Laser cladding, also called laser overlay welding, is used in manufacturing to coat different materials. The technology that has gained popularity over the years comes with various benefits. It helps to protect materials from oxidation and corrosion. Using laser cladding technology improves the overall surface properties.
This article will run through everything you need to know about laser cladding.
Table of Contents
What is laser cladding?
Laser cladding process
Benefits of laser cladding
Characteristics of laser cladding
Is laser cladding expensive?
Recent innovations in laser cladding
Conclusion
What is laser cladding?
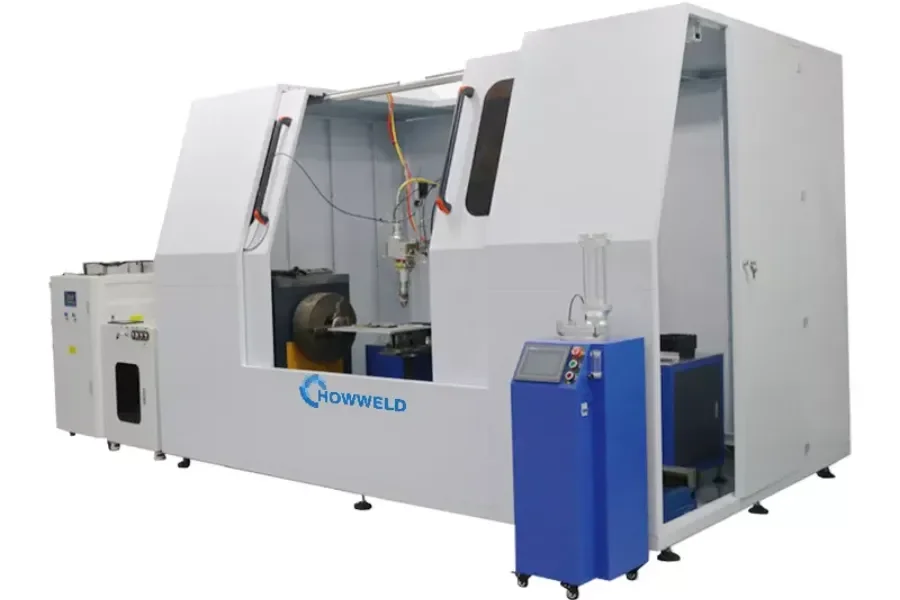
Laser cladding is an additional process in manufacturing that imparts coating on various types of material surfaces. In general, it improves surface properties, which protects the material from oxidation and corrosion. The process involves a melt pool being traversed across the base material surface. At the same time, either powder or wire feedstock is applied, which creates a thin layer of coating.
The laser-induced cladding provides evenly distributed coatings. With high repeatability, the layers are free from cracking and porosity. They also exhibit good adhesion, low surface roughness, low dilution, and less wastage of material is involved. The process can be enhanced by adjusting the density, travel speed, and diameter of the laser beams on an object’s surface.
Laser cladding process
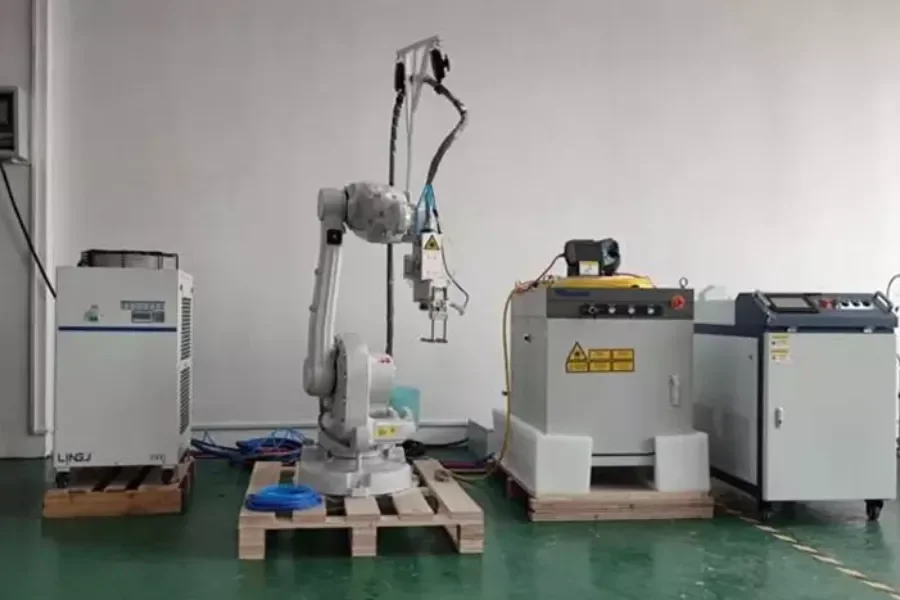
The process is a directed energy deposition (DED), and is also referred to as laser overlay welding. When used in additive manufacturing, it is called laser metal deposition (LMD) or directed laser metal deposition (DLMD).
