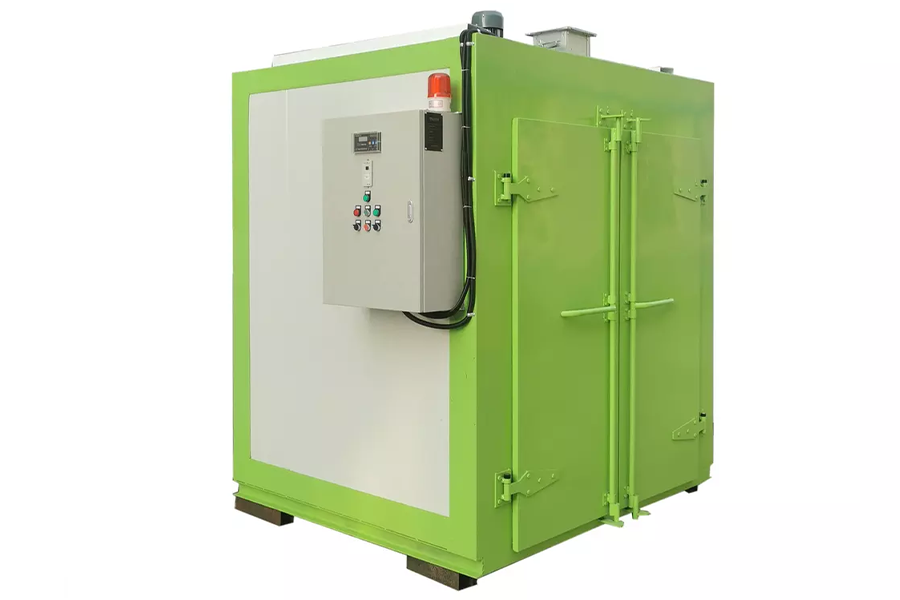
A powder spray gun needs a suitable place for usage and storage. When using spray powder, some fumes may end up in the air and on the floor. The powder spray booth helps to keep the overspray away from the workspace, thus minimizing pollution and health hazards.
The powder spray booth ensures that the rest of the workplace is clean and provides a well-lit area for painters to see what they are doing. They come with one or two exhaust fans fitted with filters to capture part of the overspray. Powder spray booths protect the powder-coated finish from airborne contaminants, especially if the shop’s environment includes blasting and welding.
Environmental room
An environmental room, also called a clean room, is needed for stringent finish requirements. Its purpose is to eliminate airborne pollutants and control humidity and temperature during powder application, thus preventing any clumping, contamination, or consistency issues. If the product has exact adhesion specifications or the shop environment is often dirty, clean rooms are required for better coating results.
Curing stage
The method and the type of powder coating material used determine what goes on at the curing stage.
If the operator chooses the ESD method, the ESD-coated materials should be cured in a powder curing oven. The time it takes to cure the material depends on its shape, size, and thickness.
The oven often operates at temperatures ranging from 325 to 450 degrees Fahrenheit, while the cure time ranges from 10 minutes to over an hour. When the ESD-coated materials reach optimal curing temperature in the oven, the melted powder particles will flow and cover them.
The process is slightly different from the fluidized bed method, where the parts are heated in the oven during preparation but before the application stage. The heated part is passed into the melted powder coating cloud for coating.