A laser beam melts and bonds metal alloys to a substrate surface or a previously deposited layer. The dense laser cladding layer is metallurgically bonded under minimal dilution from the metal material. The heat input should be sufficient to produce a high-quality overlay.
Below are various processes of laser cladding:
Single-step laser cladding
In the single-step process, the coating material is introduced into the melt pool where it changes into molten form over the substrate surface. When the moving laser beam leaves the space, the molten coating substance solidifies. As a result, a fine coating is created by overlapped tracks of laser movement.
Two-step laser cladding
The two-step processing involves the initial deposition of coating material over the substrate surface. Afterward, surface treatment takes the moving laser beam to melt the coating material and the substrate material together. The coating solidifies spontaneously as soon as the laser beam leaves the space coating.
Wire cladding
During the wire cladding process, the wire is directly fed from the spool to the off axes torch. It is then heated below the melting temperature where cladding happens through the wire guiding system.
This process is advantageous due to 100% efficiency in the usage of filler materials. It is also a clean process that has various options for wire materials. However, the radiation absorption in the wires gives an inconsistent output.
Powder cladding
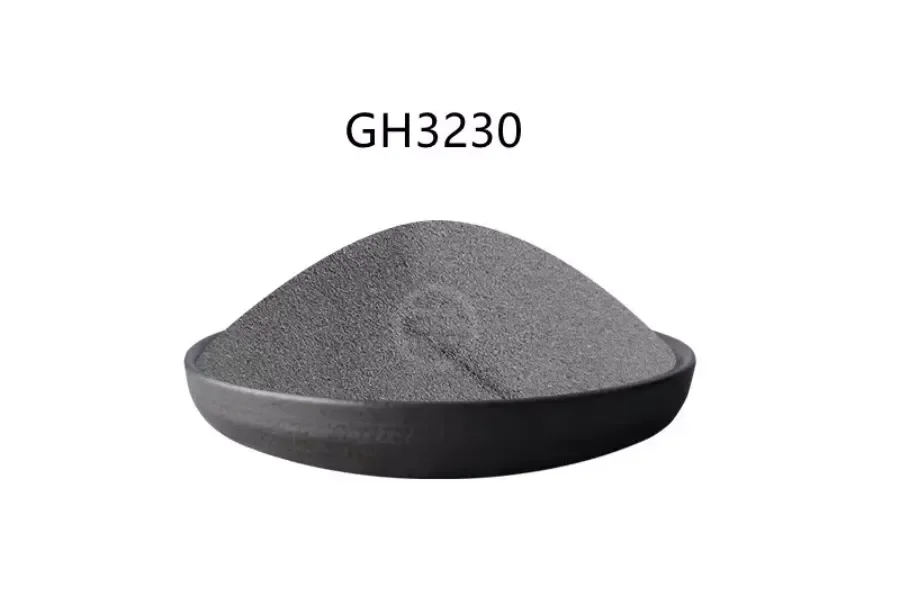
In powder cladding, the powder is transmitted from the rotating disc to the feed nozzle. It is passed through carrier gasses, for instance, Argon or Helium, where the absorption principle is applied. The powder particle is then forced out by the carrier gasses at high speed.
This results in ultimate cladding which is even and reproducible. The process has various feeding methods and materials. It is also a better option for a 3D setup.
Benefits of laser cladding
Lasers are the preferred choice for micromachining and material processing. Under laser cladding, you utilize parameters like pulse repetition frequency, laser power, wavelength, and various types of beam profiles.
The following are the advantages ascribed to laser cladding:
- It ensures the metallurgical bonding of surfaces and basic materials
- The process requires a low exposure time and depth of the laser beam
- Laser cladding produces resistant overlays compared to thermal spray coatings
- The high surface quality achieved and low warpage reduces the need for post-processing
- It is highly efficient due to the reduced cost, short laser cladding period, and less material wastage
Characteristics of laser cladding
Laser cladding mainly employs low heat impact and great precision features. It also has other characteristics, which include:
- Fast cooling rate due to the rapid solidification process; the rate goes up to about 106 K/s. It is easy to get fine crystalline evenly distributed coatings.
- It requires smaller heat input and distortion when high power density rapid cladding is used. The distortion can be minimized to within the assembly tolerances.
- Low coating dilution rate which is generally less than 5%. Through the adjustment of laser parameters, the substrate is firmly bonded metallurgically or through interfacial diffusion.
- The laser cladding layer has a large range of thicknesses with a single-channel powder feed coating of about 0.2 to 2.0 mm.
- There are no restrictions on the powder choice when depositing high melting point materials on the surface of low melting point objects.
- The laser cladding process is easy to automate.
- The process enhances selective deposition having low material consumption with an excellent performance-to-price ratio.
- Beam layers aiming overlap and thus can fuse inaccessible areas.
Is laser cladding expensive?
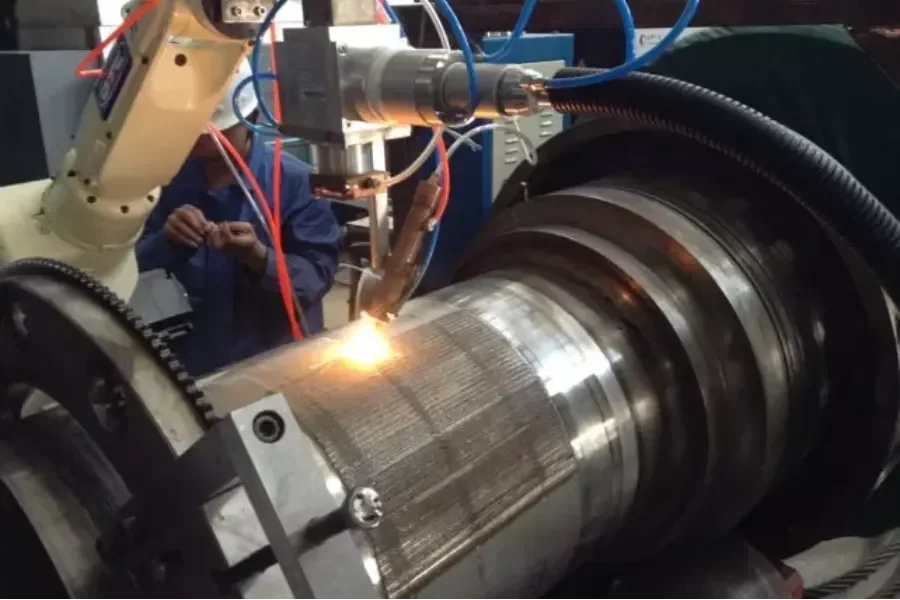
Developed over 30 years ago, laser cladding has always been considered the last-option technology. This is because of the high initial investment and operational costs of the laser equipment. However, there have been tremendous advancements in modern solid-state lasers.
The integration of robotics through fiber-coupled beam delivery has made the process more efficient and less costly. Considering the cost-benefit analysis, laser cladding is winning and growing exponentially across various industry sectors.
Recent innovations in laser cladding
The recent innovations in laser cladding have mainly focused on increasing productivity. The advancements still maintain the primary characteristics of laser cladding.
The following are examples of the innovations:
- High-speed laser cladding entirely melts the additive powder in the laser beam before reaching the base material. The solid base is fused with the molten powder through heat conduction transfer.
- The hot-wire laser cladding provides a pre-heated wire into the process; this avails more laser energy to melt the base material with an increased feed rate.
- Laser cladding employs a co-axial laser beam which feeds the additive material perpendicular to the workpiece. The laser is coaxially projected around the wire. This enhances consistent processing which is independent of the direction of travel for 3D laser metal deposition.
- The large spot laser cladding process increases the size of the laser spot on the workpiece. This enables the usage of more laser power without excessively melting the base material and increasing dilution.
Conclusion
Laser cladding technology has recently made great strides in modern manufacturing. Many production companies are considering laser technology to recondition OEM products. The process has also improved the corrosion and wear characteristics of the items.
The above guide explains the laser cladding process and its benefits. Buyers should ensure that quality is maintained during laser coating. To find the laser cladding equipment of your choice, visit Alibaba.com.