Equipment for the curing stage
Powder curing oven
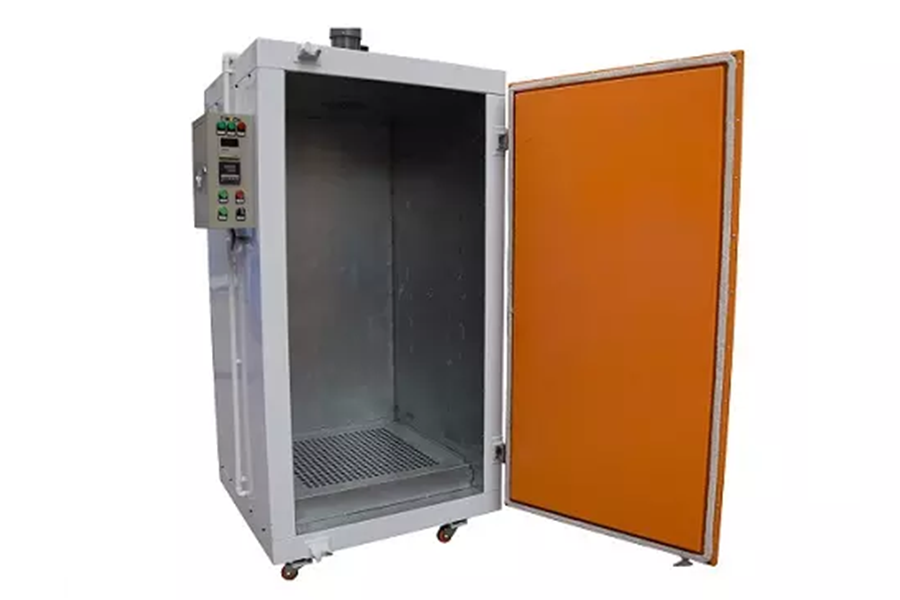
The oven is heated to an optimal temperature (325 to 450 degrees Fahrenheit), depending on the material. It helps to remove water from the material being coated. And it also heats the material and melts the powder, allowing them to stick together easily.
What to consider when buying a powder coating equipment
Choosing the best equipment for any endeavor is essential if one wants success for their business. The powder coating industry is projected to grow to $18.95 billion by 2028, exhibiting a CAGR of 6.2% from 2021 to 2028, which means having the right equipment promises success.
Consider these important factors when choosing the right powder coating equipment for a business.
Coating frequency
Buying the equipment will be economical if one intends to establish a powder coating business. However, if the plant uses the machine occasionally, hiring it will be an ideal option than purchasing a new one.
Cost of the system
Although some people aim to cut costs by purchasing cheaper equipment, it may come back to bite the business. Rather than focus on the initial cost, look for high-quality and durable equipment since they often have a better return on investment. One should conduct thorough research to ensure that the machine is from a trustworthy distributor, even if it costs a little bit more.
Storage space
Before settling for powder coating equipment, one should assess if they have enough storage space. The machines involve huge investments and cannot just be left in the open air.
Since powder coating is a three-stage process, it is reasonable to evaluate if the preparation and booth areas are large enough to meet the business needs.
If the plan is to buy huge pieces of equipment, there should be enough space to store them. Understanding the available spaces can help an entrepreneur to make good purchasing decisions.
Quality
Everyone delights in high-quality machines that last longer. Quality machines enhance productivity and result in a positive return on investment. On the other hand, low-quality powder coating equipment may cost less, but may as well lead to substandard finish products.
Size of the area to be coated
If the business coats large parts, one may need larger machines to improve efficiency and meet production deadlines. Investing in small, manually operated spray guns and other equipment is suitable for small coated parts.
Coating thickness
During the inspection and application stages of the coating process, the operator determines the powder film thickness of the metal part. The appearance and performance of the material being coated are affected by dry film thickness (DFT).
Coating thickness also affects texture, color, adhesion, hardness, flexibility, corrosion resistance, and how the parts move and fit. One can choose ideal powder coating machines that will produce the required thickness and functions.
Productivity
Automated powder-coating machines are more efficient and can coat more parts than manually-operated ones. However, productivity depends on the business’ demand for powder-coated materials. If the orders are high, an investor will need equipment with a high productivity level.
Applicable material
The type of material to be coated is another factor worth considering before purchasing powder coating equipment. For instance, a powder coating business dealing in materials with oil, solvent, chemical residue, and grease will invest in a wash station for its cleaning stage. On the hand, if the material only has old paints, dust, debris, and dirt, the business may choose to invest in a blast room and avoid a wash station.
Conclusion
The powder coating process requires considerable investments in terms of machines and space. Therefore, one should evaluate their needs and conduct due diligence before settling for a machine. This beginner’s guide to powder coating has highlighted what it is and what one needs to jump into this industry.